Основное правило измельчения. Особенности измельчения растительных материалов. Назначение и использование измельчения в промышленной технологии.
Интенсивность многих технологических процессов зависит от величины поверхности обрабатываемых твердых материалов; при этом увеличение их поверхности путем уменьшения размеров кусков повышает скорость процесса, а также увеличивает выход и повышает качество конечного продукта.
Процесс уменьшения размеров кусков твердых материалов называется дроблением или измельчением; часто под дроблением понимают уменьшение только крупных кусков. Процесс измельчения мелких кусков называется размолом.
Измельчение может производится: а) путем раздавливания - то есть приложения механической силы сверху прогрессивно; б) , в) путем раскалывания - механическая сила прикладывается сверху и снизу внезапно; г) разламывание - механическая сила действует сверху, между двумя нижними силами; д) резание - механическая сила прикладывается сверху рывком. Поверхности острые, режущие. е) — распиливание - разрушающая сила прикладывается зубьями под углом прогрессивно; ж) — истирание, механическая сила прикладывается сверху и со стороны прогрессивно; з) , и) — жесткий удар, свободный удар, - механическая сила прикладывается сверху рывком.
Способ измельчения выбирают с учетом физических свойств измельчаемого материала, в первую очередь его твердости и характера излома.
Для материалов, отличающихся большой твердостью, более эффективными являются удар и раздавливание, для материалов вязких предпочтительнее истирание, для хрупких-раскалывание.
|
|
При измельчении материалов необходимо соблюдать основное правило: не измельчать ничего лишнего.
Из этого правила вытекают следующие положения:
- Измельчение любого материала необходимо вести только до той степени измельчения, которая требуется для дальнейшей его переработки или применения; частицы материала, измельченные до требуемого размера, должны немедленно удаляться из машины; процессу измельчения должен предшествовать процесс грохочения (просеивания).
2. Измельчение по возможности должно быть «свободным», т. е. не должно осложняться побочными процессами; только преодоление сил сцепления между частицами измельчаемого материала является полезной работой, затрачиваемой на измельчение.
3. При большой степени измельчения следует вести процесс в несколько приемов.
Траворезки предназначены для измельчения растительного материала. Перед измельчением растительное сырье необходимо очистить от земли, пыли и других посторонних примесей. Если измельчаются хрупкие растительные материалы, их необходимо сначала увлажнить (на пример, листья). Увлажняют водой в хорошо закрывающихся собудах, ящиках. После увлажнения листья легко разрезываются и не образуют крошку. Твердые корни перед измельчением также размягчают с помощью воды. После измельчения сырье необходимо сразу высушить, так как при хранении во влажном состоянии оно может быстро заплесневеть и потерять свои лекарственные качества.
|
|
24. Криоизмельчение, его влияние на качество измельченного материала. Измельчение в жидких и вязких средах.
Сегодня из всех существующих способов измельчения одним из самых перспективных является криодробление (от англ. Cryo-grincling). Эта технология дает возможность предотвратить разрушение БАВ в процессе измельчения. Являясь революционной технологией в области фитотерапии, такой способ измельчения впервые был применен в 1982 году. Криодробление представляет собой процесс измельчения сырья до пылевидного состояния при низких температурах в среде инертного газа. Важнейшее преимущество криоизмельчения перед всеми другими видами измельчения в том, что оно позволяет полностью сохранять ЬАВ растительного материала.
Процесс производтсва начинается с быстрого замораживания сырья в криотуннелях в присутстуии жидких азота или аргона, так как хладоновые компрессорные замораживатели, использующие длительный обдув сырья холодным воздухом, приводят к значительным потерям низкомолекулярных компонентов. Затем сырье подвергается многоэтарной криогенной переработке. На первом этапе проводится его криогенное измельчение в специально сконструированных криогенных мельницах в парах жидкого азота при теипературах от (-100) до (-200) 0С до частиц размером 20-30 мкм. Криоизмельчение резко увеличисает удельную поверхность перерабатываемых, фракций и повышает эффективность последующего этапа переработки, криоизмельченное замороженное сырье на две фракции: фодную и сухую.
|
|
Измельчение в жидких и вязких средах
позволяет повысить эффективность процесса при получении тонкодисперсного материала. Осуществляется в коллоидных мельницах, роторно-пульсационных аппаратах и барабанных(шаровых) мельницах с использованием принципов удара и истирания.
Наибольшая эффективность наблюдается при соотношении твердой и жидкой фазы в пределах от 1:2 до 1:6 в результате материал измельчается до 1 мкм.
Коллоидные мельницы бывают различных конструкций:
1. Ударная коллоидная мельница (рис. 3.70).
Рис. 3.70. Устройство коллоидной мельницы ударного типа.
|
|
1 - корпус; 2 - диск; - пальцы.
Ударная коллоидная мельница представляет собой типичный дисмембратор, т.е. мельницу с одним вращающимся диском. На неподвижном и подвижном дисках укреплены пальцы концентрическими рядами. У основания мельницы укреплены два патрубка. В первый патрубок подается смесь жидких и порошкообразных компонентов или эмульсия с крупно измельченной твердой фазой. Из второго патрубка вытекает высокодисперсная эмульсия-суспензия. Измельчение частичек фазы происходит при вращении диска в результате гидравлических сил, возникающих от многочисленных ударов пальцев по жидкости.
2. Фрикционные коллоидные мельницы (рис.3.71).
Рис. 3.71. Устройство фрикционной коллоидной мельницы.
1 - основание с коническим гнездом; 2 - отверстие в гнезде; 3 - ротор; 4 - микрометрический винт.
Работают на принципе истирания между гладкими и рифлеными поверхностями, а не удара. Коллоидная мельница с гладким конусом имеет следующее устройство. В вогнутом конусообразном статоре на небольшом от него расстоянии точно по центру располагается выпуклый конусообразный ротор. Расстояние между статором и ротором регулируется микрометрическим винтом и составляет не более 0,05 мм. При вращении ротора через отверстие в центре статора всасывается эмульсия и движется к периферии. Крупные частички истираются. Измельченная эмульсия-суспензия вытекает через отверстие в корпусе. Коллоидная мельница с рифлеными поверхностями измельчает не только истиранием, но и ударами вихревых потоков, возникающих в жидкости от неровной поверхности.
Рис. 3.72. Устройство роторно-бильной коллоидной мельницы.
1 - корпус; 2 - штуцер для ввода суспензии; 3 - ротор; 4 - биллы; 5 - контрударники; 6 - штуцер для вывода готовой продукции.
В роторно-бильной коллоидной мельнице гетерогенная система подается через штуцер 5 в корпус 1. Попадает под билы 4, укрепленные на роторе 3 и неподвижные контрударника 5. Ряды бил ротара расположены между рядами контрударов. Измельченная эмульсия-суспензия вытекает из штуцера 6.
Рис. 3.73. Устройство виброкавитационнои коллоидной мельницы.
1 - корпус; 2 - статор; 3 - ротор; 4 - канавки дна поверхности ротора и статора; 5 - штуцер для ввода суспензии; 6 - штуцер для вывода готовой продукции.
На статоре 2 и роторе 3 имеются продольные канавки 4. Суспензия через штуцер 6 выводится из мельницы. При вращении ротора со скоростью 18 тыс. об/мин. суспензия, двигаясь от канавок ротора к канавкам с статера приобретает высокочастотные колебания, близкие к ультразвуку и диспергируется до размера частиц дисперсной фазы 1 мкм.
Наиболее широкое распространение при диспергировании эмульсий, суспензий, а также линиментов и мазей получили роторно-пульсационные аппараты, сокращенно РПА. Они бывают погруженного типа, вмонтированного в аппараты и проточного типа.
РПА проточного типа изображен на рис. 3.74.
Рис. 3.74. Устройство РПА проточного типа.
1 — приводной вал; 2 - ротор; 3 - патрубок выхода суспензии; 4 -крышка-статор; 5 - патрубок входа.
В корпусе РПА вращается ротор 2, который как и статер выполнен в виде соосных и перфорированных цилиндров. Отверстия в роторе и статере могут быть круглой, овальной или другой формы. На роторе имеется четыре радиальные лопасти. Суспензия подается в РПА через патрубок 5 и выводится через патрубок 3.
В РПА измельчение дисперсной фазы как и в коллоидных мельницах происходит за счет ударов и растираний при высокой частоте гидравлических ударов.
Классификация твердых материалов. Основы воздушной и гидравлической классификации измельченного материала. Механическая классификация (просеивание). Сита и ситовой анализ. Материалы и виды сеток (плетеные, штампованные, колосниковые). Стандарты и нумерация сит.
Различают три вида классификации материалов:
1. Ситовая классификация или механическая классификация основана на разделении смеси фракции при помощи сита или грохота. Эта классификация часто называется просто просеиванием или грохочением. В промышлености термины (понятия) просеивание и грохочение отождествляются. В галеново-фармацевтическом производстве под просеиванием понимают разделение частиц размером менее 3 мм, а под грохочением - разделение частиц размером более 3 мм.
2. Гидравлическая классификация - разделение смеси на фракции частиц, обладающих одинаковой скоростью падения в воде.
3. Воздушная классификация или воздушная сепарация – разделение смеси на фракции зерен, обладающих одинаковой скоростью падения в воздухе.
Классификация гидравлическая и воздушная основаны на различной скорости осаждения частиц различного диаметра и размера под действием силы тяжести. Существует много конструкций таких классификаторов.
Один из них изображен на рис. 2.15.
Рис. 2.15. Воздушный классификатор.
В фармацевтическом производстве в основном применяется процесс просеивания для разделения измельченного материала на фракции с одинаковым диаметром частиц.
Просеивание осуществляют с помощью сит. Сито - это плоская сетка или лист, снабженный отверстиями, соответствующая величина которых обеспечивает проход частиц требуемой величины.
При просеивании вместе с частицами оптимального размера проходят и частицы меньшего размера. Для отделения последних материал вновь просеивают, но теперь уже через сито с меньшими отверстиями, пропускающими только мелкие частицы.
Иногда измельченный материал просеивают через два сита сразу, причем сита расположены один под другим и имеют различные размеры отверстий. Эффект достигается тот же.
Сита изготавливают из шелковых или капроновых нитей, из стальной проволоки, из листового металлического полотна. Во всех случаях материалы для изготовления сит нужно использовать такие, которые не вступают в химическое взаимодействие с просеиваемым материалом. Кроме того, сита должны обладать определенной прочностью.
Основной частью просеивающих машин являются ситовые полотна, которые бывают плетенными или штампованными.
Плетеные выполняются из стальной, медной или латунной проволок, а также из шелковых и капроновых нитей, они имеют квадратные или прямоугольные отверстия шириной от 10 до 0,14 мм. Каждое ситовое полотно характеризуется номером и сечением отверстия в свету в миллиметрах.
Живое сечение - это отношение площади всех отверстий ситового полотна к общей площади в процентах. Чем больше живое сечение сита, тем выше его производительиость. Живое сечение плетеных сит составляет около 70%.
Штампованные (противные) сита - это решета из стальных листов c штампованными отверстиями. Живое сечение штампованных сит -около 50%.
Классифицируют сыпучие материалы при помощи набора сит с последовательно уменьшающимся размером отверстий.
Для выполнения ситового анализа на указанных ситах просеивают среднюю пробу материала. Затем оставшийся на каждом сите материал и частицы. прошедшие через нижнее сито, взвешивают. Отношение полученных количеств к исходной навеске вещества дает содержание различных фракций зерен в материале.
Производительность сит характеризуется КПД, т.е. отношением массы зерен, прошедших через сито, к массе зерен такого же размера, но содержащихся в исходной смеси.
На производительность просеивания влияют толщина слоя просеиваемого материала на сите, форма отверстий и частиц, скорость перемешивания материала и влажность.
Стандарты сит
Не должно быть отверстий, размер которых превышает номинальный размер более, чем на величину Х.
Средний размер отверстия не должен отклоняться от номинального размера более чем на величину +-Y.
Не более 6% общего числа отверстий могут иметь размеры между номинальный +Х» и «номинальный +Z».
Дата добавления: 2019-07-15; просмотров: 884; Мы поможем в написании вашей работы! |
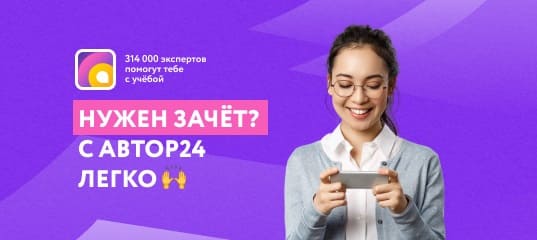
Мы поможем в написании ваших работ!