Выбор, разработка структуры и рецептуры материала
Первая стадия проектирования КМ в начале своего выполнения подразумевает ориентировочный выбор метода получения композита без конкретизации технологических параметров. В первую очередь ориентировочно выбирают способ формообразования композита. Его легко определить, так как каждый способ ограничен в своих возможностях формой, размерами, точностью (допусками) и качеством получаемой поверхности. Кроме того, действующий технологический критерий сужает область выбора компонентов композита, особенно матрицы, по пластическим свойствам. Происходит назначение температурного интервала формообразования. Поскольку каждому виду формообразования присуща своя специфика анизотропии свойств, например ориентации волокон, осуществляется выбор структуры композита. Для всех вариантов задания способом формования стержня является горячее экструдирование. Энергетические затраты при экструзии КМ с металлической матрицей в 1,5 • 1,7 раза больше, чем у КМ с полимерной матрицей и составляет 2 МДж/кг.
Выбор матричного материала КМ
Здесь конструкционные требования создают ограничения, которые рассматриваются в последовательности;
ограничения по плотности изделия (веса конструкции);
ограничения по удельным прочностным и упругим характеристикам;
ограничения по прочности, жесткости и долговечности;
ограничения по поверхностным свойствам изделия;
|
|
ограничения по времени эксплуатации изделия;
ограничения по рабочей температуре изделия;
ограничения по стоимости.
Расчетным образом определяют материал матрицы и альтернативные варианты, проводят первую конкретизацию способа получения изделия и ориентировочный экономический расчет. Выбирают наиболее приемлемые варианты материала матрицы и технологий. В настоящее время специалисты материаловеды и конструкторы КМ при поиске материалов используют справочные информационные системы ЭВМ и INTERNET. В настоящей работе используются данные приведенные в справочных таблицах. Алгоритм поиска, приведенный выше, может быть дополнен другими ограничениями. В ходе выбора матричного материала возможны два случая:
1. известные материалы без армирования не отвечают конструкционным критериям. Здесь происходит переход к композиту;
2. известные материалы для матриц удовлетворяют требованиям и
конструкционной и технологической возможности. В данном случае
проектирование КМ не прерывают, а рассматривают варианты менее прочных
(жестких) и более дешевых матричных материалов. Например, если была выбрана матрица из пластической массы, то появляется возможность ввести наполнители (мел, бумажные отходы и т.п.), что сказывается положительно на себестоимости изделия. Применение дешевых армирующих элементов (стальной проволоки, стеклянных нитей, волокон и тканей) в композите – аналоге матричного материала в данном случае достаточное условие для выполнения требований по конструкторским и технологическим ограничениям.
|
|
ПРИМЕР
При выборе матричного материала КМ по такому параметру, как плотность учитывают аддитивное правило:
где gкм, gm и gf- плотности КМ, волокна и матрицы, Vf- объемная доля волокна. Можно выбрать тяжелую матрицу и легкие волокна, можно - наоборот и получить требуемый композит.
Выбираем из табл. 1 два наиболее близких по плотности материала:
Фторопласт Ф g =2150 кг/м3 и алюминиевый сплав АК - 4 g= 2750 кг/м3. Энергетические затраты на изготовление примерно одинаковы. Рабочая температура Ф составляет 560 К, а АК-4 600 К, что близко к значениям ТЗ.
Рассчитываем их удельную прочность, подставляя численные значения получаем: sАК-4 = 0,177 МДж/кг; sФ= 0,016 МДж/кг. Расчетная удельная прочность выбранных материалов ниже требуемого значения. Возникает необходимость в армировании матрицы.
Таблица 1
Свойства матричных компонентов композиционных материалов
|
|
Материал | Плотность, gкг/м3 | Прочность, sв МПа | Рабочая температура Т, 0С | Удельные энергети- ческие затраты на изготовление мате- риала, кДж/кг |
АД-1 | 2700 | 410 | 660 | 180 |
АК-4 | 2650 | 430 | 600 | 200 |
АЛ-1 | 2750 | 470 | 560 | 210 |
В-95 | 2800 | 600 | 470 | 300 |
ПТЭ-1 (Ti) | 4700 | 1650 | 500 | 250 |
Бериллий | 1300 | 1360 | 500 | 240 |
НП-2 (Ni) | 8900 | 450 | 1100 | 540 |
ХН70Ю | 7800 | 750 | 1400 | 600 |
Полистирол | 950 | 40 | 300 | 160 |
ЭД-10 | 1160 | 35 | 370 | 180 |
Фенилон | 1350 | 120 | 400 | 200 |
Полиэтилен | 1050 | 35 | 320 | 220 |
Фторопласт Ф | 2150 | 35 | 560 | 120 |
СП90-3 (Fe-C) | 7800 | 700 | 400 | 300 |
Дата добавления: 2019-02-26; просмотров: 208; Мы поможем в написании вашей работы! |
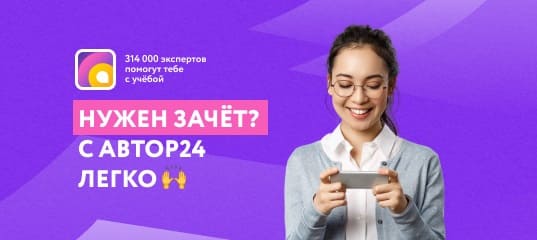
Мы поможем в написании ваших работ!