Керамика на основе глинистого сырья.
Фарфор.
Фарфор – основной представитель тонкой керамики. Характерные признаки фарфора – белый цвет с синеватым оттенком, малая пористость и высокая прочность, термическая и химическая стойкость и декоративные достоинства.
Особенности фарфора определяются его химическим составом, строением черепка, которые зависят от назначения изделий, условий их эксплуатации и предъявляемых к ним требований.
Фарфор был известен в Китае уже в самые древние времена. Фарфор был получен при сильном прокаливании («обжиге») пластичных масс, изготовленных перемешиванием каолина (фарфоровой земли) с порошкообразным полевым шпатом и кварцем с добавлением небольшого количества воды. Если температура обжига не слишком высокая, то форма изделий сохраняется, только объём сильно уменьшается, так как фарфор «садится» при обжиге. Одновременно масса («черепок») становится плотной (водонепроницаемой) и звонкой.
В средневековом мире китайские императоры были «эксклюзивными дистрибьюторами» фарфоровой посуды. Китайцы умели хранить секреты производства. Европейцы открыли собственную рецептуру изготовления фарфора. Это произошло при дворе саксонского императора Августа в 1708 году. И вскоре по всей территории Германии, а затем и остальной Европы в том числе в России начали открываться многочисленные фарфоровые мануфактуры. 1 февраля 1744 года камергер императрицы барон Николай Корф, находившийся в Стокгольме с дипломатическим поручением, заключил договор с неким Христофором Гунгером, который обязался «учредить в Санкт-Петербурге мануфактуру для делания чистого фарфора так, как оный в Саксонии делается». В 1744 в Петербурге была основана Порцелиновая мануфактура, на которой через три года Д. И. Виноградовым было начато производство русского фарфора. В 1765 мануфактура получила более высокий статус и стала называться Императорский фарфоровый завод, где с конца 18 века выпускались прекрасные сервизы, вазы, портретные бюсты в стиле раннего классицизма, а позднее в стиле ампир. Со дня основания завод работал по заказам императорского двора.
|
|
Ценность фарфора определяют четыре фактора: материал, форма, декор и глазуровка.
Различают два вида фарфора - твердый и мягкий. Твердый фарфор получают из массы, содержащей 50 % глины и каолина, 25 % кварца и 25 % полевого шпата. Это классический состав, который может быть изменен в зависимости от вида исходных материалов. В фарфоре содержится более 60%, SiO2, а также другие оксиды К2О, А2О3. От обычного или твердого фарфора отличается мягкий фарфор, из которого изготовляют главным образом художественные изделия. В мягком фарфоре содержится меньше каолина и соответственно больше «плавней», например, полевого шпата, мела. Такой фарфор в соответствии с его легкоплавкостью подвергают обжигу при менее высокой температуре (обычно при 1200-1300°С). Поэтому легко удается произвести его многоцветное подглазурное раскрашивание.
|
|
Термическая обработка исходной шихты при производстве фарфора вызывает сначала разложение каолина и в частности его основного компонента каолинита Аl2О3•2SiO2• 2Н2О. Минерал отдает конституционную воду, затем он разлагается на Al2O3 и SiO2, которые растворяются в стеклообразно размягчённом полевом шпате. При дальнейшем повышении температуры полевой шпат растворяет в возрастающих количествах крупнокристаллический кварц. По мере того, как полевой шпат обогащается двуокисью кремния, из него осаждается муллит 3Al2O3•2SiO2. Готовый фарфор состоит из стекловидной основной массы, которая пронизана тесно сплетенными между собой иглами муллита и оставшимися нерастворёнными зернышками кварца (и крохотными пузырьками воздуха). Как правило, обжиг производят дважды. После первого обжига, так называемого «сырого обжига», идущего приблизительно при 900°C, на фарфор наносят прозрачную глазурь: полученные после сырого обжига ещё пористые черепки быстро погружают в глазурную массу – водную суспензию каолина, глины, полевого шпата и мрамора. При нагревании из неё образуется тугоплавкое стекло. Последующим высушиванием (около 1450°С) производят окончательный обжиг. Часто фарфор подвергают еще третьему обжигу в муфельной печи при красном калении после нанесения красок, т.е. перетертого со скипидаром мелкоизмельчённого цветного стекла.
|
|
К физическим свойствам фарфора относятся плотность, белизна, просвечиваемость, механическая прочность черепка и глазури, блеск и твердость глазури, термическая стойкость, электрическая прочность и др.
Белизна является важным показателем качества фарфора. Она зависит от наличия в сырьевых материалах примесей железа, титана, хрома и других окрашивающих соединений, а также от режима и среды в печи при обжиге. Исходные материалы очищают от окрашивающих примесей. Существенно влияет на белизну фарфора наличие глазурного слоя и его толщина. С увеличением толщины глазурного слоя белизна снижается.
На механическую прочность черепка влияет степень дисперсности зерен кварца: чем тоньше помол, тем выше прочность за счет уменьшения пористости. Фарфор, как и стекло, в 12-13 раз лучше сопротивляется сжатию, чем растяжению.
|
|
Блеск глазури зависит от ее состава, температуры обжига, а также наличия в ней различных газовых включений и коэффициента преломления. Повышенным блеском характеризуются свинцовые, стронциевые и титановые глазури, а также глазури, содержащие редкоземельные элементы. Наличие в стекловидной фазе глазури воздушных и газовых включений сильно снижает ее блеск. При соответствии температуры политого обжига температуре плавления глазури достигается хороший блеск. Если температура обжига ниже, то глазурь имеет матовость.
Фарфор используют не только для изготовления домашней посуды и художественных изделий, но также, и при том в весьма широкой степени, для изготовления химической посуды, а благодаря его электроизоляционным свойствам – для изготовления изоляторов. В производстве электротехнического и химического оборудования широко применяют фарфор с незначительной долей закрытых пор, получаемый на основе смеси SiO2 (77,8 - 75,2%), А12О3, (19,3 - 21,1%), К2О (2,7 - 4,4%). Он обладает высокими электроизоляционными свойствами, механической прочностью и стойкостью во всех кислотах, кроме плавиковой.
Фаянс.
Фаянс, как и фарфор, белого или почти белого цвета. Однако он мягче, так что сталь оставляет на нём царапины; он легче ломается, порист, поэтому в большинстве случаев его необходимо покрывать глазурью. Фаянс получают из смеси глины, кварца, щелочи и сурика, иногда добавляют ещё окрашивающие окислы. Фаянс обжигают дважды: сначала без глазури при 1200-1300°C (сырой обжиг), а затем несколько слабее с глазурью (окончательный обжиг). Из тонкого фаянса делают мойки, ванны для купания и т.п. Некоторые сорта фаянса часто окрашивают титановой кислотой в бледно-кремовый цвет (умывальники). Примерами неглазурованного фаянса служат глиняные сосуды, глиняные трубки.
Фаянс имеет грязновато-серый пористый излом. Поэтому его покрывают глазурью, которая благодаря прибавлению двуокиси олова имеет белый цвет и непрозрачна. Раньше фаянс часто применяли для изготовления дешёвой посуды; однако фаянс изготовленный Веджвудом в Англии, почти совершенно вытеснил обычный фаянс из домашнего обихода. Более тонкий фаянс пригоден для художественной керамики. По своим свойствам фаянсу приближается майолика, покрываемая цветной глазурью.
Гжель.
Гжель – вид керамики, в основном посуда, характеризующейся синей кобальтовой росписью по белому фону. Подмосковная гжель являетсяизвестным крупным народным художественным керамическим промыслом. Этот район из 30 сел и деревень, бывших Бронницкого и Белгородского уездов, в 60 км от Москвы (ныне Раменский район), давно славился своими глинами и гончарами. Центром гончарства была Гжельская волость – деревни Речицы, Гжель, Жирово, Турыгино, Бахтеево и др., где было много мастерских. Созданная народными мастерами гжели система решения пластической формы и декоративной росписи имеет значение целой художественной школы русской народной керамики. Гжельская посуда завоевала большую популярность.
![]() | Рис. 7.2. Изделия из русской гжели. |
Дата добавления: 2019-02-22; просмотров: 348; Мы поможем в написании вашей работы! |
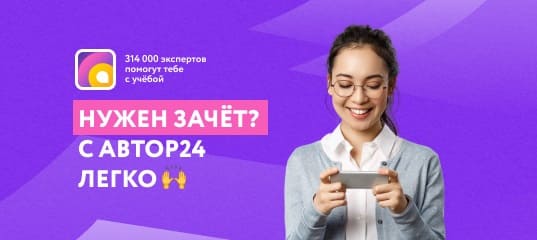
Мы поможем в написании ваших работ!