Фильтровентиляционная установка очистки воздуха
Установка предназначена это картриджные фильтровентиляционные установки с системой автоматической пневмоочистки, предназначенные для очистки воздуха от мелко- и средне дисперсной сухой пыли и дыма при процессах, сопровождаемых выделением вредных частиц размером более 1 мкм. Принцип работы: удаленный установкой, загрязненный воздух посредством имеющейся системы фильтрации очищается от пыли и других мелкодисперсных частиц, после чего очищенный от пыли воздух подается обратно в помещение, либо при наличии
газовой составляющей выводится в атмосферу. Компоненты фильтрации: цилиндрические картриджные фильтры (материал: полиэстер или полиэстер с PTFe покрытием, с классом очистки F9 (99,8%), обеспечивающие высокую износостойкость и химическую инертность по отношению к агрессивным газам и абразивной пыли. Установки оборудованы системой автоматической пневматической самоочистки фильтров. Общая схема показана на рис. 5.1.
1 - завихритель; 2 - тангенциальные щели; 3 - слой жидкости; 4 - центральное отверстие
Рисунок 5.1 – Фильтровентиляционная установка очистки воздуха
Очистка промышленных сточных вод
Очистка методом электрофлотации:
Схема флотационной установки показана на рис. 5.2.
Флотация – это метод очистки воды, основанный на прилипании взвешенных в ней примесей к пузырькам воздуха и всплывании их на поверхность. В флотационной установке с рециркуляцией загрязненная сточная вода сначала поступает в гидроциклон, где удаляется часть взвешенных частиц. Затем ее направляют в первую камеру, где смешивают с циркуляционной водой, насыщенной воздухом. Воздух выделяется в камере и флотирует загрязнение. Далее сточная вода поступает во вторую, а затем в третью камеры, в которых также происходит процесс флотации. После третьей камеры очищенную воду удаляют из установки. Часть циркулирующей воды насосом подают в напорную емкость, где растворяется воздух. Пену удаляют пеносъемниками. Кроме того, при флотации происходит аэрация сточных вод, снижение кон-центрации поверхностно-активных веществ и многочисленных микроорганизмов. Достоинствами флотации являются: высокая степень очистки (до 95 процентов), большая скорость процесса, простая аппаратура.
|
|
1 - емкость; 2 - насос; 3 – флотационная камера; 4 – гидроциклон; 5 - пеносъемник; 6 – напорный бак; 7 – аэратор
Рисунок 5.2 – Схема флотационной установки с рециркуляцией
Установка для обезвреживания паров растворителя
Выбросы сильно загрязняют воздух на территории предприятий и близлежащих территориях, на которых могут располагаться жилые кварталы, поселки и т.д.
|
|
На всех стадиях формирования защитно-декоративных покрытий образуется большое количество газов, загрязненных парами растворителей и другими летучими продуктами, которые при выбрасывании отработанного воздуха в атмосферу загрязняют воздушный бассейн.
Воздух от загрязнений очищают гидромеханическим, адсорбционным, абсорбционным, ионообменным и окислительным методами, сжиганием и др.
В качестве сорбентов используют любые мелкодисперсные вещества (зола, торф, опилки, шлаки и др.).
1 – вентилятор; 2 – абсорбер; 3 – массообменная решётка; 4 – биореактор; 5 – насос; А – абсорбент; В – вентиляционный воздух; АД – абсорбционные добавки; БД – биогенные добавки; СВ – сжатый воздух.
Рисунок 5.2 - Абсорбционно-биохимическая установка очистки воздуха
АБХУ рекомендуется использовать при применении в различных отраслях промышленности следующих технологических процессов, сопровождающихся токсичными газовыделениями в окружающую среду.
Вентиляционный воздух, удаляемый от технологического оборудования, с помощью вентилятора 1 подается в абсорбер 2, где на массообменной решетке расположен слой насадки 3. Насадка непрерывно орошается абсорбентом, подаваемым насосом 5 и находится в «кипящем» состоянии, что обеспечивает интенсивный массообмен между газовой и жидкой фазами. В качестве абсорбента применяется техническая вода. Регенерация абсорбента осуществляется в биореакторе 4, где с помощью специально селекционированного штамма микроорганизмов вредные органические вещества минерализуются до СО2 и Н2О. Для обеспечения активной жизнедеятельности микроорганизмов, за счет добавления в биореактор биогенных добавок, в растворе поддерживается концентрация азота и фосфора. Очищенный абсорбент вновь подается на орошение в абсорбер. Установка имеет замкнутый цикл циркуляции абсорбента и не имеет стоков в канализацию. Очищенный вентиляционный воздух после сепарации выбрасывается в атмосферу.
|
|
Расходные материалы: техническая вода для компенсации потери раствора при испарении – 400 л/сут; биогенные добавки 20-40 кг/год.
Расчет вредных выбросов
В работе выявляем и количественно оцениваем источники, вещества и факторы вредного воздействия на окружающую среду. Оценка выбросов и стоков может быть сделана на основе справочно-информационных материалов, расчетов, прогноза или данных предприятий. Выявленные характеристики факторов вредного воздействия на окружающую среду сопоставляют с действующими нормативами.
|
|
В качестве такого расчета определяют кратность общего воздухообмена в цехе при условиях, что выделение летучих компонентов производится в рабочие зоны, с учетом сокращения концентрации паров растворителя до требуемого уровня.
Количество воздуха, удаляемого из помещения, рассчитывается по формуле:
(5.1)
где а1–а n – часовой расход летучих компонентов ЛКМ, кг/ч;
λ1–λ n – предел допустимой концентрации (ПДК) i-го компонента, входящего в состав летучей части ЛКМ, мг/м3;
К – коэффициент, зависящий от количества выделяемых паров растворителей, равный 0,7.
Количество летучих веществ, образующихся при нанесении одного из используемых в технологическом процессе j-го ЛKM, в зависимости от способа нанесения вычисляют по следующей формуле:
(5.2)
где Gj – часовой расход j-го ЛКМ на комплект, кг/ч;
S – сухой остаток данного материала.
Тогда количество выделяемых летучих веществ по компонентам определяют по формуле:
(5.3)
где Gj – часовой расход j-го ЛКМ на комплект, кг/ч; qk– массовая составляющая k-го компонента летучей части j-го JIKM.
В свою очередь часовой расход j-го ЛКМ находят из уравнения:
(5.4)
где Пч – часовая производительность оборудования, на котором происходит нанесение j-го ЛКМ, комплект/ч (принимается из расчета производительности оборудования);
З – коэффициент загрузки оборудования;
Н j – норма расхода j-го материала на комплект, нанесенного данным способом, кг (принимается из расчета норм расхода материалов).
Кратность воздухообмена в цехе, необходимого для безопасной работы, рассчитывают по следующему выражению:
К= Q / V зд , (5.5)
где Q – количество воздуха, удаляемого из помещения, м3;
V зд – объем помещения производственного цеха, м3.
Так как в цеху используются безвредные ЛКМ, в расчете кратности воздухообмена нет необходимости.
Заключение
В курсовом проекте был разработан технологический процесс отделки столов компьютерных «Президент» с годовой программой выпуска 47000 комплектов. Был произведен анализ изделия, выбраны методы нанесения материалов, методы сушки покрытий, выбрано оборудование, произведен расчет необходимых основных и вспомогательных отделочных материалов, разработана планировка цеха.
В создании защитно-декоративных покрытий применяются основные материалы-лак Aquidol D1900, грунт Aquidol G1136, краситель Aquaphen G1800, а также вспомогательные – марля, шлифовальная шкурка и другие.
Расход лака для отделки одного изделия составит 0,5994 кг, соответствующие значения для грунтовки и красителя составят 0,6743 и 0,8891 кг соответственно. В процессе отделки используется высокопроизводительное оборудование. Благодаря грамотно построенному технологическому процессу оборудование выстроено в линию в соответствующей очерёдности, что позволяет избежать загромождения на рабочих местах и «петель» в процессе обработки. Производительность головного оборудования линии крашения и грунтования составит 99%, и линии нанесения лака 100%.
В курсовой работе освещены мероприятия по охране труда и защите окружающей среды.
Сводная ведомость расчета основных и вспомогательных материалов на годовую производственную мощность (47000 комплектов) выпуска продукции
Используемый материал | Расход материала на изделие | Расход материала на годовую программу |
Водный акриловый краситель Aquaphen G1800 | 0,5994 кг | 28171,8 кг |
Водный грунт Aquidol G1136 | 0,6743 кг | 31692,1 кг |
Водоразбавляемый лак Aquidol D1900 | 0,8891 кг | 41787,7 кг |
Шлифовальная шкурка №5 | 0,0824 м2 | 3872,8 м2 |
Шлифовальная шкурка №М50 | 0,1264 м2 | 5940,8 м2 |
Марля для фильтрования рабочих растворов ЛКМ | 0,0239 м2 | 1123,3 м2 |
Вода | - | 28171,8 кг |
Дата добавления: 2019-02-22; просмотров: 327; Мы поможем в написании вашей работы! |
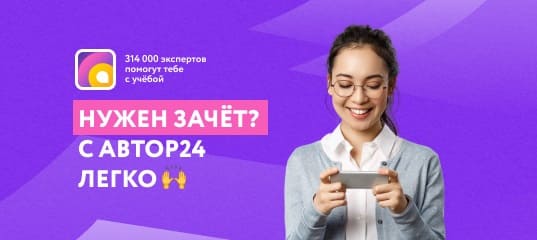
Мы поможем в написании ваших работ!