Методы выявления микроструктуры материала, методы пробподготовки
Содержание
Общая информация о структуре материала и ее влиянии на свойства.............3
Методы выявления микроструктуры материала, методы пробподготовки…..5
Методы оценки микроструктуры материала и основные характеристики…..10
Оценка микроструктуры материала. Цель, особенности пробобработки …..13
Определение механических свойств металлических материалов …………...15
Библиографический список……………………………………………………..18
Общая информация о структуре материала и ее влиянии на свойства
Кристаллическая структура. Кристаллическая структура – это такая структура, которой свойственно упорядоченное расположение частиц в строго определенных точках пространства, которые образуют кристаллическую решетку. Эта упорядоченность позволяет экспериментально и теоретически полностью изучить структуру твердого состояния и явления, связанные с природой сил взаимодействия в кристаллических телах.
Кристаллическая структура образуется при очень медленном охлаждении расплава, когда атомы (ионы) имеют возможность перемещаться в пространстве и занимать наиболее устойчивые положения, в которых их потенциальная энергия в силовом ноле окружающих атомов минимальна. Для удаления атома из вещества нужно сообщить ему энергию, достаточную для преодоления удерживающих сил. Эта энергия характеризует силу связи атома в кристалле.
Анизотропия кристалла — неравномерность свойств в разных направлениях — является следствием периодичности расположения атомов в кристалле. От направления зависят не все свойства, а только те, которые характеризуются векторными величинами (прочность, упругость, теплопроводность, удлинение). Анизотропия материалов обусловлена также их макростроением, например расположением волокон древесины вдоль оси ствола.
|
|
Полиморфизм — способность некоторых веществ под действием температуры и давления изменять структуру кристаллической решетки, образуя несколько аллотропических модификаций одного и того же вещества. Хорошо известны две модификации углерода: графит (один из самых мягких минералов) и алмаз (самый твердый минерал). Кварц (Si02) при нагревании до 573 °С переходит из р - в а-модификацию; затем при температуре 870 °С он переходит в тридимит, который при температуре 1 470 °С переходит в кристобалит. Явление полиморфизма часто наблюдается у металлов.
Изоморфизм — способность близких по составу веществ встраиваться в кристаллическую решетку друг друга без изменения ее структуры, т. е. образовывать твердые растворы замещения (изоморфные смеси).
В реальных кристаллах далеко не все атомы располагаются правильным образом. В отдельных узлах кристаллической решетки атомы могут отсутствовать, образуя вакансии; некоторые атомы могут находиться в междоузлии. В решетку могут быть внедрены чужие атомы — примеси.
|
|
Если одна из атомных плоскостей (совокупность атомов, находящихся в одной плоскости), начинаясь на одном конце кристалла, обрывается внутри его и не доходит до другого конца, то такой дефект называется краевой дислокацией.
Существует также винтовая дислокация — смещение атомов, при котором атомные плоскости образуют одну винтовую поверхность. Дефектом является также граница между зернами в кристаллических материалах — зона перехода между кристаллами, повернутыми относительно друг друга на некоторый угол. Она представляет собой поверхность выхода дислокаций.
Аморфная структура.
Аморфная структура образуется при быстром охлаждении расплава, когда атомы при переходе в твердое состояние не успевают образовать кристаллическую решетку, а остаются вблизи тех положений, которые занимали в жидкости. Аморфная структура не является совершенно беспорядочной. Некое подобие порядка наблюдается в ближайшем окружении атомов. Аморфное состояние вещества является термодинамически неустойчивым (метастабильным) в отличие от кристаллического состояния. Поэтому при нагреве, когда атомы приобретают определенную подвижность, в аморфном теле происходит кристаллизация. Термодинамическая неустойчивость обусловливает и более высокую химическую активность аморфных веществ.
|
|
Аморфные вещества прозрачны, так как не имеют границ между кристаллами, рассеивающих световые волны. Такие вещества называются стеклами, а их структура — стеклообразной. В строительстве применяются стекла, получаемые из минеральных и полимерных расплавов.
Материалы с жидкой дисперсионной средой (на стадии формования) имеют коагуляционную структуру со сравнительно слабыми контактами, осуществляемыми через жидкую прослойку и допускающими сдвиг частиц относительно друг друга. Расстояние между частицами (толщина прослойки) зависит от концентрации дискретной фазы и составляет от 1 до 100 нм. К малоконцентрированным системам относятся многие лакокрасочные материалы, представляющие собой суспензии тонкодисперсных пигментов и наполнителей в связующей жидкости. Высококонцентрированными дисперсными системами являются бетонные и растворные смеси, керамическая масса, мастики и др.
|
|
Для материалов с твердой дисперсионной средой характерны прочные контакты между «сросшимися» частицами. Структуру аморфных тел в этом случае называют конденсационной, а структуру кристаллических фаз — кристаллизационной.
Методы выявления микроструктуры материала, методы пробподготовки
Микрошлифом называют небольшой образец металла, имеющий специально приготовленную поверхность для проведения микроанализа.
Хорошо приготовленный микрошлиф должен отвечать ряду требований:
– прежде всего, он должен быть представительным для структуры и свойств изучаемого объекта (детали);
– вырезка, шлифование и полирование образца должны осуществляться таким образом, чтобы на его поверхности оставался минимальный слой металла, деформированного шлифоприготовлением;
– на поверхности шлифа не должно быть царапин, рисок, ямок и загрязнений;
– в процессе приготовления шлифа не должно происходить выкрашивания неметаллических включений, карбидных и некоторых других фаз;
– поверхность шлифа должна быть плоской и гладкой для обеспечения исследования его при больших увеличениях.
Вырезку образцов следует проводить, соблюдая определенные меры предосторожности, чтобы не вызвать изменения структуры из-за наклепа или нагрева.Наиболее часто для вырезки образцов в металлографических лабораториях используют отрезные станки с абразивными кругами. Для удовлетворительной резки, обеспечивающей отсутствие прижогов и значительного деформационного повреждения поверхности, важно выбрать соответствующий круг и режим резания:
– для резки сталей предпочтительнее использовать круги с абразивными частицами из Al2O3;
– для резки цветных металлов – круги с частицами SiC;
– грубозернистые круги обычно более быстро и с меньшим нагревом режут крупные сечения, а мелкозернистые позволяют получить лучшую чистоту поверхности и исключить прижог при резке деталей малого сечения;
– для резки мягких материалов обычно применяют твердые круги (с твердым связующим материалом), а для резки твердых материалов – мягкие круги.
Подготовка поверхности. Плоскость для исследования выбранной поверхности шлифа получают механической обработкой (торцеванием, фрезерованием, опиливанием, шлифованием) с обязательным охлаждением, не допуская нагрева. Для ручной обработки шлифа удобны образцы прямоугольной или цилиндрической формы диаметром 10–15 мм или со стороной квадрата 10–15 мм, высотой 15–20 мм. При массовом исследовании и механической подготовке шлифов в соответствии с формой и размерами образцов изготавливают специальные держатели .
Шлифование. После получения плоской поверхности образцы вручную или на специальных станках (рис. 3) шлифуют крупнозернистой шлифовальной шкуркой с постепенным переходом к мелкозернистой. Шлифование проводят в одном направлении до тех пор, пока не исчезнет рельеф от обработки шкуркой предыдущего номера (т. е. поворачивать образец на 90° можно только при переходе к шлифованию шкуркой другой зернистости).После шлифования для удаления остатков абразива шлиф промывают водой, а затем полируют.
Полирование. Полирование служит для удаления мелких рисок, оставшихся после шлифования, и получения гладкой зеркальной поверхности шлифа.Полирование осуществляется вручную или на автоматических станках
При ручном полировании образец непрерывно перемещают от центра к периферии, что обеспечивает равномерное распределение абразива и однородный износ полировального материала. Кроме того, образец периодически вращают или перемещают «восьмеркой», чтобы исключить образование «хвостов» около неметаллических включений и частиц выделившихся фаз. Чаще полирование проводят на специальном полировальном станке, диск которого обтянут тканью (фетр, сукно, бархат). В качестве абразива применяют окислы железа, алюминия, хрома и т. д. с водой.
Для выявления полной микроструктуры поверхность шлифа подвергают травлению, т. е. воздействию химически активных растворов щелочей, солей, кислот в спирте или воде. Конкретный химический реактив для травления выбирают, исходя из состава исследуемого металла, его предшествующей обработки и цели исследования. В процессе травления реактив неодинаково взаимодействует с различными участками поверхности микрошлифа, что приводит к разной степени их травимости. Принцип травления многофазных сплавов заключается в избирательном растворении (вследствие разных скоростей растворения фаз в травящем реактиве) либо окраске одной или нескольких фаз благодаря разнице в химическом составе и в меньшей степени – различной ориентации структурных составляющих.
Реактивы для микроисследования структуры сплавов
Наименование реактива | Состав реактива | Особенности применения реактива |
Для травления углеродистых, низколегированных сталей и чугуна | ||
Спиртовой раствор азотной кислоты (реактив Ржешотарского) | Азотная кислота 1–5 мл, этиловый (или метиловый) спирт 100 мл. | Окрашивает перлит в темный цвет, выявляет границы зерен феррита, структуру мартенсита. Для выявления структуры азотированной и цементированной стали. |
Спиртовой раствор пикриновой кислоты (реактив Ижевского) | Пикриновая кислота (кристаллическая) 3–5 мл, этиловый (или метиловый) спирт 100 мл. | |
Раствор соляной и пикриновой ки- слот | Соляная кислота 3 мл, пикриновая кислота 4 г, вода 100 мл. | Для выявления границ зерен в закаленной стали. |
Раствор азотной и соляной кислот | Азотная кислота 25 мл, соляная кислота 50 мл, двухромокислый калий 12 г, вода 25 мл. | Для выявления границ зерен в закаленной стали. Травление в реактиве, выдержанном 24–48 ч; время травления 1–2 с. |
Для травления высоколегированных сталей | ||
Раствор азотной и соляной кислот в глицерине | Азотная кислота 10 мл, соляная кислота 20–30 мл, глицерин 30 мл. | Для выявления структуры высокохромистой, быст- рорежущей и аустенитной стали в закаленном состоянии. |
Солянокислый раствор хлорного железа | Хлорное железо 5 г, соляная кислота 50 мл, вода 100 мл. | Для выявления структуры высоконикелевой нержавеющей стали. |
Солянокислый раствор медного купороса (реактив Марбе) | Сернокислая медь 10 г, соляная кислота 50 мл, вода (или этиловый спирт) 50 мл. | Для выявления структуры сложнолегированной аустенитной стали. |
Для травления меди и медных сплавов | ||
Солянокислый раствор хлорного железа | Хлорное железо 10 г, соляная кислота 25 мл, вода 100 мл. | Для выявления структуры меди, латуни оловянной, бронзы и т. д. |
Для травления алюминиевых сплавов | ||
Плавиковая кислота | Плавиковая кислота (48%) 0,5 мл, вода 99,5 мл. | Для выявления структуры дуралюминов и литых сплавов на алюминиевой основе. |
Дата добавления: 2019-09-13; просмотров: 440; Мы поможем в написании вашей работы! |
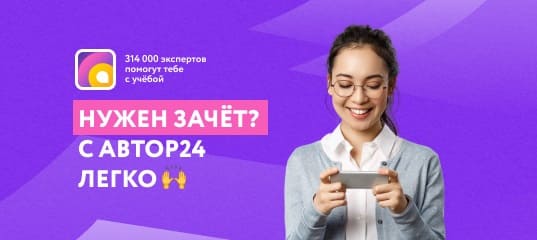
Мы поможем в написании ваших работ!