Оправка и подвялка полуфабриката
После извлечения из форм полуфабрикаты дополнительно обрабатывают (оправляют), зачищая швы, заделывают технологические отверстия и трещины, прорезают монтажные отверстия.
Перед сушкой полуфабрикаты подвяливают в течение 24–48 ч, выдерживая в условиях цеха, после чего отправляют на сушку.
Сушка
Сушку полуфабриката проводят в камерных или туннельных сушилках до влажности 1 %. В данной работе на производстве применяются туннельные сушилки. Продолжительность сушки составляет 20 ч. Для перемещения полуфабриката используют специальные тележки, на которых изделия устанавливают в один или несколько ярусов или конвейеры. Сушка осуществляется конвекцией теплоносителя (подогретого воздуха), нагнетаемого вентиляторами в пространство сушилки. Потоки воздуха распределяют по поперечному и продольному сечениям сушилки, обеспечивая равномерный и постоянный съем влаги с поверхности полуфабриката.
После сушки полуфабрикат очищают от пыли, обдувая сжатым воздухом, смачивают поверхность проблемных мест полуфабриката керосином (керосиновый контроль) и подвергают визуальному осмотру на предмет обнаружения посечек и трещин.
Глазурование
Глазурование СТИ осуществляют способом распыления и полива как вручную, так и с использованием глазуровочных конвейеров и глазуровочных роботов.
Для некоторых изделий способы глазурования комбинируют (полив и распыление), добиваясь равномерного покрытия слоем глазури толщиной до 1 мм лицевых рабочих поверхностей.
|
|
После глазурования полуфабрикаты зачищают и отправляют к печам для обжига, где устанавливают на обжиговые вагонетки. Перед обжигом глазурованные полуфабрикаты выдерживают 6–8 ч для подсушки нанесенного слоя глазури.
Обжиг
Обжиг СТИ проводят в туннельных, реже в камерных, печах. Продолжительность обжига составляет 24 ч. В данной работе на производстве применяется туннельная обжиговая печь. Общая длина печи – 100 м, зона подогрева – 35 м; зона обжига – 24 м; зона охлаждения – 41 м. Ширина печи – 3 м, рабочая высота печи – 2 м. Производительность печи составляет 120 изделий в час. Количество горелок – 18 шт. Рециркуляция продуктов сгорания в момент анализа отсутствует. Масса печной вагонетки mв = 900 кг, масса СТИ 1800 кг/вагонетку.
Для реставрации («лечки») изделий с незначительными дефектами глазурного слоя, обнаруженными после обжига, проводят повторный обжиг в камерных печах. Для реставрации дефектов изделий на проблемные места наносят глазурные препараты или изделия покрывают цветными глазурями со специальными эффектами. В некоторых случаях используют «холодную лечку» устраняя дефекты полимерными составами.
|
|
Сортировка и упаковка изделий
Прошедшие обжиг изделия сортируют, проводят функциональные испытания. Бракованные изделия, не подлежащие реставрации, отправляют в бой для дальнейшей переработки и использования в составе шликера. Годные изделия упаковывают в специальную гофротару, комплектуя необходимой арматурой.
Описание теплоэнергетики и электроэнергетики при производстве фаянсовых изделий
Примерные характеристики энергопотребления при производстве СТИ в Российской Федерации представлены в таблице 2. Ориентировочные показатели удельного энергопотребления приведены с учетом результатов отечественных исследований; оценка объемов выпускаемой продукции проведена на основе доступных материалов маркетинговых исследований.
Таблица 2 – Примерное потребление энергии при производстве СТИ
Годовой выпуск (2013 год) | Удельное энергопотребление, ГДж/т (в среднем) | Суммарное потребление энергии в отрасли, ГДж/год | |
единиц | тонн | ||
13 · 106 | 0,13 · 106 | 22 | 2,9 · 106 |
На рисунке 2 представлена потоковая схема производства СТИ
Рисунок 2 – Входные и выходные потоки производства СТИ (количественная оценка)
|
|
Производительность исследуемого завода по производству СТИ составляет 15000 т/год или 1 млн. изделий в год. Средняя масса одного СТИ составляет 15 кг. Потребление тепловой энергии составляет 18 ГДж/т продукции. Потребление электроэнергии для освещения и привода силового оборудования (дымососы, вентиляторы, насосы, оборудование котельной) составляет 3,32 ГДж/т продукции.
На первом этапе производства СТИ (приготовление шликера и глазури) основным теплоэнергетическим ресурсом является вода, качеству (содержанию в ней растворимых примесей) которой уделяют особое внимание. Для эффективности процесса шликерного литья воду часто подвергают предварительной очистке. Качество воды особо важно при производстве СТИ способом литья под давлением. Соотношение материалов и воды обычно принято 1:1.
На участке формования (литья) обеспечивают стабильные температурно-влажностные условия, во многом определяющие продолжительность каждой стадии формования и качество продукта. В нашем случае формование осуществляется способом высокопроизводительного шликерного литья, которое реализуется на автоматизированных прессах и стендах. На них предварительно подогретый до 40–45 °C шликер подается под давлением 7 бар в пористые полимерные формы.
|
|
Процесс подвялки осуществляется при влажности воздуха 45–55 % и температуре 25–35 °C. В конце подвялки влажность изделий составляет 12–18 %.
Сушка полуфабриката производится при температуре 90 °C до влажности 1 %. Теплоносителем служит горячий воздух, подогреваемый в калориферной установке. Скорость его движения в туннеле составляет 1,4 м/с. Потоки воздуха распределяют по поперечному и продольному сечениям сушилки, обеспечивая равномерный и постоянный съем влаги с поверхности полуфабриката. Производительность сушилки – 120 изделий в час. Удельный расход теплоты составляет 6 МДж/кг испаренной влаги.
Обжиг СТИ производится в туннельной печи производительностью 120 изделий в час при температуре 1200 °C. Удельный расход природного газа составляет 179 м3/т обожженной продукции. Расход природного газа составляет 322 м3/ч. Расход воздуха, идущего на горение природного газа составляет 3369 м3/ч. Расход продуктов сгорания составляет 3744 м3/ч. Теплота сгорания природного газа 33,5 МДж/м3.
Тепловой баланс обжиговой печи:
![]() | (1) |
где = 2996 кВт – теплота, которая поступает в результате сгорания природного газа (топлива),
= 8 кВт – физическая теплота, которая поступает с вагонеткой массой 900 кг и теплоёмкостью 1,550 кДж/(кг⋅К),
= 9 кВт – физическая теплота, которая поступает с сырыми необожженными СТИ теплоёмкостью 0,85 кДж/(кг⋅К),
= 24 кВт – теплота, которая поступает с воздухом,
= 1163 кВт – полезная теплота, которая была расходована на нагревание, обжиг СТИ и нагревание вагонетки, определяется при условии, что средняя теплоёмкость вагонетки и СТИ составляет 1,314 кДж/(кг⋅К).
= 977 кВт – потери теплоты с уходящими газами, выходящими из обжиговой печи при температуре 600 °C.
= 897 кВт – потери теплоты в окружающую среду через ограждающие конструкции (расчёт произведён ниже).
Определим величины потерь теплоты через ограждающие конструкции печи. Суммарное термическое сопротивление для стен и свода в разных частях печи определим по зависимости:
![]() | (2) |
где – коэффициент теплоотдачи на внутренней поверхности ограждения печи. В связи с тем, что данная величина имеет значения свыше 300 Вт/м²⋅К, то ей можно пренебречь,
– толщина слоев конструкции стены,
= 0,3 м – толщина слоя шамота,
= 0,05 м – толщина слоя волокнистого огнеупора.
– коэффициент теплопроводности материала стены,
= 0,7+0,00064⋅t,
= 0,11+0,000125⋅t, Вт/м⋅К,
= 15 Вт/м²⋅К – коэффициент теплоотдачи на наружной поверхности ограждения.
Определим величины плотности теплового потока, который проходит через ограждения:
![]() | (3) |
где – средняя температура среды в объёме печи, °C,
= 20 °C – температура окружающего воздуха в помещении.
Определим величины теплового потока, который проходит через ограждения (потерь теплоты в окружающую среду):
![]() | (4) |
где – площадь ограждения, м,
Площадь стен в зоне подогрева:
Площадь стен в зоне обжига:
Площадь стен в зоне охлаждения:
Площадь свода в зоне подогрева:
Площадь свода в зоне обжига:
Площадь свода в зоне охлаждения:
Средняя температура среды в зоне подогрева:
где °C – температура среды на выходе из печи,
°C – температура среды в зоне обжига.
Средняя температура среды в зоне обжига:
Средняя температура среды в зоне охлаждения:
Потери теплоты в окружающую среду будем находить методом последовательных приближений. Это связано с тем, что коэффициент теплопроводности материала зависит от температуры.
Расчёт произведём на примере зоны подогрева.
1. Первое приближение:
= 0,7 Вт/(м⋅К),
= 0,11 Вт/(м⋅К).
Суммарное термическое сопротивление:
Средняя температура газов в методической зоне:
Плотность теплового потока:
2. Второе приближение:
Находим температуры на границе слоев:
Температура на границе шамот – волокнистый огнеупор:
Температура на границе волокнистый огнеупор – окружающая среда:
Средняя температура шамотного слоя
Средняя температура волокнистого огнеупора
Суммарное термическое сопротивление:
Плотность теплового потока:
Погрешность:
Погрешность больше 5% – продолжаем расчет.
3. Третье приближение:
Находим температуры на границе слоев:
Температура на границе шамот – волокнистый огнеупор:
Температура на границе волокнистый огнеупор – окружающая среда:
Средняя температура шамотного слоя
Средняя температура волокнистого огнеупора
Суммарное термическое сопротивление:
Плотность теплового потока:
Погрешность:
Погрешность меньше 5% – расчет окончен.
Тепловой поток, который проходит через стены зоны подогрева:
Тепловой поток, который проходит через свод зоны подогрева:
Аналогично рассчитаем зону обжига и зону охлаждения. Результаты занесем в таблицу 3.
Таблица 3 – Потери тепла через конструкцию обжиговой печи.
Зона | ![]() ![]() | ![]() ![]() | ![]() ![]() | ![]() ![]() | ![]() | ![]() |
Нагрева | 556,5 | 107,7 | 0,654 | 1346 | 188,4 | 141,3 |
Обжига | 755,7 | 148,1 | 0,593 | 1989 | 190,9 | 143,2 |
Охлаждения | 370,3 | 73,5 | 0,726 | 813 | 133,3 | 100,0 |
Общие потери теплоты в окружающую среду – 897 кВт |
Составим таблицу 4 приходной и расходной частей теплового баланса.
Таблица 4 – Приходная и расходная части теплового баланса печи.
Приход, кВт | Расход, кВт | ||
Теплота от сгорания топлива | 2996 | Полезная теплота | 1163 |
Теплота от вагонеток | 8 | Потери с уходящими газами | 977 |
Теплота от сырых СТИ | 9 | Потери в окружающую среду | 897 |
Теплота от воздуха | 24 | ||
Сумма | 3037 | Сумма | 3037 |
Важными участками обеспечения сокращения негативного воздействия на окружающую среду на предприятиях по производству СТИ являются установки по удалению пыли из воздуха аспирации, а также для очистки производственных сточных вод. Для очистки выбросов от пыли на российских предприятиях по производству СТИ применяют циклоны и рукавные фильтры.
Сточные воды, образующиеся в процессе изготовления керамики, как правило, содержат взвешенные частицы, поэтому при их очистке часто используют отстойники. Осаждение взвешенных веществ ускоряют путем введения флокулянтов и коагулянтов.
Дата добавления: 2019-02-22; просмотров: 611; Мы поможем в написании вашей работы! |
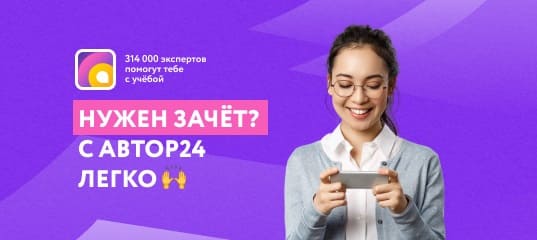
Мы поможем в написании ваших работ!