Розрахунок редуктора сумісної дії ексцентрикових валів
На початку розрахунку визначимо силові та кінематичні параметри привода:
1. Визначаєм потужності на валах привода.
2. Визначаєм кутові швидкості валів привода:
3. Визначаєм крутні моменти на валах привода:
Результати розрахунків зводимо в таблицю 2.1.
Таблиця 2.1.
Результати кінематичного і силового розрахунків приводу.
Парам. №валу | N, кВт | ω, рад/с | М, Нм | Ugj | Uд заг |
1 | 2 | 3 | 4 | 5 | 6 |
1 | 105,0 | 1,18 | 88983 | 4 5 1 0,2 | 4,0 |
2 | 100,8 | 0,29 | 343586 | ||
3 | 97,78 | 0,06 | 1629667 | ||
4 | 94,84 | 0,06 | 1580667 | ||
5 | 92,0 | 0,29 | 317241 |
Розрахунок циліндричної зубчатої передачі.
1. Кінематична схема передачі та вихідні дані для її розрахунку.
Таблиця 2.2.
Вихідні дані для розрахунку передачі
Парам. №валу | N, кВт | ω, рад/с | М, Нм | Ugj | Uд заг |
1 | 2 | 3 | 4 | 5 | 6 |
2 | 100,8 | 0,29 | 343586 | 5 | 4,0 |
3 | 97,78 | 0,06 | 1629667 |
2. Вибір матеріалу і визначення допустимих напружень.
2.1. Матеріали зубчатих коліс.
Так, як до проектуючої задачі не подаються жорсткі вимоги по габаритам, то для виготовлення зубчатих коліс прийняті матеріали, подані в табл.. 2.3.
Таблиця 2.3. Матеріали зубчатих коліс
Матеріал | Термообробка | Границя текучості, σт МПа | Твердість НВ | |
Шестерня | Сталь 50 | Нормалізація | 380 | 180 |
Колесо | Сталь 40 | Нормалізація | 340 | 854 |
2.2. Допустимі контактні напруження.
|
|
Де НВ – твердість поверхні зубів по Брінеллю
Де Dp – кількість робочих днів в році;
Рс – кількість років служби;
Tзм – час зміни;
Кзм – кількість змін в сутки.
Тоді
Для легкого режиму навантаження КHZ = 0.06 – коефіцієнт інтенсивності режиму навантаження [10, ст.. 59].
Тоді
2.3. Допустимі напруження при згині
Де - границя витривалості зубів при згині, що відповідає базі досліджень, МПа;
- коефіцієнт довговічності;
- коефіцієнт реверсивності навантаження,
= 1,0;
2.4. Допустимі граничні навантажені напруження.
2.5. Допустимі граничні напруження при згині
3. Визначення геометричних розмірів
3.1. Міжосьова відстань.
Де Ка – розрахунковий коефіцієнт, Ка=4950 Па1/3;
U – непередбачене число;
Мш – номінальний обертовий момент на валу шестерні, Нм;
ψва – коефіцієнт ширини зубчастого вінця колеса, ψва=0,3;
Кнβ - коефіцієнт ширини зубчастого вінця колеса по ділильному діаметру шестерні.
Приймаємо Кнβ=1,15
, тоді
3.2. Визначення модуля зубів
Zк=u* Zш=5*20=100, тоді
Приймаємо mn=34 мм.
3.3. Геометричний розрахунок передачі
|
|
3.3.1. Міжосьова відстань
3.3.2. Розміри шестерні:
- Ділильний діаметр:
- Діаметр вершини зубів:
- Діаметр впадин:
- Ширина:
3.3.3. Розміри колеса:
- Ділильний діаметр:
- Діаметр вершини зубів:
- Діаметр впадин:
- Ширина:
4. Перевірковий розрахунок передачі
4.1. Розрахунок на контактну втому:
Приймаємо Кyv = 1.0, табл.. 3.4., [13]:
Так як σн=735 МПа, лежить в межах (0,8…0,9)*[ σн], то змінюємо ширину колеса, і приймаємо аш=2000 мм, а
Тоді , умова виконується.
Ширину шестерні приймаємо
4.2. Розрахунок на контактну міцність.
4.3.
4.4. Розрахунок на втому при згині
Умови виконуються.
4.5. Розрахунок на міцність при згині
Умови виконуються.
5. Визначення сил в зачепленні.
- Колове зусилля:
- Радіальне зусилля:
- Осьове зусилля
ІІІ. Технологічна частина
Любу деталь можна виготовити різними способами. Наприклад, деталь призматичної форми можна обробити на стругальному, фрезерному і токарному станках, деталь циліндричного перерізу – на токарних, фрезерних, стругальних і навіть на свердлильних станках.
При наявності станків всіх типів виготовлення циліндричної деталі будуть проектувати на токарному верстаті, а призматичної на – фрезельному або стругальному верстатах. Але не завжди легко і просто визначити, на верстаті якого типу виготовити ту чи іншу деталь. Іноді необхідно розрахувати, на якому верстаті економічно доцільно працювати, буде затрачено менше часу на виготовлення деталі.
|
|
Норми часу при машинній обробці визначають методом розрахунку. Розрахувати можна норми для верстатних і зварювальних робіт, визначивши основний час. Інші елементи норми часу розраховують по відповідним таблицям.
Перш чим приступити до виготовлення чи ремонту деталі, необхідно завжди подумати за технологію, вирішити, на якому обладнання, яким інструментом і з якими режимами будуть оброблювати деталь.
При вирішенні цих питань потрібно шукати найбільш раціональні, економічні способи обробки.
Ефективність роботи залежить від вибору пристроїв для кріплення деталі. Швидкість установки і вибірка деталі. Швидкість установки і вибірка деталі на верстаті особливо важлива в одиничному виробництві, де основний (машинний) час, в основному незначний, а допоміжний, на встановлення деталі, іноді більший машинного часу.
Технологічний процес виготовлення вала редуктора складається з таких операцій: свердлильна, токарна, фрезерна, шліфувальна і термічна обробка.
|
|
Технологічний процес – части на виробничого процесу, яка містить цілеспрямовані дії по зміні і визначенні складу предмету праці.
Одиничний технологічний процес – це процес виготовлення чи ремонту виробу одного найменування типорозміру і виконання, незалежно від типу виробництва.
Технологічна енергія – кінцева частина технологічного процесу, яка виконується на одному робочому місці.
Технологічний перехід – кінцева частина технологічної операції, яка виконується одними і тими ж засобами технологічного оснащення при постійних технологічних режимах і установках.
Установа – частина технологічної операції , яка виконується при незмінному закріпленні оброблювальних заготовок.
Свердлильна операція
Для свердління центровочних отворів використовують свердло П15М5 діаметром 15 мм. Приймаємо подачу: S = 0,15 мм/об, [9, ст. 25]
Швидкість різання:
де Cv = 7,0; у = 0,40; g = 0,40; m = 0,2; [15, ст. 278]
Т = 25 хв, [15, ст.. 279, табл. 70];
де Кmv – коефіцієнт, що враховує оброблюваний матеріал;
Кmv = 0,95 [9, табл. 3];
Ккv = 0,9 [9, табл. 5];
Ккv = 1,0 [9, табл. 6];
Частота обертання
по паспорту верстата приймаємо п = 710 об/хв.
Уточнюємо швидкість обертання.
Основний машинний час.
де Lр розрахункова довжина, мм; п - частота обертання свердла, об/хв.;
S – подача на один оберт, мм/об.
Загальний основний час, що необхідний свердління двох отворів рівний:
Токарна операція
Визначаємо глибину різання:
обробку виконуємо за 8 проходів.
Вибираємо подачу:
S = 0,3 мм/об, [15, ст. 256, табл. 11].
Визначаємо швидкість різання.
,
де Кv, Cv – емпіричні коефіцієнти , Cv = 420 [9, табл. 17];
x, y, m – показники степеня, х = 0,15; y = 0,20; m = 0,20 [9, табл. 17].
,
Кmv ,Ккv, Ккv емпіричні коефіцієнти;
Кmv = 0,95 [9, табл. 3]; Ккv = 0,9 [9, табл. 5]; Ккv = 1,0 [9, табл. 6];
Т – стійкість інструменту при безперервній роботі, Т = 45 кВ
Визначаєм частоту обертання:
де D – діаметр заготовки, мм.
по паспорту верстата приймаємо найближче значення пр = 200 об/хв.
Уточнюємо дійсну швидкість різання:
Знаходимо зусилля різання:
де Ср – постійна величина, Ср = 360; x, y, n – показники степеня, x = 1,0;
y = 0,75; n = -0,15, [15, ст.268, табл. 22]
Кр – поправочний коефіцієнт.
де, - коефіцієнти, що враховують фактичні умови різання;
Знаходимо потужність різання:
Визначаєм основний машинний час:
де Lр – розрахункова довжина, мм; і – кількість проходів.
Глибина різання і подача:
- подача : S = 0,3 мм/об [9, табл. 11];
Швидкість різання:
Частота обертання:
по паспорту приймаємо пф = 500 об/хв.
Встановлюємо швидкість різання:
Основний машинний час:
Фрезерна операція
Режим різання при роботі шпоночними фрезами з матеріалом ріжучої частини Р15М5:
- діаметр фрези – 15 мм [15, ст.268, табл. 38];
- глибина фрезерування – 7 мм;
- подача на поздовжній рух – St = 0,02 мм/зуб
Визначаємо швидкість різання:
Визначаємо частоту обертання:
з паспорта верстата приймаємо пф =500 об/хв.
Уточнюємо швидкість різання:
Основний машинний час:
де Sв – вертикальна подача, мм/об;
Sа.д. – повздовжня подача, мм/зуб;
D – діаметр фрези, мм.
Термічна обробка
Термообробка складається з відпалу, сортування, відпуску і нормалізації.
Використовуємо термопіч.
Відпал і нормалізація проводиться певним чином.
- Відпал: t = 880°; T = 4 год; - повільне охолодження в печі; Vосн = 15…100 °С/год;
- Нормалізація: t = 850°; T = 4 год; - охолодження на повітрі;
- Гартування: t = 950°; T = 4 год; - охолодження в мінеральному маслі; Vосн = 100 °С/год; АВ = 350…450.
- Відпуск призначений для досягнення певної твердості
t = 500°; високотемпературний відпуск T = 5 год;
АВ = 250…350. Повільне охолодження.
Шліфувальна операція
Розробку режимів шліфування проводять із встановленням характеристики інструменту. Вибираємо шліфувальний круг типу ПП – плоскошліфувальний, для зовнішнього шліфування, ГОСТ 2424 – 83,
Ra = 1,25; В = 70 мм; зернистість – 10-40 мм.
- Швидкість обертання круга – Vкр = 70 м/с.
- Швидкість обертання заготовки, Vд = 25 м/с.
- Глибина шліфування, t = 0,02 мм
- Повздовжня подача, Sпз = 0,8 мм/об.
Визначаєм частоту обертання деталі:
Основний робочий час:
де Кy – коефіцієнт зачисних ходів, Кy = 1,2…1,7 [15, ст. 273.]
Дата добавления: 2019-09-02; просмотров: 96; Мы поможем в написании вашей работы! |
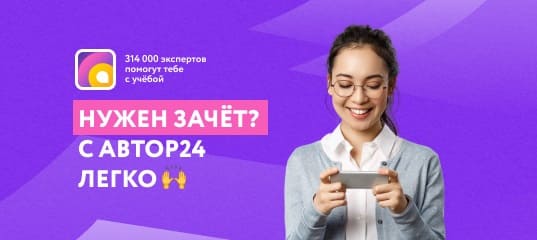
Мы поможем в написании ваших работ!