Рекомендации по конструированию валов и осей
· каждая насаживаемая на вал деталь должна проходить до своей посадочной поверхности свободно во избежание повреждения других поверхностей (рис.5, а).
· торцы валов и осей и их уступы выполняют с фасками (ГОСТ 10948-64) для удобства насадки деталей и соблюдения техники безопасности (см. рисунок 1);
· в тяжело нагруженных валах или осях для снижения напряжений в местах посадочных поверхностей рекомендуется перепады ступеней выполнять минимальными с применением галтелей переменного радиуса (см. рисунок 3);
· при прессовых посадках трудно совместить шпоночную канавку в струбцине со шпонкой вала. Для облегчения сборки на посадочной поверхности вала предусматривают небольшой направляющий цилиндрический участок с посадкойf7(см. рисунок 1);
· для уменьшения номенклатуры резцов радиусы галтелей, углы фасок ширину проточек на одном валу или оси рекомендуется выполнять одинаковыми. Если на валу несколько шпоночных пазов, то их располагают на одной образующей вала (см. рисунок 5, а);
· выбор рациональной формы вала или оси зависит от масштаба производства. При единичном производстве валы и оси изготавливают преимущественно из круглого проката, поэтому для уменьшения механической обработки принимают простую форму без буртиков (см. рисунок 5, а). При массовом производстве валы и оси изготавливают из специальных поковок, которые позволяют применять упорные бурты (см. рисунок 1);
|
|
· для увеличения изгибной жесткости валов и осей рекомендуется располагать насаживаемые детали ближе к опорам.
Способы и приемы повышения усталостной прочности валов и осей.
Поведение металлических материалов при циклическом нагружении обусловлено многими факторами [1]: 1) структурным состоянием, термической обработкой (размер зерна; размер, форма и количество выделений или различных фаз; плотность дислокаций и их распределение) и, соответственно, от его механических свойств; 2) состоянием поверхностного слоя (химический состав, механические свойства и структура; остаточные напряжения, зависящие от вида механической или химико-термической обработки); 3) температурой и средой испытания; 4) масштабным фактором; 5) частотой нагружения; 6) концентрацией напряжений; 7) асимметрией цикла нагружения; 8) вида напряженного состояния; 9) контактного трения.
В основе повышения износостойкости и усталостной прочности деталей лежит воздействие на рабочую поверхность деталей и элементы кристаллической решетки металла путем применения различных видов обработок.
Слесарно-механическая обработка.
Эта обработка применяется для устранения задиров, рисок, наработки и других дефектов поверхности, а также для получения необходимой чистоты поверхности. Чем выше чистота поверхности, тем выше износостойкость детали. Наиболее часто для этих целей применяют шабрение, шлифование, полирование, хонингование, алмазное выглажывание.
|
|
Термическая обработка (закалка).
Этот способ применяется для повышения твердости поверхности детали. Для уменьшения хрупкости и снятия закалочных напряжений производят отпуск. Сочетание закалки с действием магнитного поля увеличивает прочность стали, так как кристаллы мартенсита принимают одну ориентацию во всех зернах. Поверхностная закалка применяется для повышения прочности и износостойкости деталей, работающих при ударной нагрузке, при этом основной металл детали остается незакаленным.
Химико-термическая обработка.
Это технологический процесс, при котором происходит изменение химического состава, структуры и свойств поверхности металла. Обработка включает в себя азотирование, фосфатирование, анодирование, цианирование, сульфидирование, борирование, цементацию.
Гальваническая обработка.
Пористое хромирование рабочей поверхности производится в электролитической ванне. Вначале наносится слой хрома толщиной 0,15… 0,20 мм. Пористость создается переключением тока на обратный на 15…20 мин. Обратный ток вызывает выпадение частиц хрома с образованием мельчайших пор. Такая пористость улучшает смазку трущихся поверхностей и повышает срок службы деталей.
|
|
Механическое упрочнение.
Для механического упрочнения деталей применяют накатку, простое или ультразвуковое виброобкатывание, дробеструйную и гидроструйную обработку. Накатка шеек и галтелей осуществляется роликами, которые прижимают к поверхности детали. Трехроликовое приспособление исключает деформацию детали и разгружает суппорт и ходовой винт станка. Накатка выполняется за три оборота при 12… 15 об / мин. В процессе накатки в зону контакта подается смесь масла с керосином или полимерная жидкость. Одновременно с упрочнением поверхности повышается и ее чистота.
14. Особенности работы ригельных планок (крюковая подвеска).
Крюковая подвеска состоит из двух боковых щек, соединенных между собой распорными трубками и стяжными болтами. В верхней части щек на неподвижно закрепленной с помощью ригельных планок оси вращаются один или несколько канатных блоков. На некоторых кранах для обеспечения минимальной длины подвески применяют крюк с длинным хвостовиком, который крепят непосредственно на оси блоков. Такая подвеска называется укороченной. На нижней части подвески на траверсе закрепляется грузовой крюк с помощью гайки. Траверса может свободно вращаться в отверстиях боковых щек. Крюк, установленный на шарикоподшипниках помимо вращения вокруг оси может еще качаться вместе с траверсой, что облегчает строповку и ориентирование грузов. В зависимости от числа осей крюковые подвески бывают одно-, двух- и трехосными (рис. ).
|
|
Различают однорогие и двурогие грузовые крюки. Их изготавливают ковкой или штамповкой из малоуглеродистой стали 20, что исключает внезапное разрушение крюка.
На грузовом крюке указывается номер крюка по государственному стандарту, товарный знак, заводской номер крюка, наименование завода- поставщика, номер плавки, год изготовления. Без маркировки устанавливать крюк на кран нельзя.
Крюки бракуются в случаях, если:
· крюк не вращается на траверсе;
· отогнут рог крюка;
· износ крюка в зеве превышает 10 %;
· нет клейма ОТК;
· имеются трещины.
Дата добавления: 2019-07-15; просмотров: 585; Мы поможем в написании вашей работы! |
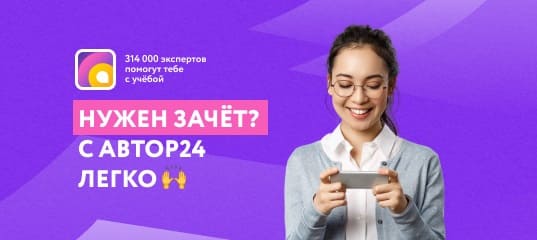
Мы поможем в написании ваших работ!