СПОСОБЫ ПОЛУЧЕНИЯ АММИАКА ИЗ АЗОТОВОДОРОДНОЙ СМЕСИ
ЗАДАНИЕ ПО КУРСОВОМУ ПРОЕКТИРОВАНИЮ
студенту гр. ХНбз-141 Антипову Р. П.
Тема проекта: Производство аммиака. Мощность 560 000 т/г.
Стадия синтеза
Исходные данные к проекту
− производительность ___________________________________________
− исходное сырье ________________________________________________
− степень превращения __________________________________________
− ______________________________________________________________
Содержание разделов расчетно-пояснительной записки
(в соответствии с МУ):
− аналитический обзор___________________________________________
− теоретические основы технологического процесса ________________
− характеристика исходного сырья, материалов и готового продукта__
− описание технологической схемы_________________________________
− технологические расчёты ______________________________________
4. Графическая часть:
− технологическая схема__________________________________________
− схема материальных потоков ____________________________________
Дата выдачи задания .__._______ 2019 г. Руководитель _______
Срок сдачи проекта .__._______ 2019 г. Студент ____________
СОДЕРЖАНИЕ
Задание на выполнение работы
| 3 | |||
Введение | 5 | |||
1 | Аналитический обзор | 7 | ||
2 | Теоретические основы технологического процесса | 18 | ||
3 | Характеристика исходного сырья, материалов и готового продукта | 24 | ||
4 | Описание технологической схемы | 26 | ||
5 | Технологические расчеты: | 31 | ||
5.1 Материальный баланс | 31 | |||
5.2 Тепловой баланс | 37 | |||
Выводы
| 40 | |||
Список использованной литературы | 41 |
ВВЕДЕНИЕ
Все развитые страны говорят о том, что в наше время азот и его соединения занимают одно из первых мест в химической промышленности и имеют большое значение для сельского хозяйства. Производству азотных удобрений и их основы, аммиака, в нашей стране уделялось первостепенное внимание.
Соединения азота очень важны в жизни на земле так как они являются основной составной частью белковых соединений и находят широкое применеие в некоторых областях жизнедеятельности человека. В наше время
Основным промежуточным продуктом для получения большого количества
разных азотосодержещих соединений является аммиак. Для таких продуктов как : карбамид, азотная кислота, полимерные материалы ( полиуретаны , полиамиды и многие другие). Болшое значение аммиак занимает в холодильной технике , производстве минеральных удобрений. В то же время из карбамида и азотной кислоты производятся : взрывчатые вещества , нитраты, нитриты и другие вещества.
|
|
Современное производство аммиака состоит из нескольких последовательно-связанных между собой технологичесих стадий : сероочистки ,конверсии, метанирования , компрессии и синтеза аммиака.
Синтез аммиака имеет исключительное значение среди других реакций : во-первых , он связан с решением одной из главных задач , а именно , с созданием мощной сырьевой базы для получения самых разнообразных органических и неорганических соединений; во-вторых, он является примером практического объединения трёх направлений физической химии- термодинамики, кинетики и катализа- при решении комплексной теоретической проблемы и в-третьих, с синтезом аммиака связаны первые эмперические обобщения по подбору катализаторов.
Блок синтеза характеризуется при менением сложной реакционной и теплообменной аппаратуры, для изготовления которой используется высококачественные стали. По капитальным затратам он один из самых весомых в производстве аммиака. Выбор технологических схем, аппаратов во многом определяется свойством катализаторов синтеза: его активностью, стабильностью, механической прочностью. По этому к качеству катализатора предъявляют самые высокие требования[1].
|
|
Изм. |
Лист |
№ докум. |
Подпись |
Дата |
Лист |
7 |
ПА 560Т 02 . 01. ПЗ |
Разраб. |
Антипов Р.П. |
Провер. |
Тихомирова А.В |
Реценз |
Н. Контр. |
Утверд. |
Производство аммиака. Стадия синтеза Расчётно-пояснительная записка |
Лит. |
Листов |
42 |
КузГТУ. ХТНВиН .грХНбз-141 кафедра ХТНВиН гр.ХНбз-131 |
ПОЛУЧЕНИЕ АММИАКА ИЗ СУЛЬФАТА АММОНИЯ
Получение аммиака из сульфата аммония, и может быть использовано для расширения возможностей переработки сульфата аммония, образующегося при утилизации отходов производств. Способ получения аммиака и серной кислоты из сульфата аммония включает термическое разложение сульфата аммония на гидросульфат аммония и аммиак, изготовление раствора гидросульфата аммония и вспомогательного сульфата, образующего с сульфатом аммония двойной сульфат, осаждение двойного сульфата, отделение двойного сульфата, полученный раствор разбавленной серной кислоты очищают, предпочтительно осаждением примесей, отделяют примеси, очищенный раствор разбавленной серной кислоты упаривают до получения товарной серной кислоты, двойной сульфат разлагают на сульфат аммония, который возвращают на термическое разложение, и на вспомогательный сульфат, который возвращают для получения раствора гидросульфата аммония и вспомогательного сульфата, образующего с сульфатом аммония двойной сульфат. Изобретение позволяет расширить возможности утилизации сульфата аммония, упростить производство аммиака и серной кислоты из сульфата аммония, исключить образование при производстве серной кислоты экологически опасного сернистого газа.
Наиболее близким по технической сущности является способ получения аммиака и серной кислоты из сульфата аммония (WO 20008025166 A1, 06/03/2008) . Согласно этому способу сульфат аммония термически разлагают на гидросульфат аммония и аммиак, полученный гидросульфат
|
|
аммония разлагают на серную кислоту и сульфат аммония: путем растворения гидросульфата аммония и обработки полученного раствора гидросульфата аммония сорбентом до абсорбции серной кислоты и
получения раствора сульфата, сульфат аммония возвращают на термическое разложение на гидросульфат аммония и аммиак, а сорбент регенерируют для повторного использования путем десорбции серной кислоты водой до получения раствора серной кислоты.
Изм. |
Лист |
№ докум. |
Подпись |
Дата |
Лист |
8 |
ПА 560Т 02 . 01. ПЗ |
Недостатком способа является также низкая экологичность процесса обусловленная тем, что образуется отработанный сорбент, накопивший примеси и представляющий экологическую опасность, а также тем, что получается серная кислота, загрязненная примесью сульфата аммония. После использования такой серной кислоты на производстве образуется дополнительное загрязнение продуктов и отходов ионом аммония. Задачей настоящего изобретения является повышение экологичности и экономичности получения аммиака и серной кислоты из сульфата аммония [2].
СПОСОБЫ ПОЛУЧЕНИЯ АММИАКА ИЗ АЗОТОВОДОРОДНОЙ СМЕСИ
Ещё один способ может быть использован в химической промышленности. Природный газ компримируют, подогревают и очищают от соединений серы в реакторе радиально-спирального типа. Осуществляют двухступенчатую каталитическую конверсию метана под давлением в разделенном на две секции реакторе радиально-спирального типа. В первой секции при температуре 800-1000°С осуществляют паровую конверсию с использованием тепла газа, конвертированного во второй ступени, а также
дополнительно сжигаемых на горелке части природного газа, продувочных и танковых газов. Температуру дымовых газов после горелки поддерживают в
Изм. |
Лист |
№ докум. |
Подпись |
Дата |
Лист |
9 |
ПА 560Т 02 . 01. ПЗ |
Способ получения аммиака из углеводородного сырья, водяного пара, воздуха и кислорода, включающий очистку сырья от соединений серы, парокислородовоздушную каталитическую конверсию метана в шахтном конверторе, конверсию оксида углерода, очистку полученной азотоводородной смеси от кислородсодержащих соединений, компримирование и проведение синтеза аммиака в замкнутом цикле Основным недостатком данного способа является использование технического кислорода при проведении конверсии метана, что сопряжено с большими капитальными и энергетическими затратами на кислородную установку[3].
Известен также способ получения аммиака из ПГ, предусматривающий очистку ПГ от соединений серы, двухступенчатую паровую (I ступень) и паровоздушную (II ступень) конверсию ПГ соответственно в трубчатой печи
Изм. |
Лист |
№ докум. |
Подпись |
Дата |
Лист |
10 |
ПА 560Т 02 .01. ПЗ |
- паровая конверсия ПГ осуществляется в трубчатой печи, для которой характерны большие размеры и металлоемкость, а также недостаточная надежность, связанная с частым прогоранием реакционных труб, несмотря на использование для их изготовления дорогостоящих жаропрочных никельсодержащих сплавов;
- для паровоздушной конверсии ПГ используется шахтный реактор, для которого характерны большое гидравлическое сопротивление, неравномерное распределение реагентов по зернистому слою катализатора, а также неравномерное распределение температур по высоте и по поперечному сечению аппарата;
- для размещения трубчатой печи и шахтного реактора необходима большая производственная площадь;
- проведение каталитической конверсии ПГ последовательно в двух аппаратах сопровождается большими потерями тепла как непосредственно от аппаратов, так и от соединяющей их «горячей» трубы, по которой частично конвертированный газ из трубчатой печи подается в шахтный конвертор;
- проведение синтеза аммиака при высоком давлении (свыше 30 МПа) связано с повышенными капитальными затратами и с большим расходом энергии на привод компрессоров.
Известен также наиболее близкий к предлагаемому способу и принятый в качестве прототипа способ получения аммиака из углеводородного сырья, водяных паров и воздуха, включающий компримирование и очистку сырья от соединений серы, паровую и паровоздушную каталитическую конверсию метана, конверсию оксида углерода, очистку полученной азотоводородной смеси от кислородсодержащих соединений, компримирование, синтез аммиака в замкнутом цикле, использование неочищенного от соединений серы сырья в качестве топлива, утилизацию тепла дымовых газов (ДГ) и их выделение в окружающую среду; отличительная особенность данного способа заключается в том, что незначительную часть углеводородного сырья, прошедшего очистку от соединений серы, сжигают в смеси с компримированным воздухом, а полученные ДГ подают на паровоздушную каталитическую конверсию. Как следует из примеров, приведенных в патенте, предусмотрено проведение синтеза аммиака при давлении 33,5 Мпа [4].
Недостатки способа заключаются в следующем:
- в качестве топлива используют сырье, не очищенное от соединений серы, что приводит к выбросу в окружающую среду вместе с ДГ диоксида серы;
- сжигание части углеводородного сырья, прошедшего очистку от соединений серы, в смеси с компримированным воздухом, и подача полученных ДГ на паровоздушную каталитическую конверсию метана, приводит к усложнению и удорожанию установки;
- проведение синтеза аммиака при высоком давлении (свыше 33,5 МПа)
связано с повышенными капитальными затратами и с большим расходом энергии на привод компрессоров;
- преимущества способа весьма незначительны - как указано в патенте, по сравнению с принятым в нем прототипе, количество газовых выбросов в атмосферу сокращаются всего на 0,18%, а расход углеводородного сырья уменьшается всего на 0,12%.
Задачей предлагаемого изобретения является повышение экономичности получения аммиака.
Изм. |
Лист |
№ докум. |
Подпись |
Дата |
Лист |
11 |
ПА 560Т 02 .01. ПЗ |
Изм. |
Лист |
№ докум. |
Подпись |
Дата |
Лист |
12 |
ПА 560Т 02 .01. ПЗ |
Задачей изобретения является также исключение или минимизация выбросов вредных веществ (СО и NOx) в окружающую среду с отходящими ДГ[5].
В настоящее время аммиак производится в России из природного газа и атмосферы воздуха. Реакция синтеза аммиака обратима N2 + 3H2 ó 2NH3 ,∆ Ho298=-92,52 кДж, полное превращение азотоводородной смеси в аммиак за один цикл невозможно. Поэтому для этого необходимо обеспечить либо многократную циркуляцию азотоводородной смеси через колонну синтеза, либо проводить многоступенчатое контактирование смеси, пуская её последовательно через ряд колонн синтеза. Последний метод в настоящее время не применяется вследствие своей громоздкости и больших энергетических затрат. Существует два вида насадок (катализаторная коробка и теплообменник) колонн синтеза:
– трубчатые насадки с теплообменником в зоне катализа;
– полочные насадки с катализатором, загруженным сплошным слоем на каждой полке.
Известны также варианты комбинированных конструкций насадок.В трубчатых насадках в слое катализатора расположены трубки, в которых поступающий на катализатор газ нагревается за счет отводимого из зоны катализа тепла до температуры начала реакции. По теплообменным
трубкам катализаторной зоны проходит газ основного потока после предварительного теплообменника и смешения с газом холодного байпаса
На рис. 1 представлена насадка колонны синтеза с противоточными трубками, нижним расположением электродвигателя и внутренним паровым котлом-утилизатором.
Изм. |
Лист |
№ докум. |
Подпись |
Дата |
Лист |
13 |
ПА 560Т 02 .01. ПЗ |
Рис 1 - Насадка колонны синтеза с противоточными трубками:
1 – катализаторная коробка; 2 – регулировочный клапан; 3 – паровой котел; 4 – теплообменник; 5 – электродвигатель.
Недостатки насадок с простыми противоточными трубками проявляется в значительном перегреве центральной части зоны катализа и низких температурах газа на выходе из слоя катализатора, таким образом, в крупных агрегатах насадки такого типа не применяются, но они находят свое применение в колоннах предкатализа.
Существуют также насадки с простыми параллельными трубками с внутренним котлом из двойных трубок. Режим у этих насадок близкий к оптимальному, однако, из-за сильного охлаждения лобового слоя
Изм. |
Лист |
№ докум. |
Подпись |
Дата |
Лист |
14 |
ПА 560Т 02 .01. ПЗ |
Еще одним видом насадки является насадка с двойными противоточными трубками (рис.2).
|
Рис 2 - Насадка с двойными противоточными трубками:
1 – катализаторная коробка; 2 – электроподогреватель; 3 – теплообменник.
Преимущества данной насадки в приближении температурного режима к оптимальному, высокой устойчивости системы, простоте и надежности конструкции, удобстве монтажа. К недостаткам можно отнести, в первую очередь, высокое гидравлическое сопротивление. Такая насадка применяется только в агрегатах синтеза средней мощности.
В полочных насадках масса катализатора разделяется на несколько слоев по высоте колонны, через них последовательно поступает газ. Между полками подается холодный газ. Так как в каждом слое катализатора реакция проходит без отвода тепла, то температура по мере поступления газа
Изм. |
Лист |
№ докум. |
Подпись |
Дата |
Лист |
15 |
ПА 560Т 02 .01. ПЗ |
По характеру движения газа в слое катализатора относительно центральной оси колонны полочные насадки разделяются на:
– аксиальные (с продольным течением газа по высоте колонны);
– радиальные (с поперечным сечением газа).
На рисунке 3 показана конструкция четырехполочной аксиальной колонны.
Рис 3 – Четырехполочная колонна синтеза аммиака:
Изм. |
Лист |
№ докум. |
Подпись |
Дата |
Лист |
16 |
ПА 560Т 02 .01. ПЗ |
Такой тип колонны синтеза с встроенным теплообменником широко применяется в промышленности, из-за простоты конструкционного оформления и высокой надежности, хотя монтаж колонны такого типа несколько затруднен, что связанно с большой высотой обечайки, а так же с тем, что аппарат, как правило выполняется цельнокованым. Однако такой тип аппарата позволяет значительно сэкономить энергетические и материальные ресурсы, в частности, уменьшается расход металла на изготовление отдельного теплообменника с собственным корпусом, а также на изготовление трубопроводной арматуры. Следует также отметить, что поддержание под высоким давлением выносного теплообменника требует значительных затрат энергии. Подача байпасного газа обеспечивает многовариантное регулирование режима в зоне катализа, однако именно подача байпаса с низким (3 – 4%) содержанием аммиака снижает эффективность работы насадки, кроме того, аксиальные полочные насадки обладают сравнительно высоким гидравлическим сопротивлением, вследствие чего применяется крупнозернистый катализатор, что, в свою очередь снижает производительность колонн синтеза[5].
Изм. |
Лист |
№ докум. |
Подпись |
Дата |
Лист |
17 |
ПА 560Т 02 . 02. ПЗ |
Разраб. |
Антипов Р.П. |
Провер. |
Тихомирова А.В |
Реценз |
Н. Контр. |
Утверд. |
Производство аммиака. Стадия синтеза Расчётно-пояснительная записка |
Лит. |
Листов |
42 |
КузГТУ. ХТНВиН .грХНбз-141 кафедра ХТНВиН гр.ХНбз-131 |
Синтез аммиака из азота и водорода описывается обратимой равновесной реакцией:
0,5N2 + 1,5 Н2 NH3 + Q (1)
протекающей с уменьшением объема и выделением тепла. По принципу Ле-Шателье сдвигу равновесия такой реакции вправо, т.е. в сторону образования аммиака, способствует повышение давления и понижения температуры. Однако в промышленных условиях, чтобы увеличить скорость реакции, процесс осуществляется при повышенных температурах и в присутствии катализаторов. А. Ларсон и Р. Додж определили экспериментально равновесные концентрации аммиака для азото-водородной смеси стехиометрического состава в интервале давлений 0,98-98,1 МПа и температур 325-5000С. Затем эти данные авторы экстрагировали до 200 и 7000С. Полученные результаты представлены в таблице 1 и на рисунке 2, а вычисленные на их основании константы равновесий в таблице 2. Экспериментальные результаты А. Ларсона и Р. Доджа отличаются большой точностью и ими пользуются до настоящего времени. Наличие надежных экспериментальных данных позволяет проверять правильность различных методов расчета химического равновесия[6].
Изм. |
Лист |
№ докум. |
Подпись |
Дата |
Лист |
18 |
ПА 560Т 02 .02. ПЗ |

Таблица 1
Равновесные концентрации аммиака (в % об.) для стехиометрической смеси азота и водорода.
Температура, 0С | Давление, МПа | |||||||
0,098 | 0,98 | 2,94 | 4,91 | 9,81 | 29,43 | 58,86 | 98,10 | |
200 | - | 50,66 | 67,56 | 74,38 | 81,54 | 89,94 | 95,37 | 98,29 |
250 | - | 28,34 | 47,22 | 56,33 | 67,24 | 81,38 | 90,66 | 96,17 |
300 | 2,18 | 14,73 | 30,25 | 39,41 | 52,04 | 70,96 | 84,21 | 92,55 |
350 | 0,864 | 7,41 | 17,78 | 25,23 | 37,35 | 59,12 | 75,62 | 87,46 |
400 | 0,415 | 3,85 | 10,15 | 15,27 | 25,12 | 47,00 | 65,20 | 79,82 |
450 | 0,218 | 2,11 | 5,86 | 9,15 | 16,43 | 35,82 | 53,71 | 69,69 |
500 | 0,124 | 1,21 | 3,49 | 5,56 | 10,61 | 26,44 | 42,15 | 57,47 |
550 | 0,078 | 0,76 | 2,18 | 3,45 | 6,82 | 19,13 | 31,63 | 41,16 |
600 | 0,049 | 0,49 | 1,39 | 2,26 | 4,52 | 13,77 | 23,10 | 31,43 |
650 | - | 0,33 | 0,96 | 1,53 | 3,11 | 9,92 | 16,02 | 20,70 |
700 | 0,022 | 0,23 | 0,68 | 1,05 | 2,18 | 7,28 | 12,60 | 12,87 |
Изм. |
Лист |
№ докум. |
Подпись |
Дата |
Лист |
19 |
ПА 560Т 02 .02. ПЗ |
Константы равновесия реакции синтеза аммиака, вычисленные по экспериментальным данным
Температура, 0С | Давление, МПа | ||||||
0,098 | 0,98 | 4,91 | 9,81 | 29,43 | 58,86 | 98,10 | |
200 | 0,66 | 0,64880 | 0,69780 | 0,73680 | 0,91200 | 2,49300 | 10,35000 |
300 | 0,07 | 0,06238 | 0,06654 | 0,06966 | 0,08667 | 0,17330 | 0,51340 |
400 | 0,0138 | 0,01282 | 0,01310 | 0,01379 | 0,01717 | 0,02761 | 0,06035 |
500 | 0,004 | 0,00378 | 0,00384 | 0,00409 | 0,00501 | 0,00646 | 0,00978 |
600 | 0,00151 | 0,00152 | 0,00146 | 0,00153 | 0,00190 | 0,00200 | 0,00206 |
700 | 0,00069 | 0,00071 | 0,00066 | 0,00070 | 0,00087 | 0,00085 | 0,00052 |
Из приведенных таблиц и рисунка видим, что равновесный выход аммиака возрастает с повышением давления и понижением температуры[7].
Константа равновесия реакции синтеза аммиака, соответствующая уравнению (1), чаще всего в литературе определяется по уравнению:
(2)
где - равновесные парциальные давления соответственно аммиака, азота и водорода.
С помощью уравнения (2) по известной константе равновесия можно рассчитать равновесное содержание аммиака при данных условиях. Если исходить из одного моля равновесной газовой смеси с соотношением Н2:N2 = 3:1, то будем иметь[8]:
;
;
(3)
где Р – общее давление равновесной газовой смеси; zр – равновесная мольная доля аммиака.
Подставляя выражение 3 в 2 и решая квадратное уравнение, получаем квадратное уравнение для zр:
(4)
Известно, что термодинамическая константа равновесия является функцией только температуры и не должна зависеть от давления и состава исходной смеси. Если же рассмотреть данные таблицы 2, то видно, что значения Кр, вычисленные через парциальные давления газов, остаются практически независимыми от давления примерно до 9,8 МПа. При более высоких давлениях наблюдается заметное возрастание величины Кр. Объясняется это тем, что при низких и умеренных давлениях равновесную реакционную смесь можно рассматривать как смесь идеальных газов, для которой применим закон Дальтона. При высоких давлениях мы имеем дело с
Изм. |
Лист |
№ докум. |
Подпись |
Дата |
Лист |
20 |
ПА 560Т 02 .02. ПЗ |
Следовательно, уравнения (2) пригодно для расчета равновесия реакции синтеза аммиака только при пониженных и умеренных давлениях. Чтобы обойти эту трудность, А. Ларсон и Р. Додж предложили эмпирическое уравнение, описывающее зависимость Кр от температуры и давления, выведенное на основе экспериментальных данных:
(5)
где β – коэффициент, зависящий от давления;
I – константа интегрирования.
Значения β и I для давлений до 98,1 МПа представлены в таблице 3.
Таблица 3
Значения β и I для различных давлений
Давление, МПа | Коэффициент β | Константа интегрирования I |
0,98 | 0 | -1,993 |
4,91 | +1,256∙10-4 | -2,090 |
9,81 | +1,256∙10-4 | -2,113 |
29,43 | +1,256∙10-1 | -2,206 |
58,86 | +1,0856∙10-3 | -3,059 |
98,10 | +2,6833∙10-3 | -4,473 |
Для высоких давлений независимость константы равновесия от давления сохраняется в случае, если при расчете вместо значений парциальных давлений газов используют значения их фугативностей[10].
(6)
где – фугативности соответственно аммиака, азота и водорода в равновесной смеси.
Точные значения фугативностей компонентов газовых смесей можно рассчитать по уравнению Гиллеспая – Лерберга, но для этого требуются данные по сжимаемости газовых смесей в широком интервале температур, давлений и составов. Определение таких зависимостей связано с проведением сложных экспериментальных работ, вследствие чего данные по сжимаемости азота, водорода и аммиака в смеси, а следовательно, по их фугативностям, в литературе практически отсутствует. Поэтому уравнением, выраженным через точные значения фугативностей компонентов газовой смеси, пользуются редко. Более часто используют приближенные методы расчета на основе этого уравнения. Дело в том, что в ряде случаев можно, вводя упрощающие допущения, вычислить фугативность компонентов
Изм. |
Лист |
№ докум. |
Подпись |
Дата |
Лист |
21 |
ПА 560Т 02 .02. ПЗ |
Для высоких давлений, применяя правило Льюиса – Рендалла, имеем:
;
;
(7)
где ,
,
– фугативности компонентов аммиака, азота и водорода в равновесной смеси;
,
,
- фугативности чистых компонентов аммиака, азота и водорода при общем давлении реакционной смеси;zр,
,
–мольные доли компонентов в смеси[12].
Подставляя выражение 7 в 6 и решая квадратное уравнение, получаем квадратное уравнение для zр:
(8)
где А’ =
Значения констант равновесия, необходимые для расчетов равновесных концентраций аммиака по уравнениям (4) и (8), могут быть определены через стандартное изменение энергии Гиббса[13]:
(9)
Уравнения (4) и (8) применимы только для вычислений равновесных концентраций аммиака в стехиометрической азото-водородной смеси. Для нестехиометрических смесей и в присутствии инертных газов эти уравнения не пригодны, а уравнения (2) и (6) действительны.
Из термодинамики известно, что в случаях, когда реакционная смесь является смесью идеальных газов или идеальным раствором реальных газов, как азото-водородно-аммиачная смесь, максимальный выход продукта достигается при стехиометрическом соотношении исходных реагирующих веществ[13].
Рис. 3 показывает нам, что при отклонении азото-водородной смеси от стехиометрического состава уменьшается равновесное содержание аммиака. Аналогичная картина наблюдается и при разбавлении стехиометрической азотно-водородной смеси инертными газами – метаном и аргоном. При этом снижение равновесного содержание аммиака происходит в большей степени, чем соответствовало бы снижению парциальных давлений азота и водорода[14].
Рис. 3 – Зависимость содержания аммиака от состава АВС
Изм. |
Лист |
№ докум. |
Подпись |
Дата |
Лист |
22 |
ПА 560Т 02 .02. ПЗ |
(10)
где - равновесные мольные доли аммиака соответственно без инертных газов, т.е. при Nин = 0, и в их присутствии; Nин – мольная доля инертных газов в исходной смеси.
Рассчитанные по уравнению (10) равновесные концентрации аммиака в присутствии инертных газов приведены в таблице 4. Из нее видно, что влияние инертных газов тем сильнее, чем выше давление и ниже температура.
Рассчитанные по уравнению (10) равновесные концентрации аммиака в присутствии инертных газов приведены в таблице 4. Из нее видно, что влияние инертных газов тем сильнее, чем выше давление и ниже температура[18].
Таблица 4
Равновесные концентрации аммиака, для различного содержания инертных газов в исходной смеси (Р=29,4 МПа)
Содержание инертных газов, %(об.) | Температура, 0С | ||||
400 | 450 | 500 | 550 | 600 | |
5,00 10,00 20,00 | 42,5 38,5 31,4 | 32,4 29,4 23,9 | 24,0 21,6 17,7 | 17,3 15,7 12,8 | 12,5 11,3 9,2 |
Изм. |
Лист |
№ докум. |
Подпись |
Дата |
Лист |
23 |
ПА 560Т 02 . 03. ПЗ |
Разраб. |
Антипов Р.П. |
Провер. |
Тихомирова А.В |
Реценз |
Н. Контр. |
Утверд. |
Производство аммиака. Стадия синтеза Расчётно-пояснительная записка |
Лит. |
Листов |
42 |
КузГТУ. ХТНВиН .грХНбз-141 кафедра ХТНВиН гр.ХНбз-131 |
Метан.
Химическая формула ( СН 4 )
Газ не имеющий ни цвета ни запаха , легче воздуха малорастворим в воде.
Простейший углеводород, первый член гомологического ряда насыщенных углеводородов (алканов), устойчивый к химическим воздействиям. Склонен вступать в реакции радикального замещения (галогенирования , метанирования и др.). Сам по себе метан не токсичен и не представляет опасности для здоровья человека . Обогащение одоронатами делается для того , чтобы человек смог заметить утечку. Взрывоопасен при концентрации кислорода в воздухе 4,4%-17% . Класс опасности четвёртый.
Азот.
Химическая формула( N2).
Двухатомный газ – не имеет ни цвета, ни запаха, безвкусный , малорастворим в воде . Простое вещество , одно из самых распространённых на земле. Является основным компонентом воздуха (78,09% объёма), разделением которого получают промышленный азот ¾ которого идёт на синтез аммиака. Химически инертен по этому применяется для множества технологических процессов. Вступает в реакции с комплексными соединениями переходных металлов. Сам по себе азот не оказывает ни какого токсикологического действия на организм человека и млекопитающих, но при высоком давлении и большой концентрации вызывает опьянение или удушье . При быстром снижении давления азот вызывает кессонную болезнь.
Изм. |
Лист |
№ докум. |
Подпись |
Дата |
Лист |
24 |
ПА 560Т 03.03 ПЗ |
Химическая формула(Н2).
Газ – бесцветный нетоксичный, без цвета и запаха. Легче воздуха , плохо растворяется в воде. При смеси с воздухом или кислородом взрывоопасен. Растворим в этаноле и ряде металлов ( железе, никеле и др.).Основной способ получения в промышленности конверсия метана с водяным паром
СН4+Н2О=СО+3Н
Водород обладает высокой теплопроводностью примерно в семь раз больше теплопроводности воздуха. [19].
Изм. |
Лист |
№ докум. |
Подпись |
Дата |
Лист |
25 |
ПА 560Т 02 . 04. ПЗ |
Разраб. |
Антипов Р.П. |
Провер. |
Тихомирова А.В |
Реценз |
Н. Контр. |
Утверд. |
Производство аммиака. Стадия синтеза Расчётно-пояснительная записка |
Лит. |
Листов |
42 |
КузГТУ. ХТНВиН .грХНбз-141 кафедра ХТНВиН гр.ХНбз-131 |
Технологическая схема представлена на рис.5.
Рис. 5 – Технологическая схема производства аммиака
1 – АВС; 2 – обагощенная АВС; 3 – Природный газ; 4 – синтез-газ; 5 – циркуляционый газ; 6 – жидкий аммиак; 7 – жидкий аммиак на выдачу; 8 – вода t=60 0C; 9 – вода t=120 0C; 9а – линия продувочных газов; 10, 11 – вода оборотная; КК – конденсационная колонна; ХГ – холодильник газа; ВТ – выносной теплообменник; ПГ – подогреватель газа; КСА – колонна синтеза аммиака; АВО – аппарат воздушного охлаждения; CЖА – сепаратор жидкого аммиака; МФ – мафгнитный фильр; Е1, Е2 – ёмкость; И1, И2 – испаритель; К – компрессор; ККПГ – конденсационная колонна продувочных газов; ИПГ – испаритель продувочных газов; ВР1, ВР2 – вентиль регулирующий.
Свежая азотоводородная смесь (АВС) с давлением 24МПа (240 кгс/см2), направляется в нижнюю часть конденсационной колонны КК, где, барботируя через слой жидкого аммиака, дополнительно промывается от следов влаги и углекислого газа и смешивается с циркуляционым газом поступающим из компрессора К. Смесь свежего и циркуляционного газа через регулирующий вентиль ВР2 направляется в межтрубное пространство выносного теплообменника ВТ. В межтрубном пространстве теплообменника ВТ газ нагревается до температуры не более 1950С, отнимая тепло у встречного газа, идущего по трубкам, и далее поступает в колонну синтеза аммиака КСА.
В колонне синтеза аммиака КСА газ сначала проходит снизу вверх по кольцевому зазору между корпусом колонны и насадкой, охлаждая корпус колонны.
Здесь газ дополнительно нагревается теплом прореагировавшего газа, выходящего по трубкам теплообменника из катализаторных трубок до температуры начала реакции и поступает последовательно на 1-ю и 2 радиальные полки колонны синтеза, на которых при давлении до 24МПа (240 кгс/см2) и температуре не более 5300С происходит экзотермическая реакция образования аммиака из азотоводородной смеси.
Далее газовая смесь поступает в межтрубное пространство подогревателя ПГ, где избыточное тепло реакции синтеза используется для подогрева природного газа.
Пройдя колонну синтеза аммиака КСА синтез-газ с температурой не более 2300С проходит межтрубное пространство холодильника ХГ, охлаждается до температуры не более 700С оборотной водой, идущим по трубному пространству, проходя через трубное пространство выносного теплообменника ВТ и поступает в аппарат воздушного
Изм. |
Лист |
№ докум. |
Подпись |
Дата |
Лист |
26 |
ПА 560Т 02 . 04. ПЗ |
Из циркуляционной ступени компрессора К циркуляционный газ поступает на вторичную конденсационную систему, состоящую из конденсационной колонны КК. Циркуляционный газ заходит сверху в конденсационную колонну КК, проходит межтрубное пространство встроенного теплообменника ВТ, охлаждается встречным потоком газа, идущим по трубкам до (18÷20)0С.
Пройдя центральную трубу в коденсационой колонне КК газ поступает в испарители жидкого аммиака И-1,2, проходит по U-образным трубкам высокого давления, где охлаждается до температуры (+3 ÷ -6)0С аммиаком, кипящим в межтрубном пространстве испарителя при температуре (–10)0С.
Испарители по циркуляционному газу работают параллельно. Аммиачная система у них разомкнута. Газообразный аммиак из межтрубного пространства испарителя И1 направляется далее на охлаждение(на схеме не показано).
Газообразный аммиак из межтрубного пространства испарителей И-2,1 с давлением (0,17÷0,2)МПа ((1,7÷2)кгс/см2) поступает на склад жидкого аммиака (на схеме не показано).
В испарительи И-1,2 и ИПГ жидкий аммиак подается из емкости Е1.
Из скпаратора СЖА часть охлажденного циркуляционного газа и сконденсировавшегося аммиака поступает в сепарационную часть конденсационной колонны продувочных газов ККПГ, где происходит
Изм. |
Лист |
№ докум. |
Подпись |
Дата |
Лист |
27 |
ПА 560Т 02 . 04. ПЗ |
Жидкий аммиак, отделившийся в сепараторе СЖА, проходит мафгнитный
Изм. |
Лист |
№ докум. |
Подпись |
Дата |
Лист |
28 |
ПА 560Т 02 . 04. ПЗ |
Изм. |
Лист |
№ докум. |
Подпись |
Дата |
Лист |
29 |
ПА 560Т 02 . 05. ПЗ |
Разраб. |
Антипов Р.П. |
Провер. |
Тихомирова А.В |
Реценз |
Н. Контр. |
Утверд. |
Производство аммиака. Стадия синтеза Расчётно-пояснительная записка |
Лит. |
Листов |
42 |
КузГТУ. ХТНВиН .грХНбз-141 кафедра ХТНВиН гр.ХНбз-131 |
М АТЕРИАЛЬНЫЙ БАЛАНС
Современное химическое производство представляет собой сложную систему по числу аппаратов и материально-тепловых потоков. В основе решения задач проектирования и эксплуатации химических производств лежит расчёт материально-тепловых балансов химико-технологических систем (ХТС).
Под материальным балансом ХТС понимают теоретический (фиктивный) материальный баланс, рассчитанный с учётом стехиометрического уравнения процесса, степени превращения и избирательности.
По данным материального баланса определяют часовые потоки сырья, готовой продукции, побочных материалов и отходов производства, часовые расходы воды и сточных вод, рассчитывают аппаратуру, определяют габариты производственных зданий, складов сырья и готовой продукции.
В основе материального баланса лежит закон сохранения массы.Применительно к материальному балансу любого технологического процесса это означает, что масса веществ, поступающих на технологическую операцию – приход, равна массе всех веществ, получающихся в результате этой операции –расход.
При составлении материальных балансов ХТС рассматривают внешние (технологические) и внутренние (условные) источники или стоки вещества системы. Внешние стоки веществаХТС соответствуют материальным физическим потокам, которые поступают на переработку и образуются в результате функционирования системы. Внутренние стоки вещества соответствуют количеству компонента, вступившего в химическую реакцию, или количеству компонента, образовавшегося в результате химического превращения. Принято считать, что каждому внутреннему стоку вещества соответствует теоретический (фиктивный) материальный баланс.
Теоретический (фиктивный) материальный баланс ХТС составляется как по общему массовому расходу вещества, так и по массовому расходу компонентов физических потоков[19].
Изм. |
Лист |
№ докум. |
Подпись |
Дата |
Лист |
30 |
ПА 560Т 02 . 05. ПЗ |
Производительность – 560000 т/г
Давление в колонне – P = 24 МПа
Содержание аммиака в газе на выходе – СHN3К = 15 %
Содержание аммиака в газе на входе – СHN3Н = 3,08 %
Содержание инертных примесей - Син=4% (метан – 3,5%, аргон – 0,5%)
Отношение водорода и азота в АВС 3,007:1[20]
Схема материальных потоков представлена на рис. 4.
Рис. 5 – Схема материальных потоков
Изм. |
Лист |
№ докум. |
Подпись |
Дата |
Лист |
31 |
ПА 560Т 02 . 05. ПЗ |
Расчет проведен по рекомендации[22].
Образование аммиака в колонне синтеза:
a = = = 11,56 %
Сокращение объема газовой смеси вследствие синтеза аммиака в колонне определяем по формуле:
s = = = 0,8963
Производительность колонны синтеза, отнесенная к 1 м3 катализатора определяется по формуле:
q = 0.771 m a s = 0,771 × 25000 × 0,1156 × 0,8963= 1997,13 кг/ч
где 0,771 – плотность газообразного аммиака, кг/м3;
m – объемная скорость газовой смеси па входе в колонну синтеза, согласно принятым исходным данным m = 25000 ч-1[20];
a – образование аммиака в колонне синтеза.
Согласно справочным данным, мольные массы компонентов смеси[21]
MCH4 = 16 кг/кмоль
MN2 = 28 кг/кмоль
MH2 = 2 кг/кмоль
MAr = 40 кг/кмоль
MNH3 = 17 кг/кмоль
Плотности компонентов смеси[21] :
CH4 =0,655 кг/м3
N2 =1,25 кг/ м3
H2 = 0,089 кг/ м3
Ar = 1,4 кг/ м3
NH3 = 0,771 кг/ м3
В поступающем газе содержится СHN3Н объём аммиака, СH2Н объём водорода и СN2Н объём азота, то при образовании х моль аммиака, согласно реакции:
N2 + 3H2 = 2NH3
Объём азота уменьшиться на:
Объём водорода уменьшиться на:
Изм. |
Лист |
№ докум. |
Подпись |
Дата |
Лист |
32 |
ПА 560Т 02 . 05. ПЗ |
Общий объём смеси после реакции:
1 - =
-
=
+
+
+ =1-х*11,202*
-х*33,645*
+х*22,091*
=1-х*22,769 нм3/ч
В этом объёме содержится аммиака:
нм3/ч
Тогда общая концентрация аммиака в выходящем газе:
Отсюда х:
моль/ч NH3 или
=
кг/ч NH3
Для получения 63930 кг/ч аммиака в колонну должно поступать газовой смеси:
нм3/ч
Объёмная концентрация азота и водорода в смеси:
СN2+H2Н =100-( Син + СNH3Н) =100-(4+3,08)=92,92 %
На входе в колонну азота:
СN2Н= СN2+H2Н /3,007 +1= 92,92/3,007+1=23,19%
На входе в колонну водорода
СН2Н= СN2+H2Н - СN2Н = 92,92-23,19=69,73 %
В поступающей газовой смеси содержится:
Изм. |
Лист |
№ докум. |
Подпись |
Дата |
Лист |
33 |
ПА 560Т 02 . 05. ПЗ |
VNH3Н = * СNH3Н =803097,01 × 0,0308 = 24735,39 нм3/ч;
mNH3Н= VNH3Н× NH3=24735,39×0,771=18772,39 кг/ч
Водорода
VH2 Н = 803097,01 × 0,6973 = 559999,54 нм3/ч;
mH2 Н = 559999,54 × 0,089 = 49999,96 кг/ч;
Азота
VN2 Н = 803097,01 × 0,2319 = 186238,2 нм3/ч;
mN2 Н = 186238,2 × 1,25 = 232797,75 кг/ч;
Аргона
VAr Н = 803097,01 × 0,005 = 4015,48 нм3/ч;
mAr Н = 4015,48 × 1,4 = 7170,5 кг/ч;
Метана
VCH4 Н = 803097,01 × 0,035= 28108,39 нм3/ч;
mN2 Н = 28108,39 × 0,655= 20077,42 кг/ч;
Приход газов:
mNH3Н+ mH2 Н+ mN2 Н+ mAr Н+ mN2 Н=18772,39+49999,96+232797,75+7170,5+
+20077,42=328818,02 кг/ч
В колонне образуется 63930 кг/ч аммиака, для этого расходуется по реакции:
N2 + 3H2 = 2NH3
Азота
MN2 Р=g* MN2/ 2*MNH3=63930*28/17*2=52648,24 кг/ч
Водорода
mH2 Р= 63930*2*3/17*2=11281,76 кг/ч
В газовой смеси на выходе содержится аммиака:
Аммиака
mNH3К= mNH3Н+ g =18772,39 +63930 =82702,39 кг/ч
VNH3К = mNH3К / NH3 =82702,39/ 0,771=108972,57 нм3/ч;
Водорода
mH2К= mH2Н-mH2Р =49999,96-126355,71=433643,83 кг/ч
VH2К = mH2К / H2 =433643,83 / 0,089=433643,83 нм3/ч;
Азота
mN2К= mN2Н-mN2Р =232797,75-52648,24=180149,51 кг/ч
VN2К = mN2К / N2 =180149,51 / 1,25=144119,61 нм3/ч
Кол-ва инертных газов не изменятся, следовательно их расходы:
Аргона
VAr К =VAr Н = 4015,48 нм3/ч;
mAr К =mAr Н = 7170,5 кг/ч;
Метана
VCH4 К =VCH4 Н = 28108,39 нм3/ч;
mN2 К =mN2 Н = 20077,42 кг/ч;
Изм. |
Лист |
№ докум. |
Подпись |
Дата |
Лист |
34 |
ПА 560Т 02 . 05. ПЗ |
Таблица 5
Материальный баланс колонны синтеза аммиака
Статья | Приход | Расход | ||||
![]() | ![]() | ![]() | ![]() | ![]() | ![]() | |
N2 | 186238,2 | 23,19 | 232797,75 | 144119,61 | 20,05 | 180149,51 |
H2 | 559999,54 | 69,73 | 49999,96 | 433643,83 | 60,32 | 38718,2 |
Ar | 4015,48 | 0,5 | 7170,50 | 4015,48 | 0,56 | 7170,50 |
CH4 | 28108,39 | 3,5 | 20077,42 | 28108,39 | 3,91 | 20077,42 |
NH3 | 24735,39 | 3,08 | 18772,39 | 108972,57 | 15 | 82702,39 |
Итого | 803097 | 100 | 328818,02 | 718859,88 | 100 | 328818,02 |
Изм. |
Лист |
№ докум. |
Подпись |
Дата |
Лист |
35 |
ПА 560Т 02 . 05. ПЗ |
Тепловой (энергетический) баланс отражает закон сохраненияэнергии, согласно которому в замкнутой системе сумма всех видов энергии постоянна. Применительно к тепловому балансу любого технологического процесса закон сохранения энергии формулируется следующим образом: приход тепла Qприх в данном аппарате должен быть равен расходу тепла Qрасх в том же аппарате.
Исходные данные[20]:
Твход = 3000С;
Твыход = 5500С;
Расчет проведен по рекомендации[22].
Согласно уравнению теплового баланса:
Qпр + Qхр = Qр + Qпот+ Qотв
где
; кДж/ч
Теплота химической реакции - Qх.р = – ΔНх.р (ΔН<0); кДж/ч
Теплота расхода веществ - ; кДж/ч
Потери - , кДж/ч
Кол-во теплоты которое следует отвести - , кДж/ч
Из справочника физико-химических величин выписываю необходимые для расчёта данные (таблица 6) [19].
Таблица 6
Термодинамические свойства веществ
№ | Компонент |
| Коэффициенты уравнения СР = f(T) | |||
a | b | c | ||||
1 | Азот | 0 | 27,88 | 4,27∙10-3 | - | |
2 | Водород | 0 | 27,28 | 3,26∙10-3 | 0,5∙105 | |
3 | Метан | -393,51 | 44,14 | 9,04∙10-3 | -8,54∙105 | |
4 | Аммиак | -45,94 | 29,80 | 25,48∙10-3 | 1,67∙105 | |
5 | Аргон | -69,2 | 16,2 | 2,3∙10-3 | 1,9∙105 | |
Находят Qпр – физическое тепло, вносимое входящими газами. Для этого определяют количество теплоты, вносимое каждым газом при температуре 300 °С.
Переводят температуру на входе из °С в К:
Твх = 300 + 273 = 573 К.
Изм. |
Лист |
№ докум. |
Подпись |
Дата |
Лист |
36 |
ПА 560Т 02 . 05. ПЗ |
Переводят мольную теплоёмкость в удельную по формуле:
Теплосодержание входящих газов определяют:
/ч
Находят Qх.р – теплоту экзотермической реакции. Для этого рассчитывают тепловой эффект реакции по уравнению Кирхгофа при температуре в аппарате.
Определяют тепловой эффект реакции при стандартных условиях по формуле:
Переводят температуру на выходе из °С в К:
Твых = 550 + 273 = 823 К.
Рассчитывают температуру в аппарате по формуле:
Вычисляют коэффициенты, необходимые для решения уравнения Кирхгофа по формуле:
Δа = Σνi ∙аi,прод – Σνi ∙аi,исх
Изм. |
Лист |
№ докум. |
Подпись |
Дата |
Лист |
37 |
ПА 560Т 02 . 05. ПЗ |
/моль
Определяют количество теплоты, выделяемое в результате протекания реакции:
Qх.р = – ΔНх.р = 52110,84 Дж/к = 52,11 кДж/моль
Количество теплоты, отнесенное к 1 молю азота, определяют по формуле:
Рассчитывают количество тепла, выделившегося из 1 кг азота, определяют по формуле:
Находят, сколько азота прореагировало в результате реакции:
Изм. |
Лист |
№ докум. |
Подпись |
Дата |
Лист |
38 |
ПА 560Т 02 . 05. ПЗ |
Qх.р = ∙ 3722,14 = 129453125,93 кДж/ч
По формуле определяют количество тепла, поступившего в реактор:
ΣQприх = Qпр + Qхр = 110055901,69+ 129453125,93 = 239509027,62 кДж
Находят Qр – физическое тепло, уносимое выходящими газами. Для этого определяют количество теплоты, уносимое каждым газом при температуре 823 К.
Мольную теплоёмкость для каждого вещества при температуре 823 К рассчитывают:
Переводят мольную теплоёмкость в удельную по формуле:
Теплосодержание выходящих газов:
/ч
Таким образом, Qр < Qприх– тепла расходуется меньше, чем подводится в реактор, поэтому необходимо отводить тепло от системы.
Потери теплоты в окружающую среду (Qпот) принимают 5 % от прихода теплоты, и рассчитываем по формуле:
Qотв = ·ΣQприх = 0,05 *239509027,62 = 11975451,38 кДж/ч
Теплота, отводимая через змеевики, помещённые внутри аппарата, рассчитываем по формуле:
Результаты расчета теплового баланса сведены в таблицу 7
Изм. |
Лист |
№ докум. |
Подпись |
Дата |
Лист |
39 |
ПА 560Т 02 . 05. ПЗ |
Тепловой баланс синтеза аммиака
Статья | Приход | Статья | Расход | ||
кДж/ч | ГДж/ч | кДж/ч | ГДж/ч | ||
Qпр – тепло вносимое вхо-дящими газами | 110055901,69 | 110,06 | Qр – тепло, уносимое газами | ![]() | 143,98 |
Qхр - теплота экзотермической реакции | 129453125,93 | 129,45 | Qпот – потери теплоты в окружающую среду | 11975451,38 | 11,98 |
Qотв – теплота, отводимая из аппарата | ![]() | 83,56 | |||
Итого | 239509027,62 | 239,51 | 239509027,62 | 239,51 |
ВЫВОДЫ
В курсовой работе рассмотрена технология получения синтетического аммиака производительностью 560 тыс. тонн в год. В аналитическом обзоре проведен анализ существующих способов получения аммиака.
В разделе теоретические основы процесса приведены технологические основы процесса синтеза аммиака.
Изучена технологическая схема производства и ее описание.
В расчетной части проведен расчет материальных и тепловых балансов.
СПИСОК ЛИТЕРАТУРЫ
1. Андреев Ф.А., Карган С.И., Козлов Л.И., Приставко В.Ф. Технология связанного азота. – М., 2008.
2. Кутепов А.М., Бондарева Т.И., Беренгартен М.Г. Общая химическая технология. – М., Высшая школа, 2000.
3. Справочник азотчика. – М., Химия, 1987.
4. Малина И.К. Развитие исследований в области синтеза аммиака. – М., Химия, 1993.
5. Тюкаева,О. А. // Хим. Промышленность за рубежом. - 1987. - № 12. -С.1-50
6. КузнецовЛ.Д. и др. // Азотная пром-тъ.- НИИТЭхим - 1967.-№4.- С.19.
7. Рабина, П.Д. Химия и технология азотных удобрений / П. Д. Рабина , Л. Д. Кузнецов , Т. Я. Малышева и др. // Труды ГИАП. М.: - 1971. - Вып 11.- С.
8. Дмитриенко Л.М. и др. //Труды 4-го Международного конгресса по катализу. М.: Наука.- 1970.- Т.1.- С. 328
9. Мищенко, Ш.Ш. и др. Химия и технология азотных удобрений. - М.: НИИТЭхим, 1971.- Вып 11.- С.53, 66, 75.
10. Лачинов С.С., Овчаренко Б.Г. Авт. Свид. СССР 118222// Б. И- 1964.- №14
11. Патрикевич Н. И. // Хим. промышленность за рубежом.- 1988.- № 2.- С. 55-86
12. Бершанский В.П.,Мнушкин ИЛ., СыркинА.М. // Сб. «Современные проблемы истории естествознания в области химии, химической технологии и нефтяного дела».- Уфа : Реактив, 2002.- С. 184-192
13. S.M. Yunusov, V.A. Likholov, V.B. Shur. Applied Catalysis A : General. 1997 (158) p. 35-39.
14.Claus J.Y. Jacobsen. Chem. Commun., 2000, P 1057-1058.
15. Huazhang, L. Opportunity of synthesis of ammonia under low pressure at use of catalysts of series A-301 / L. Huazhang, H. Zhangneg, L. Xiaonian // Huagong xuebao =J. Chem. Ind. and Eng. – 2001. - №12. – P. 1063-1067.
16. Бродская, И. Г. Разработка технологии рут ениевого катализатора синтеза аммиака/ И. Г. Бродская , Л. М. Дмитриенко , Р. В. Чеснокова , Л. Д. Кузнецов // Катализаторы в промышленности. – 2001. - № 3. - С .16-29.
17. Боресков, Г.К. Гетерогенный катализ / Г. К. Боресков. - М. : Наука, 1986. - 300с.
18. Рудницкий, Л. А. Механизм взаимодействия металлов с газами / Л. А. Рудницкий , М. И. Иванов , П. Д. Рабина , Л. Д. Кузнецов // Кинетика и катализ. – 1968. – №89. – С. 36-41.
19. Краткий справочник физико-химических величин» под редакцией К.П. Мищенко и А.А. Равделя, Л.: Химия, 1974 г. – 200 стр.
20. Постоянный технологический регламент №1 цеха синтеза аммиака КАО «Азот». – Кемерово, 2005 – 250с.а Allbest.ru
21. Павлов К.Ф.,Романков П.Г., Носков А.А. Примеры и задачи по курсу процессов и аппаратов химических технологий: Учеб. Пособие. – 12-е изд., стереотипное.-М.: ООО ТИД «Альянс»,2005.-567с.
22. Кузнецова, И.М Общая химическая технология: Материальный баланс химико-технологического процесса / И.М. Кузнецова, Х.Э. Харлампиди, Н.Н. Батыршин. – М.: Логос, 2007 – 264с.
23. Лащинский А.А., Толчинский А.Р. Основы конструирования и расчета химической аппаратуры: Справочник. 3-е изд., стереотипное. – М.: ООО ИД «Альянс», 2008. – 752 с.
24. Михалев М.Ф., Третьяков Н.П., Мильченков А.И., Зобнин В.В. Расчет и конструирование машин и аппратов химических производств: Примеры и задачи: Учеб. Пособие для студентов вузов/Под общ. ред. Михалева М.Ф.- Л.: Машиностроение, Ленингр. Отд-ние, 1984. – 301 с., ил.
25. Лащинский А.А. Конструирование сварных химических аппаратов: Справочник. – Л.: Машиностроение. Ленингр. Отд-ние, 1981. – 382 с., ил
Дата добавления: 2019-07-15; просмотров: 538; Мы поможем в написании вашей работы! |
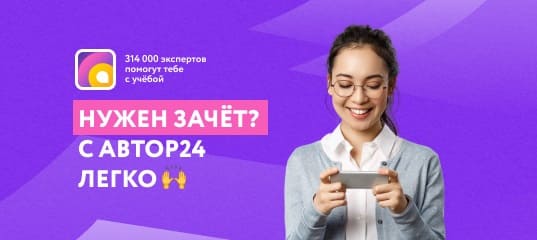
Мы поможем в написании ваших работ!