Описать химические процессы, протекающие в процессе производства стали выбранным способом.
Вариант 3
1. Расшифруйте марки заданных сплавов т.е. указать их наименование, примерный химический состав, область применения и свойства. Для сталей дополнительно укажите класс, подкласс по химическому составу и класс качества по содержанию вредных примесей – серы и фосфора.
Варианты задания – табл.П.1. (приложение 1).
2. Выбрать плавильный агрегат для производства заданной марки стали в зависимости от состава шихты и условий производства, используя блок-схему. Изобразить схему устройства выбранного агрегата, описать работу агрегата. Рассчитать мощность, выбрать тоннаж, определить количество сталеплавильных агрегатов.
Описать химические процессы, протекающие в процессе производства стали выбранным способом.
Вариант задания – табл. П.2.(приложение Б).
3. Опишите последовательность и приведите схему изготовления литейной формы одним из методов машинной формовки. Приведите эскизы металлических модельных плит, стержневого ящика и собранной литейной формы.
4. Перечислите виды листового проката. Перечислите прокатные операции технологического процесса получения листового проката, начиная с указания исходного материала.
5. Описать сущность процесса указанного способа сварки заданной детали. Зарисовать эскиз детали, определить тип соединения. Выбрать диаметр электрода или электродной проволоки. Рассчитать параметры режима указанного вида сварки.
|
|
Варианты задания – табл. П.3.(приложение В).
6. Приведите элементы токарного проходного резца, координатные плоскости для определения углов резца, углы токарного резца.
Расшифруйте марки заданных сплавов т.е. указать их наименование, примерный химический состав, область применения и свойства. Для сталей дополнительно укажите класс, подкласс по химическому составу и класс качества по содержанию вредных примесей – серы и фосфора.
Варианты задания – табл.П.1. (приложение 1).
Сталь 55, чугун ВЧ100, сталь 9ХВГ, сталь ШХ15, сплав БрБ2
Сталь 55.Сталь конструкционная углеродистая качественная.
Химический состав в % материала 55, ГОСТ 1050 – 88:
C | Si | Mn | Ni | S | P | Cr | Cu | As |
0.52 - 0.6 | 0.17 - 0.37 | 0.5 - 0.8 | до 0.3 | до 0.04 | до 0.035 | до 0.25 | до 0.3 | до 0.08 |
Применение: зубчатые колеса, прокатные валки, штоки, тяжелонагруженные валы, оси, бандажи, малонагруженные пружины и рессоры, лемехи, пальцы звеньев гусениц и муфты сцепления коробок передач, корпуса форсунок и другие детали, работающие на трение.
Свойства:
Термообработка: Нормализация и высокий отпуск Температура ковки, °С: начала 1240, конца 800. Заготовки сечением до 400 мм охлаждаются на воздухе. Твердость материала: HB 10 -1 = 212 - 248 МПа Температура критических точек: Ac1 = 725 , Ac3(Acm) = 755 , Ar3(Arcm) = 750 , Ar1 = 690 , Mn = 320 Свариваемость материала: не применяется для сварных конструкций. КТС с последующей термообработкой. Флокеночувствительность: малочувствительна. Склонность к отпускной хрупкости: не склонна. Обрабатываемость резанием: в нормализованном состоянии при HB 212-225 К υ тв. спл=1,0 и Кυ б.ст=0,65. По классификации Сталь 55 конструкционная углеродистая качественная. |
Чугун ВЧ100. Чугун с шаровидным графитом
|
|
Химический состав в % материал ВЧ100, ГОСТ 7293 – 85:
C | Si | Mn | Ni | S | P | Cr | Cu |
3.2 - 3.6 | 3 - 3.8 | 0.4 - 0.7 | до 0.8 | до 0.01 | до 0.1 | до 0.15 | до 0.6 |
Применение: для изделий с высокой прочностью и удовлетворительной пластичностью.
Механические свойства при Т=20 o С материала ВЧ100:
Сортамент | Размер | Напр. | sв | sT | d5 | y | KCU | Термообр. |
- | мм | - | МПа | МПа | % | % | кДж / м2 | - |
Отливки, ГОСТ 7293-85 | 1000 | 700 | 2 |
Твердость ВЧ100 , ГОСТ 7293-85 | HB 10 -1 = 270 - 360 МПа |
Сталь 9ХВГ. Сталь инструментальная легированная
Химический состав в % материала 9ХВГ, ГОСТ 5950 – 2000:
C | Si | Mn | Ni | S | P | Cr | W | Cu |
0.85 - 0.95 | 0.1 - 0.4 | 0.9 - 1.2 | до 0.4 | до 0.03 | до 0.03 | 0.5 - 0.8 | 0.5 - 0.8 | до 0.3 |
Применение: резьбовые калибры, лекала сложной формы, сложные весьма точные штампы для холодных работ, которые при закалке не должны подвергаться значительным объемным изменениям и короблению.
|
|
Свойства:
Твердость материала: HB 10 -1 = 255 МПа
Температура ковки °С: начала 1070, конца 860. Охлаждение замедленное.
Температура критических точек: Ac1 = 750 , Ac3(Acm) = 940 , Ar1 = 710 , Mn = 210
Свариваемость материала: не применяется для сварных конструкций.
Флокеночувствительность: чувствительна.
Склонность к отпускной хрупкости: малосклонна.
Обрабатываемость резанием: в горячекатанном состоянии при HB 235 и σв=760 МПа, К υ тв. спл=0,75 и Кυ б.ст=0,35
По классификации сталь 9ХВГ инструментальная легированная качественная.
Сталь ШХ15. Сталь конструкционная подшипниковая.
Химический состав в % материала ШХ15, ГОСТ 801 – 78:
C | Si | Mn | Ni | S | P | Cr | Ti | Cu | O |
0.95 - 1.05 | 0.17 - 0.37 | 0.2 - 0.4 | до 0.3 | до 0.02 | до 0.027 | 1.3 - 1.65 | до 0.01 | до 0.25 | до 0.0015 |
Примечание: Никель + Медь до 0.5 %. В стали ШХ15-Ш доля серы до 0.01%, фосфора - до 0.025% |
Применение: шарики диаметром до 150 мм, ролики диаметром до 23 мм, кольца подшипников с толщиной стенки до 14 мм, втулки плунжеров, плунжеры, нагнетательные клапаны, корпуса распылителей, ролики толкателей и другие детали, от которых требуется высокая твердость, износостойкость и контактная прочность.
|
|
Свойства:
1.Повышенная твердость поверхности. Подшипники и режущая кромка лезвия при эксплуатации подвергаются износу. Для того чтобы поверхность изделия не реагировала на механическое воздействие существенно повышается показатель твердости. 2.Износостойкость определяет то, что поверхность не реагирует на трение и другое воздействие. Металл ШХ9 и ШХ15 характеризуются высокой износостойкостью, поэтому создаваемые изделия могут прослужить в течение длительного периода.
3.Устойчивость к коррозии также можно назвать привлекательным качеством рассматриваемого металла. Ржавчина, которая появляется на поверхности, снижает срок службы изделия. Сталь ШХ15 не относится к нержавейкам. Поэтому на высокую устойчивость к высокой влажности и химически агрессивной среде рассчитывать не следует.
4.Стойкость к смятию. Точечное воздействие высокой нагрузки может привести к образованию вмятины, но рассматриваемый металл характеризуется высокой устойчивостью к подобному воздействию.
5.Пластичность и вязкость также учитываются при создании различных изделий.
6.Структура прекрасно поддается термической обработке. Как правило, проводится закалка после придания требуемой формы и размеров. Кроме закалки выполняется отжиг и ковка, которые также могут улучшить структуру материала.
7.Склонность к отпускной хрупкости определяет то, что после закалки могут появится структурные дефекты. Они могут повысить хрупкость получаемого изделия.
8.Плохая свариваемость. Повысить твердость смогли за счет повышения концентрации углерода. Однако, этот химический элемент существенно усложняет процесс сварки. Как правило, для повышения качества сварного шва проводится подогрев заготовки.
По классфикации сталь ШХ15 конструкционная подшипниковая качественная.
Сплав БрБ2. Бронза безоловянная, обрабатываемая давлением.
Химический состав в % материала БрБ2, ГОСТ 18175 – 78:
Fe | Si | Ni | Al | Cu | Pb | Be | Примесей |
до 0.15 | до 0.15 | 0.2 - 0.5 | до 0.15 | 96.9 - 98 | до 0.005 | 1.8 - 2.1 | всего 0.5 |
Примечание: Cu - основа; процентное содержание Cu дано приблизительно
Бериллиевая бронза. Высокая прочность и износостойкость; высокие пружинные свойства; хорошие антифрикционные свойства; средняя электропроводность и теплопроводность; очень хорошая деформируемость в закаленном состоянии.
Применение: пружины, пружинящие детали ответственного назначения, износостойкие детали всех видов, неискрящие инструменты.
Свойства:
1.Высокая упругость. Этот параметр определяет то, что изготовленные детали из рассматриваемого сплава могут выдерживать воздействие различной деформационной нагрузки, направленной перпендикулярно или под другим углом относительно оси.
2.При соударении изделий не появляются искры. Данный эффект проявляется при применении обычной стали или некоторых других материалов. Подобное качество позволяет применять бериллиевой бронзы для изготовления ответственных деталей, которые работают в сложной, легко воспламеняемой среде.
3.Высокая электропроводность бериллиевых бронз определяет большое распространение материала. Однако стоит учитывать, что показатель электропроводности чуть ниже чем у чистой меди.
4.Повышенная теплопроводность обуславливает применение материала при изготовлении отводящих тепло элементов. Примером можно назвать изготовление охладительных систем различных компьютеров. Высокая стоимость бериллиевой бронзы не позволяет ее использовать при производстве отопительных систем.
5.Не стоит забывать и о том, что сопротивление коррозии также высокое. Материал не реагирует на воздействие влаги, что определяет длительный срок службы при эксплуатации в сложных условиях.
2. Выбрать плавильный агрегат для производства заданной марки стали в зависимости от состава шихты и условий производства, используя блок-схему. Изобразить схему устройства выбранного агрегата, описать работу агрегата. Рассчитать мощность, выбрать тоннаж, определить количество сталеплавильных агрегатов.
Описать химические процессы, протекающие в процессе производства стали выбранным способом.
Вариант задания – табл. П.2.(приложение Б).
Вариант 3. Состав шихты, т/год: лом углеродистых сталей, 250000. Марка стали: сталь 30. Обеспеченность района энергоносителями: достаточно обеспечен электроэнергией.
Наша электродуговая сталеплавильная печь ДСП –100 имеет емкость до 100 т. Это камера из огнеупорного кирпича со съемным сводом. Для загрузки флюсов и легирующих элементов имеется окно; загрузка шихты производится сверху при снятом своде. Для выпуска стали печь имеет огнеупорный желоб. Она может наклоняться благодаря специальному механизму.
Тепло для химических реакций получается от горения электрических дуг между графитовыми электродами и шихтой. В электродуговой печи можно создать необходимую атмосферу (нейтральную, восстановительную или вакуум). Электрические параметры легко поддаются регулированию, поэтому в печи можно установить любую температуру.
Общий вид дуговой сталеплавильной печи ДСП - 100
Характеристики сталеплавильной печи ДСП – 100:
Номинальная ёмкость, т – 100. Диаметр кожуха, мм – 6900. Номинальная мощность трансформатора, кВ.А – 50000. Первичное напряжение, кВ – 38,5. Пределы вторичного напряжения, В – 573-200. Максимальный ток печи, кА – 63,6. Диаметр графитированного электрода, мм – 610. Диаметр распада электродов, мм – 1600. Ход электрода, мм – 3600. Максимальная скорость перемещения электрода, м/мин – 4,5. Диаметр ванны на уровне откосов, мм – 5600. Глубина ванны от порога, мм – 1100. Высота от порога до пят свода, мм – 2070. Масса металлоконструкций, т – 460. Удельный расчетный расход электроэнергии на расплавление твердой закалки, кВт.ч/т – 405.
Выбор основных электрических параметров дуговых сталеплавильных печей
Основным параметром, характеризующим ДСП, принято считать её номинальную ёмкость. За рубежом иногда в качестве такого параметра принимают диаметр кожуха печи, считая, что в зависимости от местных условий фактическая загрузка изменяется в широких пределах по сравнению с номинальной. Однако при проектировании печей нельзя исходить из местных условий, и поэтому, как правило, устанавливают зависимость между ёмкостью печи и её электрическими параметрами. При заданной ёмкости печи эти параметры — мощность и ступени напряжения печного трансформатора, реактивность контура, а также геометрические параметры определяют её режим и основные показатели работы.
Выбор основных электрических параметров дуговых печей сложен и неоднозначен. Печи работают в самых разных условиях, проводимые в них технологические процессы также могут быть различными. Основные показатели работы — производительность (суточная или годовая) и удельный расход электроэнергии — зависят от многих факторов, и дать аналитическое выражение для оптимальных значений этих показателей, пригодное для инженерных расчётов, не представляется возможным. Поэтому определение основных параметров дуговых печей приходится основывать на данных практики работы действующих печей и эксперимен- тальных формулах, выведенных на основе обработки статистических данных. При проектировании в первую очередь необходимо выбрать номинальную мощность печного трансформатора. Чем больше его мощность при той же ёмкости печи G, т, тем, казалось бы, больше должна быть её
производительность g, т/сут. Связь между ними имеет вид:
g=nG/(τ1+τ2+τ3), (2.1)
где n — число часов работы печи в сутки; τ1 — время простоев печи за плавку, ч; τ2 — время расплавления металла, ч; τ3 — время окислительного и восстановительного периодов, ч.
Время простоев печи τ1 складывается из времени, необходимого на слив
металла в ковш, на заправку подины и на загрузку печи шихтой, т. е. оно зависит от организации работы персонала во время этих операций и степени их механизации, но не от мощности печного трансформатора. Не зависит от мощности и время рафинирования металла, так как в этот период трансформатор загружен не полностью, и τ3 определяется только видом технологического процесса, умением и квалификацией персонала. Время же расплавления металла τ2, ч, зависит от мощности печного трансформатора:
τ2=QG/(Scosφ.ηэл—q2), (2.2)
где Q — теоретический удельный расход электроэнергии на расплав- ление металла (для стали равный около 340 кВт.ч/т с учетом тепла, аккумулированного футеровкой); S — мощность печного трансформатора, кВ.А; cosφ — средневзвешенный коэффициент мощности печного агрегата; ηэл — его электрический к. п. д.; q2 — мощность тепловых потерь печи, кВт (все — за время расплавления).
Удельные мощности печных агрегатов всё время росли по сравнению с первоначальными значениями, характерными для 30—40-х годов. Это вполне закономерно, так как одновременно происходили повышение рабочих напряжений печей, что облегчало токоподводы, улучшение качества огнеупоров, качества работы автоматики, проведение полной, механизации работы печей, а главное, значительное удешевление электроэнергии. В результате последнего электросталь стала конкурентоспособной с обычной сталью, и в дуговых печах начали плавить не только дорогие высоколегированные, но и дешёвые массовые сорта стали, для которых время, восстановительного периода короче.
Чем меньше время простоя (оно зависит от степени механизации печи) и восстановительного периода, тем больший эффект повышения производительности печи и уменьшения расхода электроэнергии может дать увеличение мощности печного трансформатора. Поэтому для современных печей, у которых среднее время восстановления уменьшено, а время простоя сведено к минимуму, повышение удельной мощности вполне оправдано.
Печи, плавящие сталь для фасонного литья, имеют сравнительно короткий период рафинирования, особенно если они работают кислым процессом. Следовательно, для них повышение мощности должно дать больший эффект, чем для печей, выплавляющих сталь для слитков. Действительно, даже в старых сериях удельные мощности этих печей достигали (600—500) кВт/т, а в новой серии они составляют еще большую величину, доходя до (1000—800) кВт/т. В отличие от них более крупные печи, выплавляющие сталь на слиток, ёмкостью (25—100)т имели значительно меньшие удельные мощности (400—300) кВт/т.
В последние годы в связи с резким увеличением выплавки электростали, охватившей массовые сорта, появились печи ёмкостью 100 т и более сверхвысокой мощности, с удельной мощностью (500— 600) кВт/т и более. В этих печах начальный период расплавления проводится на более высоком вторичном напряжении, с тем чтобы получить достаточный диаметр колодцев. После расплавления основной массы шихты печи переводят на пониженное напряжение, на работу с более короткой дугой, чтобы сохранить работоспособность футеровки. При этом для сохранения мощности печей увеличивают их ток. Всё это приводит к резкому увеличению номинальной мощности печной установки. Это оказывается целесообразным, так как в этого рода печах период восстановления при выплавке массовых сталей оказывается сокращённым, а иногда вообще выносится за пределы печного агрегата.
Существенными электрическими параметрами электродуговой печной установки являются величина и число ступеней вторичного напряжения печного трансформатора. Первичное напряжение трансформатора определяется напряжением питающей цех высоковольтной подстанции. Обычно трансформаторы малых печей питаются от сетей напряжения (6—10) кВ, а более крупные — (35—110) кВ.
Схема расположения печи
1 – стойка; 2 – шахта; 3 – трансформатор; 4 – выпрямитель; 5 – электрододержатель; 6 – графитированный электрод; 7 – механизм для подъема свода; 8 – портал; 9 – центральная часть свода; 10 – водоохлаждаемый свод; 11 – водоохлаждаемые стены; 12 подовые электроды; 13 – водоохлаждаемые кабеля
Этапы плавления шихты.а - начало плавления; б - опускание; в - подъем электрода; г - окончание плавления.
Опишите последовательность и приведите схему изготовления литейной формы одним из методов машинной формовки. Приведите эскизы металлических модельных плит, стержневого ящика и собранной литейной формы.
Схема процесса изготовления безопочных литейных форм на автоматических машинах
Модельная плита 1 закреплена на прессовой машине, плита 3 - на плите противодавления.
Модельные плиты 1, 3, боковые стенки и головка 2 образуют формовочную камеру (рис. 17, а), которая заполняется формовочной смесью с помощью сжатого воздуха под давлением 0,5-1 МПа.
После этого формовочная смесь прессуется плунжером 4 под давлением до 2 МПа.
Модельная плита 3 отходит влево и поворачивается в горизонтальное положение, а уплотненный ком формовочной смеси плунжером 4 проталкивается до соприкосновения с предыдущим комом, образуя полость 5 (рис. 17, б).
В результате получается непрерывный ряд форм, которые заливают расплавленным металлом из ковша 6. После затвердевания и охлаждения отливок формы подаются на выбивную решетку, где отливки 7 освобождаются от формовочной смеси. Смесь поступает на переработку и повторное использование, а отливки - в обрубное отделение.
Дата добавления: 2019-07-15; просмотров: 251; Мы поможем в написании вашей работы! |
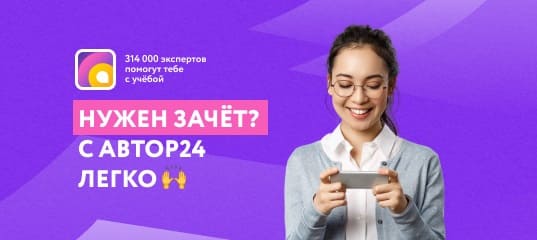
Мы поможем в написании ваших работ!