Лакокрасочные защитные покрытия
К лакокрасочным материалам относятся лаки, краски, грунтовки, шпатлевки.
Лаки — растворы пленкообразующих веществ в органических растворителях. Краски — суспензии пигментов в пленкообразующих веществах. Основой масляных красок служат олифы, эмалевых — лаки. Для получения прочного сцепления покрытия с поверхностью изделия используют грунтовки, а для устранения рисок, углублений, изъянов и т. д.— шпатлевки, состоящие из пленкообразующего, наполнителей, пигментов.
В зависимости от основных свойств и назначения покрытия подразделяются на водо-, жаро-, атмосфере- и химически стойкие, светотехнические, бактерицидные, токопроводящие, декоративные, светящиеся и др.
Атмосферостойкие покрытия применяют для окраски самолетов, автомобилей, железнодорожных вагонов, мотоциклов, оборудования, приборов и др. Они устойчивы к воздействию кислорода, воды, солнечной радиации и температуры окружающей среды.
Химически стойкие покрытия используют для защиты аппаратуры, оборудования, приборов и т. д. от воздействия кислот, щелочей, растворителей, агрессивных газов. Такие покрытия готовят на основе эпоксидных, полиуретановых, полихлорвиниловых, фенолоформальдегидных, фторорганических и других полимеров.
На основе эпоксидных соединений готовят покрытия, устойчивые к воздействию растворов NаОН (до 25 %) при нагревании (125°С), к хлороводородной (25%), серной (70%), ортофосфорной, азотной кислотам, к хлору, хлороформу, бензину и т. д. Они эластичны, влаго- и атмосферостойки, обладают высокими электроизоляционными и механическими свойствами.
|
|
Для защиты гальванических ванн, аппаратов химической водоочистки, окраски морских и речных судов применяют покрытия на основе полихлорвинила, сополимеров винилхлорида. Они устойчивы к азотной, хлороводородной, серной, уксусной и другим кислотам, щелочам, маслам и газам, содержащим SО2, SО3, N2О3, NН3, НС1. Хранилища нефти и нефтепродуктов, изделия из магниевых и алюминиевых сплавов, работающие в условиях тропического климата, и другие покрываются лаками, эмалями, грунтовками, шпатлевками, получаемыми на основе полиуретановых соединений. Широкое применение находят покрытия на основе фторопластов, фенолоформальдегидных соединений.
Термостойкие покрытия используют для защиты отдельных деталей машин и аппаратов от воздействия повышенных температур (выше 180 °С). Покрытия, получаемые на основе кремнийорганических соединений, устойчивы к температуре до 300 °С при длительном и до 500—800 °С — при кратковременном воздействии. Такую эмаль используют для окрашивания автомобильных радиаторов, калориферов, вентиляционных и сушильных установок, арматуры химических заводов.
|
|
Краски, препятствующие обрастанию судов раковинами, готовят на основе перхлорвиниловой смолы или с использованием сополимеров винилхлорида с винилацетатом путем введения в их состав соединений меди, ртути и мышьяка.
Покрытия полимерами
Металлоконструкции и различные аппараты и изделия предохраняют от коррозии, покрывая их термопластичными полимерами (полиэтилен, полипропилен, полиизобутилен, эпоксидные соединения, фторопласты, полиамиды, поливинилбутираль и др.). Полимеры на защищаемую поверхность наносят в виде листовых материалов, суспензии, мелкодисперсных порошков или растворов различными способами — газовым и вихревым напылением, приклеиванием и т. д.
При газовом напылении порошок полиэтилена наносят на грунт из поливинилбутиральных лаков на нагретую до 160 °С поверхность, а при вихревом способе — на поверхность, нагретую до 250 — 350 °С. Полиэтилен расплавляется на ней, образуя сплошное полимерное покрытие. Пленки полиамидов, нанесенные газовым или вихревым напылением, имеют высокую адгезию к металлу, прочность, устойчивы ко многим агрессивным средам.
|
|
Покрытия из фторопласта-3 устойчивы к кислотам, растворам солей, поэтому их применяют для защиты аппаратуры при производстве хлорпроизвод-ных и аппаратуры для хранения особо чистых материалов.
Пленки из фторопласта-4 устойчивы к морской воде, к растворам щелочей, минеральным кислотам, кроме олеума и концентрированной азотной кислоты. Они имеют хорошие электроизоляционные и механические свойства. Высокую химическую стойкость к кислотам и щелочам имеют хлоркаучуковые покрытия.
Полимеры широко используются для футеровки емкостей и реакторов по способу свободного вкладыша, т. е. приклеиванием или приваркой листов полимерных материалов к внутренней поверхности защищаемых изделий.
Гуммирование
Защита от коррозии химических аппаратов, трубопроводов, емкостей для перевозки и хранения химических продуктов резиной или эбонитом называется гуммированием. Аппараты, подвергающиеся сотрясениям, ударам, резким колебаниям температур, гуммируются мягкими резинами.
Нанесение покрытий производится путем облицовки поверхности изделий сырой резиновой смесью, которую прикатывают валиками, а затем вулканизируют. Для гуммирования чаще всего применяют резины и эбониты, получаемые на основе натурального, бутадиен-стирольного, бутадиен-нитрильного, бутил-каучука, хлоропреновых и фторсодержащих каучуков. Такие покрытия устойчивы к хлороводородной, фтороводородной, уксусной, лимонной кислотам любой концентрации до температуры 65°С, к щелочам, нейтральным растворам солей, к 50%-ной серной и 75 %-ной фосфорной кислотам, но они разрушаются сильными окислителями (азотной, концентрированной серной кислотами).
|
|
Покрытия смазками и пастами
Защитные смазки и пасты имеют ряд преимуществ перед другими покрытиями. Они легко наносятся на поверхность изделий, легко удаляются с нее и являются недорогими. Применяют эти покрытия для предохранения металлических изделий при хранении в закрытых помещениях и на открытых площадках, а некоторые смазки предохраняют изделия и во влажной атмосфере при наличии в ней СO2, SO2 и других газов.
Механизм защитного действия смазок состоит в создании на поверхности изделия тонкого защитного слоя, препятствующего проникновению агрессивной среды к поверхности металла.
Жидкие смазки получают на основе минеральных масел (авиационного, трансформаторного, машинного и других) с введением в их состав других добавок (парафина, мыла, жирных кислот, нитрита натрия и др.). Например, смазка К-17 содержит девять компонентов, каждый из которых выполняет определенные функции.
Защитные пасты получают из суспензий минерального воска (церезина), парафина, каучука, полиизобутилена в уайт-спирите. Нх наносят на изделие тампоном, распылением. Для предохранения поверхности изделия от плесени в состав паст вводят фунгициды.
ЭЛЕКТРОХИМИЧЕСКАЯ ЗАЩИТА
Электрохимическая защита состоит в катодной или анодной поляризации защищаемой конструкции. Она осуществляется присоединением к конструкции извне источника постоянного тока или постороннего электрода — протектора. Электрохимическую защиту подразделяют на катодную и анодную.
Катодная защита применяется для предохранения металлических изделий, находящихся в почве, морской воде, а также для защиты аппаратуры химических и других заводов (холодильники, конденсаторы, теплообменники и др.), хранилищ нефти и др. Она осуществляется присоединением металлоконструкции к отрицательному полюсу внешнего источника постоянного тока или к металлу с более отрицательным потенциалом (анодный протектор). Такое присоединение превращает металлоконструкцию в катод и тем самым предохраняет металл от разрушения. При катодной защите с помощью источника постоянного внешнего тока (рис. 22) в качестве вспомогательного электрода (анода) используют нерастворимые материалы (графит, уголь) или растворяющийся металлический лом (рельсы, старые трубы и т. д.), который периодически нужно возобновлять.
Рис. 22. Схема катодной защиты внешним током:
1 — труба с покрытием; 2 — соединительные провода; 3 — источник постоянного тока; 4 — анод
Рис. 23. Схема катодной протекторной защиты:
1 — стальная конструкция; 2 — протектор; 3 — наполнитель; 4 — электрический контакт с конструкцией; 5 — контрольно-измерительный вывод (iп.з —ток протекторной защиты)
При использовании анодного протектора создается гальванический элемент, в котором металлоконструкция является катодом, а протектор — растворимым анодом (рис. 23). В качестве протектора используют магний, цинк и их сплавы. Протектор работает эффективно, если переходное сопротивление между ним и коррозионной средой невелико. При защите изделия, лежащего в почве, протектор помещают в наполнитель — смесь неорганических солей с глиной, понижающих переходное сопротивление. Площадь протектора должна составлять 0,2 — 0,5 % от площади защищаемой конструкции.
Эффективность катодной защиты оценивают по защитному эффекту Z (в %) и коэффициенту защитного действия К.. Защитный эффект Z определяют по формуле
где K .1 — скорость коррозии металла без электрозащиты и К2с электрозащитой соответственно, г/(м2·ч).
Коэффициент защитного действия K равен
где ∆m1 и ∆m2 — убыль массы металла без электрозащиты и с ней соответственно, г/м2; iк — плотность катодного тока, А/м2.
Эффективность катодной защиты возрастает, если ее применять совместно с защитными покрытиями, например с нанесением битумного покрытия на трубопроводы.
При использовании катодной защиты, особенно с помощью внешнего источника постоянного тока, можно обеспечить полную защиту металлоконструкции от коррозии, т. е. достичь Z = 100 %. Для этого нужно, чтобы потенциал защищаемого металла был равен равновесному.
Анодная защита применяется для защиты аппаратуры, изготовленной из нержавеющих и углеродистых сталей, титана, циркония и т. д., при работе в сильно агрессивных средах. Ее используют также часто с целью снижения загрязнений агрессивной среды продуктами коррозии.
Анодная защита применяется только в тех случаях, когда металл или сплав способны перейти в пассивное состояние. Анодная защита осуществляется присоединением защищаемого изделия к положительному полюсу внешнего источника постоянного тока или к металлу с более положительным потенциалом (катодный протектор). При этом потенциал защищаемого металла должен сместиться в область устойчивого пассивного состояния (см. рис. 6).
Катоды, используемые при анодной защите от внешнего источника тока, должны иметь высокую устойчивость в коррозионной среде. Выбор материала катода определяется характером среды. Помимо платины, применяют хромоникелевые стали (для кислот), кремнистый чугун (для растворов неорганических солей, серной кислоты), никель (для щелочных сред).
В качестве катодного протектора можно использовать такие материалы, как углеграфит, диоксид марганца, магнетит, диоксид свинца, имеющие весьма положительный потенциал. Скорость коррозии при анодной защите может быть снижена до минимальной величины, соответствующей току полной пассивации (см. рис. 6), но никогда не уменьшается до нуля, как в случае катодной защиты.
Дата добавления: 2019-07-15; просмотров: 205; Мы поможем в написании вашей работы! |
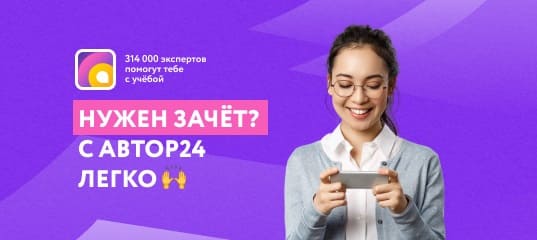
Мы поможем в написании ваших работ!