Механизированная аргонодуговая сварка плавящимся электродом.
2.4.1. Механизированная сварка плавящимся электродом непрерывным током
Механизированную сварку плавящимся электродом применяют для получения стыковых, тавровых, нахлесточных и других соединений алюминия и его сплавов толщиной 4-6 мм и более. Этот способ является самым производительным среди ручных видов сварки. За границей наиболее распространенный среди видов сварки алюминия.
Отличием механизированной сварки алюминия от традиционной механизированной сварки сталей является: использование аргона в качестве защитного газа, тефлоновых подающих каналов вместо стальных, специальной формы роликов в подающем механизме, специальных мундштуков на горелках. В СССР ввиду отсутствия дешевых тефлоновых каналов этот метод сварки был незаслуженно не востребован.
Электрическая дуга при этом способе сварки горит между изделием и плавящимся электродом (проволокой), который подается в зону дуги обычно с постоянной скоростью.
Надежное разрушение пленки окислов при механизированной сварке плавящимся электродом достигается лишь при питании дуги постоянным током обратной полярности. Механизм удаления окисной пленки в этом случае заключается в разрушении и распылении ее тяжелыми положительными ионами, бомбардирующими катод (эффект катодного распыления).
Недостатком способа сварки алюминия плавящимся электродом является некоторое снижение по сравнению со сваркой неплавящимся электродом показателей механических свойств. В частности, уменьшение прочности шва об
|
|
ясняется тем, что электродный металл, проходя через дуговой промежуток, перегревается в большей степени, чем присадочная проволока при сварке неплавящимся электродом. Также происходит худшее удаление окисной пленки, т.к. при аргонодуговой механизированной сварке непрерывным током сварочный процесс сопровождается короткими замыканиями, в момент которых катодное распыление отсутствует.
Для устранения этих недостатка в сварочной установке ВД-306ДК применены принципиально новые технические решения: низковольтная постоянная подпитка сварочной дуги напряжением 10-11В, которая накладывается на общую картину сварочного напряжения.
Для сварки, как правило, применяют проволоку диаметром 1.2-1.6 мм, так как из-за недостаточной жесткости сварка алюминиевой проволокой меньшего диаметра затруднена. Применение проволоки большего диаметра принципиально возможно, однако сварные соединения в этом случае получаются крупночешуйчатые, что ухудшает их внешний вид и механические свойства.
Установки для механизированной сварки состоят из выпрямителя (ВД-306ДК и т.д.), механизма подачи (ПДГО-508, ПДГО-510 и т.д.) со специальными роликами.
|
|
Конструкция механизма подачи должна обеспечивать надежное и стабильное поступление мягкой алюминиевой проволоки. Обычно в таких механизмах предусматривают две пары специальных ведущих и прижимных роликов, что уменьшает возможность проскальзывания проволоки и ее сминания.
Наиболее применимы сварочные горелки немецкой фирмы «Abicor Binzel» с тефлоновым подающим каналом. Следует отметить, что в виду использования аргона, как защитного газа, чаще всего применяют водоохлаждаемые модели горелок. Сопло горелки должно обеспечивать надежную защиту инертным газом жидкой сварочной ванны. Диаметр сопла горелки для механизированной сварки алюминия обычно 18-22 мм.
Ориентировочные режимы механизированной аргонодуговой сварки алюминия плавящимся электродом приведены в табл. 2.6.
Таблица 2.6.
Ориентировочные режимы механизированной аргонодуговой сварки алюминия и его сплавов плавящимся электродом. [5]
Тип соединения | b, мм | dЭЛ.ПР., мм | IСВ, А | UД, В | VCВ, м/ч | Расход аргона, л/мин | Число проходов |
Встык, без разделки кромок | 4-6 8-10 12 | 1,5-2,0 1,5-2,0 2,0 | 140-240 220-300 280-300 | 19-22 22-25 23-25 | 20-30 15-25 15-18 | 6-10 8-10 10-12 | 2 2 2 |
Встык, с Vобразной разделкой кромок на подкладке | 5-8 10-12 | 1,5-2,0 2,0 | 220-280 260-280 | 21-24 21-25 | 20-25 15-20 | 8-10 8-12 | 2-3 3-4 |
Встык, с Х образной разделкой кромок | 12-16 20-25 30-60 | 2,0 2,0 2,0 | 280-360 330-360 330-360 | 24-28 26-28 26-28 | 20-25 18-20 18-20 | 10-12 12-15 12-15 | 2-4 4-8 10-40 |
Тавровое, угловое и нахлесточное | 4-6 8-16 20-30 | 1,5-2,0 2,0 2,0 | 200-260 270-330 330-360 | 18-22 24-26 26-28 | 20-30 20-25 20-25 | 6-10 8-12 12-15 | 1 2-6 10-40 |
|
|
Особый интерес при механизированной сварке алюминия вызывает использование источника питания ВД-306ДК с механизмом подачи ПДГО-508(510) (полуавтоматический модуль мультисистемы «Сорока»). Использование этого источника вызывает большой промышленный интерес в виду того, что в нем применены принципиально новые технические решения: низковольтная постоянная подпитка сварочной дуги напряжением 10-11В. Особенностью низковольтной подпитки напряжения на сварочной дуге является наложение постоянно действующего отрицательного потенциала. Это обеспечивает непрерывное горение электрической дуги, улучшает удаление окисной пленки, обеспечивает более мягкий переход капель электродного металла в сварочную ванну, уменьшает разбрызгивание и улучшает стабильность горения электрической дуги и качество формирования сварного соединения. Высоковольтная подпитка служит для облегчения зажигания дуги. Таким образом, в указанной схеме стало возможным производить регулирование продолжительности коротких замыканий и их частоты, возможность регулирования тока короткого замыкания. Установка имеет также возможность регулировки угла наклона вольтамперных характеристик и возможность производить сварку на значительном удалении от источника питания (до 20м). Последнее обеспечивается за счет применения обратных связей по току и напряжению на дуге. Для реализации последнего необходимо применять подающий механизм ПДГО-510Т и выпрямитель ВД-306ДК. Следует напомнить, что этот источник обеспечивает высококачественную сварку алюминия и его сплавов в режиме ручной дуговой сварки. Кроме того, его использование позволяет решить проблемы комплектации сварочной техникой цехов, когда все виды сварки (ММА, МИГ,ТИГ) можно производить на базе одного выпрямителя, комплектуя его различными приставками (БУСП-ТИГ, ПДГО) для реализации различных технологических процессов.
|
|
Механические свойства сварных соединений из сплава АМг6 толщиной 10 мм, выполненных механизированной сваркой на традиционных источниках питания (типа ВДУ-506) следующие [7]: .В = 30,6 кг/мм2, угол загиба . = 133 град.
2.4.2. Механизированная импульсно-дуговая сварка плавящимся электродом.
Повысить качество металла шва алюминиевых сплавов удается применением техники управляемого переноса металла при импульсно-дуговой сварке.
Импульсно-дуговая сварка плавящимся электродом отличается от обычной тем, что на постоянный ток обратной полярности, получаемый от основного источника питания, накладываются кратковременные импульсы тока с определенной частотой (как правило, 50 или 100Гц). Импульсы генерируются импульсным устройством для получения мелкокапельного направленного переноса электродного металла через дугу при более низких значениях сварочного тока, чем это имеет место при естественном мелкокапельном переносе. Величину и длительность импульсов сварочного тока выбирают такими, чтобы можно было обеспечить управляемый перенос металла с торца электрода небольшими каплями в широком диапазоне токов. Как правило, в паузах между импульсами значение тока небольшое, но достаточное для поддержания горения сварочной дуги, при котором ввод теплоты в изделие уменьшается и отсутствует перенос металла.
Импульсно-дуговая сварка обеспечивает повышение механических свойств наплавленного металла и сварных соединений в целом, улучшает стабильность процесса, позволяет выполнять сварку в различных пространственных положениях с улучшенным формированием швов, существенно стабилизировать провар корня шва.
Для механизированной импульсно-дуговой сварки плавящимся электродом используют источник питания ВДГИ-302, который комплектуется подающим механизмом ПДИ-304.
Ориентировочные режимы механизированной импульсно-дуговой сварки алюминия и его сплавов плавящимся электродом в аргоне приведены в табл. 2.7.
Таблица 2.7.
Ориентировочные режимы механизированной импульсно-дуговой сварки алюминия и его сплавов плавящимся электродом в аргоне. [5]
b, мм | dЭЛ.ПР., мм | Частота импульсов, 1/с | , А | UД, В | , м/ч | Расход аргона, л/мин | Число проходов |
4 | 1,4-1,6 | 50 | 130-150 17- | 19 20- | 25 | 10-12 | 1 |
5 | 1,4-1,6 | 50 | 140-170 17- | 19 20- | 25 | 10-13 | 1 |
6 | 1,4-1,6 | 100 | 160-180 18- | 21 20- | 25 | 12-14 | 1 |
8 | 2,0 | 100 160- | 190 22-24 | 25- | 30 12- | 14 2 | |
10 | 2,0 | 100 220- | 280 24- | 26 25- | 30 14- | 16 | 2 |
В последние годы широкое распространение при импульсно-дуговой сварке алюминия получили инверторные установки. Наиболее характерным представителем является установка для механизированной сварки типа Sinermig – 401 («OZAS»). Работа источника осуществляется на частоте 26 кГц с возможностью наложения дополнительных импульсов регулируемой амплитуды и скважности. Применение дополнительных импульсов позволяет увеличить производительность на 25% (по данным ОАО «Адмиралтейские верфи»). Использование этого источника позволяет получать кроме указанных выше возможностей, еще и формирование швов с обратным валиком и т.д., что часто требуется при сварке трубопроводов. Это достигается за счет возможности регулировки амплитуды и скважности импульсов, что невозможно на установке ВДГИ-302, где импульсы следуют постоянной амплитуды и частоты. Однако, данных по механическим свойствам изделий из алюминия и его сплавов, сваренных на таком источнике, не существует, ввиду его новизны, поэтому, точно делать выводы о применимости его для сварки конструкций из алюминиевых сплавов нельзя. В данной работе ниже приводится систематические данные по сравнению механических свойств на различных источниках питания при различных видах сварки.
3. Оценка способов дуговой сварки алюминия и его сплавов.
1. Электродуговая сварка алюминия является сложным процессом и требует точного поддержания параметров технологического процесса. Это обусловлено специфическими свойствами алюминия (низкая температура плавления ТПЛ =
VCВ
IСВ 6600С, высокая теплопроводность . = 0.52 кал/см.сек.0С, высокая скорость кристаллизации металла шва, высокое сродство к кислороду, высокий коэффициент линейного расширения . = 24,58.10-6). При нарушении технологии швы могут быть плохого качества. Основными дефектами являются непровары, прожоги, поры, трещины, окисные и вольфрамовые включения, а также неудовлетворительное формирование шва.
2. При всех видах электродуговой сварки алюминия применяют специальные технологические и конструктивные меры, способствующие удалению окисной пленки с поверхности свариваемого металла, шлаковых включений, снижению загазованности сварочной ванны, уменьшающие коробление и т.д., которые описаны в настоящей работе.
3. Принципиально дуговая сварка алюминия и его сплавов может осуществляться всеми известными методами: ручная дуговая сварка покрытыми электродами, аргонодуговая сварка неплавящимся электродом (симметричным переменным током, асимметричным переменным током, импульсная), плазменная сварка, полуавтоматическая аргонодуговая сварка плавящимся электродом (с использованием источников питания, выполненных по стандартной схеме выпрямления, с использованием низковольтных и высоковольтных подпиток напряжения на сварочной дуге – комбинированная вольтамперная характеристика, с наложением импульсов на сварочное напряжение). Особое внимание при использовании этих методов необходимо обратить на то, что сварку необходимо осуществлять на обратной полярности или переменном токе. Этот процесс промышленно освоен. Применение сварки на прямой полярности принципиально возможно и обеспечивает высокое качество но находится в стадии лабораторных образцов. В табл. 3.1 приведено сравнение механических свойств сварного соединения из сплава АМГ-5, выполненного различными методами и наличия внутренних дефектов. Сварка производилась на сплаве АМг5, S = 2.5 мм, = 1.2 мм.
Таблица 3.1
Зависимость механических свойств сварного соединения из АМг-5 от вида сварки
Вид сварки | Установка | Режим сварки | .В, кгс/мм2 | ., град | Дефекты | |||||
Исходный материал | 32 |
| ||||||||
Механизированная сварка плавящимся электродом | ВС-300Б | =110А, UД = 18В | 19 | 105 | П1,0; 7П0,3 | |||||
ВДУ-506 | =125А, UД = 18В | 21 | 125 | 3П0,3; П1,0 | ||||||
ВД-506ДК | =120А, UД = 17В | 26 | 45 | 10П0,3 | ||||||
Механизированная импульсно-дуговая сварка плавящимся электродом | ВДГИ-302 | f = 100Гц, =100А, UД = 20В | 10 | 90 | 2Н5,0; 6П0,3; 2П1,0 | |||||
ВДГИ-302 | f = 50Гц, IСВ = 100А, UД = 20В | 27 | 103 |
| ||||||
Синермиг-401 | = 87А, UД = 16В | 18 | 130 | 3П1,0; 3П0,5 | ||||||
IСВ IСВ IСВ IСВ IСВ dПР
Аргонодуговая сварка неплавящимся вольфрамовым электродом с подачей присадочной проволоки | УДГУ-351 | Симметричный ток, IСВ = 50А | 16 | 37 | Ц5В0,5; 5П0,3; В0,5 | ||||
УДГУ-351 | Асимметричный ток, IСВ = 50А, КАС = 0.56 | 9 | 90 | 3П0,3; В2,0 | |||||
УДГУ-351 | Асимметричный ток, IСВ = 50А, КАС = 0.43 | 26 | 83 | 4С5В0,5; 2В0,5 | |||||
УДГУ-351 | Пульсир. режим = 0.15с, tп= 0.15с, IСВ = 50А | 23 | 75 | 2С10В0,5; С20В0,5; П 1,0 | |||||
Из анализа данных таблицы 3.1 следует: . . . .
Наилучший результат обеспечивает стандартная установка для импульсно-дуговой механизированной сварки типа ВДГИ-302 на частоте следования импульсов 50Гц. Сварные соединения, сваренные этим методом, единственные среди исследованных в работе, не имеют внутренних дефектов, имеют самую высокую механическую прочность сварного соединения (84% от прочности основного металла) и один из самых высоких углов загиба.
Ко второй группе установок относятся выпрямители для полуавтоматической сварки (ВД-306(506)ДК, ВДУ-506), которые показали очень неплохие результаты. Механическая прочность составляет 81,2% от прочности основного металла для ВД-306ДК и 65% для ВДУ-506.
К третьей группе установок относится синергетический источник Синермиг-401 на котором производилась импульсно-дуговая механизированная сварка на базовой частоте 26кГц и подача дополнительных импульсов на частоте 100Гц. Полученные данные по этому источнику достаточно противоречивы. С одной стороны получена самая высокая пластичность сварного соединения (данные по углу загиба), с другой стороны – один из самых низких показателей механической прочности (56% от прочности основного металла).
К четвертой группе установок можно отнести метод сварки ТИГ на установках типа УДГУ-501. Самым интересным результатом является факт, что при сварке переменным симметричным током получены одни из самых низких показателей по механической прочности и углу загиба сварного соединения (50% от прочности основного металла). Хуже имеются данные только при коэффициенте асимметрии 0,43, т.е., когда синусоида напряжения на электроде горелки и изделии сдвинута в положительную область, т.е. на изделии присутствует больше положительного потенциала, чем отрицательного (28% от прочности основного металла). Картина качественно меняется, когда коэффициент асимметрии составляет 0,53, т.е. синусоида напряжения на электроде и изделии сдвинута в отрицательную область (81,2% от прочности основного металла) или когда применен пульсирующий режим сварки (72 % от прочности основного металла).
Объяснить полученные результаты можно следующим образом: при сварке алюминиевых конструкций и использовании алюминиевой проволоки для обеспечения формирования плотного малоокисленного сварного соединения перенос должен вестись каплями достаточно однородного размера, причем размер этих капель должен не быть минимальным, а перенос, соответственно, не должен быть струйным. В противном случае, при использовании инверторных источников питания, когда из-за работы источника питания на большой частоте происходит процесс дробления капель, происходит их интенсивное окисление, ввиду резкого увеличения удельной поверхности капель. Сварное соединение формируется из капель минимального размера, которые достаточно окислены, поэтому механические свойства соединения невелики, но внешний вид и пластичность соединения находятся на высоком уровне. Для формирования высококачественного сварного соединения просто не хватает степени газовой защиты, а сварка со специальными дополнительными газовыми поддувами или камерами с контролируемой атмосферой экономически не оправдана.
Косвенно полученный вывод подтверждает результат по использованию другого импульсно-дугового источника, но работающего на промышленной частоте – ВДГИ-302. В этом случае, уменьшение частоты следования импульсов со 100 до 50Гц, т. е. не стремление к струйному переносу, а стремление фиксировать размер капель электродного металла на уровне 0,8-1 мм, позволило получить самые высокие результаты.
В таблице 3.2 приведены экспериментальные характеристики сварочного процесса при механизированной сварке плавящимся электродом (dэ=1.2 мм) в среде аргона сплава АМг5. Таблица 3.2 Экспериментальные характеристики сварочного процесса при механизированной сварке плавящимся электродом (dэ=1.2 мм) в среде аргона сплава АМг5
Дата добавления: 2019-07-15; просмотров: 287; Мы поможем в написании вашей работы! |
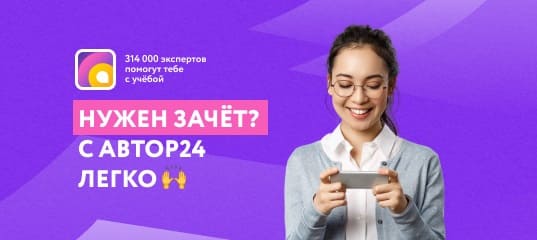
Мы поможем в написании ваших работ!