Песчано-жидкостекольные смеси
Формовочные и стержневые смеси
Качество и стоимость отливок в значительной степени зависят от правильного выбора состава и технологических свойств формовочных и стержневых смесей. Состав смесей зависит от назначения, рода заливаемого сплава, сложности и ответственности отливок, наличия необходимых исходных материалов, серийности производства, технологии изготовления и сборки форм и стержней, планируемой себестоимости отливок.
По роду заливаемого сплава различают смеси для стального, чугунного и цветного литья. Смеси для стального литья должны выдерживать температуру заливки сплава 1480-1540°С, для чугуна - 1380-1420°С и цветных сплавов - ниже 1200°С.
По назначению смеси разделяют на формовочные и стержневые, а также на единые, облицовочные и наполнительные. Стержневые смеси в отличие от формовочных должны обладать большей газопроницаемостью, прочностью, податливаемостью, огнеупорностью и т. д.
Единые смеси применяют главным образом при изготовлении мелких и средних форм в условиях высокомеханизированного производства. При использовании в эти смеси вводится значительное количество свежих материалов для поддержания прочности и газопроницаемости смеси в заданных пределах.
Облицовочные смеси применяются для крупных стальных и чугунных отливок в условиях серийного и единичного производства. Они наносятся вокруг модели слоем 15-20 мм и более, в зависимости от толщины стенки отливки. Для улучшения технологических свойств облицовочных смесей в них могут вводить более 50% свежих материалов. Облицовочные смеси используют в тех случаях, когда применение единых смесей дает значительный брак отливок по вине формовочной смеси.
|
|
Наполнительная смесь наносится поверх облицовочной и занимает остальной объем формы. Наполнительная смесь приготавливается из отработанной смеси с небольшой добавкой свежих материалов или без них и должна обладать высокой прочностью и газопроницаемостью
Естественные смеси. В настоящее время эти смеси применяются редко для изготовления мелких отливок из чугуна и цветных сплавов. Нестабильность состава и свойств этих смесей не гарантирует получения качественных отливок. Глина, входящая в состав естественных смесей, имеет малую связующую способность и низкую огнеупорность.
Смеси, в состав которых глина входит как самостоятельная добавка, называются синтетическими. На практике широко применяют синтетические смеси в связи с высокими технологическими свойствами, простотой приготовления, легкостью поддержания постоянного состава и качества смеси.
При производстве крупных толстостенных отливок сырые песчано-глинистые формы не могут обеспечить получения качественного литья. На отливках образуется повышенный пригар, возможна деформация формы по причине ее недостаточной прочности, интенсивный прогрев формы существенно увеличивает газотворность и вероятность образования газовых раковин в отливках. В связи с этим формы сушат либо подсушивают с поверхности газовыми горелками, что позволяет повысить поверхностную прочность формы, уменьшить её газотворную способность, снизить затраты и время на изготовление формы. Классификация смесей для изготовления форм и стержней по типу, виду и характеру твердения приведена в табл. 8.1.
|
|
Песчано-глинистые смеси
Технология изготовления отливок в сырых песчано-глинистых формах является основной в современных автоматизированных чугуно-сталелитейных цехах крупносерийного и массового производства. Доля литья, получаемого в сырых формах, составляет, %: Японии и ФРГ - 40; Англии - 39; Франции - 29; Италии - 30; России > 60. Формовочные смеси для изготовления сырых форм имеют низкую стоимость и минимальные отходы, так как отработанные смеси легко восстанавливаются, что позволяет сократить расход формовочного песка до 0,4 т на 1 т годных отливок.
|
|
Максимальная масса отливок из чугуна, полученных в сырых формах из единых песчано-глинистых смесей, составляет 500 кг, а из стали - 400 кг. Опыт отечественных и зарубежных литейных цехов показал, что развитие технологии литья в сырые формы идет в направлении использования высокопрочных смесей с пониженной влажностью, что позволяет получать точные отливки из чугуна и стали массой до 200 кг.
При стальном литье для смесей используют кварцевые формовочные пески с содержанием глинистой составляющей до 1%, зерновой группы 02, при мелком литье применяют пески с зерновой группой 016, а при массивном - с зерновой группой 0315. Для предупреждения образования трещин в отливках в состав смеси вводят древесные опилки, а для повышения поверхностной прочности форм в смесь вводят водный раствор лигносульфонатов (сульфитно-дрожжевая бражка). Для предупреждения пригара при массивном литье с применением сухих форм в смесь вводят до 20% пылевидного кварца. Состав и свойства типовых песчано-глинистых формовочных смесей для стального литья приведены в табл. 8.2.
При чугунном литье используют в основном кварцевые и тощие формовочные пески зерновой группы 016. При производстве мелкого литья с повышенной чистотой поверхности могут применяться пески зерновой группы 01, а при производстве крупных толстостенных отливок - зерновых групп 0315 и 04. Для предупреждения образования пригара на отливках в состав смесей вводят каменноугольную пыль. Для улучшения податливости и газопроницаемости сухих форм в смесь вводят добавку древесных опилок. Состав и свойства типовых песчано-глинистых формовочных смесей для чугунного литья приведены в табл. 8.3.
|
|
Характерное отличие смесей для отливок из цветных сплавов состоит в применении мелкозернистых формовочных песков со средним размером зерна 01 и 0063. Для крупных отливок из цветных сплавов применяют пески со средним размером зерен 016 и 02. Содержание глинистой составляющей в формовочных песках может быть значительно больше, чем при литье чугуна и стали. Для предупреждения пригара на отливках из медных сплавов в смесь вводят добавку мазута, а при литье из сплавов на основе магния для защиты металла от окисления вводят добавку борной кислоты или фтористые присадки.
Состав и свойства типовых песчано-глинистых формовочных смесей, предназначенных для цветного литья, приведены в табл. 8.4
Формовочные смеси, применяемые в современных технологических процессах для автоматических линий (табл. 8.5), представляют собой много компонентные системы. Они должны обладать комплексом свойств (прочностью, газопроницаемостью, огнеупорностью, долговечностью и т. д.), обеспечивающих высокое качество отливок и заданную производительность линии. Особенностью этих смесей является минимальное содержание (до 3%) высококачественных бентонитов в сочетании с крахмалсодержащими добавками (крахмалит от 0,01 до 0,1%) и ПАВ (от 0,01 до 0,07%). Такие смеси при минимальном содержании влаги (от 3,0 до 3,8%) обладают следующими преимуществами:
- повышенной чистотой поверхности отливок за счет образования легкоплавкой силикатной корочки на поверхности формы;
- снижением содержания бентонита, необходимого для получения заданной прочности смесей, в 2-2,5 раза по сравнению с содержанием каолинитовой глины, что приводит к увеличению газопроницаемости, огнеупорности и т. д.;
- легкой выбиваемостью отливок из форм;
- повышением податливости форм, что способствует снижению возможности образования ужимин;
- повышением текучести смесей
Песчано-жидкостекольные смеси
Песчано-жидкостекольные смеси широко применяются при единичном и серийном изготовлении форм и стержней. Одной из причин широкого использования этих смесей является возможность упрочнения форм и стержней без теплового воздействия.
Упрочнение может быть осуществлено выдержкой на воздухе (подвяливание), продувкой углекислым газом, или введением в смесь химического реагента, вызывающего аналогично углекислому газу коагуляцию жидкого стекла. Второй причиной является то, что благодаря использованию тепловой сушки продолжительность процесса упрочнения этих смесей значительно меньше, чем песчано-глинистых. Третьей причиной широкого применения данных смесей можно считать относительно низкую стоимость жидкого стекла, простоту его изготовления и нетоксичность этих смесей.
Существенным недостатком песчано-жидкостекольных смесей является плохая выбиваемость и регенерируемость вследствие повышенной спекаемости жидкого стекла с формовочным песком, а также ограниченное использование отработанных смесей в связи с тем, что в приготовляемых смесях накапливается содержание оксида натрия Na2О, который снижает огнеупорность смесей.
При изготовлении форм и стержней применяют два вида песчаножидкостекольных смесей: пластичные и жидкие.
Пластичные смеси применяют в качестве облицовочного слоя. Упрочнение готовых форм и стержней осуществляют воздушной сушкой - подвяливанием на воздухе в течение 2-8 ч; тепловой сушкой при температуре 220- 250°С в течение 0,5-1 ч и химическим путем. При химическом упрочнении применяют продувку форм и стержней углекислым газом, вводя в смесь порошкообразные добавки феррохромового шлака или нефелинового шлама, а также жидкие добавки - ацетаты этиленгликоля (АЦЭГ) либо пропиленкарбонат. Время отверждения пластичных самотвердеющих смесей (ПСС) составляет около 40-60 мин, при этом смесь приобретает значение прочности на разрыв в пределах 0,07-0,13 МПа (0,7 - 1,3 кг/см2), а по прошествии более длительного времени прочность повышается до 0,7 МПа (7,0 кг/см2) и более. Важное преимущество смесей с продувкой СО2 и ПСС по сравнению с обычными способами изготовления форм и стержней состоит в том, что упрочнение смесей происходит в контакте с оснасткой, что повышает точность размеров отливок.
Состав и свойства песчано-жидкостекольных смесей приведены в табл. 8.6 и 8.7.
Пластичные самотвердеющие смеси (ПСС) приготовляют по двухстадийной технологии. Сначала делают базовую смесь состоящую из формовочного песка, глины, молотого угля, жидкого стекла и воды. Смесь высокопластичная, прочность на сжатие во влажном состоянии 0,015 МПа (0,15 кг/см2). На участке формовки в лопастном смесителе в базовую смесь вводят отвердитель - феррохромовый шлак или др. После перемешивания в течение 45-60 с готовая смесь подается в опоку и распределяется по поверхности как облицовочная. Жидкое стекло и отвердитель взаимодействуют во всем объеме смеси, в результате чего она затвердевает. После изготовления формы из нее сразу можно удалять модель, через 30 мин на поверхность формы можно наносить противопригарное покрытие, а через 4-6 ч заливать металлом.
Жидкие самотвердеющие смеси (ЖСС). Эти смеси имеют высокую текучесть, так как они подобно жидкости могут быть залиты в опоку или стержневой ящик. Другое важное свойство этих смесей - самозатвердевание. Их применяют при изготовлении средних и крупных по величине форм и стержней, так как в этом случае, ввиду отсутствия операции уплотнения смеси, их использование наиболее эффективно. Перевод в жидкое состояние достигается за счет введения в смесь добавок пенообразователей - поверхностно-активных веществ (ПАВ). Пузырьки пены разделяют зерна песка, уменьшают силы трения, что и придает смеси свойство текучести. Текучесть смеси можно изменять в зависимости от ее состава и времени перемешивания. Время сохранения текучести также можно регулировать, оно составляет 9-10 мин. Смесь приобретает достаточную прочность через 20-30 мин. Газопроницаемость этих смесей может превышать 1000 ед., прочность на сжатие через 4 ч после заливки составляет 0,2-0,4 МПа (2-4 кг/см2). Применение ЖСС позволяет резко повысить производительность труда, исключить ручной труд при изготовлении форм и стержней, устранить энергоемкую операцию сушки, механизировать производство крупных отливок. Состав и свойства ЖСС, предназначенных для изготовления форм и стержней при стальном и чугуном литье, приведены в табл. 8.8
Для придания ЖСС газопроницаемости применяют пеногасители (НЧК). НЧК - нейтрализованный черный контакт - 25%-й раствор аммонийных солей нефтяных сульфокислот нейтральной или слабощелочной реакции. Добавкой НЧК можно быстро восстановить газопроницаемость даже при низкой температуре (3—5 °С) воздуха. Применение НЧК исключает необходимость сушки форм и стержней с целью восстановления газопроницаемости.
Песчано-жидкостекольные холоднотвердеющие смеси с жидкими отвердителями сложноэфирного типа (ацетаты этиленгликоля, про- пиленкарбонат) обладают высокой сыпучестью и низкой прочностью в исходном (влажном) состоянии - не более 0,003 МПа при сжатии. Эти ХТС содержат 3,5-4,0% жидкого стекла, легко уплотняются вибрацией и вручную, позволяют получить широкий диапазон значений живучести, имеют высокую прочность и технологичны. Для приготовления смесей применяют жидкое стекло модуля 2,6-3,0, плотностью 1,35 г/см3. Жидкие отвердители составляют 0,3-0,4%. Живучесть ХТС с жидкими отвердителями при 20°С составляет 6 - 15 мин, прочность при сжатии, МПа через 1ч- 0,5-1,4; 2 ч- 1,0 - 1,85; 4ч- 1,6-2,5; 24 ч - 2,5-5,0. Осыпаемость смесей через 24 ч менее 0,1-0,2%. Газопроницаемость ХТС определяется в основном зерновым составом песка и составляет 150-200 ед.
Ввиду повышенной хрупкости в отвержденном состоянии, ХТС, отверждаемые жидкими отвердителями, применяются в основном для изготовления средних и крупных форм. Помимо хрупкости, к недостаткам этих смесей относятся:
- отставание в скорости отверждения внутренних слоев формы (стержня) по сравнению с внешними зонами;
- усадка при отверждении смеси в оснастке и зажим оснастки;
- затрудненная выбиваемость при нагреве смеси выше 700°С;
- более сложная регенерация и ограниченное повторное использование полученного регенерата (не более 50%).
-
Песчано-смоляные смеси
Связующими материалами в песчано-смоляных смесях являются синтетические смолы. Процесс твердения синтетических смол связан с переводом полимеров с низкой молекулярной массой в полимеры с высокой молекулярной массой. Процессы отверждения синтетических смол, в зависимости от структуры получаемых полимеров, называют полимеризацией или поликонденсацией. В зависимости от типа синтетических смол их твердение может происходить в присутствии катализаторов и без катализаторов, у которых отверждение достигается тепловым воздействием.
Песчано-смоляные смеси (ПСС) достаточно дорогие и поэтому применяются в основном для оболочковых форм и стержней. ПСС имеют ряд преимуществ перед песчано-жидкостекольными:
- легкое удаление стержней (они высыпаются при выбивке отливок из форм);
- высокая производительность процесса при времени контакта с горячей оснасткой от 15 до 60 с;
- возможность регенерации отработанных смесей.
К недостаткам ПСС относят их токсичность - при заливке форм выделяются вредные вещества, такие, как фурфулол, формальдегид и др., поэтому в литейном цехе необходимо обеспечивать усиленную вентиляцию.
В литейном производстве применяют сыпучие, пластичные и жидкие песчано-смоляные смеси. Сыпучие смеси в исходном состоянии характеризуются отсутствием связи между зернами. Они применяются при изготовлении форм и стержней. Упрочнение смесей осуществляется с помощью тепловой обработки в два этапа: первый этап - в течение 20-30 с - в контакте с модельной или стержневой оснасткой, нагретой до 180-240°С; второй - в течение 1—4 мин - в печи с температурой рабочего пространства 350-450°С. При изготовлении сыпучих смесей используют термоактивные фенолоформальдегидные смолы (см. табл. 5.4). Применяют плакированные и неплакированные песчано-смоляные смеси. В плакированных смесях смола покрывает тонкой пленкой зерна формовочного песка. В табл. 8.9 приведены состав и свойства плакированных песчано-смоляных смесей
Плакирование песчано-смоляных смесей может быть произведено горячим и холодным способами. При горячем способе плакирования смола переходит в жидкое состояние в смесителе под действием горячего песка. При интенсивном перемешивании смола обволакивает зерна формовочного песка и при последующем охлаждении и перемешивании застывает на зернах в виде тонкой пленки. После просеивания и окончательного охлаждения смесь хранится в коробах, откуда распределяется по стержневым автоматам.
При холодном плакировании перевод смолы в жидкое состояние происходит за счет растворения ее ацетоном или другими растворителями. При перемешивании смеси с одновременной продувкой через смеситель холодного воздуха растворитель испаряется и смола в виде тонкой пленки остается на зернах формовочного песка.
Плакирование позволяет получить смеси с высокими физико-механическими (на 25-30%) и технологическими свойствами. Для приготовления песчано-смоляных смесей применяют обогащенные кварцевые пески с содержанием глинистой составляющей не более 0,5%, так как глина существенно увеличивает расход смолы, удорожает смесь и ухудшает ее свойства.
Пластичные песчано-смоляные смеси упрочняют как за счет введения добавок катализаторов, ускоряющих протекание реакций полимеризации смолы, так и тепловой обработки.
Песчано-смоляные смеси, твердение которых осуществляется за счет введения катализаторов, получили название - холоднотвердеющие смеси (ХТС). Изготовленные из них стержни упрочняются непосредственно в стержневых ящиках и не требуют тепловой обработки.
В настоящее время наибольшее распространение получили ХТС, из которых изготовляют стержни различного класса сложности при единичном и серийном производстве отливок. При изготовлении ХТС применяют синтетические смолы, представленные в табл. 5.3. В качестве катализаторов при изготовлении ХТС наибольшее распространение получили бензосульфокислота (БСК) и ортофосфорная кислота (ОК). БСК используется в виде водного раствора плотностью (1200-1250) кг/м3 в качестве катализатора для отверждения смол ОФ-1, ФФ-1Ф и др. ОК в виде водного раствора плотностью (1200-1550) кг/м3 используется в качестве катализатора для отверждения смол КФ-90, УКС-Л и других смол карбамидофуранового класса. Состав и свойства пластичных песчано-смоляных ХТС, предназначенных для изготовления стержней, приведены в табл. 8.10.
Одной из разновидностей теплового метода упрочнения стержней, изготовленных из песчано-смоляных смесей, является их выдержка в нагретом до определенной температуры стержневом ящике. Этот метод называют процессом изготовления стержней в горячих ящиках. В зависимости от класса применяемых смол, температура нагрева ящика составляет от 220 до 280°С, а выдержка в нем стержня продолжается в течение 40-70 с. В горячих ящиках изготавливают в основном мелкие стержни сложной конфигурации в условиях массового производства.
Для изготовления смесей, упрочняемых в горячих ящиках, применяют следующие марки синтетических смол: смесь фенолоспирта с карбамидом, ФФ-1С, КФ-90 и некоторые другие.
Для ускорения процесса отверждения песчано-смоляных смесей в горячих ящиках используют водный раствор соляной кислоты, а также катализаторы ЛСФ, AM и др. Катализатор ЛСФ представляет собой концентрат сульфитно-спиртовой барды, подкисленной ортофосфорной кислотой; применяется при использовании смолы КФ-90.
Состав и свойства пластичных песчано-смоляных смесей, предназначенных для изготовления стержней в горячих ящиках, приведены в табл. 8.11
Жидкие смеси применяют для изготовления стержней, твердение которых осуществляется как за счет тепловой обработки, так и за счет введения катализатора. В качестве добавки, способствующей переводу смеси в жидкое состояние, применяют сульфонол НП-1. Состав и свойства жидкой песчано-смоляной смеси для изготовления стержней в горячих ящиках при чугунном литье приведены в табл. 8.12.
При изготовлении жидких самотвердеющих смесей применяют синтетические смолы марок КФ-35, КФ-90 и МСФ-1.
В качестве пенообразователя в смесь вводят сульфонол НП-1, а в качестве катализатора - 70%-й раствор бензосульфокислоты (БСК).
Состав и свойства жидких песчано-смоляных самотвердеющих смесей для изготовления стержней приведены в табл. 8.13
Песчано-сульфитные смеси
Данный тип смесей характеризуется тем, что в качестве связующего материала в них используют сульфитно-дрожжевую бражку С ДБ в количестве 2-5%.
Основу СДБ составляют лигносульфонаты, и процесс твердения связывают с их поликонденсацией. Твердение данного типа смесей осуществляется за счет тепловой обработки или за счет введения добавок химических реагентов (окислителей), вызывающих поликонденсацию лигносульфонатов и самотвердение. При тепловой обработке процессу поликонденсации лигносульфонатов предшествует процесс возгонки растворителя (воды), содержащегося в связующем материале, который сопровождается резким сокращением объема связующего и возникновением в пленках на зернах песка микротрещин, вызывающих снижение прочности смеси. С целью предупреждения процесса образования микротрещин используют два способа. Первый способ основан на введении в смесь добавки пластификатора, который создает условия для устранения напряжений, вызывающих образование микротрещин. В качестве пластификатора используют техническую мочевину в количестве 12% от содержания связующего материала в смеси. Второй способ основан на введении в смесь мелкозернистых добавок, создающих каркас в пленках связующего, который разобщает их на мелкие зоны; при этом процессы, связанные с возгонкой растворителя в пленках связующего, протекают без значительных концентраций внутренних напряжений. В качестве такой добавки используют пылевидный кварц в соотношении к связующему материалу 1:1. При самотвердении смеси возгонки растворителя не происходит. В этом случае содержащаяся влага в связующем материале лишь локализуется (защемляется) пространственно-сетчатой структурой макромолекул лигносульфонатов. В качестве добавок, вызывающих самотвердение песчано-сульфитных смесей, используют хромовый ангидрид Сг2Оз, бихроматы натрия и калия и персульфат аммония в количестве от 0,2 до 0,7% от массы смеси.
По сравнению с песчано-смоляными данный тип смесей экономичнее, так как в состав его входит недорогой и недефицитный связующий материал, а также менее токсичная упрочняющая добавка. Применяют пластичные и жидкие песчано-сульфитные смеси.
Пластичные смеси используются для изготовления мелких стержней, упрочняемых в горячих ящиках в условиях крупносерийного и массового производства, а также для изготовления самотвердеющих литейных форм и стержней взамен песчано-глинистых и песчано-жидкостекольных смесей при чугунном и стальном литье.
При изготовлении смесей, предназначенных для получения стержней в горячих ящиках, помимо указанных выше добавок, в состав смеси вводят строительный гипс или мылонафт, которые повышают прочность стержней при извлечении из ящика, а также добавку поли- винилацетатной эмульсии (ПВАЭ), снижающей гигроскопичность стержней.
Продолжительность твердения стержней в ящиках, нагретых до 230-280°С (толщина стенок изготовляемых стержней не должна превышать 30-40 мм), составляет 1,0-2,0 мин. Состав и свойства пластичных песчано-сульфитных смесей для изготовления стержней в горячих ящиках для чугунных и стальных отливок приведены в табл. 8.14.
При изготовлении самотвердеющих смесей в их состав в качестве отвердителя вводят добавку хромового ангидрида в виде водного раствора плотностью 1,3-103 кг/м3, а также синтетических жирных кислот (СЖК), предотвращающих пенообразование в процессе приготовления смесей. Самотвердеющая смесь с добавкой СЖК относится к легкоуплотняемому виду, поэтому изготовление форм и стержней может быть осуществлено на вибростолах. Состав и свойства пластичной песчано-сульфитной самотвердеющей смеси для изготовления форм и стержней для чугунных и стальных отливок приведены в табл. 8.15
Жидкие песчано-сульфитные смеси применяют для изготовления форм и стержней. Упрочняют их как за счет тепловой обработки, так и за счет введения в смесь химических реагентов, вызывающих само- твердение. При изготовлении смесей, предназначенных для получения стержней в горячих ящиках, в качестве добавки, способствующей переводу смеси в жидкое состояние, используют сульфонол НП- 1, а для повышения прочности стержня при его извлечении из ящика - фенолоспирт. Продолжительность упрочнения стержней в ящике, нагретом до 300°С, составляет 1,0-1,5 мин. Состав и свойства жидкой песчано-сульфитной смеси для изготовления стержней в горячих ящиках для чугунных отливок приведены в табл. 8.12.
При изготовлении самотвердеющих смесей для перевода их в жидкое состояние вводят добавку РАС. В качестве добавок, вызывающих твердение смеси, вводят хромовый ангидрид, бихромат натрия и персульфат аммония, а в качестве катализатора - добавку медного купороса. При использовании персульфата аммония с целью повышения активности его действия в смесь вводят добавку ферро- хромового шлака. Состав и свойства жидких песчано-сульфитных самотвердеющих смесей для изготовления форм и стержней для чугунных и стальных отливок приведены в табл. 8.16
Песчано-цементные смеси
Песчано-цементные смеси применяют главным образом для изготовления крупных форм и стержней в условиях единичного производства отливок.
В качестве связующего материала для данного типа смесей используют цемент в количестве 7-10%.
Твердение песчано-цементных смесей связывают с выделением из пересыщенного водно-цементного раствора кристаллогидратов, которые, срастаясь друг с другом, образуют прочный кристаллический каркас, связывающий зерна формовочного песка. При использовании портландцемента такими кристаллогидратами преимущественно являются гидросиликаты кальция, а при использовании глиноземистого цемента - гидроалюминаты кальция. С целью ускорения процесса твердения песчано-цементных смесей в их состав вводят специальные добавки, такие, как патока, хлористый кальций, железный корпус, а для улучшения выбиваемости - небольшие добавки СДБ (до 2,5%). Песчано-цементные смеси относят к категории самотвердеющих смесей. Применяют пластичные и жидкие песчаноцементные смеси.
Состав и свойства пластичных песчано-цементных смесей для изготовления форм и стержней при стальном и чугунном литье приведены в табл. 8.17.
При изготовлении жидких песчано-цементных смесей в состав их вводят СДБ в количестве 9-11%, которая проявляет себя как пенообразующее поверхностно-активное вещество. Состав и свойства жидких песчано-цементных смесей, предназначенных для изготовления форм и стержней для стальных и чугунных отливок, приведены в табл. 8.15
Песчано-масляные смеси
Название данного типа смесей условное, так как в настоящее время вместо масляных связующих широко используются их заменители (связующие П, ПТ, ГТФ, КО и др.), не содержащие в своем составе растительных масел.
Песчано-масляные смеси широко применяют для изготовления ответственных стержней I, II и III классов в условиях мелкосерийного и крупносерийного производства отливок. Упрочнение стержней, изготовленных из данного типа смесей, как правило, осуществляют тепловой обработкой - сушкой, температура которой зависит от природы применяемого связующего материала и колеблется от 170 до 180°С при использовании в качестве основного связующего крепителя М, декстрина, пектинового клея, а при использовании крепителей П, ПТ, ГТФ - до 200-220°С. Помимо связующих материалов, в состав песчано-масляных смесей вводят добавки формовочной глины с целью повышения прочности стержней во влажном состоянии и предупреждения их деформации под влиянием собственной массы, а также добавки СДБ.
Кроме указанных выше добавок, при литье сплавов на основе магния в состав смесей вводят специальные добавки: борную кислоту, фтористую присадку, которые предупреждают процесс окисления сплава в литейной форме.
Состав и свойства песчано-масляных стержневых смесей, предназначенных для стальных, чугунных и цветных отливок, приведены в табл. 8.18 и 8.19.
Противопригарные покрытия
Механизм образования пригара и способы его предупреждения
Пригаром называют дефект в виде трудно отделяемого слоя на поверхности отливки, образовавшегося вследствие физико-химического взаимодействия формы или стержня с расплавом и его окислами. Различают два вида пригара: механический и химический.
Механический пригар образуется вследствие проникновения расплавленного металла в поры формы. Чем больше температура сплава и гидростатическое давление, а также размер пор в смеси, тем больше механический пригар. Для того, чтобы возник механический пригар, сплав должен проникнуть в поры формы или стержня на глубину не меньше диаметра зерна формовочного песка (0,1-0,315 мм). В этих условиях возникает капиллярное давление, которое может способствовать (при условии смачивания сплавом формы) либо препятствовать (когда сплав не смачивает форму) проникновению сплава в поры формы. Сплав проникает в поры формы под действием гидростатического и капиллярного давления. Глубина проникновения металла в поры формы может быть найдена из выражения
где h - глубина проникновения металла в поры формы: Н - гидростатический напор сплава в форме; s - поверхностное натяжение сплава; q - краевой угол смачивания; р - плотность сплава; r - радиус пор.
Капиллярное давление будет препятствовать (при 90°<q<180°) либо способствовать (при 0°< q <90°) проникновению сплава в поры формы.
Жидкий неокисленный сплав не смачивает поверхность формы, и поэтому капиллярное давление будет препятствовать образованию пригара на отливках. Исключить или значительно уменьшить образование механического пригара возможно созданием восстановительной атмосферы в полости литейной формы и на границе “металл - форма” при заполнении ее сплавом до момента образования на поверхности отливки твердой корочки затвердевшего сплава.
Химический пригар возникает на отливках в результате физикохимического взаимодействия на границе “металл - форма” в результате сложных реакций между металлом отливки, его оксидами и материалом формы.
В отличие от механического пригара зерна формовочного песка в прогреваемом слое связываются главным образом продуктами химических реакций, протекающих при высоких температурах, преимущественно силикатами. Оксиды железа хорошо смачивают кварцевый песок и под действием капиллярного давления легко проникают в поры формы, вступая в реакцию с кремнеземом:
В сплавах с высоким содержанием марганца образованию пригара способствует аналогичная реакция между закисью марганца и кремнеземом
Образующиеся в результате этих реакций легкоплавкие силикаты после затвердевания цементируют зерна песка в слой пригара. Для уменьшения пригара в формовочные и стержневые смеси вводят специальные противопригарные добавки.
При производстве крупных стальных отливок в качестве противопригарных добавок в облицовочные формовочные и стержневые смеси вводят: 15-30% пылевидного кварца (> 94,5% Si02), до 25% цирконового песка; до 15% серебристого графита (кристаллического), обладающего большой термохимической устойчивостью до 1800°С. Пылевидный кварц уменьшает пористость, цирконовый песок и серебристый графит увеличивают огнеупорность смесей.
При чугунном литье для уменьшения пригара в смеси вводят пылевидный каменный уголь. В период заливки формы частицы угольной пыли сгорают, выделяя СО и С02, образующие газовую прослойку между формой и жидким металлом. В начальный момент заливки и в период снятия теплоты перегрева при дефиците 02 на поверхности отливки образуется в основном оксид углерода СО. Кроме того, СО создает в форме восстановительную атмосферу, которая препятствует образованию оксидов сплава, способствующих смачиванию зерен формовочного песка и проникновению металла в поры формы. Каменный уголь должен выделять при сгорании не менее 30% летучих веществ и не более 11% золы. В нем должно быть не более 2% серы и 12% влаги. Дисперсность помола угля и его содержание в смеси зависят от толщины стенок отливок и могут быть выбраны по табл. 9.1.
Мазут в качестве противопригарной добавки применяют в облицовочных смесях для мелких чугунных отливок и отливок из медных сплавов, получаемых в сырых песчано-глинистых формах. Действие его подобно каменноугольной пыли. Мазут обладает меньшей зольностью, поэтому смеси более долговечны и газопроницаемы. Обладая большей газотворностью, содержание мазута в смеси не должно превышать 1—1,5%.
При литье магниевых сплавов в формовочные и стержневые смеси вводят защитные присадки (табл. 9.2), которые, интенсивно выгорая в процессе заливки металла, образуют между сплавом и стенками формы или стержня газовую прослойку с инертной атмосферой, препятствующей окислению отливки и горению сплава.
Противопригарные краски и пасты
Введение противопригарных добавок в состав формовочных и стержневых смесей не всегда может обеспечить получение отливок без пригара. Одним из наиболее распространенных способов предупреждения образования пригара на отливках является нанесение защитных покрытий на поверхность изготовленных форм и стержней, которые препятствуют проникновению жидкого металла в поры смеси и химическому взаимодействию оксидов металла с материалом формы. Формовочные краски должны обладать следующими свойствами:
- иметь большую температуру плавления и не размягчаться от соприкосновения с расплавом;
- оставаться постоянными по составу во время их приготовления, хранения и использования;
- обладать хорошей кроющей способностью;
- слой краски, нанесенный на поверхность формы или стержня, не должен трескаться при сушке форм и стержней;
- после подсушки удерживаться на поверхности формы или стержня.
Противопригарные краски состоят из огнеупорной основы (наполнителя), связующего материала и растворителя. Для предупреждения преждевременного осаждения наполнителя, т. е. с целью повышения устойчивости красок, в их состав вводят стабилизаторы. В качестве стабилизатора применяют такие вещества, которые неограниченно набухают в жидкости и тем самым создают условия, препятствующие осаждению частичек наполнителя. В состав красок также вводят специальные добавки, предупреждающие брожение (формалин), ускоряющие их упрочнение (катализатор) и др.
В качестве наполнителей красок используют пылевидный кварц, графит, тальк, циркон, а также некоторые другие материалы. Пылевидный кварц применяют для покрытий форм и стержней при стальном литье, графит - для покрытий форм и стержней при чугунном и цветном литье, тальк - при цветном литье и циркон - при крупных стальных отливках.
Для приготовления красок применяют водорастворимые и органорастворимые связующие материалы. В состав водорастворимых красок входят органические связующие материалы: сульфитно-дрож- жевая бражка, декстрин, патока, крахмалит, древесный пек - и не органические материалы: жидкое стекло, сульфат алюминия, [(A12(SО4)3 • 18Н2О], сульфат магния (MgSО4- 7Н2О), триполифосфат натрия (Na5P3O10)n.
В составе органорастворимых красок (самовысыхающих - не требующих сушки) в качестве связующих применяют органические материалы: нитролак 644, поливинилбутираль и кремнийорганические материалы: лак КО-075 и смолу К-9.
Для разведения красок до требуемой плотности используют воду или органические жидкости. В качестве органических растворителей красок применяют уайт-спирит, этиловый спирт, растворитель 646, растворитель обувного гарнитоля.
В качестве стабилизаторов в состав красок вводят добавку бентонита, а также высокомолекулярные вещества, такие, как поливиниловый спирт (ПВС), карбоксиметилцеллюлозу (КМЦ). Помимо своего назначения, стабилизаторы являются и связующими материалами, повышающими прочность слоя краски.
При подборе составов противопригарных красок принимается во внимание вид сплава, масса изготовляемых отливок, особенности формовочных или стержневых смесей. Учитывая многообразие факторов, определяющих требования к противопригарным покрытиям, оптимальные составы красок, как правило, устанавливаются опытным путем.
Водные противопригарные краски
Водные краски применяют главным образом для форм и стержней, подвергаемых сушке. В отдельных случаях их также применяют при изготовлении форм и стержней из самотвердеющих смесей, но при этом необходимо использовать поверхностную подсушку слоя краски. Состав и свойства водных противопригарных красок с органическими и неорганическими связующими материалами приведены в табл. 9.3 и 9.4.
Водные краски с неорганическими связующими материалами применяют главным образом при массивном чугунном и стальном литье. Характерной особенностью этих красок является использование в качестве связующего материала водных растворов сульфатов алюминия и магния, а также триполифосфата натрия, которые придают краскам высокую термостойкость. Последняя достигается благодаря тому, что в процессе теплового разложения этих связующих материалов при температурах 700-1000°С они прочно спекаются в химически инертное к оксидам металла состояние. Упрочнение красочного слоя происходит после испарения влаги при температуре 100-200°С, поэтому формы и стержни, окрашенные такими красками, подвергают сушке при указанной выше температуре.
Номенклатура и свойства наиболее распространенных промышленно выпускаемых водных противопригарных красок, а также рекомендации по их применению представлены в табл. 9.5.
Они поставляются в виде порошкообразных композиций, содержащих все необходимые компоненты (наполнитель, связующее, стабилизаторы, технологические добавки). Для получения готовых к употреблению противопригарных красок эти порошки разводят в воде до нужной консистенции.
В табл. 9.6 приведены составы самотвердеющих водных красок, которые не требуют подсушки.
В качестве связующего материала в них применяют сульфитнодрожжевую бражку. В качестве окислителя связующего, который придает краске способность к самотвердению, используется добавка персульфата аммония [(NH4)2S208]. Для получения требуемой плотности при оптимальном количестве воды в состав краски вводят добавку технической мочевины. В отличие от обычных водных красок, у которых при сушке происходит испарение воды, из данных красок вода не испаряется, а лишь химически связывается, поэтому в отдельных случаях, во избежание вскипов жидкого металла, формы и стержни целесообразно подсушивать. Водные самотвердеющие покрытия применяют для окраски форм и стержней, изготовленных из самотвердеющих смесей, при стальном и чугунном литье.
Самовысыхающие противопригарные краски
Данный тип красок имеет быстроиспаряющиеся неорганические растворители, для возгонки которых нет необходимости применять сушку. Самовысыхающие покрытия применяют для форм и стержней, изготовляемых из самотвердеющих смесей.
В табл. 9.7 приведены составы самовысыхающих противопригарных красок.
В качестве связующих материалов в состав красок вводят древесный пек, нитролаки 644 и 68, поливинилбутираль, причем нитролаки и поливинилбутираль одновременно с основным своим назначением выполняют также функцию стабилизатора. В качестве растворителей в состав красок вводят этиловый спирт, уайт-спирит или растворитель 646. Краски № 1 и 2 с цирконовым наполнителем применяют при стальных отливках. Краски № 3, 4, 5 и 6 на графитовом наполнителе применяют при чугунном, а краску № 7 на тальковом наполнителе - при цветном литье. Противопригарные самовысыхающие краски в виде готовых к употреблению суспензий на основе связующего форлака выпускаются централизованно (ТУ 4191-004-00224656-00) (табл. 9.8). Эти краски наиболее эффективны при использовании холоднотвердеющих смесей.
Лак представляет собой раствор модифицированного высокополимерного связующего в органическом растворителе, после испарения которого формируются прочные эластичные пленки. Растворителем лака служит растворитель антипригарных красок, состоящий из спирта этилового, ацетона и бензина-растворителя.
Дата добавления: 2019-07-15; просмотров: 1909; Мы поможем в написании вашей работы! |
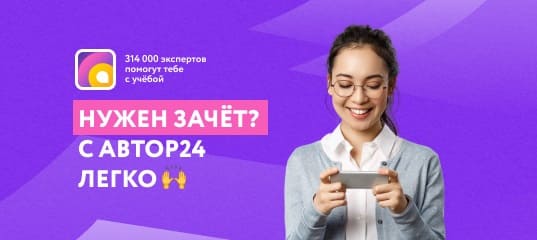
Мы поможем в написании ваших работ!