Управление фазой распределительного вала
Фазеры распределительных валов производятся в больших количествах. Приняты гидравлические системы, одновременно развиваются электромеханические системы. Последние обеспечивают оптимальную скорость и изменчивость (рис. 5). Однако электромеханические системы также более дороги. Имея это в виду, Schaeffler не только стремится к началу производства для электромеханических фазированных систем Cam, запланированных на 2015 год; мы также постоянно оптимизируем производительность гидравлических систем.
Скорость регулирования фазных блоков гидравлического распределительного вала в значительной степени определяется характеристиками масляного контура. За последние несколько лет давление масла в двигателе было последовательно снижено для снижения энергопотребления насосов моторного масла. Низкое давление масла является сложным ограничением, когда речь идет о разработке новых и разрабатываемых существующих фаз фаз газораспределительного механизма. Это связано с тем, что чем ниже давление масла, тем меньше энергии для регулировки распределительного вала.
Поэтому Schaeffler впервые демонстрирует фазер со вторичным масляным резервуаром: дополнительный масляный резервуар расположен в дополнительных отверстиях в роторе фазного ротора распределительного вала - другими словами, рядом с масляными камерами, которые вызывают фазирование, когда они заполняются. Этот резервуар не находится под давлением, он улучшает скорость регулировки, обеспечивая объем, который не должен подаваться масляным насосом
|
|
Переключающие элементы
Другим способом повышения изменчивости клапанной системы являются переключающие элементы, которые изменяют подъем отдельных клапанов. Такие системы нацелены, в частности, на деактивацию цилиндров, частичное демпфирование и внутреннюю рециркуляцию выхлопных газов и доступны в ряде конструкций (рисунок 6):
- Простейший пример включает только закрытие отдельных клапанов - и, следовательно, цилиндров - через переключаемый элемент поворота; эти типы элементов успешно используются на рынке в течение нескольких лет.
- Переключаемые последователи пальцев или толкатели ковша используются также для двухступенчатого переключения подъема и, следовательно, для частичного демплинга. При использовании скользящей кулачковой системы даже можно изменить ход клапана в три этапа. 3-х ступенчатые переключающие системы либо объединяют деактивацию цилиндра с переключением между двумя дискретными ходами, либо позволяют переключаться между тремя ходами. Schaeffler разрабатывает механическое решение для трехступенчатого переключения, которое должно быть достаточно прочным для удовлетворения всех стандартных требований, касающихся срока службы клапанов.
|
|
- Используя переключаемый следящий палец, второй ход клапана может выполняться вне указанного контура первого хода. Это позволяет выполнять рециркуляцию внутреннего рециркуляции отработавших газов путем повторного нажатия отходящего газа во впускной коллектор или путем повторного дыхания выхлопных газов, открывая выпускной клапан второй раз во время фазы всасывания. Schaeffler адаптировал такую систему для японского дизельного двигателя.
Полностью изменяемый клапан
Электромеханические или электрогидравлические системы с полным переключением клапанов обеспечивают высокую степень изменчивости, последние уже находятся в серийном производстве. Электрогидравлические системы все еще приводятся в движение распределительным валом. Электромагнитные системы без распределительного вала были предметом исследований в течение некоторого времени, но они еще не введены, что объясняется не только требовательными требованиями к электропитанию. Распределительный вал также действует как предохранительный элемент, предотвращая неисправные действия и, следовательно, клапан и поршень входят в контакт.
|
|
В 2009 году Schaeffler начал серийное производство электрогидравлической системы клапанов UniAir. Эта система Schaeffler включает:
- Электрогидравлический приводной модуль
- программное обеспечение, необходимое для управления фазами газораспределения; это программное обеспечение интегрировано в блок управления двигателем клиента
- Набор данных калибровки для соответствующего приложения
С 2009 года эта система адаптирована для различных производственных двигателей мощностью от 0,9 до 2,4 л и поставляется в больших объемах для клиентов в Европе и Северной и Южной Америке.
UniAir не только обеспечивает бесступенчатую настройку подъема клапана; он также позволяет в значительной степени свободную конфигурацию события подъема клапана в пределах максимального контура, определенного огибающей распределительного вала. Таким образом, деструктирование возможно в широких диапазонах карт двигателя (рисунок 7). Это приводит к снижению расхода топлива до 15% в новом европейском вождении (NEDC).
Будущие поколения системы UniAir представят новые функции, которые будут представлены более подробно на симпозиуме Schaeffler 2014 [4]. Одной из примечательных функций является индивидуальное управление двумя впускными клапанами. Такая активация позволяет генерировать определенное движение заряда (особенно при низких нагрузках), тем самым значительно увеличивая эффективность сгорания. На рисунке 8 показаны асимметричные кривые подъема клапанов, которые разрешены индивидуальным управлением.
|
|
С точки зрения Шеффлера, свобода в конструкции процесса горения, предоставляемая системой UniAir, может применяться ко всем сегментам транспортных средств. Низкозатратные двигатели с небольшим количеством цилиндров могут извлечь выгоду из увеличения крутящего момента, одновременно снижая удельный расход топлива. В этом сегменте транспортного средства соотношение затрат и выгод намного превосходит другие меры, такие как добавление турбонаддува и прямого впрыска выхлопных газов. Большие двигатели особенно полезны для демплинга в диапазоне нагрузки деталей. Новые функции также могут поддерживать будущие процессы горения, которые могут использовать преимущества чрезвычайно быстрого механизма работы системы.
Уменьшение потерь на трение
Снижение потерь на трение всегда было важной целью развития конструкции двигателя. В прошлом основное внимание уделялось внутреннему трению в цилиндре, в частности трению между соединением поршневого и поршневого кольцевых цилиндров. В связи с все более жестким законодательством по СО2, все другие источники потерь также изучаются в настоящее время. Это относится, в частности, к
- Коленчатый вал
- Направляющий клапан
- Балансировочные валы
- Приводы распределительных валов и вспомогательного оборудования
- Убытки, вызванные работой хладагента и масляного насоса
В целом, эти значения трения составляют около 50% потерь на трение в среднем двигателе внутреннего сгорания (рис. 9). Кроме того, процесс нагрева двигателя становится более важным из-за взаимосвязи между трением и температурой масла. Эта потеря мощности напрямую влияет на стандартное потребление из-за секции холодного запуска в новом европейском вождении (NEDC).
Привод клапанов отвечает за особенно высокую долю потерь на трение, возникающих при низких оборотах двигателя. За последние 20 лет в этой области был достигнут значительный прогресс за счет трибологической оптимизации ковшовых толкателей; среднее эффективное значение трения было уменьшено примерно на 50% (рис. 10). В то же время были установлены следящие устройства для управления клапанами - они соединяют компенсаторы зазора гидравлического клапана с изначально низким трением. Для современных двигателей - как бензина, так и дизельного топлива - все чаще, с высокими удельными номинальными значениями мощности и несколькими цилиндрами устанавливаются балансировочные валы. Трение на подшипнике вала особенно важно из-за его высокой скорости (двойная скорость коленчатого вала в четырехцилиндровом двигателе). Переключение на роликовый подшипник при одновременном проектировании более легких компонентов (рис. 5 в [2]) может снизить выбросы CO2 на автомобиле до 2%. В четырехцилиндровом двигателе этот вид раствора может уменьшить вес примерно на 0,5 кг на вал / 1 кг на систему. Значительно меньшие потери на трение также могут быть достигнуты путем поддержки распредвала на роликовых подшипниках (рис. 11). Однако, если этот подход сделан, важно рассмотреть концепцию сборки головки блока цилиндров.
Основная цель приводов вспомогательного оборудования - обеспечить бесперебойную работу на протяжении всего срока службы. Передача постоянно растущих крутящих моментов и номиналов мощности приводит к увеличению преднатяжений в ременном приводе, что приводит к увеличению потерь мощности. В то же время динамические амплитуды в ленточном приводе возрастают, поскольку двигатели имеют меньшее количество цилиндров и более высокое среднее эффективное давление; это приводит к высоким вращательным неоднородностям. Инновационные натяжители ремней и развязки коленчатого вала, разработанные Schaeffler, способны надежно переносить увеличенный крутящий момент, одновременно минимизируя потери мощности [5].
Дата добавления: 2019-01-14; просмотров: 79; Мы поможем в написании вашей работы! |
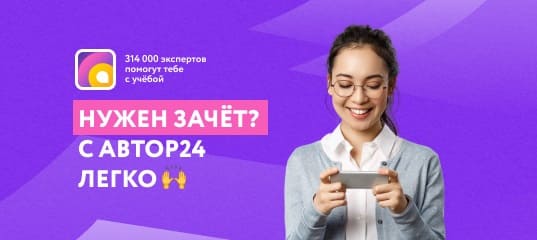
Мы поможем в написании ваших работ!