Петля контроля качества продукции
Глава 12. Контроль качества продукции
Назначение, объекты и процессы контроля качества
Контроль – эта деятельность, включающая проведение измерений, экспертизы, испытаний и оценок нескольких характеристик, сравнение полученных результатов с установленными требованиями для определения достигнуто ли соответствие по каждой из характеристик. Назначение контроля заключается в получении информации о состоянии объекта контроля.
Цели контроля состоят в следующем:
– защитить потребителя от некачественной продукции проведением приемочного контроля продукции;
– защитить производителя от некачественных входящих ресурсов;
– обеспечить производителю уверенность в том, что выпускаемая продукция соответствует требованиям потребителя путем осуществления системы производственного контроля качества продукции.
Особенность контроля в области качества состоит в том, что его объектами являются продукция и процессы (рис. 12.1).
![]() |
Рис.12.1. Объекты и процессы контроля качества
Контроль качества продукции, согласно ГОСТ 16504–81,это проверка с помощью специальных технических средств, органолептических и экспертных методов соответствия характеристик продукции требованиям, что полностью соответствует определению контроля по ISO 9000. Контроль качества процессов – это проверка выполнения технологического регламента процесса. Она осуществляется посредством непрерывного или периодического измерения качества «выхода» каждого процесса технологической цепочки. Контроль, как следует из его определения, осуществляется посредством следующих процессов: измерение, испытания и экспертиза.
|
|
Измерение - это инструментальное получение числового (количество) значения некоторого параметра, характеризующего одно или несколько свойств объекта.
Испытание – экспериментальное определение количественных и (или) качественных показателей свойств объекта как результата воздействия на него условий испытаний. Условия испытаний – совокупность воздействующих факторов и режимов функционирования объекта при испытаниях.
Экспертиза. Понятие «expertise» в переводе с латинского языка означает исследование, проверка какого–либо вопроса, требующего специальных знаний, с представлением мотивированного заключения. В подготовке экспертизы участвуют исследователь или консультант, менеджер – организатор и эксперты.
Контроль в области качества осуществляется практически по всем процессам жизненного цикла продукции, изображенным на рис. 6.3. Объектами контроля выступают, прежде всего, продукция каждого процесса, а затем сами процессы. Контроль качества является обязательной и, на сегодняшний день на российских предприятиях, первостепенной функцией управления качеством. Для этой функции характерна системная деятельность. Под системой контроля качества понимается совокупность объектов контроля, средств контроля, методик проведения измерений, испытаний, анализов и исполнителей, взаимодействующих по определенным правилам и регламенту, установленным соответствующей документацией.
|
|
Виды контроля качества продукции
Контроль качества продукции – это контроль количественных и качественных характеристик продукции, их соответствия установленным требованиям. Виды контроля различаются по классификационным признакам, определенным в основном ГОСТ 16504–81. Рассмотрим их.
1.Стадия жизни продукции:
– производственный контроль, осуществляемый на стадии производства;
– эксплуатационный контроль, осуществляемый на стадии эксплуатации продукции.
2.Стадия производственного цикла:
– входной контроль сырья, материалов, комплектующих, поступающих к потребителю или заказчику и предназначенных для использования на стадии изготовления, ремонта или эксплуатации продукции;
|
|
– операционный контроль качества продукции в процессе ее изготовления для оценки состояния технологического процесса с последующей наладкой, если это необходимо;
– приемочный, или финишный контроль, предназначенный для определения того, приемлема ли для использования поставляемая или предполагаемая для поставки единица или партия готовой продукции;
– контроль хранения продукции;
– контроль транспортировки продукции.
3. Полнота проверки продукции:
– сплошной контроль, при котором проверяются все единицы изделия;
– выборочный контроль, при котором проверяется из совокупности (партии) относительно небольшое количество единиц изделий;
Сплошной (непрерывный) контроль – это предельный (100%-го) вариант контроля, Проведение этого вида контроля связано с большими затратами и, он, как правило, выступает для обоснования генеральной гипотезы о природе изменения контролируемой случайной величины. Сплошной контроль осуществляется в следующих случаях:
– на стадии освоения новой продукции;
– когда технологический процесс не обеспечивает необходимой стабильности качества продукции;
– при высоких требованиях к качеству выпускаемой продукции, когда абсолютно не допустим дефект.
|
|
Выборочный контроль – это периодический отбор проб из партии для анализа или периодически выполняемое некоторое количество измерений показателей качества продукции. Объем выборки или числа измерений определяется на основе методов математической статистики. Выборочный контроль применяется в следующих случаях:
– массового и крупносерийного производства, когда допускаются риски для изготовителя и потребителя продукции;
– когда контролируемые единицы продукции разрушаются или теряют свойства при контроле;
– высокой трудоемкости контроля.
4. Характер поступления продукции на контроль:
– непрерывный контроль (контроль сыпучих и жидких материалов), обеспечивающий непрерывное поступление информации о контролируемых характеристиках;
– периодический контроль специальной партии продукции (или выборки продукции) и соответственно этому происходит дискретное поступление информации о контролируемых характеристиках продукции.
5. Период проверки качества:
– плановый контроль по регламенту;
– летучий контроль, осуществляемый внезапно, в незапланированные ранее моменты времени;
– инспекционный контроль – это периодический контроль уже проверенной продукции, из которой удален обнаруженный брак, осуществляемый при необходимости проверки качества работы отделом технического контроля;
Инспекционный контроль в особых случаях выполняется представителями заказчика для повышения ответственности проверяющего органа изготовителя.
6. Способы и средства контроля:
– измерительный контроль, осуществляемый с применением средств измерения;
– регистрационный контроль, осуществляемых регистрацией значений контролируемых параметров продукции или процессов;
– органолептический контроль, при котором первичная информация воспринимается органами чувств – это вкус продукта питания, цвет ткани, различимость шрифта, соответствие моде и т.д.;
– визуальный контроль – органолептический контроль, осуществляемый органами зрения;
– технический осмотр – контроль, осуществляемый в основном при помощи органов чувств и, в случае необходимости, средств контроля, номенклатура которых указана соответствующей документацией.
7. По способу проведения проверки:
– ручной;
– механизированный;
– автоматические системы;
– автоматизированные системы;
8. Вид контролируемого параметра:
– количественная характеристика;
– качественная характеристика;
– альтернативный признак.
Количественные характеристики представлены переменными, измерение которых основано на непрерывных числовых шкалах, например, длина, вес, содержание компонентов и др. Качественные характеристики – это атрибуты, которые оценивают либо без детального измерения (по принципу «годен или не годен»), либо субъективно (нечто имеет некий атрибут, или не имеет, к примеру, поверхность отделана приемлемо или неприемлемо). Оценка качества продукции по принципу «годен, или не годен» называется оценка по альтернативному признаку.
Контроль по количественному признаку означает измерение (определение числового значения) и проверка на соответствие физических величин, технических параметров, состава и физико-механических (прочность, твердость, вязкость), биологические, химические и другие свойства продукции. В России ежедневно производится около 200 млрд. измерений.
При контроле по качественному признаку каждую проверенную единицу относят к определенной группе градации качества. Градация качества приводится в соответствие со шкалой квантификации или шкалой балловой оценки. Контроль по качественному признаку осуществляют с привлечением органолептического и визуального контроля и экспертных методов оценивания.
При контроле по альтернативному признаку все изделия контролируемой партии делятся на две группы: годные и дефектные. Дефектная единица продукции – единица продукции, имеющая хотя бы одно несоответствие требованиям. Дефект – каждое отдельное несоответствие продукции требованиям, установленным нормативной документацией. Продукция, передача которой не допускается из-за наличия дефектов, рассматривается как брак.
9. Влияние контроля на состояние объекта:
– разрушающий контроль, при котором продукция становится непригодной к дальнейшему использованию;
– неразрушающий контроль, при котором сохраняется пригодность объекта к применению.
Петля контроля качества продукции
Согласно концепции ISO 9000, управление качеством должно охватывать весь жизненный цикл продукции (рис. 6.2). Получить информации о соответствии качества продукции каждого процесса требованиям возможно только на основе контроля. На рис. 12.2 рассмотрены «точки» контроля соответствующие процессам жизненного цикла продукции. Они дополняют производственный и эксплуатационный контроль, введенный ГОСТ 16504–81.
Контроль по ISO 9000 рекомендуется начинать с проверки соответствия между требованиями потребителя к качеству продукции и возможностями производителя удовлетворить поставленное требование (процесс маркетинга), и оканчивается контролем эксплуатации и ремонтопригодностью продукции, или результатами её потребления. Между первым и последним процессами, на которых осуществляется контроль качества продукции, на основе анализа информации о соответствии ожидания потребителя фактическим результатам формируется обратная связь, образуя «петлю контроля» (рис. 12.2). Информация, получаемая об удовлетворенности ожидания потребителей, является входной для контроля запросов потребителя, включенных в договор или контракт на исполнение продукции.
![]() |
![]() |

Данная на рис. 12.2. «петля контроля» действует в контурах системы менеджмента качества. Контроль по большей части процессов таких, как контроль контрактов, проекта, входных ресурсов, хранения и упаковки, транспортирование проводится в целях установление соответствия выходных параметров процессов установленным требованиям нормативными документами (государственными стандартами, техническими условиями, документированными процедурами и стандартами предприятия). Кратко рассмотрим особенности контроля по основным процессам ЖЦП, основываясь на материалах международных стандартов ISO 9000.
Контроль запросов клиентов и их контрактов. В широком смысле качество определяется как способность изделия или услуги последовательно отвечать на ожидания потребителей или предвосхищать их. Основу контроля качества запросов потребителя составляет система информирования клиентов о продукции или услуге. Выстраиваются модели продукции в виде реальных образцов с просмотром функционального качества, технической документации или компьютерных объектных моделей с имитацией функционального качества. Контроль контракта проводится и для подтверждения соответствия между параметрами продукции в контракте и эталонной продукцией, выпускаемой производителем. Цель контроля минимизация расхождений между ожиданиями потребителя и функциональным качеством продукции.
Контроль качества при проектировании. Качество начинает реально воплощаться в продукции в процессах проектирования, обеспечивается в производстве и проявляется при эксплуатации. Контроль проектирования продукции сводится к контролю документации на продукцию и процессы ее производства. Целью контроля является выявление отклонений для своевременной корректировки параметров продукции и её процессов. Проверка осуществляется в виде систематического контроля проектируемой документации, построения контрольных графиков, диаграммы Парето, причинно-следственной диаграммы и др. Оценка качества проводится с применением как количественных, так и качественных показателей.
Контроль входных ресурсов. Для оценкиважности этой функции необходимо помнить, что в себестоимости продукции свыше 50% занимает доля сырья и материалов. Снижение издержек в первую очередь связано с качеством входных ресурсов и полным соответствием их потребностям производства. Входной контроль включает следующие операции:
– контроль поставок на соответствие стандартам качества, техническим и технологическим требованиям;
– контроль временного цикла поставок и условий перевозок;
– контроль соотношения цены и качества по партии поставок в целях определения размера партии;
– участие в выборе поставщиков для контроля качества их работы и процедур обеспечения уровня качества продукции;
– контроль соответствия уровня прогрессивности материальных ресурсов уровню конкурентоспособности продукции.
Уровни качества материалов на начальном этапе поступления продукции от поставщиков допускают 1-5% бракованных изделий. При дальнейшем развитии отношений с поставщиками возможно снижение брака до 0,5 – 0,1%. Основываясь на принятом браковочном уровне, формируется контроль поставляемых ресурсов. Устанавливаются контрольные значения объема партии, объема выборки партии, а также уровень риска поставщика и потребителя. Разрабатывается методика выполнения контроля и оценки его трудоемкости.
Контроль производства. Цель контроля качества на этапе изготовления продукции – гарантировать, что все производственные операции выполняются в соответствии с регламентом и требованиями нормативной документации. Основные функции по проверке качества продукции в ходе её производства возлагаются на операционный контроль и приемочный контроль. И тот и другой виды контроля заключаются в систематическом выявлении и анализе отклонений в характеристиках продукции, что. позволяет сократить внепроизводственные потери, обусловленные поздним обнаружением дефекта. Контроль производства является наиболее динамичным и сложным. Область контроля определяется необходимостью его проведения и ограничивается величиной издержек.
Контроль готовой продукции. Цель контроля качества готовой продукции состоит в том, чтобы гарантировать потребителю выполнение всех его требований к продукции. Эту функцию выполняет приемочный контроль, организация которого может осуществляться по нескольким схемам: контроль последовательных партий, сплошной или выборочный контроль, контроль с разбраковкой, косвенный контроль.
Контроль качества при хранении продукции проводится с целью подтверждения сохраняемости продукции в установленный срок. Основная его функция – это периодическая проверка соответствия параметров (температура, влажность, освещенность) установленных условий и продолжительности хранения продукции требованиям, а также в периодическом отборе проб и проведении испытаний для подтверждения пригодности продукции к использованию в гарантированный срок годности.
Контроль транспортирования – это контроль способности продукции сохранять свою пригодность в процессе транспортирования, а также приспособленность к перемещению, не сопровождающемуся эксплуатацией или использованием. Он обычно состоит во внешнем осмотре изделия, а также в отборе и анализе проб сыпучих материалов и продукции для потребления.
Контроль монтажа и эксплуатации. На этапе монтажа изделия проявляются такие его свойства как степень унификации и стандартизации, качество проекта и качество изготовления. Здесь же изготовитель непосредственно вступает во взаимодействие с потребителем продукции и отслеживает его восприятие изделия. Информация этого этапа является первым источником формирования обратной связи между потребителем и поставщиком.
На этапе эксплуатации продукции проявляются основные характеристики качества продукции такие, как соответствие назначению, надежность, долговечность, экологичность, технологичность, безопасность и другие свойства. Поэтому для подтверждения уровня качества изготовленной продукции проводят контроль параметров и показателей работы оборудования, расход энергетических ресурсов, а также количества отказов в период гарантийного срока службы, время между отказами и время на устранение отказов. Результаты эксплуатации являются основой для оценки качества работы производителя и являются источником обратной связи между потребителем и производителем продукции.
Контроль технического обслуживания. Основным руководством к контролю технического обслуживания изделия является план-график планово-предупредительных ремонтов оборудования, установок и приборов, а также комплекс показателей надежности и ремонтопригодности оборудования. Исходные данные для их расчета измеряются в процессе эксплуатации оборудования. Основными контролируемыми параметрами графика планово-предупредительных ремонтов является очередность видов ремонтов (например, текущий, средний, текущий, капитальный и т.д.), наработка на очередной ремонт, его продолжительность и трудоемкость.
Дата добавления: 2019-09-02; просмотров: 318; Мы поможем в написании вашей работы! |
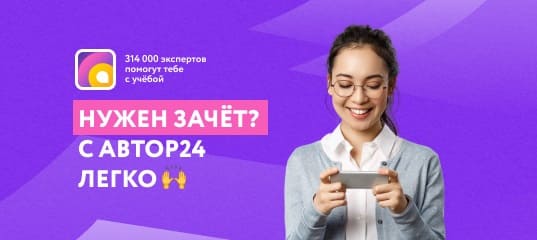
Мы поможем в написании ваших работ!