Выполнение работ в особо опасных условиях.
Преимущества ручной дуговой сварки:
· возможность сварки в любых пространственных положениях;
· возможность сварки в местах с ограниченным доступом;
· сравнительно быстрый переход от одного свариваемого материала к другому;
·
Изм. |
Лист |
№ докум. |
Подпись |
Дата |
Лист |
6 |
ПЭР 15.01.05 2117 |
· простота и транспортабельность сварочного оборудования.
Недостатки ручной дуговой сварки
· низкие КПД и производительность по сравнению с другими технологиями сварки;
· качество соединения во многом зависит от квалификации сварщика;
· вредные условия процесса сварки
Изм. |
Лист |
№ докум. |
Подпись |
Дата |
Лист |
7 |
ПЭР 15.01.05 2117 |
Тема моей письменной экзаменационной работы является разработка и технология сварки «Бака 1744СБ»
Эта конструкция в виде куба с одной стороны приварен патрубок.
Бак изготовлен из 8-ми деталей по 5-ти позициям:
Позиция 1:патрубок 24мм (1шт.)
Позиция 2: лист 208 х 208 толщиной 4мм(2шт)
Позиция 3: лист 180 х 180 толщиной 4мм (2шт).
Позиция4: лист 180 х 180 с отверстием, толщиной 4мм (1шт.)
Позиция5: лист 180 х 90 толщиной 4мм (2шт)
Бак сваривается ручной дуговой сваркой покрытыми электродами.
Бак изготовлен из стали марки Ст.3;
|
|
Габаритные размеры:
· Длина 208 мм
· Ширина 180 мм
· Высота 188 мм.
Изм. |
Лист |
№ докум. |
Подпись |
Дата |
Лист |
8 |
ПЭР 15.01.05 2117 |
Размеры сварных швов соответствуют ГОСТ 5264-80. Ручная электродуговая сварка. Всего необходимо выполнить три вида сварных соединений, которые на чертеже обозначаются: С2, У4, Т1.
Таблица № 1Сварные швы
№ п/п |
Условное обозначение сварного шва на чертеже |
Наименование шва |
Количество швов | Размеры конструктивных элементов, мм | ||
Подготовленных кромок свариваемых деталей | Сварного шва | |||||
1. | С2 | Стыковое соединение, без скоса кромок | 1 |
![]() |
| |
2. | У4 4 | Угловое соединение, одностороннее, без скоса кромок | 4 |
![]() |
| |
3. | Т1- 4 | Тавровое соединение, одностороннее, без скоса кромок | 8 |
|
![]() | |
Изм. |
Лист |
№ докум. |
Подпись |
Дата |
Лист |
9 |
ПЭР 15.01.05 2117 |
на производстве
Рабочее место электросварщика называют сварочным постом, оборудованным всем необходимым для выполнения сварочных работ.
|
|
Виды сварочных постов
В классификацию сварочных постов входит два вида: стационарный и передвижной (переносной). Последний можно перевозить на разные объекты. Особенность деятельности в стационарном посту – это заготовка приносится к сварщику. В передвижном варианте сварщик приезжает к заготовке.Стационарный сварочный постРазмеры сварочного поста определяются объемом выполняемых сварщиком работ. Но высота кабины обычно не меньше 2 м. Пол, потолок и стены изготавливаются из негорючих материалов. Это требования безопасности.Освещение рабочего места не должно быть меньше 80 Люкс. Идеально, если будет комбинация искусственного освещения с дневным. Подключение всех видов электрического оборудования к системе заземления здания цеха обязательно. Пост для ручной дуговой сварки стационарного типа должен оборудоваться хорошо работающей вентиляцией. Основное к ней требование – это воздухообмен в пространстве поста 40 м³/ч.Поверхность рабочего верстака – это чугунная плита толщиною 20-25 мм. При этом ее поверхность должна находиться на высоте 50-70 см над уровнем пола. Внутри каждой рабочей кабины должен устанавливаться рубильник и магнитный пускать, обеспечивающие включение и отключение сварочного трансформатора.Внимание! Сварочное оборудование может устанавливаться как внутри помещения, так и снаружи. При этом максимальное расстояние от него до сварного аппарата не должно превышать 15 м.
|
|
Передвижной сварочный пост
По сути, это рабочее место электро- или газосварщика на открытом воздухе. Поэтому к данному месту не такие жесткие требования безопасности. Здесь нет системы вентиляции, из поверхностей лишь потолок, который является крышей навеса, закрывающего пространство от природных осадков.В основном используется дневное освещение, но каждый верстак снабжен локальной осветительной системой, которая работает независимо от других объектов. Но, как и на стационарном посту, на переносном также организуется система заземления. Некоторые переносные сварочные кабины закрываются со всех сторон защитными панелями. Но есть к его обустройству одно требование – между панелями должен всегда оставляться зазор в пределах 50 см. Это и будет своеобразная система вентиляции сварочного поста.Что касается оборудования сварочного поста для ручной дуговой сварки или газосварки (имеется в виду передвижного типа), то кроме верстака и стула устанавливаются тумбы, в которых
|
|
хранится инструмент и расходный материал для проведения работ.Существуют передвижные сварочные посты, которые организуются на автомобильных шасси. Это по-
Изм. |
Лист |
№ докум. |
Подпись |
Дата |
Лист |
10 |
ПЭР 15.01.05 2117 |
Схема рабочего места
Таблица2. Оборудование сварочного поста
| Наименование элемента оборудования | Назначение элемента оборудования | ||||||||
1. | Источник питания ВДМ-1001 | Для понижения напряжения сети необходимого для зажигания дуги с 220/380В до 60-70В., | ||||||||
2. | Балластный реостат РБ-301 | Для создания падающей вольт-амперной характеристики | ||||||||
3. | Стол | Необходим для сборки детали | ||||||||
4. | Вытяжка | Для отвода токсичных газов сварщика | ||||||||
5. | Электрододержатель | Для зажима электрода и подвода к нему тока | ||||||||
6. | Инструмент | Для вспомогательных работ до и после сварки | ||||||||
7. | Средства защиты: сварочный щиток, брезентовые рукавицы, защитный костюм, защитный щиток, кожаные ботинки, головной убор | Для защиты сварщика во время и после проведения сварочных работ |
4.
Изм. |
Лист |
№ докум. |
Подпись |
Дата |
Лист |
12 |
ПЭР 15.01.05 2117 |
Сталь— сплав железа с углеродом (и другими элементами), содержащий не менее 45 % железа и в котором содержание углерода находится в диапазоне от 0,02 до 2,14 %, причём содержанию от 0,6 % до 2,14 % соответствует высокоуглеродистая сталь. Если содержание углерода в сплаве превышает 2,14 %, то такой сплав называется чугуном. Углерод придаёт сплавам прочность и твёрдость, снижая пластичность и вязкость.
Углеродистые стали имеются:
Низкоуглеродистые до 0,25% углерода, 0% легирующий элемент
Среднеуглеродистые 0,25-06% углерода, 0% легирующий элемент
Высокоуглеродистые 0,5-2,0% углерода, 0% легирующий элемент
Углеродистаясталь обыкновенного качества содержит 0,14-0,22% углерода.
Имеются три группы сталей: Гр.А, Гр.Б, Гр.В
Группа А –сталь поставляется по механическим свойствам
Группа Б – сталь поставляется по химическому составу
Группа В – сталь поставляется по механическим свойствам и химическому составу
В процессе образования сварного соединения участвуют с одной стороны
основной металл, а с другой металл электрода.
Основной металл, из которого изготовлен бак имеет марку стали Ст.3
Это конструкционная углеродистая сталь обыкновенного качества.
Низкоуглеродистая конструкционная сталь, обыкновенного качества.
Расшифровывается следующим образом:
· Ст - сталь
· 3- порядковый номер
Химический состав стал:
Содержание углерода 0,14%-0,22%
Содержание марганца 0,4%-0,65%
Содержание кремния 0,12%-0,3%
Прочие элементы до 1%
Механические свойства стали:
Предел прочности 380-490 Мпа
Предел текучести 340 МПа
Относительное удлинение 27%
Ст.3 относится к 1 классу свариваемости. Свариваемость стали хорошая(1класс). Свариваемость – способность металла образовывать сварное соединение без дефектов. Существует 4 класса свариваемости:
1 класс свариваемости – Х - хорошо свариваемая сталь, то есть сваривается без дефектов при любой температуре воздуха, любой толщины металла.
2 класс свариваемости –У- удовлетворительно свариваемая сталь, то есть существует 2 условия при сварке: температура воздуха >-5, -S 20мм
3 класс свариваемости – О - ограниченная то есть требуется подогрев кромок соединения перед сваркой
4 класс свариваемости – П- плохо, то есть требуется подогрев до и после сварки.
Сварка низкоуглеродистых сталей
Низкоуглеродистые стали (до 0,25% С) обладают хорошей свариваемостью. При их сварке учитывают, что металл шва отличается от основного металла несколько пониженным содержанием углерода. Это незначительно понижает прочность сварного соединения. Увеличение прочности сварного соединения при дуговой сварке осуществляют легированием металла шва марганцем или кремнием, через проволоку или покрытие, а также за счет увеличения скорости охлаждения. При увеличении скорости охлаждения прочностные свойства сварного шва возрастают, а пластические (угол загиба, ударная вязкость, относительное удлинение и сужение) снижаются.
Изм. |
Лист |
№ докум. |
Подпись |
Дата |
Лист |
13 |
ПЭР 15.01.05 2117 |
Cварочными материалами называют материалы, которые участвуют в
процессе создания сварочного шва. К сварочным материалам относятся:
электроды, проволока, защитный газ, горючий газ, кислород, флюс.
Для сварки низкоуглеродистой стали марки Ст.3 используют электрод марки
УОНИИ 13/45;
Технологическое свойство электрода УОНИИ 13/45:
Тип электрода- -Э42А
Коэффициент наплавки -85 ГА, час
Род тока- постоянная обратная полярность
Расход электродов на l кг наплавленного металла (кг) -16
Пространственное положение при сварке- любое
Условия сварки:
· сварка производится предельно коротким дуговым методомопирания
· свариваемые кромки необходимо очищать от ржавчины и следовмасла
· электроды хранить в герметичной таре в сухом отапливаемом помещении
· при отсырении сушить при 350⁰-370⁰ Cв течении 1 часа
Область применения:
· для сварки особо ответственных конструкций работающих при отрицательных температурах
· для сварки металла большой толщины, заварки дефектов литья.
ПОКРЫТИЯ электродов
Назначение электродного покрытия:
1. Защита сварного шва от воздуха и газов
2. Для стабильного горения дуги
3. Для получения качественного шва (легированием)
4. Для удаления вредных примесей
Состав электродного покрытия:
1. Защита – газообразующие (древесная мука, крахмал, пищевая мука, целлюлоза) Шлакообразующие: мрамор, мел, песок, полевой шпак
2. Стабилизирующее: кальций и натрий
3. Легирующий компонент : легирующие элементы кроме серы, фосфора и кремния
4. Раскисляющие компоненты: марганец, кремний
5. Связующие: жидкое стекло
Виды покрытия:
Кислое-А – образует шлак, в состав которых входят силикаты и титаны марганца и железа, а также компоненты окисляющие металл Э-42 СМ-5 КПЗ-32 УНЛ-1
Рутиловое-Р – образует шлаки, в состав которых входят силикаты и титаны марганца и железа, а также другие компоненты, практически не содержащие оксидов железа Э42 АНО-1 АНО-5 АНО-6
Основное-Б – шлаки, в состав которых входят силикаты кальция и магния, а также фторид кальция
Целлюлозное -Ц – содержит органические составляющие, образующиеся защитные газы, в основном элементе целлюлозы марки Эц.
Для изготовления бака, я применяю электрод тип Э42А, марка УОНИИ 13/45.
Изм. |
Лист |
№ докум. |
Подпись |
Дата |
Лист |
14 |
ПЭР 15.01.05 2117 |
Сварные швы по своей длине делятся на короткие (до 300 мм), средние (от 300 до 1000 мм), длинные (более 1000 мм). Для каждого видов швов применяются различная техника: короткие швы свариваются на проход, средние от середины к концам, длинные обратно-ступенчатым способом.
Таблица 3.Техника сварки швов
Условное обозначение сварного соединения | Сечение по ГОСТу и толщина кромок | Длина шва, мм | Техника сварки по длине | Техника сварки по сечению (число слоев) |
С2 |
![]() | 180 | Напроход | Однослойный, односторонний |
У4 4 | ![]() | 180 | Напроход | Однослойный, односторонний |
Т1- 4(1) |
![]() | 75,36 | Напроход | Однослойный, односторонний |
Т1- 4(2) | ![]() | 720 | Напроход | Однослойный, односторонний |
7.
Изм. |
Лист |
№ докум. |
Подпись |
Дата |
Лист |
15 |
ПЭР 15.01.05 2117 |
До начала выполнения работ сварщик выбирает режим сварки. Под режимом сварки понимают совместимость параметров определения сварочного процесса. Параметра могут быть основные и дополнительные. К основным параметрам относится диаметр электрода, сила свариваемого тока, скорость сварки, напряжение на дуге, а к дополнительным – род тока, длина дуги и другие.
Диаметр электрода зависит от толщины металла, катета шва и положение шва в пространстве. Для вертикальных и потолочных швов dэ≤4мм.
Sметалла(мм) | 1,5 | 2 | 3 | 4-5 | 6-8 | 9-12 | 13-15 | 16-20 |
dэ (мм) | 1,6 | 2 | 2-3 | 3,4 | 4 | 4,5 | 5 | 5,6 |
Для сварки бака я выбираю диаметр электрода, пользуясь таблицей, 3мм.
При сварке таврового соединения Т3 катетом 6 мм диаметр электрод 4 мм. При сварке нахлёсточного соединения катетом 6 мм диаметром электрода 4 мм.
Сила сварочного тока в нижнем положении выбирается по формуле:
I = K*d,
где:
K = 30÷40 – коэффициент пропорциональности для электрода 4 мм равно:
I=(30÷40)*4=120÷160 A.
dэ (мм) | 1-2 | 3-4 | 5-6 |
K (АММ) | 25-30 | 30-45 | 45-60 |
Пользуясь таблицей, я выбираю ток сварочный 90-135А.
Угол наклона электрода зависит от типа соединения. При сварке таврового и углового соединения угол наклона электрода равен 45градусов.
8.
Изм. |
Лист |
№ докум. |
Подпись |
Дата |
Лист |
16 |
ПЭР 15.01.05 2117 |
Вполне очевидно, что качество сварных швов влияет на функциональность всей сваренной конструкции. Дефекты приводят к ослаблению прочности изделий и их разрушению в процессе эксплуатации. Из-за проницаемости швов нарушается герметичность сосудов и систем, работающих под давлением.
После завершения сварочных работ, изделия должны подвергаться контролю сварных соединений с целью обнаружения и исправления дефектов. Невооруженным глазом можно рассмотреть лишь часть из них - крупные наружные трещины и поры, непровары, подрезы и т.п. Большая часть дефектов скрыта в глубине металла или имеет такие малые размеры, что обнаружить их можно только с использованием специальных приборов и материалов.
Существует много способов контроля сварных швов, различающихся по принципу действия, способности к обнаружению тех или иных видов дефектов, техническому оснащению. Методы контроля сварных соединений подразделяются на разрушающие и неразрушающие. Последние, в силу понятных причин, являются наиболее широко используемыми. Применяются следующие основные методы неразрушающего контроля сварных соединений:
- внешний осмотр;
- радиационная дефектоскопия;
- магнитный контроль;
- ультразвуковая дефектоскопия;
- капиллярная дефектоскопия;
- контроль сварных швов на проницаемость;
- прочие методы (проверка с использованием вихревых токов и т.п.).
Внешний осмотр (ГОСТ 3242-79) служит для определения наружных дефектов в сварных швах и производится не вооруженным глазом или с помощью лупы, увеличивающей в 5-10 раз. Перед осмотром шов и прилегающие к нему поверхность металла 20х20 мм очищают от шлаков, брызг и загрязнений, а стыки аустенитных паропроводов проходят специальную механическую обработку. Размеры сварного шва и дефектных участков определяются измерительным инструментом и специальными шаблонами (рис, 21.1.)
Испытание гидравлическим давлением производится следующим образом. Герметичную емкость изделия заполняют водой под давлением, значение которого определяется Техническими условиями и Правилами Госгортехнадзора. При проведении испытаний
Изм. |
Лист |
№ докум. |
Подпись |
Дата |
Лист |
17 |
ПЭР 15.01.05 2117 |
Контролькеросином основан на физическом явлении капиллярности, которое заключается в способности керосина подниматься по капиллярным ходам - сквозным порам и трещинам. В процессе испытания сварные швы покрываются водным раствором мела с той стороны, которая более доступна для осмотра и выявления дефектов. После высушивания окрашенной поверхности с обратной стороны шов обильно смачивают керосином. Не плотности швов выявляют по наличию на меловом покрытии следов проникшего керосина. Появление отдельных пятен указывает на поры и свищи, полос - сквозных трещин и не проваров в шве. Благодаря высокой проникающей способности керосина обнаруживаются дефекты с поперечным размером 0,1 мм и менее.
Пневматическое испытание – проводят с целью контроля плотности сварных соединений. Для этого в замкнутый сосуд нагнетают воздух до рабочего давления. Снаружи все швы смачиваются мыльным раствором. Сжатый воздух в местах не плотностей образует мыльные пузыри. В зависимости от наличия и величины мыльных пузырей можно судить о характере и величине дефекта.
Химический контроль - Для покрытия сварных швов используется раствор мела в воде, которым обрабатывается доступная сторона шва, что позволяет провести тщательный осмотр и выявить все дефекты. После высушивания окрашенной поверхности шов следует обильно смочить керосином. Если швы неплотные, то это выявляется при наличии покрытия мелом и следов керосина на нем.
Контроль за счет аммиака проводится при наличии индикаторов, способных менять свою окраску при наличии щелочной среды, оказывающей воздействие на него. Реагентом в данном процессе выступает газ аммиак, который используют для контроля.
Проводя испытания, с одной стороны шва укладывают ленту из бумаги, которая смочена в 5%-тном растворе специального индикатора. На противоположной стороне шва проводится обработка соединения за счет смеси газообразного аммиака и воздуха. При проникновении аммиака через неплотные сварные швы происходит его окрашивание в местах наличия дефектов.
Капилярное исследование - Применение капиллярного метода основано на определенном свойстве жидкостей, связанном с возможностью проникновения через капилляры, представляющие собой микроскопические трещины, в структуру металлов. Капиллярный метод связан с активностью жидкости в капиллярах. Жидкость способна втягиваться, проникая в капилляры. Применение определенных из них (керосина) позволяет обнаружить наличие сквозных дефектов сварных швов.
Использование капиллярного контроля связано с осуществлением проверки любых сварных изделий без учета их форм, размеров и материалов, из которого они сделаны. Данный метод является более подходящим при обнаружении различных недостатков на поверхности швов. Недостатки являются невидимыми, поэтому их нельзя обнаружить простым невооруженным глазом, а также с лупой.
Испытать сварные швы на плотность на основе капиллярного способа позволяют специальные вещества, которые носят название пенетранты. Проникая в структуру
Изм. |
Лист |
№ докум. |
Подпись |
Дата |
Лист |
18 |
ПЭР 15.01.05 2117 |
При высоком уровне смачиваемости жидкости и наименьшем радиусе капилляра происходит увеличение глубины и скорости проникновения жидкости. В результате применения капиллярного метода можно обнаружить не только невидимые или слабовидимые дефекты с открытой полостью. Вместе с тем данный способ позволяет выявлять и сквозные виды дефектов, если в процессе их обнаружения использовать керосин.
Магнитный метод - Обнаружение дефектов в процессе осуществления магнитного контроля основано на такой способности магнитного поля, как его рассеивание. С этой целью необходимо подключение электромагнитного сердечника с последующим помещением его в соленоид. Намагниченное соединение должно иметь поверхность, предварительно покрытую железными опилками, окалиной и др. Должны быть использованы такие элементы, которые реагируют на появление магнитных полей.
Если сварной шов имеет дефекты, то происходит образование скоплений порошка, который при взаимодействии с магнитным полем начинает перемещаться с образованием магнитного направленного спектра. Для более легкого перемещения порошка под влиянием магнитных полей сварные изделия простукивают, что придает наибольшую подвижность мелким крупинкам и зернам.
Фиксацию магнитного поля рассеивания осуществляют с использованием специального прибора, то есть магнитографического дефектоскопа. Определить качество соединения можно с помощью метода сравнения с эталоном. Данный метод является простым и надежным, а также дешевым. Магнитный метод контроля сварочных швов незаменим в процессе прокладки трубопроводов, которые играют ответственную роль. Его часто используют во время строительства.
Радиационный способ контроля и ультразвуковой метод - Радиационный способ контроля связан с определением недочетов в любой полости сварных швов, которые являются невидимыми. Просвечивают швы с применением рентгеновских лучей или с помощью гамма-излучения, которое способно проникать через металлическую структуру изделия.
Излучение создается за счет специальных источников, рентгеновской либо гамма-установки. Шов и источник излучения должны находиться друг перед другом. Расположение рентгеновской пленки связано с ее установкой в специальную кассету, которая является светонепроницаемой. При облучении пленки рентгеновским излучением, проходящим через структуру металла, остаются пятна, которые являются более темными. Это связано с наименьшим поглощением лучей дефектными местами.
Использование метода рентгеновского излучения является безопасным для здоровья человека, но источник излучения, то есть рентгеновский аппарат, является слишком громоздким. Используют его исключительно в условиях стационара. Интенсивность работы источника гамма-излучения бывает значительной, что позволяет контролировать сварные швы, которым свойственна наибольшая толщина. Портативная аппаратура и доступность дешевого метода делает данный тип контроля наиболее распространенным в строительстве.Гамма-излучение более опасно, чем рентгеновское, что обусловлено прохождением специального обучения. Применение радиографического метода контроля имеет недостаток, связанный с отсутствием возможности выявлять наличие трещин, которые располагаются не в соответствии с направлением потока лучей.
Использование ультразвукового метода связано с применением акустического способа контроля. Это позволяет выявлять различные недочеты, то есть газовые поры и трещины, включая такие дефекты, ради определения которых не применяется способ радиационной дефектоскопии.
Ультразвуковым методом проводят испытания, связанные с отражением звуковой волны от границы разделения сред. Использование пьезоэлектрического способа при создании звуковой волны получило широкое распространение в качестве способа контроля сварного шва. В основе данного метода лежит принцип создания механического колебания в результате наложения переменного электрического поля.
Изм. |
Лист |
№ докум. |
Подпись |
Дата |
Лист |
19 |
ПЭР 15.01.05 2117 |
9.
Изм. |
Лист |
№ докум. |
Подпись |
Дата |
Лист |
ПЭР 15.01.05 2117 |
Рабочее место сварщика (сварочный) должноотвечать следующимтребованиям:
При работе на стационарных постах: оборудуется специальная кабина, укоторой:
· Стены и пол должны быть Выполнены из огнестойких материалов илипокрыты огнестойкими составами.
· Стены окрашивают в светло серый цвет красками, хорошо поглощающими ультрафиолетовое излучение.
· Освещенность кабины! должна быть не менее 80… 100 лк.
· Кабина оборудуется средствами пожаротушения и местнойвентиляцией с воздухообменом 40 мз час на одного сварщика. Приэтом направление отсасываемых газов, выделяющихся при сварке, недолжно проходить мимо сварщика.
Вход в кабину должен быть занавешен плотной огнестойкой тканью.
Сварщик (и его помощник) должны быть одетыми в плотную робу, закрывающую всё тело, выполненную из огнестойких материалов, а так же должны работать в брезентовых рукавицах.
Для защиты лица и глаз от воздействия ультрафиолетового излучения дуги сварщика(и его помощник) должны закрывать лицо сварочной маской со светофильтром. Прозрачность светофильтра регламентирована.
Для защиты от поражения электрическим током, сварщик(и его помощник) должны быть обутыми в ботинки(сапоги) на резиновой подошве или работать стоя на диэлектрическом коврике.
В связи с тем, что электросварочные работы являются работами повышенной опасности, при их выполнении должны соблюдаться соответствующие требования безопасности при электросварочных работах, регламентируемые соответствующими документами. Выполнение данных нормативов является единственной возможностью вести подобные работы без риска для здоровья и жизни. Начинать электросварочные работы можно только при выполнении следующих предварительных условий:
· Электросварщик должен быть экипирован в спецодежду, а также обувь, обеспечивающую гарантированную защиту от попадания на тело расплавленных частиц металла. В комплект одежды входят брезентовые брюки и куртка, имеющие карманы закрытые специальными клапанами (одеваться должны только навыпуск), шнуровка обуви должна быть плотной. На руках должны быть сварочные перчатки.
· Должна быть проверена электрическая изоляция токоведущих элементов (электрокабель) и держателя электродов.
·
Изм. |
Лист |
№ докум. |
Подпись |
Дата |
Лист |
20 |
ПЭР 15.01.05 2117 |
· Все соединения кабеля и сварочного агрегата должны быть надежными.
· У места ведения работ не должны находиться любые воспламеняющиеся материалы, расстояние от рабочей площадки до места их возможного размещения должно составлять не менее 10 метров.
Общие меры безопасности при электросварочных работах.
· Вести работы на открытой территории при атмосферных осадках (снег, дождь) запрещено, по их завершении сварка разрешена только с применением диэлектрических перчаток, обуви и ковриков, которые должны проходить обязательную поверку в установленные сроки.
· При замене электрода запрещается дотрагиваться свободной рукой до свариваемой заготовки
· Для защиты органов зрения и лица обязательно применение защитных масок или щитков, они должны обеспечить защиту всего лица. Также необходимо предусмотреть защиту от воздействия сварочной дуги посторонних лиц. С этой целью устанавливаются специальные экраны или щиты, не допускающие ослепления подручных сварщика.
Изм.
Лист
№ докум.
Подпись
Дата
Лист
21
Ведение электросварочных работ на высоте. ПЭР 15.01.05 2117
· Работы в таких условиях с переносных лестниц категорически запрещены. Они могут выполняться только со специально оборудованных площадок, имеющих ограждение. Ширина площадки не должна быть меньше 1 метра.
· При работе на высотных лесах обязательно применение поверенного предохранительного пояса.
· Деревянные подмости и леса должны быть защищены асбестовыми или металлическими листами.
· Если высотные сварочные работы ведутся несколькими исполнителями на различной высоте, но по одной вертикальной линии, для защиты ниже расположенных сварщиков от искр и брызг металла необходимо устанавливать специальные тенты, козырьки из негорючих материалов.
Выполнение работ в особо опасных условиях.
К такому виду работ причисляют сварку в резервуарах, емкостях. В этих случаях требования безопасности при электросварочных работах ужесточаются.
· Для выполнения такого вида работ, применяются сварочные аппараты с электроблокировкой, способные отключать сварочную цепь в режиме холостого хода (при замене электродов).
· Запрещено вести сварку на баллонах, находящихся под давлением, также не допускается работа в емкостях, в которых не была проведена очистка от горючих, взрывоопасных, токсичных веществ. После очистных работ в обязательном порядке должна быть проведена проверка на их наличие.
· Запрещены работы по сварке конструкций подвергшихся покраске до полного высыхания поверхности.
· Внутри емкостей не допускается одновременное ведение электро и газосварочных работ.
Дата добавления: 2019-07-15; просмотров: 205; Мы поможем в написании вашей работы! |
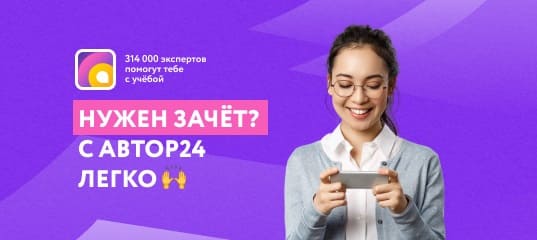
Мы поможем в написании ваших работ!