Выполнение индивидуального задания.
Трубопрокатный агрегат ТПА 30-102. Девятиклетевой непрерывный стан.
Введение
Агрегаты с непрерывным станомв силу их высокой производительности ( до 1 млн. тонн/год )применяются для производства труб массового сортамента. На этих агрегатах производят трубы диаметром от 16 мм до 170 мм с толщиной стенки 2...25 мм преимущественно из углеродистых и низколегированных марок стали. Способ непрерывной прокатки труб на длинной подвижной оправке (способ Фассля - Форена) известен с 1920 г. В начале он применялся для производства готовых и передельных труб диаметром 60...80 мм сравнительно небольшой длины. С 1960 г. начато производство труб диаметром 46...83 мм и толщиной стенки 3...4,5 мм, а на установках оборудованных редукционно-растяжными станами - диаметром 21...133 мм и стенкой 2,5...8 мм.
В результате этого появилась возможность прокатывать широкий сортамент труб из заготовки и черновой трубы постоянного диаметра. Последнее позволило увеличить производительность ТПА (при определенном сортаменте до 1 млн. т/год. К преимуществам данного способа прокатки следует также отнести благоприятные условия деформации трубы в непрерывном стане, минимальные технологические отходы (удельный расход металла 1050 кг/т) и расположение оборудования, удобное для автоматизации технологических операций. В 60-е годы был пущен первый отечественный ТПА 30-102 на Первоуральском новотрубном заводе, который предназначен для производства горячекатаных бесшовных труб диаметром 30...102 мм и толщиной стенки 3...8 мм из низкоуглеродистой стали.
|
|
В процессе эксплуатации ТПА 30-102 ПНТЗ выявились возможности интенсификации производства путем прошивки заготовки на углах подачи 14...17 град., модернизации входной стороны непрерывного стана для снижения времени такта прокатки до 8,5 с, повышение мощности индукционных подогревательных печей перед редукционным и калибровочным станами, замена 19-клетевого редукционного стана на 24-клетевой. В результате реконструкции цеха в 1974 г производительность ТПА 30-102 увеличилась в 1,5 раза и достигла 700 тыс.т/год..
С учетом опыта работы этого агрегата в 1970 г. был пущен второй ТПА 30-102 на Никопольском южнотрубном заводе, который отличается целым рядом технологических и конструктивных особенностей: усовершенствована технология прокатки и создана новая конструкция линии непрерывного стана с роликовой задачей гильзы и оправки в стан, применены более надежные рабочие клети, привод стана выполнен наклонным, усовершенствован дифференциально-групповой привод редукционного и калибровочного станов и т.д. Все это позволило довести время рабочего такта непрерывного стана до 7,5 с. Интенсивное развитие производства труб на ТПА с непрерывным станом в конце 70-х годов стало возможным благодаря улучшению качества непрерывнолитых заготовок, автоматизации технологических процессов и создания нового оборудования непрерывных станов.
|
|
Схема технологического процесса производства труб на агрегате ТПА 30-102.
Рисунок 1 - Схема технологического процесса производства труб натрубопрокатномагрегате ТПА 30-102.
Последовательность технологических операций производства труб на агрегате ТПА 30-102.
Сменным оборудованием в непрерывном справочном стане являются входная проводка первой клети и выводная проводка последней клети, которые служат направляющими для трубы.
Технологические операции при производстве бесшовных труб на установках с 9-клетевым непрерывным станом следующие:
1. Подача пакетов заготовок-штанг длиной 6—12 м, диаметром
140 мм со склада мостовым краном на качающиеся решетки секционных печей.
2. Взвешивание на автоматических весах.
3. Подача дозатором по одной заготовке на загрузочный рольганг
секционных печей.
4. Автоматический замер длины заготовки и передача сведений в за
поминающий блок счетно-решающего устройства для безостаточного деления штанг.
|
|
5. Нагрев заготовки в секционных печах до температуры 1230—
1260° С при скорости перемещения ее в печи от 1,65 до 2,9 м/мин
и производительности до 40 т/ч. Каждая секционная печь имеет
двухручьевые ролики. Ролики зоны выдержки имеют две скорости: скорость зоны нагрева печи и скорость выдачи, равную
12,5 м/мин. После отрезки штанга возвращается в печь для
подогрева перед следующей выдачей.
6. Разрезка нагретых штанг на мерные длины 1320—3200 мм заготовок на двух делительных ножницах, имеющих общую производительность 300 резов в час. Темп выдачи 12 с.
7. Зацентровка заготовки пневматическим центрователем.
8. Передача заготовки по стеллажам в прошивной стан.
9. Прошивка заготовки в прошивном стане в гильзу диаметром
136 мм при толщине стенки 14,5—19 мм, длиной 3700—7000 мм
с коэффициентом вытяжки до 2,9.
10. Передача гильзы на входную сторону непрерывного стана.
11. Введение предварительно промасленной оправки в гильзу. В качестве смазки применяются фосфатные неорганические соединения вместо графита и мазута, использование которых приводит
к появлению дыма и загрязнению цеха; наносят смазку при температуре около 200° С.
|
|
12. Прокатка гильзы в непрерывном стане в трубу всегда одного
диаметра 108 мм с толщиной стенки 3—7,5 мм, длиной до 20,5 м.
В процессе прокатки труба частично сползает с оправки. Прокатка происходит практически без натяжения. Длина оправки
19,5 м. Максимальный коэффициент вытяжки 6,0.
13. Выход бесшовной трубы со стана со скоростью 6 м/с и торможение ее на выходном рольганге, вследствие чего скорость трубы снижается в конце рольганга до 3,5 м/с.
14. Передача трубы с оправкой шлеппером на один из двух рольгангов сдвоенного цепного оправкоизвлекателя.
15. Извлечение оправки. При нормальной работе усилие извлечения
50—70 кН (5—7 тс). Оправкоизвлекатели рассчитаны на усилие
200 кН (20 тс).
16. Передача оправки в ванну для охлаждения с температуры 400° С
до 100° С и затем в промасливающую машину.
17. Передача трубы по рольгангу к дисковым пилам.
18. Обрезка заднего разлохмаченного конца на дисковых пилах.
19. Передача труб на линию калибровочного стана с подогревом
трубы в индукционной печи до температуры 950—1050° С. Индукционная печь состоит из 16 последовательно расположенных индукторов с напряжением 1500 В, силой тока 1000 А, общей мощностью 9 тыс. кВт. Частота тока 2,5 кГц, скорость прохождения
труб через индуктор 1,25—1,8 м/с. Общая длина индукционной
печи 20 м.
20. Прокатка трубы в 11-клетевом калибровочном стане с увеличением длины трубы до 50 м. Калибровочный стан состоит из девяти черновых клетей, имеющих дифференциально-групповой
привод, и двух чистовых клетей, установленных на общей раме
и имеющих общий привод на две клети.
21. Разрезка труб пополам на пиле горячей резки.
22. Передача труб в линию редукционного стана.
23. Нагрев концов для стыкования в секции длиной до 35 м. На
грев в одновитковом индукторе до температуры 1350—1400° С,
мощность сварки 150—250 кВт, частота 2,5 кГц.
24. Поступление по рольгангу секции труб ко второй стыкосварочной
машине, где трубы привариваются к концу бесконечной редуцируемой трубы.
25. Снятие наружного грата на трубах в гратоснимателе.
26. Прохождение трубы через петлеобразователь для обеспечения
безостановочной работы редукционного стана во время стыковки
труб.
27. Правка трубы после петлеобразователя.
28. Подогрев труб до температуры 950—1050° С в индукционной
подогревательной печи. Характеристика печи дана выше.
29. Редуцирование трубы в 19-клетевом редукционном стане с увеличением длины трубы до 120—150 м и выходом трубы из последней клети со скоростью до 12 м/с. Редукционный стан состоит из трехвалковых клетей. Первые по ходу прокатки 17 черновых клетей имеют дифференциально-групповой привод. Последние две клети имеют общий привод на две клети.
30. Разрезка трубы на части длиной до 24 м на летучих, ножницах
(при скорости выхода до 7 м/с) или летучей пиле (при скорости
выхода более 7 м/с).
31. Сбрасывание трубы с рольганга сбрасывающим устройством.
32. Выравнивание и начало охлаждения на винтовой секции холодильника.
33. Охлаждение труб на цепной секции холодильника.
Клети непрерывного девятиклетевого стана расположены под углом 45° к горизонту и 90° по отношению друг к другу. Благодаря этому труба в месте выпусков в следующей клети раскатывается в круглой части калибра.
ДЕВЯТИКЛЕТЕВОЙ СТАН
Стан имеет 9 двухвалковых нереверсивных клетей с индивидуальным приводом. Клети расположены под углом 45º к горизонту и 90°друг к другу. В каждой клети производится по одному проходу. Раскатку гильзы в черновую трубу ведут на длинной подвижной оправке. Длина оправки 19,5м.
Непрерывная прокатка на длинной оправке получила широкое применение при производстве тонкостенных труб из углеродистых и низколегированных сталей. Основное достоинство процесса – возможность прокатки черновых труб большой длины (до 33 м) с высокой (до 7м/с) скоростью прокатки. Суммарное обжатие на стане – 60-80= 3l%, общий коэффициент вытяжки-7.
Трубы имеют хорошее качество наружной и внутренней поверхности, низкую разностенность. Обычно на непрерывных станах прокатывают трубы одного-двух диаметров с различной толщиной стенки, зависящей от диаметра оправки, а получение труб широкого диапазона диаметров и толщин стенок достигается прокаткой на многоклетевом редукционном стане.
Дата добавления: 2019-02-22; просмотров: 1547; Мы поможем в написании вашей работы! |
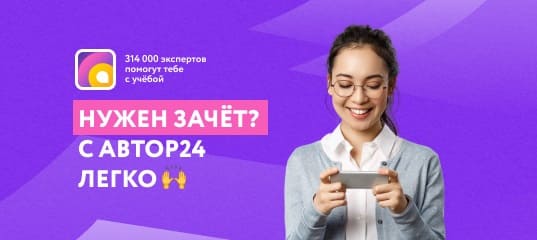
Мы поможем в написании ваших работ!