Основные отделы завода и их назначение.
Белорусский Национальный Технический Университет
Кафедра «Материаловедение в машиностроении»
Гр. 104218
ОТЧЁТ
по преддипломной практике
на ПО «Минский завод колесных тягачей»
Выполнил: Васильев А.В.
Руководитель практики: Борисов С.В.
Руководитель практики от МЗКТ: Жинович П.В.
Минск–2013
Содержание.
Введение.
1. Термический цех.
1.1. Назначение термообработки.
1.2. Оборудование термического цеха.
1.3. Закалка ТВЧ.
2. Гальванический цех.
3. Структура термического цеха.
4. Основные отделы завода и их назначение
5. Центральная заводская лаборатория.
6. Отдел технологического контроля
7. Техника безопасности и охрана труда при работе.
8. Экономический раздел
Введение
Минский завод колесных тягачей – единственное в СНГ предприятие, специализирующееся на выпуске уникальных многоосных автомобилей, автопоездов и колесных шасси высокой проходимости и грузоподъемности.
Белорусские многоосные автомобили своим техническим уровнем и надежностью завоевали высокий авторитет в Вооруженных Силах России, Содружества Независимых Государств, а также стран дальнего зарубежья. В настоящее время специализированные автомобили с эмблемой ВОЛАТ («Волат» – в переводе с белорусского языка «богатырь») успешно работают в разных отраслях – в нефтяной, газовой, лесной, строительной промышленности, в геологоразведочном и коммунальном хозяйстве. Страны, в которых эксплуатируются автомобили: Россия, Китай, Корея, Пакистан, Йемен, Ливия, Алжир, Египет, Сирия, ОАЭ, Вьетнам, Индия, Югославия, Румыния, Турция.
|
|
Минский завод колесных тягачей образован в 1991 году на базе производства специальных колесных тягачей Минского автомобильного завода, которое специализировалось ранее на выпуске транспортной базы для мобильных ракетных комплексов бывшего СССР – полноприводных колесных шасси.
Первое поколение внедорожных автомобилей появилось в 50-х годах. Это были полноприводные инженерные и артиллерийские тягачи. Воплощенные в них технические решения наглядно показали большие возможности этой техники, а созданные в 70-х годах на базе четырехосных шасси грузовые автомобили и тягачи стали незаменимыми для нефтяников, газовиков, геологов и строителей при освоении труднодоступных районов Сибири и Средней Азии.
|
|
Располагая современным оборудованием, специалистами высокой квалификации, которые имеют многолетний опыт создания, производства и эксплуатации внедорожной автомобильной техники большой грузоподъемнотси, завод успешно осуществляет конверсионную программу.
В 1986 году введен в эксплуатацию цех гибких производственных систем.
В 1987 году производство специальных колесных тягачей достигло самого высокого пика выпускаемой продукции.
В 1990 году изготовлены экспериментальные образцы восьмиосных шасси 7922 и 7923.
В 1991 приказом генерального директора ПО «БелавтоМаз» организован Минский завод колесных тягачей. Высокий уровень технологии, помноженный на хорошую профессиональную квалификацию персонала, позволили значительно улучшить качество и надежность выпускаемой продукции.
В 1998 году указом Президента российской Федерации группа работников МЗКТ награждена орденом Дружбы «За большой вклад в создание специальной техники, укрепление дружбы и сотрудничества между народами».
1999 – сороколетний трудовой юбилей со дня организации производства специальных колесных тягачей.
На протяжении многих лет завод являлся важным научно-техническим и производственным объектом военно-промышленного комплекса Советского Союза. Коллектив завода с искренним одобрением воспринял мирные инициативы стран бывшего СССР и последовавшее за ним резкое сокращение вооружений. В результате разработанной программы конверсии завод взял курс на создание и освоение производства новых специализированных автомобилей и автопоездов широкого назначения для различных отраслей промышленности. Накопленный практический опыт по созданию трех- , четырех- , шести- , семи- и восьмиосных транспортных средств позволяет МЗКТ изготавливать технику под любой конкретный заказ самого требовательного делового партнера. Завод располагает высоким научно-техническим потенциалом, квалифицированным инженерным персоналом и исследовательским центром, оснащенным современным испытательным оборудованием.
|
|
Для предприятий и транспортных организаций строительного, нефтегазового и машиностроительного комплексов завод предлагает:
· Внедорожные автомобили и автомобили-самосвалы грузоподъемностью 22 и 24 тонны, а также автопоезда грузоподъемностью от 34 до 75 тонн;
· Внедорожные четырех и шестиосные шасси и автопоезда под оборудование для капитального ремонта и бурения скважин, а также автопоезда для перевозки труб длиной 36 метров;
|
|
· Специальные четырехосные шасси автомобильного типа под монтаж кранового и другого грузоподъемного оборудования грузоподъемностью 50 тонн и вылетом стрелы 50 м;
· Готовы разработать и изготовить специальные колесные шасси по требованию самого взыскательного Заказчика.
Семейство «Волат» – это полноприводные автомобили колесной формулы 8х8, предназначенные для движения по всем видам дорог, так и по местности, наиболее полно их эффективность проявляется в сложных дорожных условиях.
Функциональная панель приборов, регулируемые сидения и спальные места создают повышенный комфорт для водителя.
Специально для этих машин разработан целый ряд прицепов и полуприцепов с такими же шинами и такой же колеей. Их также можно использовать как на всех типах дорог, так и на бездорожье.
Назначение основных видов автопоездов:
· для перевозки различных грузов
· для перевозки леса в сортиментах
· для транспортировки плетей труб длиной до 36-ти метров и массой до 40 тонн
· под монтаж и транспортировку различного оборудования массой 34 (40) тонн.
· для перевозки крупногабаритных грузов или тяжелой гусеничной техники массой до 50-ти тонн
· для перевозки техники в условиях ограничений по высоте (полуприцеп имеет малую погрузочную высоту)
· для перевозки грузов и техники массой до 65-ти тонн
Многолетний опыт создания и производства специальных колесных шасси большой и особо большой грузоподъемности для нужд МО бывшего СССР позволил заводу создать с учетом требований различных заказчиков широкую гамму колесных шасси под монтаж самого разнообразного оборудования и транспортировку его как по всем видам дорог, так и без дорог.
Специальные шасси 6923 и 69232 с колесной формулой 8х4, с двухместной кабиной, расположенной перед двигателем мощностью, соответственно, 243 кВт (330 л.с.) и 265 кВт (360 л.с.) предназначены для монтажа кранового оборудования массой до 22,5 тонн. Шасси 6923 используется в составе крана КС-6473 производство ПО «Краян» (Украина), шасси 69232 – в составе крана МКШ-40 Средневоложского машиностроительного завода №1 (Россия) грузоподъемностью 50 тонн. Шасси могут быть с успехом применены и в составе автопоездов.
МЗКТ располагает значительными производственными мощностями и специалистами высокой квалификации для производства автомобильной техники большой грузоподъемности и проходимости. Проведение в сжатые сроки опытно-конструкторских работ и освоение их в производстве позволили сохранить численность коллектива. Проводятся работы по повышению технического уровня выпускаемой продукции при одновременном сокращении сроков и стоимости ее создания, внедрению в практику инженерных, экономических и других служб завода новой информационной технологии и технологической оснастки. С целью повышения качества, расширения экспортных возможностей, повышения конкурентоспособности коллективом завода проводится большая работа по применению моторно-трансмиссионных установок «Детройт дизель», «Мерседес-Бенц», «МАН», «Катерпиллер», имеющих развитое сервисное обслуживание в регионах сбыта. Разработанные мероприятия по созданию новой техники и рациональное использование производственных площадей позволили довести долю продукции гражданского назначения в общем объеме до более чем 90%, повысить качество и надежность, тем самым поднять ее технический уровень до лучших мировых аналогов.
Термический цех является основным производственным подразделением завода, действующим на основе внутрихозяйственного расчета и административно подчиняется начальнику производства. Структурная схема управления предприятием «МЗКТ» приведена в приложении А.
Цех имеет в своем составе структурные подразделения согласно схеме а приложении Б. Руководство цехом осуществляет на основе единоначалия начальник цеха, который является полноправным руководителем и организатором производства и труда в коллективе цеха. Начальник цеха имеет двух заместителей. Конечной структурной единицей являются производственная и вспомогательная бригады. Работа в бригаде организуется бригадиром, который подчиняется сменному мастеру, мастер подчиняется старшему мастеру или заместителю начальника цеха по производству. Наличие должности старшего мастера определяется численностью рабочих на данном участке.
1. Термический цех.
1.1. Назначение термообработки
При решении вопроса качества выпускаемых автомобилей, их надежности и долговечности, а также надежности и долговечности инструмента важнейшую роль играет ТО.
ТО — один из эффективных и экономичных методов упрочнения металлов и сплавов. ТО металлов является составной частью общего цикла изготовления деталей машин и инструмента, позволяет повысить долговечность деталей и, следовательно, машин, уменьшить их массу и габаритные размеры.
На МЗКТ имеется термогальванический корпус, состоящий из двух цехов: термический и гальванический цех. Также в состав этого корпуса входит экспресс-лаборатория, которая контролирует качество продукции обоих цехов.
Цех имеет два участка: №1 и №2. На 1-ом участке проводится закалка длинноосных деталей, цианирование, обработка ТВЧ и очистка. На 2-ом участке проводится улучшение, нормализация, отжиг, химико-термическая обработка, полное азотирование.
Основными видами ТО являются:
1) Цементация (поверхностное насыщение стали углеродом, в результате чего получается высокоуглеродистый поверхностный слой),
2) Закалка и высокий отпуск (существенно улучшается общий комплекс механических свойств);
3) Нормализация (разновидность отжига, при котором охлаждение проводят на спокойном воздухе, что создает более быстрое охлаждение, чем при обычном отжиге),
4) Цианирование (процесс одновременного насыщения стали С и N),
5) Ионно-вакуумное азотирование;
Важным видом ТО на МАЗе является науглераживание (цементация). Этой операции подвергаются шестерни, валы, муфты, крестовины и т. д. Термической и химико-термической обработке подвергаются различные марки стали:
- углеродистые (10,20, 25,35,40,45);
- легированные (40Х, 40ХН, 65Г, 35ГСА, 45Х2МФА)
Цементируются стали: 12ХНЗА, 15ХФ, 18ХТТ, 15ХГБ2ДА, 25ХГТ, 20ХНР, 20ХНМ, углеродистые стали 20 и 45. Подвергаются цианированию стали: 10, 20, ЗКП, 18ХГТ,40Х.
1.2. Оборудование термического цеха
Все оборудование термического цеха разделяют на: основное (термические печи, печи-ванны) и дополнительное (прессы, моечные машины)
По принципу действия термические печи подразделяются на: печи периодического действия (камерные, шахтные) и печи непрерывного действия (конвейерные, карусельные, толкательные).
По источнику тепловой энергии печи делят на: нефтяные, газовые и электрические. По технологическому назначению на: для закалки, для отпуска, цементации и азотирования.
Оборудование для цементации:
1) шахтные печи ПН-34(СШО),
2) агрегаты ХТО 2ВГТЦА-600П;
3) линия универсальных камерных печей фирмы «Pekat» и «Elterma».
Процесс идет в среде эндогаза и природного газа при t = 920-950°С. Основные глубины: 0,8-1,2 мм, 1,0-1,5 мм, 1,3-, 1,8 мм, 0,3-0,6 мм. После ХТО в Ц-105 может производится дальнейшая мехобработка и последующая закалка. После 26ГТЦА-600П и очистки детали могут подвергаться шлифовке, но в основном идут на сборку.
Закалка и отпуск (низкий, средний, высокий) производится в конвейерных агрегатах СКЗА8401/3, СИЗА4201/3 и толкательных агрегатов СТЗА5405/3. Оборудование работает без защитной атмосферы.
Производительность оборудования:
СКЗА—150-300 кг/ч
СИЗА — 50-60 кг/ч
СТЗА— 150-250 кг/ч.
Основные изделия: цапфы, кольца, метизы, рычаги и т. д.
Нормализация производится в шахтных печах У-105 (50-60 кг/ч) и агрегате СКЗА-8501/11 (350-400 кг/ч).
Цианирование производится в соляных ваннах С-100, в расплаве солей: NaCl, СаСl, Fe(CN)6. Основные глубины: 0,1-0,2 мм, 0,05-0,35 мм, t= 850°С. Основные стали: 40Х, СтЗКП, А12, Ст10-20, Ст35.
После цианирования и закалки из С-100 детали проходят низкий отпусках в печах ПН-34, ПН-32, Детали, имеющие сложную геометрическую форму, проходят ХТО в печах фирмы «Elterma» (Польша). Процесс идет в плазме тлеющего разряда в среде диссоциированного аммиака в вакуумной камере, t= 520-680°C, h=0,l 5-0,5 мм, твердость HV = 500-1200. Детали имеют минимальное коробление.
Дополнительное оборудование:
1) Правильные прессы (правка стержней, осей, валов, протяжек);
2) Травильные установки (очистка от окалины 3-5% раствором MnSO.0;
3) Моечные машины (очистка после ХТО и ТО от солей, масла, грязи 8% раствором соли);
4) Дробеструйная установка (очистка дробью деталей массового производства);
5) Дробеметная установка (очистка от окалины потоком металлической дроби, летящей со скоростью 60 м/с);
6) Эндотермический генератор (приготовление контролируемых атмосфер).
Оборудование для контроля качества по твердости: ТК-2М,ТШ-2Н. В составе ТГК имеется экспресс-лаборатория, которая проводит металлографический, газовый, химический анализ.
1.3. Закалка ТВЧ
Закалка при поверхностном нагреве ТВЧ (без упрочнения сердцевины детали) заключается в нагреве и последующем быстром охлаждении деталей на толщину, равной требуемой толщине закаленного слоя.
Поверхностная закалка при глубинном нагреве ТВЧ (с упрочнением сердцевины) заключается в нагреве деталей на толщину, большую чем требуемая толщина закалочного слоя с последующем быстрым охлаждением. Вследствие этого деталь калится на толщину, определяемую прокаливаемостью.
Закалка с индукционным нагревом ТВЧ применяется для упрочнения деталей несложной конфигурации, изготавливаемой из углеродистых и низколегированных марок стали (30, 35, У7, У10, 40Л-11). После закалки детали проходят промывку в шахтной моечной печи.
Закалка ТВЧ бывает двух видов: одновременная и последовательная. При одновременной закалке деталь устанавливается в индуктор, нагревается, а затем через спрейер индуктора подается вода и она закаливается.
При последовательной закалке деталь проходит через индуктор с определенной скоростью, при этом она нагревается и сразу охлаждается по мере прохождения через индуктор.
2. Гальванический цех.
Коррозия металлов — разрушение металлов вследствие химического или электрохимического взаимодействия их с коррозионной средой. Коррозия сопровождается распадом структурных составляющих металла, снижением его прочности, твёрдости, износостойкости и т.д.
Коррозия может быть уменьшена или практически устранена нанесением электрохимических, химических и анодно-окисных покрытий. Покрытия служат не только средством защиты от коррозии, но и способом повышения износостойкости деталей, повышения электропроводности, способности к пайке и др. свойств поверхности.
Для нанесения электрохимических, химических, анодно-окисных покрытий на детали машин предназначен гальванический цех. За год в цехе проводят обработку примерно 13500 тонн деталей автомобиля.
Гальванический цех входит в структуру термо-гальванического корпуса МЗКТ. Общая численность работающих 194 человека, в том числе:
-производственных рабочих — 75 человек;
-вспомогательных рабочих — 96 человек;
-инженерно-технических работников — 23 человека.
Находится гальванический цех в механосборочном корпусе № 1 на 1 и 2 этажах в осях П-Ж 49-52. Площадь цеха составляет 13800 м2, т.ч. производственная-6620 м2.
На 1 этаже размещено вспомогательное оборудование: источники тока выпрямители ВАКГ-6300,, вентиляционные установки с фильтрами, ёмкости для приготовления и слива электролитов, насосы.
На 2 этаже размещено основное гальваническое оборудование. Там размещены автоматические линии цинкования в колоколах, на подвесках, твердого хромирования на подвесках, фосфатирования на подвесках. Так же механизированные линии цинкования в барабанах и на подвесках, трёхслойного фосфатирования в корзинах, анодирования алюминия на подвесках, линия травления.
На отметке "-5,8" размещён подвал в осях П-К6 49-52 площадью 375 м2. В подвале размещены ёмкости для сбора отработанных растворов, промывных вод и насосы для перекачки их на заводскую станцию нейтрализации.
В гальваническом цехе имеются следующие вспомогательные службы:
1) экспресс-лаборатория - выполняет анализ растворов электролитов;
2) мастерская по ремонту и изоляции подвесок;
3) участки приготовления и корректирования электролитов;
4) мастерские механика и энергетика;
5) кладовая кислот и хим. реактивов;
6) участки контроля качества толщины покрытий.
В основу организации производства гальванического цеха положен принцип групповой обработки технологически и конструктивно подобных деталей.
В гальванический цех детали поступают из разных цехов завода. Все детали и узлы из цехов поступают в спец. унифицированной оборотной таре, обеспечивающей сохранность.
Поверхность деталей должна удовлетворять следующим
требованиям:
1) поверхность деталей из горячекатанного металла должна быть чистой, без видимых следов окалины, ржавчины и др. загрязнений; шлифованные и полированные детали должны поступать без забоин, вмятин, раковин, прижогов, трещин, заусенцев, пор;
2) независимо от вида механической обработки и подготовки деталей острые углы и кромки деталей должны быть скруглены или иметь фаски, за исключением технически обоснованных случаев.
Вид и толщина покрытия — в соответствии с требованиями конструкторско-технологической документации, определяемыми при разработке того или иного изделия, в зависимости от условий его эксплуатации или хранения. Толщина гальванического покрытия кратна "3". Покрытие деталей автомобиля МЗКТ, в зависимости от вида, имеет следующую толщину:
- цинкование — 6-12 мкм;
- хромирование твёрдое — 9-30 мкм;
- никелирование—9-21 мкм;
- меднение — 9-12 мкм.
Гальванические покрытия контролируют в основном по толщине и внешнему виду.
При контроле гальванических покрытий по внешнему виду детали подразделяют на годные, дефектные и бракованные. Дефектными считаются детали, требующие снятия недоброкачественного покрытия и нанесения нового. К дефектам гальванических покрытий относят подгар, питтинг, отслоение, шелушение и др. Дефекты гальванических покрытий возникают по следующим причинам: плохая подготовка поверхности, нарушение режима процесса осаждения, неправильный состав электролита, неправильное расположение деталей относительно анода. К браку гальванических покрытий относят перетравливание.
Толщину гальванических покрытий определяют в основном струйно-объёмным методом. Этот метод основан на растворении покрытия раствором, подающимся на поверхность контролируемой детали в виде струи с определённой скоростью. Толщину покрытия рассчитывают по объёму раствора, затраченному на растворение покрытия.
Гальваническое производство связано с выделением большого
количества вредных для организма человека паров и газов. Разработана
система мероприятий, направленных на улучшение условий труда.
Гальванические ванны снабжены бортовыми отсосами. Кроме бортовых
отсосов в цехе установлена общая вытяжная и приточная вентиляция.
Вентиляционные установки размещены в отдельных звукоизолированных помещениях для уменьшения уровня шума. Зеркало ванн хромирования и травления защищено полиэтиленовыми шариками для снижения газовыделения и испарения растворов. Пол гальванического цеха не впитывает растворы электролитов и имеет уклон для обеспечения стоков жидкости. Раздача по ваннам гальванических линий растворов щёлочи и серной кислоты производится централизованно насосами. Рабочие цеха ежемесячно проходят инструктаж по безопасности труда с регистрацией в специальном журнале. Принятие пищи и курение в рабочих помещениях строго запрещается.
По опасности поражения электрическим током гальванический цех относится к классу "помещения особо опасные". Для предотвращения возможности поражения электрическим током всё оборудование заземлено, токоведущие части изолированы.
По взрывоопасной и пожарной опасности гальванический цех относится к категории "Д". В цехе установлены противопожарные посты, где имеется противопожарный инвентарь, пенные огнетушители и ящики с сухим песком.
Структура термического цеха.
Основные отделы завода и их назначение.
Создание конструкций тракторов, их внедрение в серийное производство осуществляют на заводе инженерно-технические службы.
Главными инженерными службами завода являются: ГСКБ – головное специализированное конструкторское бюро (отдел главного конструктора); отдел главного технолога; отдел главного металлурга; отдел главного сварщика; отдел механизации и автоматизации производства.
ГСКБ – осуществляет разработки новых конструкций тракторов, усовершенствование модификаций, поставленных на производство, участвует в проведении заводских, межведомственных, полевых и других испытаний тракторов в выдаче технической документации подразделениям завода.
Основной технологической службой завода является отдел главного технолога (ОГТ), в функции которого входит организация производства на заводе, начиная от разработки технологических процессов. ОГТ обеспечивает централизацию проведения технологической подготовки и технологическое обслуживание механообрабатывающего производства, реконструкцию, перепрофилирование производства, создание новых цехов и их специализацию. ОГТ состоит из многих специализированных подразделений и бюро, имеющих определённую направленность в работе, а имеющиеся в цехах технологические бюро подведомственны ОГТ. Отдел имеет большую центральную технологическую лабораторию, которая занимается апробированием и внедрением в цехах новых технологий.
Организацией и развитием заготовительного производства на заводе занимается служба главного металлурга. Она решает все вопросы перевооружения и реконструкции заготовительных цехов, осуществляет комплексную механизацию и автоматизацию производственных процессов.
Структурно служба состоит из многих специализированных бюро, возглавляемых опытными специалистами. В ее составе имеются бюро: подготовки производства; технологическое бюро; кузнечно-штамповочного производства, проектно-конструкторское бюро; технологическое бюро по всем видам термообработки и всем идам чугунного, стального, цветного и специальных видов литья, а также модельно-конструкторское бюро.
Отдел главного сварщика состоит из технологических и конструкторских бюро. Технологические бюро разрабатывают технологии по всем видам сварки; конструкторские бюро разрабатывают сварочное оборудование, сварочную оснастку и т.д. ОГС проводит научно-исследовательские работы с привлечением различных НИИ. Сварочное производство завода освоило полуавтоматическую и автоматическую сварку в среде углекислого газа, автоматическую под слоем флюса, контактно-точечную, стыковую, сварку трением.
Отдел механизации и автоматизации (ОМА) осуществляет комплексную механизацию и автоматизацию всех видов производств завода, разрабатывает нестандартное оборудование. Для выполнения этой задачи в ОМА имеются конструкторские и другие бюро определенного профиля для разработки средств механизации в литейных, кузнечных, механосборочных и других цехах. Изготовлением разрабатываемой ОМА оснастки в составе этого отдела занимается цех нестандартного оборудования. Специфика отдела очень разнообразна. ОМА разрабатывает подъемно-транспортное оборудование и различные стенды для испытаний узлов и механизмов в цехах, механизирует работы складских помещениях.
ОКС – отдел капитального строительства. Осуществляет руководство капитальным строительством производственных объектов и объектов соцкультбыта, жилья собственными силами. Заказывает оборудование и комплектующие к нему.
ФО, ПЭО, ООТиЗ – финансовый, планово-экономический отделы, отдел труда и заработной платы. Отделы осуществляют финансовую, планово-экономическую деятельность завода, производят расчёт и оплату заработной платы работающих.
ОВК – одел внешней кооперации. Осуществляет и регулирует поставку узлов и комплектующих изделий на сборку с других заводов, а также поставку заготовок, поковок и литья.
ОМТС – отдел материально-технического снабжения. Занимается снабжением завода металлопрокатом, сырьём для металлургического производства, материалами и комплектующими изделиями на ремонт оборудования, химикатами, красками и другой необходимой заводу продукцией.
ОВЭС – отдел внешнеэкономических связей. Осуществляет и регулирует экспортные поставки тракторов и запасных частей с зарубежными странами, а также комплектующих изделий на трактора.
ОТК – отдел технического контроля. Производит контроль всех изготовленных на заводе изделий, а также входной контроль получаемой про-
дукции. В состав ОТК входит ЦЗЛ – центральная заводская лаборатория, которая располагает металлографической, химической спектральной, рентгеновской лабораториями, лабораторией механических испытаний. Может осуществить любой анализ деталей как разрушающими, так неразрушающими методами и дать заключение о годности деталей или исследовать причину их поломки.
ОГМех – отдел главного механика. Ведет вопросы эксплуатации и ремонта оборудования. Проектирует внутреннее подъемно-транспортное оборудование, комплектует запчастями технологическое оборудование.
ОГЭ – отдел главного энергетика. Занимается эксплуатацией и ремонтом энергетических установок, электрических и газовых печей, решает вопросы энерго- и теплоснабжения завода, комплектующих для ремонта оборудования.
НИЦ – научно-исследовательский центр. Занимается разработкой новых перспективных технологических процессов, материалов, помогает производству оперативно разрешать вопросы, возникающие в процессе изготовления деталей, нарушения или отклонения от технологических процессов. В состав НИЦ входят проблемные лаборатории: технологическая, металловедения и термообработки, токов высокой частоты, давления, литейная, сварочная.
ТТО – транспортно-технологический отдел. Занимается организацией внутрицеховых и внешних перевозок продукции. Разрабатывает технологические процессы на перевозки, комплектует тарой.
ООТ и ТБ – отдел охраны труда и техники безопасности. Занимается вопросами охраны труда и техники безопасности на заводе. Комплектует спецодеждой и средствами индивидуальной защиты всех работающих. Обеспечивает контроль за выполнением инструкций по ТБ, безопасностью движения.
Дата добавления: 2019-03-09; просмотров: 373; Мы поможем в написании вашей работы! |
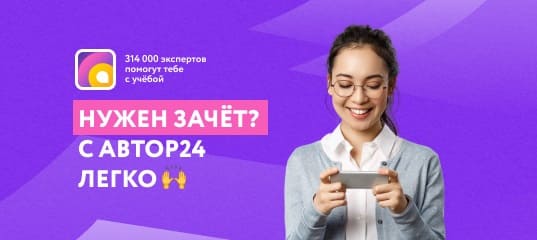
Мы поможем в написании ваших работ!