Сталь углеродистая обыкновенного качества, ГОСТ 380-88
Марка стали | Содержа-ние С, % | Механические свойства | |||
НВ | σв , Н/мм2 | σТ , Н/мм2 | δ , % | ||
Ст0 Ст1 Ст2 Ст3 Ст4 Ст5 Ст6 | < 0,23 0,06…0,12 0,2…0,15 0,14…0,22 0,18…0,27 0,28…0,37 0,38…0,49 | – – 210 220 240 270 300 | Не менее 320 320…400 340…420 380…470 420…520 500…620 600…720 | – – 220…190 200…250 230…270 460…640 320…300 | 22 33 31 27…25 25…23 21…19 16…14 |
Таблица 2
Примерное назначение различных марок углеродистой
Инструментальной стали, ГОСТ 1435-88
Марка стали | Область применения |
У7, У7А | Изготовление ударно-режущего инструмента: топоров, зубил, бойков, стамесок, молотков, кусачек и др. |
У8, У8А, У9, У9А | Изготовление режущих инструментов, работающих в условиях, не вызывающих разогрева режущей кромки более 200 оС: фрез, пил продольных и дисковых, зенковок, долот и др. |
У10, У10А. У11, У11А | Изготовление штампов холодной штамповки (вытяжных, высадочных, обрезных и вырубных), напильников, шаберов. |
У12, У12А | Изготовление метчиков, напильников, шаберов, штампов холодной штамповки. |
У 13, У13А | Изготовление бритвенных лезвий и ножей, острых хирургических инструментов, гравировальных инструментов. |
|
|
Таблица 3
Марки серых чугунов и их механические свойства, ГОСТ 1412-85
Марка чугуна | σв, Н/мм2 не менее | НВ |
СЧ10 | 100 | 120…205 |
СЧ15 | 150 | 130…241 |
СЧ20 | 200 | 143…255 |
СЧ25 | 250 | 156…260 |
СЧ30 | 300 | 153…270 |
СЧ35 | 350 | 179...290 |
Таблица 4
Марки ковких чугунов и их механические свойства, ГОСТ 1215-79
Марка чугуна | σв, Н/мм2 | δ ,% | НВ |
Не менее | |||
КЧ30-6 | 300 | 6 | 100…163 |
КЧ33-8 | 330 | 8 | 100…163 |
КЧ35-10 | 350 | 10 | 100…163 |
КЧ37-12 | 370 | 12 | 110…163 |
КЧ45-7 | 450 | 7 | 150…207 |
КЧ50-5 | 500 | 5 | 170…230 |
КЧ55-4 | 550 | 4 | 192…241 |
КЧ60-3 | 600 | 3 | 200…269 |
КЧ65-3 | 650 | 3 | 212…269 |
КЧ70-2 | 700 | 2 | 241…285 |
КЧ80-1,5 | 800 | 1,5 | 270…320 |
Таблица 5
|
|
Марки высокопрочных чугунов и их механические свойства,
ГОСТ 7293-85
Марка чугуна | σв , Н/мм2 | σ0,2 , Н/мм2 | δ ,% | НВ |
Не менее | ||||
ВЧ35 | 350 | 220 | 22 | 140…170 |
ВЧ40 | 400 | 250 | 15 | 140…202 |
ВЧ45 | 450 | 310 | 10 | 140…225 |
ВЧ50 | 500 | 320 | 7 | 153…245 |
ВЧ60 | 600 | 370 | 3 | 192…277 |
ВЧ70 | 700 | 420 | 2 | 223…302 |
ВЧ80 | 800 | 480 | 2 | 248…351 |
ВЧ100 | 1000 | 700 | 2 | 270…360 |
Содержание отчета
1. Название и цель лабораторной работы.
2. Оснащение.
3. Схемы микроструктур сталей (6 образцов) с указанием структурных составляющих, содержания углерода, марки стали (ГОСТ1050-88, ГОСТ 380-88, ГОСТ 1435-88) и механических свойств.
4. Схемы микроструктур чугунов (6 образцов) с указанием структурных составляющих, содержания связанного углерода, марки и механических свойств.
Пример оформления схемы микроструктуры
Перлит 40%
Феррит 60%
|
Лабораторная работа №3
Получение литых заготовок
|
|
Цель работы
Ознакомиться с изготовлением отливок в песчано-глинистые и металлические формы.
Оснащение:
1. Чертёж детали.
2. Модель изделия и модель литниковой системы.
3. Муфельная электропечь сопротивления.
4. Стержневой ящик.
5. Парные опоки.
6. Формовочные материалы (песок, глина, опилки, припылы и др.).
7. Разъемный кокиль.
8. Машина центробежного литья.
Общие сведения
1.1. Получение отливок в песчано-глинистых формах
Технологический процесс получения отливок в песчано-глинистые формы можно представить следующим образом. По чертежу детали разрабатывают чертёж элементов литейной формы и чертёж отливки. При изготовлении несложных отливок чертёж отливки и литейной формы делают совмещённым. По нему изготавливают модельный комплект, куда входят модель детали, стержневой ящик и модели литниковой системы. По моделям детали и литниковой системы из формовочной смеси изготовляют литейную форму, а из стержневой смеси – стержни, конфигурация которых соответствует внутренним полостям детали. Для повышения прочности стержней их сушат в сушильных печах. Изготовленную форму раскрывают, извлекают из обеих полуформ половинки модели детали и модели литниковой системы, покрывают полость формы припылами или красками, устанавливают в форму стержень и вновь ее собирают. Затем в форму заливают расплавленный металл. После затвердевания металла в форме образуется отливка, которую выбивают из формы. Готовую отливку освобождают от пригоревшей формовочной смеси, удаляют литниковую систему, выбивают стержень и отправляют на механическую обработку.
|
|
Основой для разработки технологического процесса изготовления отливки является чертеж детали. На копии чертежа детали в соответствии с ГОСТ 3.1125-88 (взамен устаревшего ГОСТ 2.423-73) наносят технологические указания, необходимые для изготовления модельного комплекта, формы и стержня, и получают чертеж элементов литейной формы.
На рис. 3.1 в качестве примера приведен эскиз детали. Поверхности детали, подвергающиеся механической обработке, условно обозначены знаком . Остальные поверхности механической обработке не подлежат, на что указывает знак
в правом верхнем углу эскиза.
![]() |
«Ступица»
СЧ 20 ГОСТ 1412
Рис. 3.1. Чертёж детали «Ступица»
![]() |
«Ступица»
СЧ 20 ГОСТ 1412
Формовочные
уклоны 30
Усадка 1%
Рис. 3.2. Чертёж элементов литейной формы с модельно-литейными указаниями
При разработке чертежа (эскиза) "Элементы литейной формы" детали формы обозначают условно (рис. 3.2).
1. Разъем модели и формы показывают отрезком или ломаной сплошной линией, заканчивающейся знаком « », над которым указывают буквенное обозначение разъема 1 – "МФ", что означает: М – разъём модели, а Ф – разъём формы.
Направление разъема показывают сплошной основной линией, ограниченной стрелками и перпендикулярной линии разъема.
Положение отливки в форме при заливке обозначают буквами В (верх) и Н (низ). Буквы проставляют у стрелок, показывающих направление разъема формы.
2. Припуски на механическую обработку изображают сплошной тонкой линией у поверхностей 9, где указан знак обработки (допускается выполнять линию припуска красным карандашом). Величину припуска 2 проставляют перед знаком шероховатости.
Припуск на механическую обработку – это слой металла, удаляемый в процессе механической обработки отливки с ее обрабатываемых поверхностей для обеспечения геометрической точности и качества поверхности детали. Величина припуска зависит от материала и размеров отливки, ее положения в форме и регламентируется соответствующим ГОСТом. Для мелких отливок припуск может быть в пределах 2...5 мм.
3. Отверстия, впадины и т. п., не выполняемые при изготовлении отливки детали зачеркивают сплошной тонкой линией 3, которую допускается выполнять красным карандашом.
4. Стержни, их знаки изображают сплошной тонкой линией, которую допускается выполнять синим цветом, а также обозначают буквами "cm ." и порядковыми номерами, например, cm .1 (см. рис.3.2). Стержни 4 в разрезе штрихуют только у контурных линий. Размеры знаков 5 стержней и зазоры между знаками стержней и модели принимают по ГОСТ 3606-80.
Стержни соответствуют конфигурации внутренней полости отливки.
Отверстия деталей диаметром менее 20 мм обычно в литье не выполняются, а изготовляются механической обработкой.
5. Литниковую систему и прибыли – каналы, питающие форму расплавленным металлом (стояк 6, шлакоуловитель 7, питатели 8, выпор), вычерчивают тонкими линиями в поле чертежа, которые допускается выполнять красным цветом (см. рис. 3.2). Геометрические размеры элементов литниковой системы определяются из отдельных расчётов.
6. Формовочные уклоны служат для облегчения выемки модели из формы без ее разрушения (см. рис. 3.2). Величина уклона зависит от материала модели и высоты боковой поверхности и может составлять 0,5...3°. Величину уклона указывают рядом в поле чертежа детали.
7. Усадка. Модели и стержневые ящики должны быть больше соответствующих размеров отливки на величину усадки металла. Усадка серого чугуна составляет 1 %, стали – 2 %, цветных сплавов – 1,5...2 %. Величину усадки указывают в списке технических требований в поле чертежа детали.
При разработке чертежа (эскиза) " Элементы литейной формы" исходят из условия обеспечения качества отливки и экономичности ее изготовления. Выбирая плоскость разъема, следует помнить, что наиболее ответственные поверхности отливки целесообразно располагать в нижней части формы или вертикально, так как в верхней части отливки скапливаются дефекты – газовые раковины и шлаковые включения. Плоскость разъема выбирают с учетом удобства формовки и извлечения модели из формы. Кроме того, желательно, чтобы отливка или, по крайней мере, ее базовые поверхности для механической обработки были расположены в одной полуформе.
Чертеж (эскиз) "Элементы литейной формы" служит основой для разработки модельного комплекта: модели и стержневых ящиков.
Модель детали – это приспособление для получения полости, по форме и размерам близкой к конфигурации получаемой отливки. Модели могут быть неразъёмными, разъёмными, могут иметь отделяемые части.
Стержневой ящик – приспособление, служащее для изготовления стержней. Стержневые ящики бывают цельными, разъёмными и вытряхными. Их изготавливают из дерева или металла в зависимости от вида производства. Внутренняя полость стержневого ящика должна полностью соответствовать наружному контуру стержня.
Модели элементов литниковой системы – это приспособления для получения в литейной форме системы каналов, через которые жидкий металл будет заливаться в полость формы.
Стояк 1 представляет собой конический стержень, образующий в форме вертикальный канал, по которому металл из литниковой чаши поступает в шлакоуловитель 2, расположенный в верхней половине формы (рис. 3.3).
Fn =…см2
Кол=…шт.
∑ F п =…см2
F шл =…см2
Кол=…шт.
∑ F шл =…см2
F ст =…см2
Кол=…шт.
∑ F ст =…см2
Рис. 3.3. Элементы литниковой системы:
1 – питатели, 2 – шлакоуловитель, 3 – стояк
Шлакоуловитель 2 представляет собой в поперечном сечении трапецию и служит для задержания шлака и неметаллических включений, попавших в стояк.
Питатели 3, расположенные в нижней половине формы, имеют также трапецеидальное сечение и служат для плавного подвода металла в самые тонкие участки отливки непосредственно из шлакоуловителя.
Выпор представляет собой конический стержень, который устанавливается на модели в самой высокой ее части и служит для вывода из формы воздуха, газов, шлака.
Соотношение суммы площадей поперечного сечения стояка, шлакоуловителей и питателей должно отвечать следующей зависимости:
.
На рис. 3.4 дан эскиз деревянной модели для ручной формовки. Модель имеет разъем 1, стержневые знаки 2 (они окрашены черным цветом), конфигурация которых соответствует конфигурации знаков, указанных на рис. 3.2. На модели предусматривают формовочные уклоны на стенках, перпендикулярных плоскости разъема (определены ГОСТом), и радиусы скруглений в местах сопряжения стенок. Размеры моделей выполняют с учетом припусков на механическую обработку, технологических припусков и усадки сплава, из которого изготавливают отливку (см. рис. 3.2).
Рис. 3.4. Эскиз модели: 1 – плоскость разъема; 2 – стержневые знаки
На рис. 3.5 показан деревянный стержневой ящик, предназначенный для ручного изготовления стержня
а) б)
Рис. 3.5. Стержневой ящик (а) и стержень (б)
Приготовление формовочной и стержневой смесей
Литейные формы изготовляют из формовочных смесей. Основными формовочными материалами являются кварцевый песок и огнеупорная глина, вспомогательными – молотый уголь, древесный пек, опилки и др.
Формовочные смеси подразделяются на единые, облицовочные, наполнительные, стержневые. Облицовочные смеси приготовляются только из свежих материалов и применяются для изготовления высококачественных отливок (например, художественных). Наполнительные смеси имеют грубый зерновой состав для большей газопроницаемости.
В состав всех единых формовочных смесей вводят отработанную формовочную смесь в количестве 70...90 % в зависимости от вида литья.
Все формовочные смеси должны обладать комплексом специальных свойств: пластичностью, прочностью, газопроницаемостью, податливостью, огнеупорностью.
Свойства формовочных смесей определяются влажностью, содержанием глины (ее общее содержание не должно превышать 10%), величиной и формой зерен песка. Влажность формовочных смесей должна быть в пределах 5 % к общей массе сухих материалов.
Процесс приготовления формовочных смесей сводится к перемешиванию подготовленных составляющих смеси в бегунах или специальных смесителях. Компоненты смеси перемешиваются вначале в сухом состоянии, а затем при добавлении воды.
Готовая формовочная смесь из бегунов поступает в отстойники, из них в разрыхлитель и оттуда к месту изготовления форм.
Стержневые смеси приготавливаются аналогичным способом, но должны обладать более высокой прочностью, огнеупорностью и газопроницаемостью, лучшей податливостью и выбиваемостью, что обеспечивается специальными добавками (опилки, торф и др.).
Изготовление стержней
Процесс изготовления стержней состоит из следующих операций: формовка сырого стержня, сушка, отделка и окраска сухого стержня.
При ручном изготовлении стержня внутреннюю полость стержневого ящика смазывают керосином или машинным маслом, наполняют стержневой смесью и уплотняют, металлической иглой делают вентиляционный канал и извлекают стержень из ящика. Готовый стержень устанавливают на сушильную плиту и отправляют в сушильную печь, где производится сушка при температуре 350…400° С. Тонкие, ажурные стержни для повышения прочности армируют проволокой.
Изготовление литейной формы
По степени механизации различают ручную и машинную формовку. Ручная формовка применяется для получения небольших партий отливок в условиях единичного производства.
Наиболее распространённым способом изготовления литейных форм является формовка в парных опоках по разъемным моделям. Опоки представляют собой металлические рамки, в которых изготавливают литейные формы. Изготовление литейной формы производится в следующей последовательности (рис. 3.6). На подмодельную плиту устанавливают нижнюю половину модели, модели питателей и опоку, в которую засыпают формовочную смесь и уплотняют (рис. 3.6, а). Опоку поворачивают на 180° и устанавливают вторую половину модели, модели шлакоуловителя, стояка и выпора. По центрирующим штырям устанавливают верхнюю опоку, засыпают в неё формовочную смесь и уплотняют (рис. 3.6, б). После извлечения моделей стояка и выпора форму раскрывают. Из полуформ извлекают модели изделия, модели шлакоуловителя и питателей, в нижнюю полуформу устанавливают стержень и накрывают нижнюю половину формы верхней (рис. 3.6, в).
После заливки жидкого металла и его затвердевания литейную форму разрушают и извлекают готовую отливку (рис. 3.7).
Готовые отливки после отделения литников, выпора и очистки подвергаются контролю с целью выявления дефектов отливки и установления причин их образования. Видами брака отливок считаются: шлаковые и усадочные раковины, трещины, непроливы, заливы в плоскости разъема, коробление, искажение размеров и веса, газовая пористость.
2 3 4 5
6
1
8 9 10 11 12 13
7
14
Рис. 3.6. Этапы формовки: а – нижней опоки: б – верхней опоки; в – форма в сборе;
1 – подмодельная плита; 2 – питатель, 3 – нижняя полумодель; 4 – формовочная смесь; 5 – вентиляционные наколы; 6 – нижняя опока; 7 – центрирующие штыри; 8 – модель шлакоуловителя; 9 – модель стояка; 10 – литниковая чаша; 11 – верхняя полумодель; 12 – модель выпора; 13 – верхняя опока; 14 – стержень
Рис. 3.7. Готовая отливка с литниковой системой:1 – отливка; 2 – питатели; 3 – шлакоуловитель; 4 – стояк; 5 – литниковая чаша; 6 – выпор
1.2. Литье в металлические формы
Литье в металлические формы является частью специальных видов литья и объединяет такие способы, как литье в кокиль, центробежное литье, литье под давлением. В данной работе будут рассмотрены первые два способа.
1.2.1. Центробежное литьё
Сущность этого метода заключается в заливке расплавленного металла во вращающуюся форму. Под действием центробежных сил жидкий металл прижимается к стенкам формы и в таком положении затвердевает. После затвердевания металла вращение формы прекращается и готовая отливка извлекается из формы.
Этим способом получают отливки, представляющие собой тела вращения типа втулок, колец, труб и т.п.
При центробежном литье отверстие получается без применения стержней, отливки отличаются высокой плотностью и механическими свойствами. К преимуществам этого способа следует отнести высокую производительность процесса, а также отсутствие литниковой системы, что уменьшает расход металла.
Отливки при этом способе производятся на специальных центробежных машинах. В зависимости от расположения оси вращения формы в пространстве различают машины с горизонтальными и вертикальными осями вращения (рис. 3.8).
В форме с вертикальной осью вращения внутренняя поверхность отливки получается параболической формы, вследствие чего на этих машинах отливают заготовки небольшой высоты. На машинах с горизонтальной осью вращения можно отливать заготовки практически любой длины.
|
|
|
|
Рис. 3.8. Схемы получения центробежных отливок:
а – с вертикальной осью вращения формы; б – с горизонтальной осью вращения формы
На рис. 3.9 представлена схема общего вида центробежной машины с горизонтальной осью вращения для отливки детали втулка.
Рис. 3.9. Схема общего вида центробежной машины: 1 – разъёмная форма;
2 – крышка; 3 – зажим; 4 – несущий вал; 5 – корпус; 6 – толкатель; 7 – подпружиненная штанга; 8, 9 – клиноремённая передача; 10 – электродвигатель; 11 – лоток
Вращающаяся разъемная форма 1 закрывается крышкой 2 с помощью подпружиненных зажимов 3. Несущий вал 4 литейной формы вращается в корпусе 5 на двух подшипниках от электродвигателя 10 через клино-ремённую передачу 8 и 9. Для выталкивания отливки из формы служит подпружиненная штанга 7 с толкателем 6. Заливка жидкого металла осуществляется через лоток 11.
1.2.2. Литьё в кокиль
Кокиль – это постоянная металлическая форма, выполняемая из чугуна или стали. Принцип заливки жидкого металла в кокиль такой же, как и в песчано-глинистые формы через литниковую систему.
Литьё в кокиль значительно выгоднее, чем литьё в песчано-глинистые формы за счет его многократного использования. Кокили в зависимости от заливаемого в них сплава могут выдержать большое количество заливок (от сотен до десятков тысяч). Стойкость кокилей будет зависеть от температуры заливаемого сплава: чем ниже температура, тем выше их стойкость. Стойкость кокилей повышают предварительным их подогревом.
Отливки, получаемые при литье в кокиль, отличаются чистотой поверхности, точностью размеров, высокими механическими свойствами.
Однако применение кокилей ограничивается деталями сравнительно простой конфигурации, так как выполнить в металле контур детали сложной формы трудно и весьма дорого.
Из всего объема литья в машиностроении методом литья в кокиль получают до 45 % всех отливок из алюминиевых и магниевых сплавов, 11 % чугунных отливок и только 6 % – стальных. Чугунные отливки получаются с отбелённой структурой, поэтому их подвергают графитизирующему отжигу.
Экономическая целесообразность применения литья в кокиль имеет место в серийном и массовом производстве за счёт возможности частичной или полной механизации процесса.
По конструкции кокили бывают вытряхные, разъемные из двух или нескольких частей, с металлическими или песчаными стержнями, с толкателями для извлечения отливок из формы и т.п.
Наиболее простыми по конструкции являются вытряхные кокили, которые применяются большей частью при отливке чугунных и стальных отливок. На рис. 3.10 приведен разрез вытряхного кокиля для отливки чугунных втулок.
Рис. 3.10. Вытряхной кокиль: 1 – корпус; 2 – крышка; 3 – полость для отливки; 4 – стержень; 5 – литниковые каналы; 6 – литниковая чаша; 7 – цапфы для поворота кокиля на 180 º
Для отливки деталей из алюминиевых и магниевых сплавов применяются более сложные конструкции кокилей с металлическими стержнями, с толкателями и механизированным разъёмом.
На рис. 3.11 показана схема общего вида кокиля с вертикальной плоскостью разъема для отливки детали хомут из алюминиевого сплава.
Кокиль состоит из неподвижной части 1 и подвижной части 2. Внутри неподвижной части выполнена полость 3, образующая форму детали хомут. Внутри полости установлен металлический стержень 5, образующий в отливке отверстие. Заливка металла в форму осуществляется через литниковую чашу 4 и щелевой питатель. Подвижная часть кокиля перемещается с помощью винта 6, установленного в задней стойке 7, по направляющим 8. После затвердевания отливки полуформу 2 кокиля отодвигают и отливка удаляется при помощи толкателей 9.
Рис. 3.11. Схема общего вида разъёмного кокиля
Порядок проведения работы
1. Вычертить эскиз детали втулка (рис. 3.12).
«Втулка»
АЛ2 ГОСТ 2685
Рис. 3.12. Эскиз детали «Втулка»
2. Вычертить копию эскиза детали. Нанести на копию модельно-литейные указания: разъем модели и формы, расположение отливки в форме «В» и «Н», припуски на механическую обработку, формовочные уклоны, форму стержней и размеры стержневых знаков, усадку, неотливаемые отверстия (п. 1…7 с. 35, 36).
З. В соответствии с модельно-литейными указаниями вычертить модель отливки и стержневой ящик со стержнем.
4. Загрузить в электропечь тигель с необходимым количеством сплава, из которого будет отливаться деталь.
5. Приготовить З кг формовочной смеси следующего состава:
– сухая отработанная формовочная смесь – 90 %;
– сухой свежеприготовленный кварцевый песок – 8 %;
– сухая свежеприготовленная огнеупорная глина – 2 %;
– вода – 5 % (сверх 100%).
Взвешенные компоненты формовочной смеси загрузить в лабораторные бегуны. Произвести перемешивание их в сухом виде в течение 2...3 минут. Добавить в смесь воду и продолжить перемешивание еще в течение 5...6 минут. Приготовленную смесь выгрузить в металлический противень.
6. Приготовить 0,1...0,2 кг стержневой смеси, для чего взять указанное количество формовочной смеси и добавить в нее 2...3 % опилок или торфяной крошки и перемешать вручную.
7. Изготовить стержень. Стержневой ящик установить на плиту. Наполнить полость ящика стержневой смесью и уплотнить ее при помощи трамбовки. Загладить торцевые части стержня и при помощи душника произвести по оси стержня накол для получения вентиляционного канала. Извлечь стержень из стержневого ящика и поместить в сушильный шкаф для сушки. Сушка длится в течение 1...1,5 часа при температуре 350...400° С.
8. Изготовить и собрать форму. Нижнюю половину модели, не имеющую центрирующих шипов, и модели питателя положить плоскостью разъема на подмодельную плиту. Сверху установить нижнюю опоку плоскостью разъёма вниз так, чтобы расстояние от модели до стенок опоки было примерно одинаковым. На модель насыпать слой формовочной смеси 20...30 мм и уплотнить ее руками вокруг всей модели. Наполнить формовочной смесью остальной объем опоки. Клиновым концом трамбовки смесь уплотнить сначала у стенок опоки, а затем в средней части. После добавления смеси выше краёв опоки уплотнить её тупым концом трамбовки. Излишек смеси срезать линейкой. Душником наколоть вентиляционные каналы.
Заформованную нижнюю опоку перевернуть на 180º. На нижнюю половину модели по центрирующим шипам установить верхнюю половину модели и модели шлакоуловителя, стояка и выпора. Поверхность разъема формы посыпать тонким слоем сухого кварцевого песка или графита, чтобы формовочная смесь в верхней опоке не прилипала к смеси в нижней опоке. По центрирующим штырям на нижнюю опоку установить верхнюю опоку.
Наполнить и уплотнить смесь в верхней опоке в таком же порядке, как и в нижней.
После накалывания вентиляционных каналов гладилкой вокруг стояка прорезать литниковую чашу.
Модели стояка и выпора слегка раскачать и удалить из верхней полуформы. Верхнюю опоку снять и перевернуть на 180 град. Из полуформы после легкого раскачивания удалить модель отливки и модели шлакоуловителя и питателей. Обе полуформы припылить серебристым графитом, тальком или другими пылевидными материалами с целью получения отливки с более чистой поверхностью.
В нижнюю полуформу установить высушенный и охлаждённый стержень и закрыть ее по центрирующим штырям верхней полуформой.
На верхнюю полуформу установить груз для предотвращения ухода жидкого металла через разъем формы во время заливки.
9. Залить форму жидким металлом (работу с расплавленным металлом и горячей отливкой выполняет учебный мастер). Металл перед заливкой должен быть перегрет на 30…110° С выше температуры плавления для повышения жидкотекучести. При достижении заданной температуры сплава тигель вынуть из печи и выдержать некоторое время для выделения газов, всплывания шлака и неметаллических включений, которые с поверхности жидкого металла удалить. Разливку сплава вести, не прерывая струи, до появления его из отверстия выпора.
10. Выбить отливку из формы после затвердевания и частичного остывания (через 10…15 минут после заливки). Извлечённую отливку охладить и очистить.
11. Вычертить эскизы формовки (нижней опоки, верхней опоки) и формы в сборе.
12. Вычертить эскиз готовой отливки с элементами литниковой системы в аксонометрии.
13. Произвести заливку алюминиевым сплавом кокиля и центробежной машины. Оценить качество отливок, полученных литьем в кокиль, центробежную машину и в песчано-глинистую форму.
Содержание отчета
1. Название и цель лабораторной работы.
2. Оснащение.
3. Эскиз детали «Втулка».
4. Эскиз элементов литейной формы для литья детали «Втулка» в
песчано-глинистую форму.
5. Эскизы модели, стержневого ящика и стержня.
6. Эскизы этапов формовки (нижней полуформы, верхней полу-формы и формы в сборе).
7. Эскиз отливки.
8. Оценка качества полученного литья в песчано-глинистую форму, в кокиль и центробежную машину.
Лабораторная работа №4
Обработка металлов резанием
Цель работы
Познакомиться с основными видами обработки материалов резанием.
Материальное обеспечение работы
1. Металлорежущие станки: токарные, фрезерные, сверлильные, зубообрабатывающие, шлифовальные.
2. Металлорежущий инструмент: резцы, фрезы, свёрла, зенкеры, развёртки и др.
Общие сведения
Обработка металлов резанием в настоящее время является основным методом окончательной обработки деталей. Объясняется это, в первую очередь, тем, что общий прогресс в машиностроении и интенсификация технологических процессов во всех областях промышленности требуют изготовления все более точных и обработанных с высокой степенью качества поверхностей деталей машин, а это можно в основном получить обработкой металлов резанием.
До начала обработки резанием будущую деталь принято называть заготовкой, в процессе обработки эта заготовка по окончании всех видов обработок превращается в готовую деталь, которая может быть передана на сборку изделия.
Слой металла, который необходимо удалить с заготовки для получения детали в окончательно обработанном виде, называется припуском на обработку. Удаление с заготовки припуска ручным способом называется слесарной обработкой, а снятие припуска на станках – механической обработкой.
Механическая обработка выполняется на металлорежущих станках: токарных, фрезерных, сверлильных и др. с использованием различного инструмента, режущая часть которого должна быть твёрже обрабатываемого материала и иметь форму клина.
При любом методе механической обработки детали различают три основных вида поверхностей.
Обрабатываемая поверхность 1 (рис. 4.1, а) – это поверхность, срезаемая с обрабатываемой детали за данный проход. Она исчезает по окончании прохода. Обработанная поверхность 3 определяется как поверхность, полученная в результате снятия слоя материала с обрабатываемой детали за один проход. Эта поверхность отсутствует до начала прохода.
Рис. 4.1. Процесс точения: а – вид в плане; б – части и поверхности резца; в – углы резания
Поверхностью резания 2 называется поверхность, непосредственно образованная на обрабатываемой детали главным лезвием инструмента.
Геометрия режущего инструмента. Принцип работы любого режущего инструмента основан на действии клина. Наиболее наглядно можно рассмотреть элементы и геометрию режущего инструмента на примере токарного резца. Последний состоит из головки (рис. 4.1, б), которая принимает непосредственное участие в отделении срезаемого слоя металла, подошвы, на которую опирается резец при установке его на станке, и тела, с помощью которого производится закрепление резца в резцедержателе. Основными элементами головки резца являются: передняя поверхность 9, по которой сходит стружка, главная задняя поверхность 5, обращенная к поверхности резания, вспомогательная задняя поверхность 6, обращенная к обработанной поверхности, главное лезвие 4, являющееся пересечением передней и главной задней поверхностей, вспомогательное лезвие 8, являющееся пересечением передней и вспомогательной задней поверхностей, и вершина 7, образованная пересечением лезвий.
Углы режущей части инструмента. Различают главные и вспомогательные углы, а также углы в плане. Главные углы измеряются в главной секущей плоскости Г – Г (рис. 4.1, а, в). К ним относятся: главный задний угол, угол заострения, главный передний угол и угол резания.
Главным задним углом α называется угол, образованный главной задней поверхностью инструмента и плоскостью резания А – А (рис. 4.1, в). Этот угол необходим для уменьшения трения между обрабатываемой деталью и резцом. Угол α равен 6…12°. Главным передним углом γ называется угол между передней поверхностью и нормальной плоскостью В – В. Значение угла γ колеблется в пределах от + 25° до – 10°. Углом заострения β называется угол между передней и главной задней поверхностями. Углом резания δ называется угол между передней поверхностью и плоскостью резания А – А.
Углы в плане рассматриваются в основной плоскости (см. рис. 4.1, а). Имеются главный угол в плане, вспомогательный угол в плане и угол при вершине резца.
Главным углом в плане φ называется угол между проекцией главного лезвия на основную плоскость и направлением движения подачи s. В зависимости от условий обработки угол φ принимается от 30 до 90°.
Вспомогательный угол в плане φ1 – это угол между проекцией вспомогательного лезвия на основную плоскость и направлением, обратным направлению движения подачи. Вспомогательный угол в плане в зависимости от условий обработки выбирается от 0 до 30°. Углом при вершине резца ε, называется угол между проекциями главного и вспомогательного лезвий на основную плоскость. Чем больше этот угол, тем лучше условия отвода тепла от лезвий.
Углом наклона глав ного лезвия (см. рис. 4.1, б) называется угол между главным лезвием и основной плоскостью Б – Б. Кроме углов резания различают аналогичные углы заточки резца.
Силы резания. Для отделения стружки режущий инструмент должен преодолеть силы сопротивления металла резанию, которые зависят от усилий, возникающих при деформировании и отделении срезаемого слоя, и сил трения стружки о переднюю поверхность и обрабатываемой детали о заднюю поверхность режущего инструмента. Равнодействующую всех сил сопротивления R (Н) принято называть силой сопротивления резанию или силой резания (рис. 4.1, в), которая является геометрической суммой сил резания Px, Py, Pz.
Знание сил резания необходимо для производства расчетов на жесткость и прочность инструментов, приспособлений и станков, а также для определения потребляемой мощности на резание.
Скорость резания. Скоростью резания v (см. рис. 4.1, в) называется линейная скорость перемещения точки поверхности резания относительно главного лезвия инструмента. Для станков с вращательным движением скорость резания (м/мин) определяется по формуле
V = π .D .n/1000, м/мин,
где D – максимальный диаметр поверхности резания, мм;
п – частота вращения детали, мин-1 (об/мин).
Мощность резания. Зная скорость резания и силу резания Pz , эффективную мощность (кВт), затрачиваемую на резание, можно определить по формуле
|

Для того чтобы узнать, какая мощность затрачивается электродвигателем (NЭ) для осуществления процесса резания, надо учесть к. п. д. станка.
Выбор режимов резания. Определение по формулам силы резания, оптимальной скорости резания и эффективной мощности, затрачиваемой на резание, занимает много времени и относительно сложно. Поэтому эти величины практически определяются по таблицам, приведенным в соответствующих справочниках.
Дата добавления: 2019-02-12; просмотров: 190; Мы поможем в написании вашей работы! |
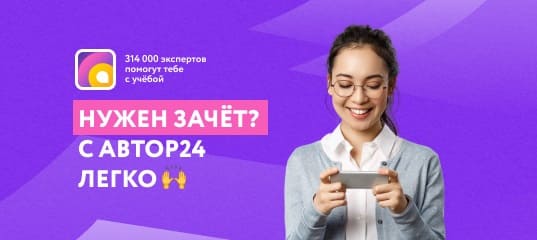
Мы поможем в написании ваших работ!