Микроскопические и фрактографические исследования.
МИНОБРНАУКИ РОССИИ федеральное государственное бюджетное образовательное учреждение высшего образования «Самарский государственный технический университет» (ФГБОУ ВО «СамГТУ»)
Отчет по производственной практике на тему
Микроскопические и фрактографические исследования образцов трубопровода».
Подготовил: студент гр.17БМ Хегай С.М.
Проверил: к.п.н, доцент Богдасарова Ю.А.
2019
Содержание
1. Введение………………………………………………………………………...стр.3
2. Данные электронной микроскопии и фрактографии………………...…..стр.4
3. Микроскопические и фрактографические исследования………………..стр.5
4. Список литературы…………………………………………………………..стр.22
Введение
Для исследования причин появления дефектов и сравнения методов неразрушающего контроля (НК) при исследовании ТВЧ – швов, были вырезаны 2 фрагмента аварийного газопровода.
Длина фрагментов (по осевой образующей трубы) 570 и 600 мм.. Дата ввода в эксплуатацию 1994 год. Условия эксплуатации: рабочее давление 75 кгс/см2; наружный диаметр 219 мм; толщина стенки 7 мм; рабочая среда – природный газ; глубина залегания – 1 м при глубине промерзания грунта 1,4 м.
Фрактографический и микроскопический анализ поверхности трещин в образцах проводили в СГАУ на растровом электронном микроскопе TESCAN с программным обеспечением VEGA при увеличениях до 4 тыс. крат.
|
|
Общий вид сканирующего электронного микроскопа TЕSCAN VEGA SBH Easy Probe показан на Рисунке.
Данные электронной микроскопии и фрактографии.
Для микроскопических и фрактографических исследований из фрагмента № 1 и фрагмента № 2, методом плазменной резки были вырезаны части, содержащие продольный и кольцевой сварные швы и дефекты в них (Рис. 1)
а б
а – вырезка из фрагмента №1; б – вырезка из фрагмента №2;
Рисунок 1 - Вырезки из фрагментов аварийного газопровода
В продольном шве фрагмента №1 имеется трещиноподобный объмено-плоскостной дефект. В кольцевом шве фрагмента №2 присутствует почти сплошная сеть трещин различной длины, глубины и степени раскрытия.
Далее были приготовлены образцы для микроскопических исследований сварного шва и зоны термического влияния. Здесь и в дальнейшем за зону термического влияния условно принимали участок поверхности образца, расположенный на границе сварного шва с основой шириной 1 мм.
Интересующие дефекты были выделены из вырезок механическим способом. При этом учитывалось направление ориентировки дефекта. Ширина образцов 30 мм, длинна от 25 до 45 мм.
|
|
Образцы пронумерованы с 1 до 5.
Образцы 1 – 4 относятся к кольцевому шву фрагмента № 2;
образец 5 – вырезан из продольного шва фрагмента №1.
Фотографии образцов представлены на Рис. 2
Рисунок 2 - Образцы для микроскопичекиских исследований (1-5)
После изготовления образцы были очищены от следов пенетранта, проявителя, краски и загрязнений, при помощи очистителя фирмы MAGNAFLUX, входящего в состав комплекта КК.
Характер разрушения был изучен на данных образцах при помощи электронной микроскопии и металлографического анализа.
Далее дефекты в образцах были последовательно исследованы в растровом электронном микроскопе.
Микроскопические и фрактографические исследования.
Все образцы содержат сеть продольных трещин в кольцевом сварном шве по всей его длине, например таких как трещины в образце №1, протяженностью до 8 мм и раскрытием до 0,5 мм. Вид трещин в образце, с увеличением в 20 – 30 раз представлен на Рис. 3
Рисунок 3 - Трещины в образце 1.
При более детальном рассмотрение участка растрескивания, содержащего несколько трещин, были обнаружены развивающиеся трещины в сварном шве. На Рис. 4 а представлено изображения зоны развития трещин (6 трещин: 4 в противолежащих непрерывных цепочках, соединенных линиями сброса; 1 между цепочками трещин; одна в стороне от цепочки).
|
|
То, что трещины развивались во времени, подтверждается при более детальном рассмотрении устья нескольких из них. На Рис. 4 б представлена зона устья двух трещин увеличено (видно, как распространяется разрушение в двух нижних трещинах; как образуются линии сброса, направленные от устья верхней трещины к нижним).
а б
а – общий вид участка растрескивания; б – Зона начала разрушения. Рисунок Рис. 4 - Участок растрескивания в образце 1.
Расположение, ориентация, и формы трещин позволяют предположить, что характер разрушения усталостный. В зоне зарождения трещины зигзагообразные, а также имеют многочисленные вторичные трещины, перпендикулярные поверхности разрушения.
В месте образования линии сброса (микротрещины м/у трещинами большого раскрытия) видно, как разрушение находится в первой стадии усталостного разрушения: образование усталостных линий и растрескивание окислов, покрывающих поверхность металла.
Наличие первой стадии усталостного разрушения свидетельствует о низком значении амплитуды усталостных напряжений
|
|
Внутренние и внешние поверхности устья трещины покрыты окислами, что видно на увеличенном снимке. (Рис. 5 б)
а б
а – зона образование линии сброса; б – оксиды на внутренней и внешней поверхности;
Рисунок 5 - Окисленные поверхности трещин образца 1.
Считается, что усталостный излом обычно образуется после 1 – 5 млн. циклов нагружения, что вполне возможно при длительной эксплуатации трубы фрагмента № 2 – 17 лет;
Наличие сети трещин различной длинны, их вид; наличие оксидов даже непосредственно в устье трещин; а также известные срок и характер эксплуатации трубы позволяют сделать вывод о том, что растрескивание носит длительный усталостный характер. Предположительно разрушение началось с образования отдельных трещин возле внутренних концентраторов напряжений, и развивалось в течении долгого времени.
Это подтвердилось обнаружением неметаллических включений, расположенные непосредственно в зоне распространения трещины. На рис. 6 они пронумерованы с 1 до 5.
Рисунок 6 - Неметаллические включения в зоне распространения трещины.
Образование включений имеет металлургический характер, о чем свидетельствует глобулярная форма включения №1, изображение которого представлено на рисунке А (если бы это было включение, попавшее внутрь трещины механическим путем – то форма была бы неправильной, оскольчатой).
Спектральный анализ включения показал большое содержание во включении кремния (Рис. 7 б), предположительно, введенного в расплав для раскисления при выплавке стали, и выделившегося из металла в зоне, прилагающей к сварному шву в процессе сварки.
а б
Рисунок 7 - Силикатное неметаллическое включение
а – Вид и размеры включения; б – данные спектрального анализа включения;
Элемент | Весовой % | Атомный % |
C | 4,57 | 7,32 |
O | 53,76 | 64,58 |
Si | 40,46 | 27,69 |
Mn | 0,18 | 0,06 |
Fe | 1,02 | 0,35 |
Итого 100.00 |
Рисунок 8 - Содержание различных химических элементов в неметаллическом включении.
Исследования показали, что включения 2 – 5 являются очагами растрескивания. По своей форме включения похожи на сульфиды. На Рис. 9 а, видно, как от включения в разные направления расходятся микротрещины.
Повышенное содержание серы подтвердил спектральный анализ (Рис. 9 б), и состаренный на его основе химический анализ Рис. 10.
а б
Рисунок 9 - Сульфидное неметаллическое включение
а – Вид и размеры включения; б – данные спектрального анализа включения;
Элемент | Весовой % | Атомный % |
C | 11,04 | 23,84 |
O | 29,61 | 47,99 |
Si | 0,74 | 0,68 |
S | 0,80 | 0,65 |
Mn | 0,32 | 0,15 |
Fe | 57,49 | 26,69 |
Итого 100.00 |
Рисунок 10 - Содержание различных химических элементов в неметаллическом включении.
Найденные вблизи сварного соединения неметаллические включения (в первую очередь сульфидные), могут стать концентраторами усталостных напряжений и являться очагами растрескивания металла.
Образец 2, также, как и образец 1 содержал сеть трещин в сварном соединении, длинной до 2 мм и раскрытием до 0,5 мм. (Рис. 11)
Рисунок 11 - Общий вид трещины в образце 2.
Трещины имеют ориентировку вдоль сварного соединения, аналогичную трещинам в образце 1 (представляют цепочку локальных трещин, вытянутых вдоль шва, в некоторых местах соединенных микротрещинами линии сброса).
И в 1 и во 2 образце дефекты имеют характерную для картины усталостного разрушения тонкостенных труб ориентировку. Развитие трещин вдоль волокон метала показано на Рис. 12.
Рисунок 12 - Трещины вдоль волокон металла в 1 и 2 образцах.
При исследовании устья одной из трещин в образце 2, также как и в образце 1, была выявлена группа неметаллических включений. (Рис. 13 а). Спектральный анализ показал, что эти включения представляют собой сложные оксиды Fe, Si, Al. (Рис. 13 б ). Хим. состав включения Рис. 14.
а б
Рисунок 13 - Сложных неметаллических включений
а – Вид группы включений; б – данные спектрального анализа включения;
Элемент | Весовой % | Атомный % |
C | 19,12 | 31,67 |
O | 43,06 | 53,55 |
Si | 2,57 | 1,82 |
S | 0,68 | 0,42 |
Mn | 0,22 | 0,08 |
Fe | 33,78 | 12,04 |
Al | 0,57 | 0,42 |
Итого 100.00 |
Рисунок 14. Содержание различных химических элементов в неметаллическом включении.
Характер усталостного разрушения сварного соединения инициированном неметаллическими включениями – концентраторами усталостных напряжений, подтверждается и при исследовании образца 2.
Образец №3 содержит сеть трещин диной до 8мм, и раскрытием до 0,5 мм. Трещины имеют такой же вид и, очевидно, характер образования, как и трещины в образцах 1 и 2.
Образец №4 имеет аналогичную сеть трещин. Диной до 5мм, и раскрытием до 0,5 мм. (Рис. 15)
Рисунок 15 - Общий вид образца №4
Трещины соединены между собой линиями сброса. Образование линии начинается с появления микротрещины, и растрескивания покрывающих поверхность металла окислов. Затем поверхностный слой металла разрывается, трещина начинает раскрываться и уходить вглубь сварного шва, имея направление развития, соответствующее расположению неметаллических включений.
При микроскопическом исследовании образца 4 удалось подробнее рассмотреть механизм образования линий сброса между уже имеющимися трещинами.
Изображение картины пластической деформации поверхности представлено на Рис. 16.
На Рис. 17 представлено изображение одной из линий сброса линий.
Рисунок 16 - Пластическая деформация в зоне растрескивания.
Рисунок 17. Линия сброса между трещинами.
Обобщая результаты микроскопических исследований образцов 1- 4, , с достаточной уверенностью можно утверждать:
-усталостные напряжения в металле, связанные с циклической работой по перекачке среды, накапливаются около концентраторов напряжений.
-пластичность включений меньше, чем пластичность основного металла, поэтому вокруг и внутри включений образуются очаги растрескивания.
-так как пластическим деформациям, при работе, подвергается весь объем металл, а включения распределены по сварному шву, то и зародыши разрушения возникают во многих местах.
-разрушение начинается как усталостное, развивается как вязкое.
-при углублении и расширении, трещины смыкаются по линиям сброса сначала микро, а затем и макро трещинами, образуя магистральную трещину, опоясывающую весь шов.
Разрушение продольного шва проанализировано на примере образца №5.
Образец 5 содержал объемно плоскостной трещиноподобный эксплуатационный дефект продольного сварного шва. Это причина утечки газа. Косвенно подтверждает образование дефекта входе эксплуатации трубы то, что труба прошла приемные гидроиспытания при строительстве газопровода, а после около 17 лет работала в составе его линейной части,.
Общий вид дефекта представлен на рисунке 18.
а б
а – вид с внешней стороны трубы; б – вид с внутренней стороны трубы. Рисунок 18 - Объемно-плоскостной дефект в продольном сварном шве.
Вероятнее всего инициатором образования такого крупного объемно – плоскостного дефекта был заводской брак (непровар в следствии забоины на кромке штрипса или т.п.).
Обнаружена сеть трещин в обоих в устьях дефекта, что говорит о том, что если даже причины появления дефекта технологические, то дальнейшее растрескивание идет по той же схеме что и в образцах 1 – 4. Устья дефекта в образце № 5 представлены на Рис. 19.
Рисунок 19 - Устья трещины в объемно-плоскостном дефекте образца 5.
Для анализа внутреннего строения поверхности разрушения, образцы №1 и № 5 были раскрыты таким образом, чтобы стало возможно исследовать устья трещин перпендикулярно направлению разрушения.
Общий вид раскрытых образцов представлен на Рис. 20.
Рисунок 20 - Сломанные образцы №1 и №5.
Картина разрушения образца 1 подтверждает усталостный характер растрескивания шва. Отчетливо видны усталостные бороздки в приповерхностном слое. (Рис. 21 а, б)
а б
а – Общая картина разрушения; б – Приповерхностный слой увеличено;
Рисунок 21 - Усталостное разрушение сварного шва образца 1.
Также на внутренней поверхности было обнаружено множество различных неметаллических включений. Преимущественно это глобулярные оксиды, сульфиды и силикаты неправильной оскольчатой формы, (Рис. 22, 24,25), на которых зарождались и распространялись вглубь металла трещины, и по которым проходили линии сброса.
Рисунок 22 - Внутренняя поверхность трещины образца 2
а б
Элемент | Весовой % | Атомный % |
O | 37,33 | 63,31 |
Al | 1,11 | 1,11 |
Si | 10,89 | 10,52 |
S | 1,9 | 1,01 |
Mn | 2,07 | 1,02 |
Fe | 47,49 | 23,03 |
Итого 100.00 |
в
а – Вид и размеры включения; б – данные спектрального анализа включения; в - Содержание различных химических элементов в неметаллическом включении.
Рисунок 23 - Силикатное неметаллическое включение
а б
Элемент | Весовой % | Атомный % |
C | 5,61 | 12,76 |
O | 32,88 | 56,20 |
Al | 0,45 | 0,45 |
Si | 1,26 | 1,23 |
S | 0,2 | 0,17 |
Mn | 0,17 | 0,08 |
Fe | 59,44 | 29,11 |
Итого 100.00 |
в
а – Вид и размеры включения; б – данные спектрального анализа включения; в - Содержание различных химических элементов в неметаллическом включении.
Рисунок 24 - Оксидное неметаллическое включение.
а б
Элемент | Весовой % | Атомный % |
C | 8,84 | 19,10 |
O | 26,63 | 46,44 |
Al | 1,55 | 1,49 |
Si | 8,19 | 7,57 |
S | 1,8 | 1,46 |
Mn | 33,21 | 15,69 |
Fe | 17,71 | 8,26 |
Итого 100.00 |
в
а – Вид и размеры включения; б – данные спектрального анализа включения; в - Содержание различных химических элементов в неметаллическом включении.
Рисунок 25 - Сульфидное неметаллическое включение
Разрушение сварного шва в образце № 5, растянуто во времени и имеет вязкий характер. Инициатором его предположительно явился технологический дефект, связанный с непроваром кромок штрипса.
Вероятно, что в процессе эксплуатации, дефект являлся концентратором усталостных напряжений. Деформации вследствие знакопеременных нагрузок и коррозия металла, привели к увеличению размеров дефекта, и к тому, что он стал сквозным. В устье дефекта продолжалось усталостное разрушение. Это подтверждает тот факт, что вблизи устья дефекта обнаружены микротрещины, уходящие в глубь металла, имеющие выход на внутреннюю поверхность образца 5. Вид их представлен на Рис. 26.
Рисунок 26 - Микротрещины на внутренней поверхности дефекта обр№5.
Размеры дефекта позволяют предположить, что очаг его образования изначально был скрыт в металле. Негерметичная труба не прошла бы входной контроль, а газопровод – гидроиспытания. Внутренняя поверхность дефекта в образце 5 заглаженная, окисленная. Это в первую очередь связано, что она подвергалась активному воздействию агрессивной коррозионной среды и является подтверждением того, что дефект образовывался и существовал очень длительное время.
В следствии окисленности поверхности, ни неметаллических включений, ни усталостных бороздок в зоне излома обнаружить не удалось. Общий вид внутренней поверхности объемно – плоскостного дефекта в образце 5 представлен на Рис. 27.
Рисунок 27 - Внутренняя поверхность дефекта образца №5.
Список литературы
1. Бернштейн, М.Л. Механические свойства металлов [Текст] / М.Л. Бернштейн, В.А. Займовский. – М.: Металлургия, 1979. – 495 с.
2. Гуляев А.П. Металловедение [Текст]: Учебник для вузов. 6 – е изд., перераб. и доп./ Гуляев, А.П. – М.: Металлургия, 1986. – 544 с.
3. Важенин, Д. В. Особенности контроля кольцевых сварных соединений газопроводов – отводов, выполненных сваркой токами высокой частоты [Текст]/ Д. В. Важенин, Д. М. Коваль, Е. Ю. Ярусов, Д. В. Жуков // Megatech. – 2010. - №4. С. 20 – 23.
4. Лившиц Л.С. Металловедение для сварщиков[Текст]/ Л.С. Лившиц. – М.: Машиностроение, 1979. – 253 с.
5. ГОСТ 8233-56. Сталь. Эталоны микроструктуры[Текст] – Введ. 1957-07-01 – М.: Изд-во стандартов, 1972. – 43 с.
6. ГОСТ 1778—70 Сталь. металлографические методы определения неметаллических включений[Текст] – Введ. 1972-01-01 – М.: Изд-во стандартов, 1990. – 35 с.
7. РД 24.200.04-90 Швы сварных соединений. Металлографический метод контроля основного металла и сварных соединений химнефтеаппаратуры[Текст ]–Введ. 1991-07-01. - М.: Газпром эксмо, 1999. – 134 с.
Дата добавления: 2019-02-22; просмотров: 710; Мы поможем в написании вашей работы! |
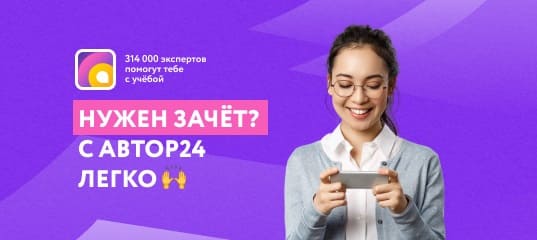
Мы поможем в написании ваших работ!