Приложение 1. Механизм поворота автокрана
Федеральное агенство морского и речного транспорта
Государственное образовательное учреждение
Высшего профессионального образования
«Волжская государственная академия водного транспорта»
Кафедра ПМ и ПТМ
ОТЧЕТ
Вид практики
Место практики: НОАО «Гидромаш»
Срок практики с 24 апреля 2018г по 24 мая 2018г
Руководитель практики: Адамов Е.И. от ВГАВТ
От предприятия НОАО «Гидромаш»
Отчет составил:
Студент группы ПТМ(б)-16-4512 Смирнова И.О.
Отчет защищен с оценкой:
Нижний Новгород
2018
Содержание
1 | Механизм поворота автокрана | 3 |
2 | Цевочное зацепление | 4 |
3 | Анализ контактного взаимодействия деталей планетарного цевочного редуктора | 6 |
4 | Приложение | 7 |
5 | Список используемой литературы | 9 |
Механизм поворота автокрана
Принцип работы
Механизм поворота служит для вращения поворотной части крана и представляет собой двухступенчатый редуктор с цилиндрическими косозубыми колесами.
Корпус механизма чугунный, разъемный. Верхняя часть корпуса 13 с нижней частью 15 соединяются болтами. К торцу корпуса 13 крепятся болтами фланец 11 и гидромотор 12. На конце вала гидромотора 12 установлен тормозной шкив 10, зубчатый конец которого вместе с зубчатой втулкой 9 образуют зубчатую муфту.
|
|
Шкив с зубчатой муфтой и деталями тормоза размещается в верхней части корпуса, имеющей специальное окно для доступа к указанным деталям.
В нижней части редуктора размещены два вала-шестерни 7 и 16, зубчатые колеса 5 и 20 и выходной вал 4.
Вращение от гидромотора через зубчатую муфту, вал-шестерню 7, зубчатое колесо 20, промежуточный вал-шестерню 16 и зубчатое колесо 5 передается на выходной вал 4 и выходную шестерню 2, которая находится в постоянном зацеплении с зубчатым венцом поворотной опоры.
Все валы редуктора опираются на подшипники.
Тормоз механизма поворота колодочный, нормально закрытый.
Тормоз расположен в верхней части корпуса редуктора и состоит из следующих основных частей: колодок 26, рычагов 21 и 28, тяги 24, пружины 22 и гидроразмыкателя тормоза 31.
При отключении (растормаживании) тормоза плунжеры гидроразмыкателя тормоза 31, под давлением рабочей жидкости гидравлической системы, поворачивают рычаги 21 и 28, которые, преодолевая усилие пружины 22, отводят колодки 26 от тормозного шкива 10.
При включении тормоза давление под плунжером гидроразмыкателя снижается и пружина 22 через тягу 24 и рычаги 21 и 28 прижимает колодки 26 к тормозному шкиву 10.
|
|
Рабочая длина пружины устанавливается гайками 23.
Равномерный отход колодок от шкива регулируется болтами 33.
Масло в корпус редуктора заливается через отверстие, закрытое пробкой 29. Уровень масла проверяется маслоуказателем 30.
Для предотвращения течи масла из редуктора по шейке вала 4 в крышку 17 вмонтированы две манжеты 3.
Для вращения поворотной части крана вручную промежуточный вал-шестерня 16 имеет квадратный хвостовик, выведенный наружу. Вращение осуществляется с помощью ключа, надеваемого на квадратный хвостовик вала-шестерни 16. (Приложение 1)
Установка и регулировка
При установке механизма поворота необходимо отрегулировать положение шестерни выходного вала редуктора относительно венца поворотной опоры. Должно быть обеспечено полное зацепление по высоте шестерни с зубчатым венцом поворотной опоры. Регулировать установкой прокладок.
Регулировку тормоза механизма поворота производите в следующей последовательности:
- установите гайками рабочую длину пружины, равную 99±1 (которая соответствует размеру 85±1 мм между внутренними торцами опорных чашек пружины) и зафиксируйте второй контргайкой;
- отрегулируйте винтами отход колодок от тормозного шкива: расстояние между упорными болтами и планками рычагов тормоза должно быть равно 4±1 мм.
|
|
Меры безопасности
- В процессе эксплуатации и обслуживании механизма поворота заливайте и сливайте масло, а также проверяйте уровень масла только при полной остановке механизма;
- соединительные муфты и наружная шестерня должны быть защищены предохранительным кожухом;
- включение механизма производить только после его закрепления;
- регулировку тормоза, разборку и ремонтные работы производить только при выключенном гидромоторе;
- при ремонтных и регулировочных работах соблюдайте правила по технике безопасности для слесарных, сварочных и такелажных работ.
Технические характеристики
Максимальная мощность на выходном валу, кВт | 13,6 |
Максимальный расчетный предельный момент на выходном валу, Нм | 3663 |
Передаточное число | 48,67 |
Минимальное давление размыкания тормоза, МПа | 0,8 |
КПД механизма | 0,97 (97%) |
Температура окружающей среды, С | -40/+50 |
Габаритные размеры, мм | |
Длина | 500 |
Ширина | 500 |
Высота | 820 |
Масса, кг., не более | 170 |
Цевочного зацепления
|
|
Цевочный механизм - зубчатый механизм для передачи вращения между параллельными валами, в котором одно из колёс, называемое цевочным, имеет зубья, выполненные в виде круговых цилиндров — цевок 3 (рис. 1). Зубья колеса 1, сопряжённого с цевочным 2, выполнены по эквидистанте (равноотстоящей кривой) к эпи- или гипоциклоиде. Преимущество цевочного механизма перед др. видами зубчатых механизмов в том, что цевки можно сделать вращающимися относительно своих осей. При этом уменьшаются потери на Tpenpie в зубчатом зацеплении и снижается износ поверхностей зубьев. Цевочное зацепление является частным случаем циклоидного зацепления. На рис. изображен цевочный механизм с внешним зацеплением, при котором цевочное колесо 2 и зубчатое колесо 1 вращаются в противоположных направлениях. Цевки в этом случае располагаются на начальной окружности цевочного колеса 2. При внутреннем зацеплении цевочное и зубчатое колёса вращаются в одном н том же направлении. Цевки располагаются на окружности, радиус которой больше радиуса начальной окружности цевочного механизма с внутренним зацеплением даёт возможность получить разность между числом цевок и числом зубьев, равную единице, что обеспечивает большое Передаточное число в планетарном редукторе (до 1: 100 в одной ступени) при относительно высоком кпд (около 0,75) и компактности передачи. Ц. м. применяется преимущественно в планетарных редукторах и приборах.
Рис. 1 Цевочный механизм
Также образовано на основе циклоидального. В этом зацеплении зубья одного колеса заменены цевками – цилиндрами, вставленными между дисками, закрепленными на оси. Второе колесо выполняется с зубьями часового профиля. Минимальное число цевок равно шести. Цевочное зацепление имеет ограниченное применение. Оно используется главным образом для передач с большой редукцией в общем машиностроении и в точной механике, применяют при передаче незначительных усилий, при отсутствии жестких требований к точности и возможности загрязнения передачи. Это зацепление отличается простотой изготовления, так же используется в некоторых механизмах приборов и машин при малых скоростях и обычно при больших усилиях.
Цевочное зацепление является частным случаем циклоидального зацепления, когда в качестве образующей окружности головки зуба малого колеса взята точка, лежащая на начальной окружности большого колеса. Ножка зуба малого колеса равна нулю, так как радиус образующей окружности ножки равен радиусу начальной окружности. При таком условии зуб малого колеса превращается в точку. Практически зубья выполняются в виде цилиндров (цевок), закрепленных между двумя дисками. Цевочное зацепление (точечное циклоидальное) по характеру близко к часовому. Применяется, главным образом, при малых усилиях и скоростях в дешевых изделиях, а также в маломощных планетарных редукторах с внутренним зацеплением, где замена колеса с зубьями, нарезанными по внутреннему ободу, цевочным колесом дает экономический эффект.
Применяется в дешевых механизмах при передаче малых усилий и в механизмах, подверженных сильному загрязнению. Недостатком цевочного зацепления является сильный износ зубьев.
Достоинством цевочного зацепления является малая чувствительность к загрязнению, простота конструкции, меньшая стоимость изготовления, значительные передаточные числа, удобства при монтаже, эксплуатации и ремонте, малая величина потерь на трение, если цевки выполнить вращающимися на осях. Колесо с цевками изготовляется очень просто, но изготовить сопряженное ему зубчатое колесо с большой точностью трудно. Поэтому внешнее цевочное зацепление применяется преимущественно в громоздких тихоходных передачах, например, в башенных кранах.
Для проверки цевочного зацепления замеряют радиальные зазоры между поверхностями и впадиной зуба. Если полученный размер отличается от указанного в чертежах (порядка 2 мм), необходимо сместить механизм поворота и закрепить его в таком положении приваркой упоров.
Анализ контактного взаимодействия деталей планетарного цевочного редуктора.
Последние достижения в области разработок машиностроительной, авиационной, автомобильной и другой техники привели к повышению контактных нагрузок в силовых механизмах. Именно такие механизмы, предназначенные для передачи больших нагрузок и/или высоких скоростей вращения посредством силовых элементов, находящихся в непосредственном или опосредованном контакте, очень широко применяются в современной технике. К числу таких узлов и механизмов можно отнести винтовые передачи и соединения, шлицевые соединения, зубчатые передачи, муфты различных типов и т.д. Характерной особенностью этих узлов и механизмов является распределение передаваемой ими силы или момента между несколькими парами (группами) силовых элементов. Например, в винтовой передаче, имеющей гайку с четырьмя витками резьбы, осевая сила в каждый момент времени распределяется некоторым образом между четырьмя витками резьбы винта и гайки; в шлицевом соединении с шестью парами шлицев втулки и вала между шлицами распределяется рабочий крутящий момент; в зубчатой муфте с шестнадцатью зубьями у втулки и вала, по этой логике, крутящий момент распределяется между шестнадцатью парами элементов и т.д. Необходимое число силовых рабочих элементов определяется в зависимости от величины передаваемой нагрузки с учетом свойств конструкционных материалов. При этом все существующие методики таких расчетов основаны на жестком детерминированном подходе и используют эмпирические и полуэмпирические зависимости. Возникающие несоответствия между результатами проектных расчетов и эксплуатационными свойствами объектов расчетов устраняются путем введения в расчетные формулы большого количества эмпирических коэффициентов, среди которых превалирует по величине коэффициент запаса прочности. Величина этого коэффициента при расчете параметров различных механизмов может достигать десяти и больше, что, фактически, обесценивает значение самих расчетов и приближает процесс принятия решений к интуитивному уровню.
Приложение
Приложение 1. Механизм поворота автокрана
Продолжение приложения 1
Список используемой литературы
1. Литвин Ф. Л., Проектирование механизмов и деталей приборов, Л., 1973. Н. И. Левитский.
2. Быстрова В.И. Проектирование механизмов и приборов
3. Гаврилов А.Н. Приборостроение и средства автоматики Т 2 Кн. 1
4. Ачеркан Н.С. Справочник машиностроителя Том 1 Изд.3
5. Первицкий Ю.Д. Расчет и конструирование точных механизмов
6. Гевондян Т.А. Детали механизмов точной механики
7. Ванторин В.Д. Механизмы приборных и вычислительных систем
8. Добровольский В.В. Теория механизмов Издание 2
9. Моргачев В.Л. Подъемно-транспортные машины
10. Левитский Н.И. Теория механизмов и машин
11. Невзоров Л.А. Машинист башенного крана Издание 2
12. Курдюков Е.С. АНАЛИЗ МЕХАНИЗМА КОНТАКТНОГО ВЗАИМОДЕЙСТВИЯ ДЕТАЛЕЙ ПЛАНЕТАРНО ЦЕВОЧНОГО РЕДУКТОРА
Дата добавления: 2019-02-22; просмотров: 555; Мы поможем в написании вашей работы! |
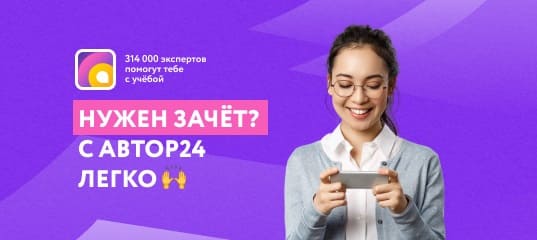
Мы поможем в написании ваших работ!