СИСТЕМЫ ДИАГНОСТИКИ, КОНТРОЛЯ И УЧЁТА РАБОТЫ ЭКСКАВАТОРА
Системы диагностики обеспечивают сокращение времени поиска и устранения неисправностей, а также своевременные отключения неисправных элементов, что препятствует возникновению и развитию аварий. Это уменьшает экономические потери от простоя и процедуры ремонта или замены узла.
Системы диагностики на основе современных управляющих ЭВМ решают следующие задачи:
– оценка технического состояния определяющих параметров электрооборудования, на основании которых устанавливается факт правильной и неправильной работы электрических машин, тиристорных преобразователей, систем управления, релейно-контакторной аппаратуры;
– формирование и вывод на пульт оператора сигналов о различных повреждениях;
– формирование диагностических сигналов и выдача визуальной информации, необходимой для локализации места отказа электрооборудования с точностью до заменяемого (или ремонтируемого на месте) элемента.
Система диагностики включает в себя контроль за текущими параметрами механизмов, электрооборудования, электроснабжения и режимов эксплуатации.
Объектами контроля являются:
– ответственные узлы механизмов (подшипники, редукторы, канаты, стрелы и пр.);
– основные элементы электропривода (тиристоры, блоки управления, регуляторы, обратные связи и пр.);
– крупные электрические машины (состояние щёточно-коллекторного аппарата, нагрев обмоток и подшипников);
|
|
– напряжение питания, замыкание на землю, гармоническиё состав, коэффициент мощности, превышение допустимого тока, включая короткое замыкание;
– недопустимые режимы эксплуатации (самоход, стопорение, превышение пройденного пути над заданным и пр.).
Система управления карьерным экскаватором включает в себя также систему автоматического контроля и учёта работы экскаватора с передачей информации на диспетчерский пункт.
Системы контроля и учёта работы экскаватора. Контроль и учёт работы способствует улучшению использования оборудования, позволяет сократить простои, уменьшить время необходимое для оценки фактического состояния оборудования, использования ресурсов механизмов, расхода запасных частей и т.п.
В системах реализуются следующие функции:
– получение информации об объёмах выполненных работ и их длительности;
– формирование информации, характеризующей использование экскаватора во времени;
– формирование информации, характеризующей объём (вес) переработанной горной массы;
– формирование информации, характеризующей энергозатраты на произведённую работу;
– формирование внутрисменной и итоговой информации по результатам смены.
|
|
Системы контроля и учёта, как правило, выдают следующую информацию:
– общий расход электроэнергии;
– усилие в механизме подъёма (по току якорной цепи двигателя механизма подъёма);
– усилие в механизме напора или тяги (по току якорной цепи двигателя механизма напора-тяги);
– угол поворота платформы;
– время рабочего цикла;
– сигнализация о наполнении ковша;
– время поворота;
– энергопотребление за цикл экскавации;
– общее количество перемещённой горной массы;
– общее количество рабочих циклов за смену, сутки, месяц.
Информация о работе экскаватора и неисправностях поступает на пульты и панели, расположенные в кабине машиниста. По вызову машиниста экскаватора на информационных панелях инициируется большое количество данных (количество циклов, выполненных с начала смены, вес переработанной горной массы, время поворота, длительность цикла, расход электроэнергии и т.д.).
АВТОМАТИЧЕСКОЕ УПРАВЛЕНИЕ ТЕХНОЛОГИЧЕСКИМИ ПРОЦЕССАМИ
Системы автоматизации экскаваторов решают две основные задачи: автоматическое управление режимом работы электроприводов и автоматическое управление технологическими процессами.
Первая задача решается вполне успешно: автоматическое управление электроприводами обеспечивает заданную производительность и требования эксплуатации. Применение управляющих ЭВМ дополнительно улучшает эти характеристики в части их стабильности и точности, независимых от внешних условий.
|
|
Вторая задача в отечественной практике не вышла за пределы опытно-экспериментальной стадии.
В 80-90 годы в СССР были разработаны алгоритмы, изготовлены и испытаны опытные образцы некоторых локальных систем автоматизации.
Локальные системы автоматического управления технологическими процессами эскаватора - прямой лопаты должны решать следующие задачи: координация работы электроприводов подъёма и напора в процессе копания; требуемое перемещение поворотной платформы при выполнении транспортных операций.
Локальные системы автоматического управления технологическими процессами драглайна должны решать следующие задачи: координация работы электроприводов подъёма и тяги в процессе копания; выбор слабины подъёмного каната; координация работы электроприводов поворота, подъёма и тяги при выполнении транспортных операций; исключение колебаний ковша и его стабилизация в вертикальной плоскости, проходящей через стрелу, в периоды разгрузки и посадки порожнего ковша в точку начала копания.
|
|
Система управления драглайном должна включать систему автоматического контроля и защиты ковша драглайна, которая исключает саморазгрузку, растяжку, переподъём, задевание за отвал, удары о кромку забоя.
Ниже приведены примеры локальных систем автоматического управления.
Автоматизация процесса копания для карьерного экскаватора. При копании ковш должен заполняться за минимальное время и при наименьшем удельном расходе электроэнергии. Управление процессом копания связано с регулированием толщины стружки. Если толщина стружки велика, то процесс протекает при пониженной скорости, увеличивается длительность копания, возможна перегрузка электроприводов. При недостаточной толщине стружки снижается производительность. Максимально возможная производительность и лучшие энергетические показатели в процессе копания могут быть достигнуты только при правильном сочетании напорного и подъёмного движений, обеспечивающих оптимальную толщину стружки и максимальное использование мощности подъёмного двигателя. Такое сочетание возможно лишь при автоматическом регулировании процесса копания.
Наименьшая длительность процесса черпания достигается при работе электропривода подъёма вблизи точки отсечки механической характеристики. Поэтому система автоматического управления процессом копания осуществляет координацию работы напорного и подъёмного механизмов таким образом, чтобы выполнить это условие для любой, заданной машинистом скорости привода подъёма.
Защита драглайна от аварийных режимов растяжки, переподъёма и перетяги. Защита от аварийных режимов растяжки, переподъёма и перетяги осуществляется в функции длин подъёмного и тягового канатов. Длины канатов определяются с помощью датчиков перемещений, установленных на валах соответствующих барабанов. В качестве уставки срабатывания защиты от переподъёма и перетяги приняты минимальные длины подъёмного и тягового канатов. Уставка защиты от растяжки представляет собой постоянное значение функции этих длин, аппроксимирующее граниицы аварийной зоны растяжки.
Ограничение раскачивания ковша драглайна при повороте платформы. Алгоритм управления приводом поворота заключается в формировании дополнительного сигнала в функции выходного напряжения регулятора напряжения с помощью динамического звена. Дополнительный сигнал поступает на вход регулятора тока, где он вычитается из выходного напряжения регулятора напряжения. Это позволяет снизить максимальную скорость отклонения ковша, ограничивая при этом его колебания.
Дата добавления: 2019-02-22; просмотров: 516; Мы поможем в написании вашей работы! |
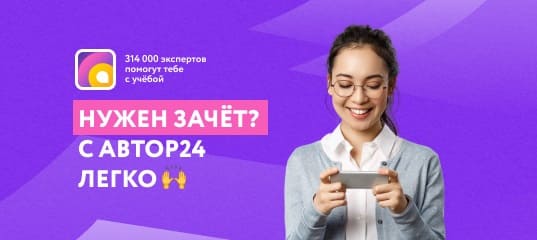
Мы поможем в написании ваших работ!