Fig. Hydraulic downhole pump
High pressure power fluid is directed down the tubing to the nozzle where the pressure energy is converted to velocity head. The high velocity- low pressure power fluid entrains the production in the throat of the pump. A diffuser then reduces the velocity and increases the pressure to allow the coming-led fluid to low to the surface.
Fig. Cutaway drawing of a jet pump
Advantages:
· Free pump- being able to circulate the pump in and out of the well;
· Deep wells- positive displacement pumps are capable of pumping depths up to 17.000ft and deeper (for jet pumps this depth is limited to around 9000ft);
· Speed control- by changing the power fluid rate to pumps, production can be varied from 10 to 100% of pump capacity;
· Cooked wells- deviated wells typically present no problems to hydraulic free pumps;
· Sand production- jet pumps as they have no moving parts, can handle sand and other solids very well;
· Viscous oils- positive displacement pumps can handle viscous oils very well;
· Corrosion- corrosion inhibitors can be injected into the power fluid for corrosion control.
Disadvantages:
· Power fluid cleaning- removing solids from the power fluid is very important for positive displacement pumps. Maintenance of surface plunger pumps is also affected by solids in the power fluid;
· Pump life- positive displacement pumps, on average, have shorter life between repairs than jet, sucker rod and electrical submersible pumps;
· Skilled personnel- positive displacement pumps generally require more highly skilled operating personnel, or perhaps, just more attention. First, pump speed needs to be monitored daily and not allowed to become excessive. Secondly, power fluid cleaning systems need frequent checking, and action taken, to keep them operating at their optimum effectiveness.
3. ESP
Fig. Electrical submersible pump installation
Electric Submersible Pumps consist of three parts, a downhole pump and motor, electric power cable from the pump to the surface and surface controls to operate the pump. The centrifugal pump (the part that introduces energy to the fluid) attaches to the bottom of the production tubing and couples to a submersible electric motor that turns the pump. The power cable connects the surface control system to the downhole motor. ESP’s are a very versatile artificial lift method and can be found in operating environments all over the world. They can handle a very wide range of flowrates (from 200 to 90,000 bpd) and lift requirements (from virtually zero to 10,000 ft of lift). They can be modified to handle contaminants commonly found in oil, aggressive corrosive fluids such as H2S and CO2, abrasive contaminants such as sand, exceptionally high downhole temperatures, and high levels of gas production. Increasing water cut has been shown to have no significant detrimental effect on the ESP performance. It is possible to locate them in vertical, deviated, or horizontal wells, but it is recommended for optimum run-life performance they are located in straight section of casing.
|
|
The selection of the submersible pump as the most economical method of lift is as following:
· Adaptable to highly deviated wells;
· Permit use of minimum space for subsurface controls and associated producing facilities. Method is quiet, safe and sanitary for acceptable operations in an offshore and environmentally conscious area;
· Permits placing well on production immediately after drilling and completion;
· Permits continued well production even while drilling and working over wells in immediate vicinity.
Some of the weaknesses of the ESP are as following:
· Will tolerate minimal percents of solids production;
· Costly pulling operations to correct downhole failures (DHF);
· While on DHF there is a loss of production; during time well is covered by drilling operations in immediate vicinity;
· Not particularly adaptable to low volumes.
4. Gas Lift dominates the Gulf Coast of the USA as a means of artificial lift and is used extensively around the world. Most of these wells are on constant flow gas lift. Thus the following questions arise: Why is gas lift chosen? Where do you use constant flow? When do you select intermittent lift?
Constant flow gas lift is recommended for high volume and high static bottom hole pressure wells where major pumping will occur. Constant flow gas lift uses the produced gas with additional injection allowing the producing gradient to be lowered so that the well will “flow” much better. Constant flow gas lift imposes a relatively high back pressure on the reservoir and is at best only moderately efficient as compared with most pumping methods.
|
|
What are the strengths of constant flow gas lift?
· Gas lift is the best artificial lift method for handling sand or slid materials;
· Deviated or crooked holes can be gas lifted with only minor lift problems;
· Gas lift permits the use of wireline equipment and such equipment is easily and economically serviced;
· Normal design leaves the tubing full opening;
· In gas lift, less injection gas is required;
· Gas lift is flexible- a wide range of volumes and lift depths can be achieved with essentially the same well equipment;
· A central gas lift system can be easily used to service many wells or operate an entire field;
· Gas lift has a low profile;
· Well subsurface equipment is relatively inexpensive and repair and maintenance of this subsurface equipment is normally low. The equipment is easily pulled and replaced. Also major well workover occur infrequently;
· Installation of gas lift is compatible with subsurface safety valves and other surface equipment;
· Gas lift tolerate some bad design assumptions and still work.
What are the limitations?
· Relatively high back pressure may seriously restrict production in continuous gas lift;
· Gas lift is relatively inefficient, often re-resulting in large capital investments and high energy operating costs;
· Adequate gas supply is needed throughout the life of the project;
· Operation and maintenance of compressors ca be expensive;
· Good data are required to make a good design.
SELECTION OF ARTIFICIAL LIFT METHOD | |
artificial lift | механизированная добыча нефти |
electric submersible pump | установка электроцентробежного насоса (ЭЦН) |
hydraulic pump | гидравлический насос |
sucker rod pump | штанговая глубинонасосная установка (ШНГУ) |
jet pumping | струйный насос |
gas lift | газлифт |
well productivity | продуктивность скважины |
gas-liquid ratio (glr) | газожидкостный фактор |
reservoir performance | поведение пласта |
stripper well | малодебитная (истощенная) скважина |
sucker rod string | штанга глубинного насоса |
pump | насос |
beam pumping (pump jack \ pumping unit) | балансирный станок-качалка (ШГНУ) |
back pressure | обратное давление \ противодавление |
deviated (crooked) hole (well) | наклонно-направленная скважина |
well workovers | капитальный ремонт скважины |
downhole failure (DHF) | повреждение забоя скважины |
displacement pump | поршневой насос |
pump plunger | плунжер насоса |
pump piston | поршень |
nozzle | насадка |
throat (pump) | горловина |
bottomhole pressure (BHP) | забойное давление |
maintenance | техническое обслуживание |
|
|
Oil extraction and recovery
Primary recovery
If the underground pressure in the oil reservoir is sufficient, then this pressure will force the oil to the surface. Gaseous fuels, natural gas or water are usually present, which also supply needed underground pressure. In this situation, it is sufficient to place a complex arrangement of valves (the Christmas tree) on the well head to connect the well to a pipeline network for storage and processing.
Usually, about 20% of the oil in a reservoir can be extracted using primary recovery methods.
Secondary recovery
Over the lifetime of the well the pressure will fall, and at some point there will be insufficient underground pressure to force the oil to the surface. If economical, as often is, the remaining oil in the well is extracted using secondary oil recovery methods (see: energy balance and net energy gain).
|
|
Secondary oil recovery uses various techniques to aid in recovering oil from depleted or low-pressure reservoirs. Sometimes pumps, such as beam pumps and electrical submersible pumps (ESPs), are used to bring the oil to the surface. Other secondary recovery techniques increase the reservoir's pressure by water injection, natural gas re-injection and gas lift, which injects air, carbon dioxide or some other gas into the reservoir.
Together, primary and secondary recovery generally allows 25% to 35% of the reservoir's oil to be recovered.
Tertiary recovery
Tertiary oil recovery reduces the oil's viscosity to increase oil production. Thermally enhanced oil recovery methods (TEOR) are tertiary recovery techniques that heat the oil and make it easier to extract. Steam injection is the most common form of TEOR, and is often done with a cogeneration plant. In this type of cogeneration plant, a gas turbine is used to generate electricity and the waste heat is used to produce steam, which is then injected into the reservoir. This form of recovery is used extensively to increase oil production in the San Joaquin Valley, which has very heavy oil, yet accounts for 10% of the United States' oil products. In-situ burning is another form of TEOR, but instead of steam, some of the oil is burned to heat the surrounding oil. Occasionally, detergents are also used to decrease oil viscosity as a tertiary oil recovery method.
Tertiary recovery allows another 5% to 15% of the reservoir's oil to be recovered.
Tertiary recovery begins when secondary oil recovery techniques are no longer enough to sustain production, but only when the oil can still be extracted profitably. This depends on the cost of the extraction method and the current price of crude oil. When prices are high, previously unprofitable wells are brought back into production and when they are low, production is curtailed.
Enhanced oil recovery
Enhanced Oil Recovery (EOR) is a generic term for techniques for increasing the amount of oil that can be extracted from an oil field. Using EOR, 30-60 %, or more, of the reservoir's original oil can be extracted compared with 20-40% using primary and secondary recovery.
Enhanced oil recovery is also called improved oil recovery or tertiary recovery (as opposed to primary and secondary recovery).
// How it works
This improved extraction is achieved by either gas injection, thermal recovery, or chemical injection.
Gas injection is the most commonly used EOR technique. Here, gas such as carbon dioxide (CO2), natural gas, or nitrogen is injected into the reservoir whereupon it expands and thereby pushes additional oil to a production wellbore, and moreover dissolves in the oil to lower its viscosity and improves the flow rate of the oil. The prospects of using CO2 has gathered much interest, as this would allow storing it away from the atmosphere and hence a tool to combat global warming. However, the extra oil extracted would, when combusted, add additional CO2 to the atmosphere, partially or completely offsetting the benefits of the removed CO2. Oil displacement by CO2 injection relies on the phase behaviour of CO2 and crude oil mixtures that are strongly dependent on reservoir temperature, pressure and crude oil composition. These mechanisms range from oil swelling and viscosity reduction for injection of immiscible fluids (at low pressures) to completely miscible displacement in high-pressure applications. In these applications, more than half and up to two-thirds of the injected CO2 returns with the produced oil and is usually re-injected into the reservoir to minimize operating costs. The remainder is trapped in the oil reservoir by various means.
Other techniques include thermal recovery (which uses heat to improve flow rates), and, more rarely, chemical injection, where polymers are injected to increase the effectiveness of waterfloods, or the use of detergent-like surfactants to help lower the surface tension that often prevents oil droplets from moving through a reservoir.
Economic costs and benefits
The injection of gas costs money — in the case of CO2 typically between 0.5-8.0 US$ per tonne of CO2. The increased extraction of oil on the other hand, is an economic benefit with the revenue depending on prevailing oil prices. Onshore EOR have paid in the range of a net 10-16 US$ per tonne of CO2 injected for oil prices of 15-20 US$/barrel. With oil prices at a currently more realistic level of 50 US$/barrel, the economic benefit rises to about 30 US$ per tonne CO2.
Examples of current EOR projects
In Canada, a CO2-EOR project has been established by EnCana at the Weyburn Oil Field in southern Saskatchewan. The project is expected to inject a net 18 million ton CO2 and recover an additional 130 million barrels of oil, extending the life of the oil field by 25 years [1]. When combusted, this extra volume of oil will produce nearly 60 million ton CO2, so in this case carbon capture and storage in combination with EOR leads to more CO2 emissions than without injection of CO2. Since CO2 injection began in late 2000, the EOR project has performed largely as predicted. Currently, some 1600 m3 (10,063 barrels) per day of incremental oil is being produced from the field.
Дата добавления: 2019-01-14; просмотров: 266; Мы поможем в написании вашей работы! |
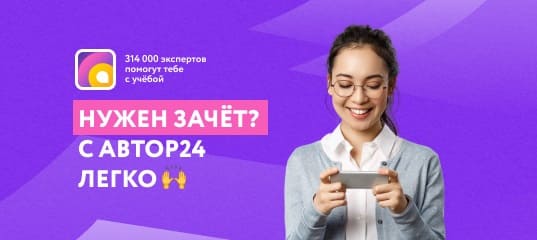
Мы поможем в написании ваших работ!