Технологическая схема установки депарафинизации масел с применением кетоно-толуольной смеси
Технологическая схема первого и второго отделений депарафинизации рафината селективной очистки дистиллятной масляной
В отделении кристаллизации и фильтрования (рис. 1, а) сырье насосом 1 через подогреватель 2 и водяной холодильник 3 подается в регенеративный кристаллизатор 4, где охлаждается раствором депарафинированного масла. Затем сырье смешивается с охлажденным влажным растворителем и циркулирующим фильтратом и поступает в кристаллизатор 5, где охлаждается .жидким аммиаком, после чего снова смешивается с порцией охлажденного влажного растворителя, а также с порцией охлажденного сухого растворителя. Кристаллы твердых углеводородов выпадают из раствора. Суспензия кристаллов твердых углеводородов в растворе масла направляется в питательную емкость I ступени фильтрования 6, откуда перетекает в барабанный фильтр I ступени 7.
В фильтре 7 твердые углеводороды осаждаются в виде лепешки на барабане фильтра, а фильтрат просачивается внутрь барабана и собирается в емкости депарафинированного масла 17. Раствор депарафината через кристаллизаторы 4, 12 и теплообменники 10, 11, 15, где нагревается за счет охлаждения сырья, сухого растворителя и влажного растворителя, направляется в отделение регенерации растворителя. Лепешка гача на барабане фильтра 7 промывается от увлеченного масла порцией сухого растворителя, и фильтрат собирается в емкости некондиционного депарафинированного масла 20.
|
|
Срезанный ножом с барабана гач шнеком продавливается в емкость 18, куда также поступает порция сухого растворителя для разбавления гача. Из емкости 18 раствор гача насосом 19 переводится в питательную емкость фильтра II ступени 8, откуда перетекает в фильтр II ступени 9. Твердые углеводороды остаются в виде лепешки на барабане фильтра 9, а фильтрат — некондиционный депарафинат — собирается в емкости 20. Лепешка так же, как в фильтре I ступени, промывается порцией сухого растворителя. Некондиционное депарафинированное масло насосом 21 добавляется к сырью перед кристаллизатором 5. Гач удаляется из фильтра II ступени точно так же, как из фильтра I ступени. Раствор гача собирается в емкости 23, из которой насосом 22 направляется через кристаллизатор 14 в отделение регенерации растворителя. В гаче содержатся кристаллы льда, попавшие в него из влажного растворителя.
В отделении регенерации растворителя (рис. 1, б) отгон растворителя от депарафинированного масла осуществляется в четыре ступени. Раствор депарафинированного масла нагревается в теплообменниках 18—20 и пароподогревателе 22 и поступает последовательно в колонны 4, 24, 7 и 28. В низ колонны 28 подается водяной пар. Депарафинированное масло с низа колонны 28 через теплообменник 19 и холодильник 1 отводится с установки. С верха колонн 4, 24, и 7 уходят пары сухого растворителя, конденсируются, охлаждаются и поступают в емкость сухого растворителя 3, откуда насосом 2 сухой растворитель возвращается в отделение кристаллизации.
|
|
Отгон растворителя от гача также происходит в четыре ступени, в колоннах 11, 36,13 и 41.С верха колонн 11, 36 и 13 уходят пары влажного растворителя, конденсируются и охлаждаются. Влажный растворитель собирается в емкости 9, откуда насосом 8 возвращается в отделение кристаллизации.
С верха колонн 28 и 41 уходят пары растворителя и водяной пар. После охлаждения и конденсации растворитель и вода поступают в емкость 43, где происходит расслоение жидкости. Верхний слой — влажный растворитель — насосом 14 перекачивается в емкость 9. Нижний слой, содержащий 15 % метилэтилкетоца, подается насосом 44 в кетоновую колонну 16, с низа которой отводится в канализацию вода, а с верха азеотропная смесь метилэтил-кетона и воды через конденсатор 15 поступает обратно в емкость 43.
Для просушки (отдувки) лепешки от растворителя в фильтрах, а также для создания подушки в емкостях с растворителем применяется инертный газ.
|
|
В холодильном отделении осуществляется охлаждение сырья, растворителя и инертного газа на холодильной установке со схемой непосредственного испарения хладагента (аммиака, пропана, этана) в кристаллизаторах при -35 и -43 °С.
а — Отделение кристаллизации:
1, 16, 19, 21, 22 — насосы; 2 — пароподогреватель; 3 — холодильник; 4, 5, 12—14-—кристаллизаторы; 6, 8, 17, 18, 20, 23 — емкости; 7, 9 — фильтры; 10, 11, 15 — теплообменники;
б — Отделение регенерации растворителя:
1, 5, 10, 15, 18, 21, 27, 31, 34, 40 — холодильники; 2, 8, 14, 23, 25, 37, 38, 44 — насосы; 3, 9, 43 — емкости; 4, 7, 11. 13, 16, 24, 28, 36, 41 — колонны; 6, 12, 22, 26, 29, 35, 39, 42 — пароподогреватели; 17—20, 30, 32, 33 — теплообменники;
I — сырье; II — влажный растворитель; III — cyxoй растворитель; IV — раствор депарафинированного масла; V — раствор гача; VI — аммиак; VII — депарафинированное масло; VIII — гач; IX — вода; X — водяной пар.
Технологическая схема установки депарафинизации масел с применением кетоно-толуольной смеси
Дата добавления: 2019-02-26; просмотров: 839; Мы поможем в написании вашей работы! |
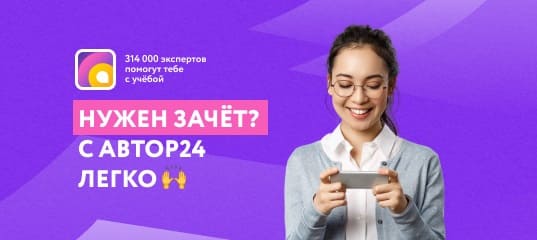
Мы поможем в написании ваших работ!