Конструкционные стали, особенности термической обработки.
Конструкционные стали применяются для деталей машин конструкций и сооружений.
По сравнению с углеродистыми имеют более лучшие механические свойства: лег. эл. увеличивают закаливаемость и прокаливаемость, измельчают зерно, повышают мех. свойства деталей в отпущенном состоянии. Основные легирующие элементы: хром, никель, магний. Добавочные: вальфрам, молибден, титан. Углерода 0,4-0,5% стали являются доэвтектоидными.
Конструкционные подразделяются на:
1)строительные – до 0,3% углерода, до 4% легир. эл., применение – сооружение мостов, каркасов зданий;
2)машиностроительные: а)цементируемые (углерода до 0,3%, легир. эл. до 5-6%), б)улучшаемые (углерода 0,5-0,6%, легир. эл. 8-10%), в)инструментальные (углерода 0,7-0,8%, легир. эл. 2-10-20%). Инструментальные подразделяются на стали для режущего инструмента, быстрорежущие, штамповые.
1) Низколегированные низкоуглеродистые стали – применяются для вагоностроения, трубопроводов. В большинстве случаев поступают в нормализованном состоянии
2) Цементуемые стали. Легированные элементы позволяют иметь в середине высокий предел текучести и твёрдый цементуемый слой. Углерода менее 0,3%. Подразделяются на: а) хромистые стали (15Х, 15ХА) в этих сталях сильно развит распад аустенита(промежуточное превращение). После цементации сердцевина имеет более мелкое строение (более мелкое зерно). б) хромоникелевые стали. Применяются для изделий крупного сечения сильно нагруженных. Легирующие элементы увеличивают прокаливаемость стали. Устойчивость переохлажденного аустенита позволяет охлаждать сталь в масле после цементации (пр. 12ХН3А, 20Х2Н4А). в) хромомарганцевые стали они являются заменой дорогим сталям. Их недостатком является малая устойчивость против перегрева (пр. 18ХГТ)
|
|
3) Улучшаемые стали имеют высокий предел текучести и малую чувствительность к концентраторам напряжений, высокий запас вязкости. Бывают: а) хромистые улучшаемые (30Х), б)хромоникелевые (45ХН), применяются для сильно нагруженных и крупных деталей, после отпуска должны быстро охлаждаться (отпуск 550-560С). Все легирующие элементы увеличивают прокаливаемость.
Термическая обработка конструкционных сталей:
1) Низкоуглеродистые конструкционные стали следует подвергать закалке с низким отпуском, закалку проводят при температуре чуть выше Ас3 с последыющим охлаждением в масле. После закалки подвергают низкому отпуску при температуре 150С, получаемая структура мартенсит отпущенный.
2) Среднеуглеродистые стали(0,3-0,45% углерода) подвергают закалке(850С с последующим охлаждением в масле) с высоким отпуском(550-560С) – улучшение, полученная структура – сорбит отпуска.
|
|
Отпускная хрупкость легированных сталей.
Отпускная хрупкость – охрупчивание стали при некоторых условиях. Понижение вязкости при этом обусл. повышением температуры перехода в хладноломкое состояние.
С повышением температуры отпуска при определённых значениях сталь переходит в хрупкое состояние – отпускная хрупкость.
Отпускная хрупкость первого рода – остаточный аустенит превращается в мартенсит, появляется при 300С, является необратимой, поэтому стали от 250-350С не подвергаются отпуску.
При отпуске при температуре выше 600 обнаруживается отпускная хрупкость второго рода, она обратима, если обнаруживается хрупкость второго рода, то сталь повторно подвергается отпуску с быстрым охлаждением. Дополнительно вводится вольфрам, ванадий, молибден для уменьшения отпускной хрупкости. Характерная особенность: появляется в рез.медленного охлаждения при отпуске . Возникает у углеродистых сталей, а также при легировании хромом, никелем, марганцем.
Инструментальные стали.
Должны обладать высокой твёрдостью, износостойкостью.
1) легированные стали. По сравнению с углеродистыми имеют большую прокаливаемость и износостойкость. а)хромистые стали, б)хромокремнистые стали дают углубление прокаливаемости и снижение коробления изделия, в)хромомарганцевые, г)стали ледебуритного класса температура закалки 1150С
|
|
Так как при высоких температурах карбиды будут растворятся в аустените после закалки будет насыщаться углеродом мартенсит. Структура после закалки мартенсит+аустенит остаточный+карбиды. Аустенит остаточный переходит в мартенсит, значит повышает содержание мертенсита, значит повышается твёрдость. Делают отпуск на вторичную твёрдость. Если в процессе закалки размеры уменьшились, то делается отпуск при 520С, это совпадает с превращением МАУ—М. Если размеры увеличились, то делается отпуск при температуре 350С. Это совпадает с превращением тетрагонального мартенсита в отпущенный
2) быстрорежущие. Применяются для изготовления инструмента, работающего при высоких скоростях резания, обладают высокой износостойкостью и красностойкостью(способностью сохранять твёрдость в нагретом состоянии). Эти стали легируют элементами задерживающими укрупнение карбидов и распад мартенсита. Происходит самоотпуск в режиме резанья в режущей кромке, хром, вальфрам, ванадий, молибден - легирующие элементы(Р18 – сталь быстрорежущая ледебуритного класса при кристаллизации образуется эвтектика – ледебурит.) Лед.=Аус.+карбиды. Карбид – Fe2W2C, Ау--П+К
|
|
Для получения максимальной красностойкости закалку следует проводить при максимально возможной температуре 1200С, выдержка при закалке способствует переводу карбидов в раствор, охлаждение следует проводить в масле, чтобы не выделялись карбиды. Отпуск можно проводить двумя способами: 1) трёхкратный отпуск при 560С в течении часа каждый, аустенит остаточный примерно 5%. 2)после закалки следует обработка холодом -80С, после этого отпуск при 560С в течении 1часа, при этом дополнительно образуется около 10-15% мартенсита.
Дата добавления: 2019-02-12; просмотров: 198; Мы поможем в написании вашей работы! |
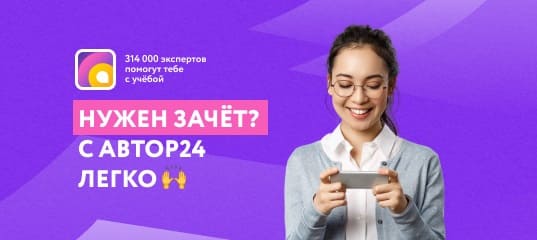
Мы поможем в написании ваших работ!