Получение композиционных материалов на металлической основе, армированных волокнами
Выбор метода получения композиции из различных сочетаний матрицы и армирующего волокна определяется следующими факторами:
• размерами, профилем и природой исходных материалов матрицы и упрочнителя;
• возможностью создания прочной связи на границе раздела матрица - упрочнитель;
• получением равномерного распределения волокон в матрице;
• возможностью совмещения процессов получения композиционного материала и изготовления из него деталей;
• экономичностью процесса.
При производстве композиционных материалов с металлической матрицей наибольшее распространение получили твердофазные, жидкофазные, газопарофазные, химические и электрохимические процессы.
Твердофазный метод совмещения компонентов композиции предполагает использование материала матрицы в виде листов, фольги, проволоки или порошка. Композиционный материал получают одним из следующих приемов: диффузионной сваркой под давлением; сваркой взрывом; деформационной обработкой под давлением; прессованием с последующим спеканием (порошковой металлургией).
Жидкофазные процессы получения композиционных материалов заключаются в пропитке упрочняющих волокон или нитевидных кристаллов, расположенных в определенной последовательности или беспорядочно, расплавом материала матрицы.
К жидкофазному процессу следует отнести метод получения композиции направленной кристаллизацией из расплавов эвтектического состава. Важнейшим моментом получения качественного композиционного материала пропиткой является хорошая смачиваемость упрочняющих волокон расплавом матрицы. Возможности метода значительно ограничиваются высокой реакционной способностью материалов волокон в контакте с металлическими расплавами.
|
|
Газопарофазными способами наносят на армирующие волокна барьерные или технологические покрытия, обеспечивающие их защиту от разрушения при взаимодействии его с материалом матрицы. Их фазовый состав (чаще всего нитриды, бориды, оксиды, карбиды) выбирают исходя из физико-химической и термомеханической совместимости армирующих волокон и материала матрицы. Покрытия получают в результате либо разложения летучих карбонильных соединений металлов, либо испарения металлов и сплавов при термическом воздействии электронным лучом, ионными пучками.
Методом газотермического плазменного напыления получают полуфабрикаты композиционных материалов. Плазменным напылением наносят покрытия из матричного материала на армирующие волокна без существенного повышения их температуры. Прочность сцепления покрытия с основой определяется механическим сцеплением частиц напыляемого металла или сплава с шероховатой поверхностью, силами адгезии и химическим взаимодействием. Прочность связи плазменных покрытий значительно ниже, чем покрытий, получаемых металлизацией, испарением или конденсацией в вакууме.
|
|
Электролитические методы позволяют получать композиционные материалы в результате осаждения матричного материала на нитевидные кристаллы и волокна, которые непрерывно находятся в контакте с катодом. Процесс протекает при низкой температуре и в отсутствие давления, что практически полностью исключает разрушение волокон и вредное влияние температурного фактора. Покрытие получается плотным, беспористым в том случае, если оно равномерно покрывает поверхность волокон и пространство между ними. Пористость наблюдается при использовании волокон бора, карбида бора или металлических волокон диаметром более 100 мкм.
Химические методы позволяют осаждать металлические покрытия на не проводящие ток упрочнители в виде нитевидных кристаллов (сапфир), а также на углеродные волокна (ленты, пряди). Металлическая пленка точно воспроизводит профиль волокна, и ее толщина легко контролируется параметрами технологического процесса. Сущность химического метода осаждения покрытий заключается в восстановлении ионов металлов на поверхности покрываемого вещества.
|
|
Методом химического осаждения получают покрытия толщиной до 30 мкм и более. Наиболее широко используют осаждения на упрочнители никеля, в меньшей степени меди, хрома, кобальта.
Свойства композиции наиболее полно реализуются в деталях и узлах с непрерывным расположением волокон. Целесообразно изготавливать детали из композиционного материала непосредственно в процессе производства композиции. Изготавливать детали и элементы конструкций из полуфабрикатов композиционных материалов в виде прутков, листов, труб, лент и т. п. затруднительно, и в этом случае не реализуются до конца преимущества композиционных материалов по сравнению с обычными.
Дата добавления: 2019-02-22; просмотров: 272; Мы поможем в написании вашей работы! |
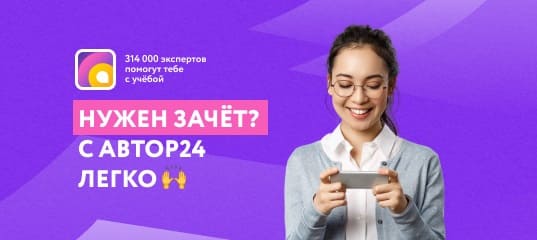
Мы поможем в написании ваших работ!