ЭКСПЛУАТАЦИОННАЯ БЕЗОПАСНОСТЬ ПС
5
6
ОБЕСПЕЧЕНИЕ БЕЗОПАСНОСТИ ДВИЖЕНИЯ ПОЕЗДОВ
Тенденции повышения безопасности движения должны предусматривать:
- принципиально новые узлы и детали в конструкциях подвижного состава. Состояние локомотивного и моторвагонного парка характеризуется его изношенностью, переработкой нормативного ресурса, использованием устаревших технических решений (коллекторные тяговые электродвигатели, контакторное регулирование, пусковые реостаты, моторно-осевые подшипники скольжения). Новые технические решения включают установку моторно-якорных подшипников качения, асинхронного привода тяговых электродвигателей и вспомогательного оборудования локомотивов, электронные устройства вместо контактного регулирования в электрических цепях, поосное регулирование силы тяги, полную автоматизацию управления для режима тяги и торможения;
- комплексное решение методов безопасного вождения поездов повышенной массы и длины. При этом особое внимание должно быть обращено на использование распределенной локомотивной тяги и применение средств автоведения. Они должны исключать появление в поезде сверхнормативных продольных и поперечных усилий, которые обычно являются причиной схода колесных пар вагонов с рельсов;
- повышение эффективности действия тормозной системы. Необходимы усовершенствования электрического тормоза ТПС;
- повышение качества контроля текущего ремонта локомотивов и вагонов из-за недостаточной эффективности средств технической диагностики. Информация с приборов выдается в трудно интерпретируемом виде, что требует высокой квалификации персонала депо и фактически обесценивает преимущество автоматизации. Полученная информация не всегда позволяет перейти к режиму работы «годен – негоден»;
|
|
- технологичность конструкции изделия. Технология изготовления и ремонта узлов подвижного состава определяет его надежность. В процессе эксплуатации постепенно надежность и, как следствие, безопасность снижается по причине изнашивания трущихся деталей, усталости металла и других необратимых процессов. Вызванные по этой причине повреждения, устранение которых становиться необходимым для дальнейшей безотказной работы подвижного состава, снижают надежность ТПС. Максимально уменьшить возможность появления различных дефектов необходимо на стадии разработки детали. Данное условие должно быть на первом месте при обеспечении технологичности конструкции изделия. Следовательно, каждая деталь или узел локомотива или вагона должны быть сертифицированы и их изготовление соответствовать заданной вероятности безотказной работы;
|
|
- комплексы технических средств обеспечения безопасности движения, поставляемые на железные дороги (стационарные и бортовые системы). Указанные системы отслеживают на станциях и перегонах нарушения безопасности движения подвижного состава, тем самым, предупреждая возникновение рисков безопасного движения, которые всегда имеют место. Поэтому необходимо оценивать предаварийное состояние подвижного состава в эксплуатации;
- системы контроля предаварийного состояния основных технических объектов железнодорожного транспорта, уделяя при этом особое внимание остаточному ресурсу технических средств. Повышенное внимание фактору остаточного ресурса связано с общепринятыми в отрасли оценками повышения рисков и с износом основных фондов железных дорог. Разрабатываемая система позволяет дать помимо качественных оценок («лучше – хуже») количественные динамики рисков (по времени) в зависимости от действий отрасли по обновлению основных технических средств контроля.
Прогноз на примере исследования ресурса вагонного парка показывает тенденцию увеличения рисков аварий и крушений (тележки вагонов), даже при выполнении заложенного в комплексной программе реорганизации процента обновления вагонного парка. Необходимы дополнительные меры по парированию роста аварийности на фоне исчерпания ресурса вагонного парка.
|
|
Возможности автоматизированной информационной системы контроля предаварийного состояния – АИС «Риск – Ресурс» позволяют определять слабые места в принятии решений по обновлению технических средств, своевременно планировать и осуществлять широкий спектр корректирующих воздействий по тем или иным узким местам, особенно в новых условиях работы отрасли [7];
- использование автоматизированных средств в техническом обслуживании вагонов. Система обеспечивает обнаружение перегретых букс по темпу приращения температуры корпуса буксы по мере движения поезда. Новые датчики счета осей, действующие в диапазоне скоростей от 0 до 300 км/ч, предотвращают сбои в счете осей и вагонов при низких скоростях движения поезда;
- систему контроля технологической дисциплины – как в корпорации в целом, так и в отдельных ее хозяйствах.
Главное назначение системы контроля технологической дисциплины –обеспечение соблюдения технологии работы железнодорожного транспорта путем сбора, обработки и анализа соответствующей информации АСУЖТ, технологических средств СЦБ и информации от ТПС.
|
|
Более 90% брака в работе происходит по причине нарушения технологической дисциплины. Браки по причине отказа технических средств могут происходить как по вине соответствующих хозяйств (некачественное обслуживание), так и по вине неправильной эксплуатации.
Создание системы контроля технологической дисциплины ведется для повышения качества работы оперативного персонала, задействованного в перевозочном процессе. Реализация данной системы позволяет улучшить технологическую дисциплину, повысить эффективность перевозочного процесса в целом и улучшить качество взаимодействие работников диспетчерского центра, ДСП и локомотивных бригад;
- наличие устройств автоматизированной диагностики подвижного состава. Аппаратура автоматического обнаружения перегретых букс в поездах типа ПОНАБ и КТСМ получили широкое распространение на отечественных железных дорогах. В основе используется принцип контроля исправности буксовых узлов по уровню инфракрасной энергии, излучаемой корпусом буксового узла в окружающее пространство.
Дальность передачи информации от перегонного оборудования к станционному – 20 км, от регистрирующего оборудования к сигнализирующим устройствам – 2км. ПОНАБ и КТСМ устанавливаются вдоль участка безостановочного следования поездов с интервалом 40-60 км между смежными пунктами контроля.
В соответствии с требованиями эксплуатации о заблаговременной выдачи персоналу станции информации о наличии в поезде перегретых букс, аппаратура ПОНАБ и КТСМ имеет перегонное и станционное оборудование.
Общий принцип работы ПОНАБ и КТСМ заключается в восприятии чувствительными элементами (приемниками) импульсов инфракрасной энергии, преобразование их в электрические сигналы и выделение по определенным критериям сигналов от перегретых букс;
- повышение квалификации персонала, связанного с техническим обслуживанием и эксплуатацией подвижного состава. В настоящее время в депо начинают использовать новые технологии ремонта и восстановления, сложные устройства технической диагностики и послеремонтного контроля. На локомотивах применяют электронные системы управления и регулирования, бортовые диагностические системы, микропроцессорное оборудование, бесколлекторный (асинхронный) тяговый привод локомотивов, что на порядок усложняет электронное оборудование электровозов и тепловозов.
Наметилась тенденция постепенного перехода к ремонту по фактическому состоянию. Внедряется комплексная информационно-управляющая система АСУТ.
В связи с эти выдвигаются принципиально новые требования к квалификации персонала депо. В ОАО «РЖД» создан центр повышения квалификации сотрудников компании с включением в учебных программах Центра разделов по:
- новым технологиям обслуживания и ремонта ТПС;
- организации эксплуатации локомотивов и бригад с использованием новых информационных средств – АСУТ, АРМ, бортовой диагностики, непрерывного контроля бдительности машиниста и т.д.;
- обеспечению безопасности на базе технических и нормативно-правовых средств (системы КЛУБ-У, БЛОК и др.);
- использованию современных методов оперативного управления и менеджмента;
- минимизированию рисков (факторов угроз) в перевозочном процессе. Происшествия на сети дорог сигнализируют о том, что только своевременное устранение факторов риска на местах может предотвратить нарушение безопасности;
- риск–менеджмент – новый подход Компании, изложенный в стратегии «Обеспечение гарантированной безопасности и надежности перевозочного процесса», предусматривающий не только управление и инновации, но и прогнозирование, планирование, обеспечение гарантированных уровней безопасности. В том числе с помощью современных технологий и оборудования.
Задача современных руководителей – выявить риски на своем поле. Для этого в целях выявления угроз необходимо проводить аудиты и мониторинги, анализы базы данных информационных систем – все это позволит заблаговременно устранить риски.
Дата добавления: 2019-09-13; просмотров: 752; Мы поможем в написании вашей работы! |
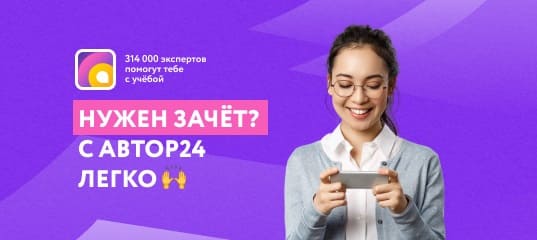
Мы поможем в написании ваших работ!