Средняя точность и шероховатость обработки резьбовых поверхностей
Способ обработки | Квалитет | Параметр шеро-ховатости Rа, мкм |
Круглыми плашками | 6g | 12,5…6,3 |
Метчиками | 6H | 6,3…3,2 |
Фрезерование: | ||
дисковыми фрезами | 6g | 6,3…1,6 |
гребенчатыми фрезами | 6g | 6,3…3,2 |
Точение: | ||
резцами | 4h | 3,2…0,8 |
гребенками | 6g | 6,3…0,8 |
Вращающимися резцами (вихревой метод) | 6g | 3,2…1,6 |
Самораскрывающимися головками | 4h | 6,3…1,6 |
Накатывание: | ||
плоскими плашками | 6g | 0,8…0,4 |
резьбонакатными роликами | 6g…4h | 0,8…0,2 |
Таблица 2.48
Средняя точность обработки зубчатых колес
Способ обработки | Квалитет | Параметр шеро-ховатости Rа, мкм |
Фрезерование: | ||
предварительное | 9…10 | 12,5…6,3 |
чистовое дисковой фрезой | 8…9 | 6,3…1,6 |
чистовое червячной фрезой | 7…8 | 6,3…1,6 |
Долбление чистовое | 6…8 | 3,2…0,8 |
Протягивание | 6…7 | 3,2…0,8 |
Строгание чистовое | 5…7 | 3,2…0,8 |
Шевингование | 6…7 | 1,6…0,4 |
Шлифование | 4…5 | 0,8…0,2 |
Пример. Рассчитать припуски на обработку и промежуточ-
ные предельные размеры для отверстия корпуса , показанного на рис. 2.3. На остальные обрабатываемые поверхности (2, 3, 4) назначить припуски и допуски по ГОСТ 1855–55.
Заготовка, представляет собой отливку 1-го класса точности, массой 3,5 кг. Технологический маршрут обработки отверстия состоит из двух операций: чернового и чистового растачивания, выполняемых при одной установке обрабатываемой детали. Базами для заготовки служат плоскость основания и два отверстия
. Схема установки при обра-ботке показана на рис. 2.3.
|
|
Расчет припусков на обработку отверстия приведен в табл. 2.49, в которой последовательно записывается технологический маршрут обработки отверстия и все значения элементов припуска.
Суммарное значение и Т,характеризующее качество поверхно-сти литых заготовок, составляет 600 мкм (табл. 2.34) После первого тех-нологического перехода T для деталей из чугуна исключается из расчетов, поэтому для чернового и чистового растачивания находим по табл. 2.36 только значения
(соответственно 50 и 20 мкм) и записываем их в рас-четную таблицу.
Суммарное значение пространственных отклонений для заготовки данного типа определится по формуле (2.179)
(2.179)
где – погрешность коробления отверстия,
– погрешность смещения.
Коробление отверстия следует учитывать как в диаметральном, так
и в осевом его сечении, поэтому
|
|
(2.180)
Удельное коробление отливок находим по табл. 2.38 (d и l – диаметр
и длина обрабатываемого отверстия).
Рис. 2.3. Корпус (чертеж и схема установки при обработке отверстия
)
При определении в данном случае следует принимать во внимание точность расположения базовых поверхностей, используемых при данной схеме установки и полученных на предыдущих операциях, относительно обрабатываемой в данной установке поверхности.
Так, если бы для получения размера (Б) при обработке плоскости основания 2 базой было отверстие, то последующая погрешность расположения отверстия относительно поверхности 2 определилась бы по вышеприведенной формуле для
.
Допуск на размер 47 для отливки 1-го класса 400 мкм. При однократном фрезеровании возможно получение 11-го квалитета с допуском 0,16 мм, следовательно, = (0,4 + 0,16) /2 = 0,28 мм.
Если же при обработке поверхности 2 базой служила какая-то наружная поверхность, следует учитывать смещение стержня, который формирует отверстие относительно наружной поверхности. Это смещение принято определять как отклонение от номинального размера в отливке, определяемое допуском на размер соответствующего класса точности.
|
|
Таблица 2.49
Расчет припусков и предельных размеров по технологическим переходам
на обработку отверстия корпуса (рис. 2.3 )
Технологические переходы обработки | Элементы | Расчет- | Расчет- | До-пуск | Предельный размер, | Предельные значения припусков, мкм | |||||
![]() | T | ![]() | ![]() | ![]() | ![]() | ![]() | ![]() | ||||
Заготовка | 600 | 294 | – | 48,090 | 400 | 47,69 | 48,09 | ||||
Растачивание: | |||||||||||
черновое | 50 | – | 15 | 127 | 2·920 | 49,930 | 160 | 49,77 | 49,93 | 1840 | 2080 |
чистовое | 20 | – | – | 6 | 2·66 | 50,062 | 62 | 50,00 | 50,06 | 130 | 230 |
Итого |
|
| 1970 | 2310 |
Эти же соображения следует принимать во внимание при определении погрешности размера (Г) в горизонтальной плоскости, т. е. также смещения положения отверстия заготовки относительно наружной поверхности. Так как в качестве базы при сверлении и развертывании отверстий использовалась боковая поверхность отливки, для определения погрешности расположения, обрабатываемого в данной установке отверстия
относительно базовых отверстий
следует принять смещение стержня относительно наружной поверхности отливки, определяемое допуском на размер (Г) отливки.
|
|
Учитывая, что суммарное смещение отверстия в отливке относительно наружной ее поверхности представляет геометрическую сумму
в двух взаимно перпендикулярных плоскостях, получаем
=284 мкм, (2.181)
где и
– допуски на размеры (Б) и (Г) по классу точности, соответствующему данной отливке.
Таким образом, суммарное значение пространственного отклонения заготовки:
=294 мкм. (2.182)
Остаточное пространственное отклонение после чернового растачивания = 0,05 ·
= 0,05 · 294= 15 мкм.
Погрешность установки при черновом растачивании
(2.183)
Погрешность базирования в данном случае возникает за счет перекоса заготовки в горизонтальной плоскости при установке ее на штыри приспособления. Перекос при этом происходит из-за наличия зазоров между наибольшим диаметром установочных отверстий и наименьшим диаметром штырей.
Наибольший зазор между отверстиями и штырями
, (2.184)
где – допуск на отверстие:
= 15 мкм = 0,015 мм;
– допуск на диаметр штыря:
= 15 мкм = 0,015 мм;
– минимальный зазор между ди-аметрами штыря и отверстия:
= 13 мкм = 0,013 мм.
Тогда наибольший угол поворота заготовки на штырях может быть найден из отношения наибольшего зазора при повороте в одну сторону от среднего положения к расстоянию между базовыми отверстиями:
. (2.185)
Погрешность базирования на длине обрабатываемого отверстия l
(2.186)
Погрешность закрепления заготовки (табл. 5.20) принимаем равной 120 мкм. Тогда погрешность установки при черновом растачивании
=127 мкм. (2.187)
Остаточная погрешность установки при чистовом растачивании
. (2.188)
Так как черновое и чистовое растачивание производится в одной установке, то
На основании записанных в таблице данных производим расчет минимальных значений межоперационных припусков, пользуясь основной формулой
(2.189)
Минимальный припуск под растачивание:
черновое
(2.190)
чистовое
(2.191)
Графа табл. 2.49 «Расчетный размер» (dр) заполняется, начиная с конечного (в данном случае чертежного) размера последовательным вычи-танием расчетного минимального припуска каждого технологического перехода.
Таким образом, имея расчетный (чертежный) размер, после последнего перехода (в данном случае чистового растачивания 50,062) для остальных переходов получаем:
для чернового растачивания dр1 = 50,062 – 0,132 = 49,930 мм;
для заготовки dр3 = 49,930 – 1,84 = 48,090 мм.
Значения допусков каждого перехода принимаются по таблицам
в соответствии с квалитетом того или иного вида обработки.
Так, для чистового растачивания значение допуска составляет 62 мкм (чертежный размер); для чернового растачивания δ = 160 мкм; допуск на отверстие в отливке 1-го класса точности по ГОСТ составляет δ = 400 мкм.
В графе «Предельный размер» наибольшее значение ( ) получается по расчетным размерам, округленным до точности допуска соответствующего перехода Наименьшие предельные размеры (
) определяются из наибольших предельных размеров вычитанием допусков соответствующих переходов.
Таким образом, для чистового растачивания наибольший предельный размер – 50,062 мм, наименьший – 50,062–0,062 =50 мм; для чернового растачивания наибольший предельный размер – 49,93, а наименьший – 49,93–0,16 = 49,77; для заготовки наибольший предельный размер – 48,09 мм, наименьший – 48,09–0,4 = 47,69 мм.
Минимальные предельные значения припусков равны разности наибольших предельных размеров выполняемого и предшествующего переходов, а максимальные значения
– соответственно разности наименьших предельных размеров.
|

Рис. 2.4. Схема графического расположения припусков и допусков
на обработку отверстия корпуса.
Тогда для чистового растачивания
50,06 – 49,93 = 0,13 мм = 130 мкм; (2.192)
50 – 49,77 = 0,23 мм = 230 мкм; (2.193)
для чернового растачивания
49,93 – 48,09 = 1,84 мм = 1840 мкм; (2.194)
49,77 – 47,69 = 2,08 мм = 2080 мкм. (2.195)
Все результаты произведенных расчетов сведены в табл. 2.49.
На основании данных расчета строим схему графического распо-ложения припусков и допусков по обработке отверстия (рис. 2.4).
Общие припуски и
определяем, суммируя промежуточные припуски, и записываем их значения внизу соответствующих граф:
= 130 + 1840 = 1970 мкм; (2.196)
=230 + 2080 = 2310 мкм; (2.197)
Общий номинальный припуск
=
+
= 1970 + 200 – 60 = 2110 мкм; (2.198)
=
= 50 –2,1 = 47,9 мм. (2.199)
Производим проверку правильности выполненных расчетов:
(2.200)
2080 – 1840 = 240 мкм;
400 – 160 = 240 мкм. (2.201)
На остальные обрабатываемые поверхности корпуса припуски и до-пуски выбираем по таблицам (ГОСТ 1885–55) и записываем их значения
в табл. 2.50.
Таблица 2.50
Припуски и допуски на обрабатываемые поверхности корпуса (рис. 2.3 )
по ГОСТ 1885–55 (размеры в мм)
Поверхность | Размер | Припуск | Допуск | |
табличный | расчетный | |||
1 | ![]() | 2 · 2,0 | 2 · 1,06 | ± 0,2 |
2 | ![]() | 2,0 | – | ± 0,3 |
3,4 | ![]() | 2,0 | – | ± 0,3 |
На рис. 2.5 показан чертеж заготовки корпуса с припусками на меха-ническую обработку.
|
|
|





|
|

|
|

Рис. 2.5. Заготовка корпуса с начисленными припусками и допусками
Пример. Рассчитать припуски на обработку и промежуточные предельные размеры на поверхность ведущей шестерни (рис. 2.6). На остальные обрабатываемые поверхности назначить припуски и допуски по таблицам ГОСТ 7505–74.
Заготовка – штамповка на ГКМ повышенной точности. Масса заго-товки 11,3 кг.
Технологический маршрут обработки поверхности состоит из обтачивания предварительного и окончательного и шлифования предварительного и окончательного. Обтачивание и шлифование производятся в центрах, схема установки показана на рис. 2.6.
|
|





|
|
|
|
|
|
|
|
|
|
|
|
|
|



|

Рис. 2.6. Шестерня ведущая (чертеж и схема установки
при обработке поверхностей ):
:
1…9 – обрабатываемые поверхности.
Таблица 2.51
Расчет припусков и предельных размеров по технологическим переходам
на обработку поверхности ведущей шестерни (рис. 2.6 )
Технологиче-ские переходы обработки поверхности | Элементы припуска, | Расчет- | Расчет- | До- | Предельный размер, | Предельные значения припусков, мкм | ||||
![]() | T | ![]() | ![]() | ![]() | ![]() | ![]() | ||||
Заготовка, h17 | 150 | 250 | 1820 | 65,27 | 3000 | 65,3 | 68,3 | |||
Обтачивание: | ||||||||||
предвари-тельное, h13 | 50 | 50 | 109 | 2 · 2220 | 60,83 | 400 | 60,9 | 61,3 | 4400 | 7000 |
окончатель-ное (h10) | 30 | 30 | 73 | 2 · 209 | 60,41 | 120 | 60,41 | 60,53 | 490 | 770 |
Шлифование: | ||||||||||
предвари-тельное (h7) | 10 | 10 | 36 | 2 · 133 | 60,14 | 30 | 60,14 | 60,17 | 270 | 360 |
окончатель-ное (h6) | 5 | 15 | 2 · 66 | 60,01 | 20 | 60,01 | 60,03 | 130 | 140 |
Так же как и в предыдущем примере, записываем технологический маршрут обработки в расчетную табл. 2.51. В таблицу также записываем соответствующие заготовке и каждому технологическому переходу значения элементов припуска. Так как в данном случае обработка ведется в центрах, погрешность установки в радиальном направлении равна нулю, что имеет значение для рассчитываемого размера. В этом случае эта величина исключается из основной формулы для расчета минимального припуска,
и соответствующую графу можно не включать в расчетную таблицу.
Суммарное отклонение
; (2.202)
;
; (2.203)
. (2.204)
Допуск на поверхности, используемые в качестве базовых на фрезерно-центровальной операции, определяем по ГОСТ 7505–74 для штамповок повышенной точности, для группы стали M1, степени сложности C2:
=3,0 мм; (2.205)
(2.206)
. (2.207)
Остаточное пространственное отклонение:
после предварительного обтачивания ;
после окончательного обтачивания ;
после предварительного шлифования .
Расчет минимальных значений припусков' производим, пользуясь ос-новной формулой
. (2.208)
Минимальный припуск:
под предварительное обтачивание
; (2.209)
под окончательное обтачивание
; (2.210)
под предварительное шлифование
; (2.211)
под окончательное шлифование
; (2.212)
Аналогично предыдущему примеру производим расчет по остальным графам таблицы.
Графа табл. 2.51 «Расчетный размер » заполняется, начиная с конечного (чертежного) размера, путем последовательного прибавления расчетного минимального припуска каждого технологического перехода:
; (2.213)
; (2.214)
; (2.215)
; (2.216)
Записав в соответствующей графе расчетной таблицы значения допусков на каждый технологический переход и заготовку, и графе «Наименьший предельный размер», определим их значения для каждого технологического перехода, округляя расчетные размеры увеличением их значений. Округление производим до того же знака десятичной дроби, с каким дан допуск на размер для каждого перехода. Наибольшие предельные размеры вычисляем прибавлением допуска к округленному наименьшему предельному размеру:
60,01 + 0,02 = 60,03 мм; (2.217)
60,14 + 0,03 = 60,17 мм; (2.218)
60,41 + 0,12 = 60,53 мм; (2.219)
60,9 + 0,4 = 61,3 мм; (2.220)
65,3 + 3,0 = 68,3 мм; (2.221)
Предельные значения припусков определяем как разность наибольших предельных размеров и
как разность наименьших предельных размеров предшествующего и выполняемого переходов:
; (2.222)
; (2.223)
; (2.224)
; (2.225)
; (2.226)
; (2.227)
; (2.228)
. (2.229)
Общие припуски и
рассчитываем так же, как и в предыду-щем примере, суммируя промежуточные припуски и записывая их значения внизу соответствующих граф.
Аналогично проверяется правильность произведенных расчетов
и строится схема графического расположения полей припусков и допусков, учитывая в данном случае, что построение производится на наружную, а не на внутреннюю поверхность.
Номинальный припуск в данном случае определяем с учетом несимметричного расположения поля допуска заготовки:
. (2.230)
где Тз и Тд – допуск на размер заготовки и детали соответственно.
Нижнее отклонение размера заготовкой находим по ГОСТ 7505–74, 700 мкм:
5290 + 700 — 20 =5970 мкм (2.231)
60,01 + 5,97 = 65,98 » 66 мм. (2.232)
На остальные обрабатываемые поверхности детали припуски и допуски принимаем по ГОСТ 7505–74 и записываем их значения в табл. 2.52.
Таблица 2.52
Припуски и допуски на обрабатываемые поверхности ведущей шестерни
(рис. 2.6) по ГОСТ 7505–74 (размер в мм)
Поверхность | Размер | Припуск | Допуск | |
табличный | расчетный | |||
1,8 | 276,5 | ![]() | – | + 1,8 – 1,0 |
2,6 | ![]() | | + 1,3 – 0,7 | |
3,5 | 68,5 | ![]() | + 1,3 – 0,7 | |
4 | ![]() | ![]() | + 1,3 – 0,7 | |
7 | ![]() | ![]() | + 1,3 – 0,7 | |
9 | 55,5 | 2,4 | + 1,3 – 0,7 |
Чертеж заготовки (штамповки на ГКМ) шестерни ведущей показан на рис. 2.7.
|
|
|
|
|
|
|
|
|
|








Рис. 2.7. Заготовка шестерни ведущей с начисленным припусками и допусками
Наряду с необходимыми исходными данными в начале расчета приводится схема установки обрабатываемой заготовки; на ней должны быть показаны поверхности, для которых рассчитываются или назначаются по таблицам припуски на обработку. На схеме условными обозначениями, принятыми для технологических операционных эскизов, показывается также базирование заготовки в данной установке.
В один расчет можно включать только последовательно выполняемые переходы при одной и той же (неизменной) установке обрабатываемой заготовки. В том случае, если обработка даже одной поверхности производится за несколько различных установок, необходимо для каждой установки, показав ее схему, произвести самостоятельный расчет.
В заголовках вертикальных граф расчетной таблицы, как показано
в приведенном примере формуляра, достаточно записать только индексы рассчитываемых параметров, например, .
Цифровые индексы составляющих элементов припуска по переходам, например, ,
и другие, соответствуют порядковым номерам выполняемых переходов.
В этом случае, когда расчет какого-то элемента, как, например, , представляет несложное вычисление суммы или разности двух-трех составляющих, то в формуляре следует привести только формулу в общем виде, а расчет при наличии исходных данных, уже записанных в таблицу для каждого из переходов в формуле можно произ-водить, записывая только результаты расчета в соответствующую графу таблицы.
Номинальные значения припусков рассчитываются только для сопоставления с табличными или производственными величинами.
При расчете номинальных припусков значения ,
и другие заготовки берутся из таблиц соответствующих стандартов, а для штамповок рассчитываются по приводимым выше формулам.
Эскиз заготовки с начисленными припусками и допусками дан в выше приведенных расчетах и формуляре в качестве примера, который может быть использован для оформления чертежа заготовки.
Дата добавления: 2019-02-12; просмотров: 583; Мы поможем в написании вашей работы! |
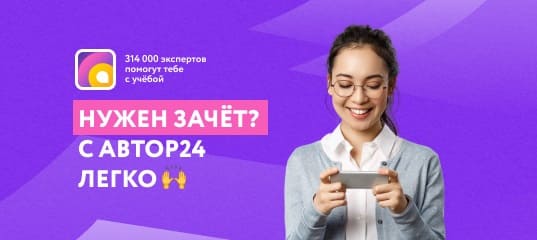
Мы поможем в написании ваших работ!