Сборка узлов с применением пластмассовых компенсаторов
Одним из направлений совершенствования технологии сборки машин и механизмов является создание компенсаторов погрешностей изготовления деталей и узлов, позволяющих значительно сократить, а часто и полностью устранить пригоночные работы. Возможности обеспечения точности взаимного расположения деталей и узлов при их сборке методом регулирования могут быть значительно расширены за счет использования в качестве компенсатора погрешностей пластмассовой прослойки.
Сущность этого метода состоит в следующем. При сборке узла или машины в зазоры, образовавшиеся или специально создаваемые между сопрягаемыми поверхностями деталей после их взаимной выверки, нагнетается пластмасса в вязкотекучем состоянии. Последняя, выбирая зазоры, воспринимает на себя погрешности механической обработки и сборки деталей и после затвердевания превращается в компенсатор требуемого размера и формы. Весьма важно, что компенсация погрешностей при этом происходит одновременно во всех плоскостях, т.е. в пространстве.
Новый метод позволяет повысить точность сборки узлов и машин на 20…25% без повышения точности обработки деталей. При этом следует особо отметить, что контактная поверхность в сопряжении деталей увеличивается, так как пластмасса в вязкотекучем состоянии хорошо заполняет макро- и микронеровности. Вследствие этого жесткость стыка деталей, несмотря на то, что механические свойства пластмасс ниже соответствующих характеристик материалов деталей, не снижается, а повышается по сравнению с жесткостью стыков деталей, собираемых с применением известных компенсаторов (например, прокладок, колец и т.д.). В то же время, наличие упругой прослойки в сопряжениях деталей благоприятно сказывается на снижении вибраций и уровня шума.
|
|
Наряду с этим, метод сборки с применением пластмассовых компенсаторов является и более экономичным, так как он позволяет значительно сократить объем регулировочных работ, имеющих место при использовании как непрерывных, так и ступенчатых компенсаторов.
Технологический процесс сборки при этом включает следующие операции:
1. подготовку сопрягаемых поверхностей деталей к сборке;
2. установку и выверку деталей и узлов;
3. заполнение зазоров пластмассой;
4. обеспечение условий полимеризации в зазоре;
5. закрепление деталей и узлов после нагнетания отверстия пластмассовой прослойки;
6. контроль качества компенсатора.
Для ускорения полимеризации пластмассы и контроля качества заполнения зазоров эффективно использовать ультразвуковой метод. При этом для ускорения процесса полимеризации рекомендуются частоты 25...30 МГц, а для контроля качества заполнения зазоров – частоты 1,8 ... 2,5 мГц.
|
|
Вопросы для самоконтроля
1. Для какой цели используются компенсаторы при сборке машин?
2. Сущность метода сборки с пластмассовым компенсатором.
3. Технологический процесс сборки соединений с пластмассовым компенсатором.
Способы уплотнения соединений
Во всех соединениях, ' подверженных в процессе работы воздействию гидравлической среды (жидкого топлива, масла, воды, воздуха и т. п.) и газов, при сборке должна быть обеспечена герметичность стыков. Плотность, или герметичность, неподвижных соединений может быть достигнута либо непосредственным плотным прилеганием друг к другу опорных поверхностей, либо с помощью специальных прокладок в стыке.
Основное преимущество беспрокладочных соединений состоит в том, что при их сборке не нужно учитывать изменение толщины прокладки; невозможны, кроме того, перекосы фланцев, достигается большая прочность и жесткость соединения. Повторная сборка беспрокладочных соединений производится сравнительно легко и без всяких повреждений. Одновременно необходимость точной пригонки сопрягаемых поверхностей и чувствительность их ко всяким механическим повреждениям делают соединения этого вида трудоемкими и относительно дорогими.
|
|
В отдельных случаях для создания лучшего уплотнения плоских стыков применяют специальные мастики (герметики), которые с помощью кисти наносятся тонким слоем на опорные поверхности.
Если нет возможности или просто затруднительно получить достаточную плотность прилегания опорных поверхностей путем механической обработки, то под плоскости фланцев кладут прокладки из легко деформирующегося материала. Этот прокладочный материал должен быть эластичным, чтобы он мог заполнить все неровности на стыковых поверхностях, стойким и непроницаемым (не должен быть подвержен разъеданию соприкасающейся с ним жидкостью, разрыву и выдавливанию).
Прокладки бумажные представляют собой картон или бумагу (толщиной от 0,05 до 0,5 мм), пропитанные смесью касторового масла с глицерином. Если опорные поверхности тщательно обработаны, то использование этих прокладок дает хорошие результаты уплотнения при работе с насыщенным паром и сжатым воздухом при температуре до 200°, а также с маслом и бензином.
Бумажные прокладки широко применяют в трубопроводах при соединении картеров и корпусов, в крышках цилиндров, бензомаслопроводах и т. п.
|
|
Прокладки паронитовые, представляющие собой асбестовое волокно, пропитанное специальной резиновой смесью, изготавливают в виде пластин толщиной от 0,5 до 1 мм. Они являются хорошим средством уплотнения в воде, паротрубопроводах и бензо-маслопроводах; используют их при соединении крышек с картерами и корпусами механизмов машин.
Прокладки асбестовые, употребляемые в виде листов или шнура, являются вполне пригодными для уплотнения горячих соединений (находящихся при высокой температуре). К недостаткам асбеста следует отнести и его незначительную механическую прочность и свойство прилипать к металлу, вследствие чего при повторной сборке соединений нужно зачищать опорные поверхности.
Прокладки из армированного полотна представляют собой металлическую ткань, оплетенную асбестовой пряжей, пропитанную графитом и отделанную специальной вулканизированной резиной. Толщина прокладок от 0,5 до 2 мм. Применяют эти прокладки в соединениях, подверженных при высоких температурах воздействию бензина, масла и воды. К недостаткам прокладок из армированного полотна следует отнести их сравнительную дороговизну.
Прокладки резиновые являются самым лучшим средством для достижения водонепроницаемости соединений. Прокладки изготавливают или в виде шнура, или в виде пластин толщиной от 2 до 3 мм. Исходный материал при производстве резиновых прокладок – это плотная резина без воздушных пузырьков и газовых включений. Различают резину эластичную, применяемую в водо- и воздухопроводах при температуре от 30 до 60°, теплостойкую, применяемую в тех же условиях, но уже при высоких температурах (до 140°), и маслобензостойкую, используемую при средних температурах (до 80°).
В случае высокого давления для всех видов резиновых прокладок в опорных поверхностях соединений предусматривают специальные проточки, предохраняющие прокладки от разрыва и выдавливания (рисунок 8.36,а).
![]() | 1,2 – соединяемые детали; 3 – болт; 4 – гайка; 5 – прокладка; 6 – прокладка П-образная Рисунок 8.36 – Уплотнения стыков резиновыми прокладками |
В настоящее время для уплотнения гладких стыков труб нередко применяют мягкие кольца с П-образным профилем изготовленные из маслостойкого материала (рисунок 8.36,б). Кольца свободно вкладывают в выточку на сопрягаемых поверхностях. При этом значительно упрощаются технология обработки стыка и сборка трубопроводов, вполне обеспечивается надежность соединений при давлении до 25 МПа.
Герметичности соединений, работающих в условиях высокого давления, достигают использованием жестких прокладок, способных противостоять внутреннему давлению и надежно уплотнять стыковые поверхности.
Наиболее распространенными материалами для таких прокладок являются:
1) фибра – композиция, изготовляемая на основе бумаги, раствора хлористого цинка, касторового масла и глицерина и представляющая собой листы толщиной от 0,5 до 2,5 мм;
2) текстолит – слоистый прессованный материал из хлопчатобумажной ткани (бязь, шифон, башмачная ткань и др.), пропитанный резольной бакелитовой смолой;
3) многослойная латунь – тонкие слои фольги ( 0,05 мм), спаянные между собой специальным припоем.
Средством для уплотнения соединений могут служить также мягкие металлы (свинец, баббитовые и алюминиевые сплавы), применяемые в виде колец и шайб. При стягивании опорных плоскостей металл течет, благодаря чему прокладки вдавливаются в поверхность стыков. В результате получаются довольно плотные соединения.
В случае воздействия горячих газов для уплотнения газового пространства иногда применяют прокладки из красной отожженной меди. Однако вследствие дефицитности красной меди такого рода уплотнения используют лишь в особо ответственных конструкциях.
Чтобы достичь хорошей герметичности соединений, необходимо все болты или шпильки затягивать равномерно; все прокладки должны быть одинаковой толщины, с ровными краями, без разрывов и складок. Соединяемые опорные поверхности стыков должны быть зачищены от заусениц. Всякого рода забоины на рабочих поверхностях не допускаются.
Для подвижных соединений, у которых выходят наружу вращающиеся (перемещающиеся) валы, штоки, скалки, шпиндели и т. п., также применяют различные виды уплотнений, препятствующих утечке жидкостей, паров или газов вследствие избыточного наружного или внутреннего давления.
Дата добавления: 2019-01-14; просмотров: 536; Мы поможем в написании вашей работы! |
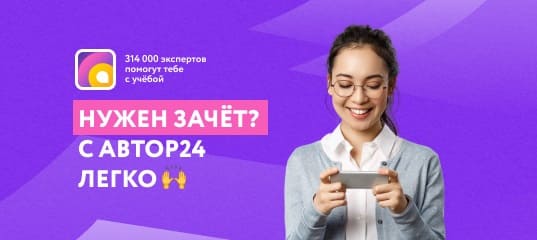
Мы поможем в написании ваших работ!