Прочие инерционные золоуловители
Не так широко, как циклоны или батарейные циклоны применяются на ТЭС другие типы инерционных золоуловителей. Однако, в промышленной теплоэнергетике, металлургии, нефтегазовой промышленности, деревообрабатывающем производстве и некоторых других семейство циклонных пылеуловители представлено достаточно разнообразно. К ним относят:
- жалюзийные пылеуловители;
- вихревые пылеуловители;
- отражательные инерционные пылеуловители;
- ротационные пылеуловители.
Кроме того, для улавливания частиц размером от 100 до 1000 мкм применяют также осадительные камеры.
Жалюзийные пылеуловители
Жалюзийные пылеуловители - это аппараты для очистки газов от пыли инерционного действия. Движущийся в газопроводе запыленный поток встречается с жалюзийной решеткой, состоящей из ряда наклонно установленных пластин, рисунок 8.
Рисунок 8 - Схема действия жалюзийного пылеуловителя
Огибая пластины, струи газа резко меняют направление движения, проходят на другую сторону решетки и движутся в прежнем направлении. Частицы пыли, встречаясь с пластинами решетки, стремятся по инерции сохранить первоначальное направление движения, не огибают пластину, а ударяются о ее поверхность и отражаются в сторону, противоположную движению газов. Затем опять поворачивают по направлению газового потока, ударяются о следующую по ходу газов пластину и т.д. В результате газы, прошедшие через решетку, очищаются, а газы, оставшиеся по другую сторону решетки, обогащаются пылью. Эта часть газового потока (около 10% газов) направляется для окончательной очистки в другой пылеуловитель - циклон.
|
|
Жалюзийный пылеуловитель применяют для улавливания пыли размером >20 мкм.
Вихревые пылеуловители
Вихревые пылеуловители (ВПУ) - это аппараты центробежного действия для очистки газов от пыли. Отличительная особенность ВПУ - высокая степень очистки газов от тончайших фракций (<3...5 мкм) пыли. Существует две основные разновидности ВПУ: сопловой (рисунок 9а) и лопаточный (рисунок 9б).
Процесс обеспыливания в ВПУ происходит следующим образом: запыленный газ поступает в камеру 5 через изогнутый патрубок 4. Для предварительного закручивания запыленного газа в камеру 5 встроен лопаточный завихритель типа розетки 2. Двигаясь вверх к выходному патрубку 6, газовый поток подвергается воздействию вытекающих из завихрителя 1 (наклонные сопла в ВПУ соплового типа, наклонные лопатки в ВПУ лопаточного типа) струй вторичного воздуха, которые придают потоку вращательное движение. Под действием центробежных сил, возникающих при закручивании потока, частицы пыли устремляются к периферии, откуда спиральными струями вторичного потока перемещаются вниз аппарата, в кольцевое межтрубное пространство. Безвозвратный спуск пыли в бункер обеспечивается подпорной шайбой 3. Вторичный воздух в ходе спирального обтекания потока очищаемого газа постепенно проникает в него.
|
|
Рисунок 9 -Вихревые пылеуловители: сопловой (а) и лопаточный (б)
Отражательные инерционные пылеуловители
Отражательные инерционные пылеуловители - это аппараты для выделения пыли из газового потока, в которых происходит изменение направления газового потока. Сталкиваясь с каким-нибудь телом, обтекая его, частицы пыли или капли, обладающие большей инерцией, ударяются о поверхность тела и оседают на ней. Некоторые типы отражательных пылеуловителей приведены на рисунке 10.
а - с перегородкой; б - с плавным поворотом газового потока; в - с расширяющимся конусом; г - с боковым подводом газа.
Рисунок 10 - Отражательные инерционные пылеуловители
Ротационные пылеуловители
Ротационные пылеуловители - это аппараты для очистки газов от пыли, центробежного действия, которые одновременно с перемещением газов очищают его от фракций пыли крупнее 5 мкм. Конструктивная схема простейшего пылеуловителя ротационного типа представлена на рисунке 11.
|
|
При работе вентиляторного колеса 1 частицы пыли за счет центробежных сил отбрасываются к стенке спиралеобразного кожуха 2 и двигаются по ней в направлении выходного отверстия 3. Газ, обогащенный пылью, через специальное пылеприемное отверстие 3 отводится в пылевой бункер, а очищенный газ поступает в пылевую трубу 4.
1 - вентиляторное колесо; 2 - кожух; 3 - пылеприемное отверстие; 4 - выхлопной патрубок
Рисунок 11 - Пылеуловитель ротационного типа
Мокрые золоуловители
Простейшим типом мокрого золоуловителя является центробежный скруббер (рисунок 12а). Главным отличием его от сухого инерционного золоуловителя является наличие на внутренней стенке стекающей пленки воды. Отсепарированная за счет центробежных сил зола лучше отводится из скруббера в бункер, при этом уменьшается вторичный захват зольных частиц со стенки газовым потоком. Характер зависимостей описывается такими же теоретическими формулами, как и для сухих инерционных золоуловителей.
Золоуловитель тина МП-ВТИ (мокропрутковый конструкции Всесоюзного теплотехнического института им. Ф. Э. Дзержинского) во входном патрубке 1 (рисунок 12а) имеет шахматный пучок горизонтальных прутков диаметром 20 мм. Прутковые решетки орошаются водой, распыливаемой механическими форсунками, установленными но ходу очищаемых газов перед решетками. Улавливание золы в аппарате МП-ВТИ проходит две ступени: на орошаемых решетках за счет осаждения частиц золы и на внутренней орошаемой поверхности скруббера. Эффективность золоулавливания составляет 88...90 %.
|
|
Достоинства: сравнительно небольшая стоимость и более эффективная степень улавливания частиц по сравнению с сухими золоуловителями за счет улавливания частиц с меньшим диаметром.
Недостатками золоуловителей МП-ВТИ кроме низкой эффективности золоулавливания являются следующие:
- возникновение отложений золы в прутковых пучках, что приводит к увеличению аэродинамического сопротивления и снижению нагрузки котла;
- повышенный расход воды для обеспечения нормального функционирования золоуловителя;
- необходимость антикоррозионной защиты оборудования.
Уральским отделением Союзтехэнерго совместно с ВТИ разработаны и внедрены на многих электростанциях более эффективные мокрые золоуловители с коагуляторами Вентури (рисунок 12б). Основными достоинствами этих аппаратов являются стабильная степень очистки газов от золы, составляющая 94...96 % при умеренном аэродинамическом сопротивлении (1100 -1300 Па), относительно небольшие капитальные и эксплуатационные затраты, а также возможность работы на оборотной воде. Попытки осуществить питание аппаратов типа МП-ВТИ оборотной осветленной водой с золоотвала, чтобы избежать ее сброса в водоемы общего пользования, приводили к образованию в прутковых пучках трудноудаляемых минеральных отложений, серьезно нарушающих работу золоуловителя. При этом наблюдалось:
- падение степени очистки газов;
- возрастание аэродинамического сопротивления;
- появление интенсивного брызгоуноса.
Коагуляторы Вентури могут устанавливаться как вертикально, так и горизонтально с небольшим уклоном.
Принцип работы мокрого золоуловителя с коагулятором Вентури заключается в следующем, рисунок 12б. В конфузор 3 коагулятора через форсунки подается орошающая вода, которая дополнительно диспергируется (распыляется) скоростным газовым потоком на мелкие капли. Летучая зола при прохождении с дымовыми газами через коагулятор частично осаждается на каплях и на его орошаемых стенках. Далее капли и неуловленные частицы золы поступают в корпус аппарата - центробежный скруббер, где дымовые газы освобождаются от капель и дополнительно очищаются от золы, после чего дымососом выбрасываются в атмосферу. Гидрозоловая пульпа сбрасывается через гидрозатвор в канал системы гидрозолоудаления (ГЗУ).
В конфузоре пылегазовый поток разгоняется от 4...7 до 50...70 м/с. Дополнительное дробление капель воды осуществляется в горловине 4. В диффузоре 5 происходит столкновение частиц золы с каплями воды (кинематическая коагуляция) и снижение скорости пылегазового потока, который, в свою очередь, тангенциально вводится в скруббер.
Размер капель тем меньше, чем больше скорость газа в горловине. Средний диаметр капель dК, м, можно определить
где ur - скорость газа в горловине, м/с.
Захват частиц золы каплями может происходить по двум причинам:
- быстро несущиеся со скоростью газов частицы золы попадают в капли, которые еще не успели разогнаться потоком газа. Тогда они попадают в каплю за счет разности скоростей (ur- uК), где uК - скорость движения капли;
- за счет турбулентных пульсаций частиц золы, которые попадают в практически мало пульсирующие капли.
Если принять за основу коагуляции второй механизм, то параметр золоулавливания для трубы Вентури определяется из выражения:
где e Т - степень турбулентных пульсаций, определяемая как отношение скорости дрейфа к скорости газа в горловине;
q Ж - удельный расход орошающей жидкое на 1 м3 очищаемого газа, л/м3;
L - расстояние между горловиной трубы и скруббером.
а - центробежный скруббер; 1 - входной патрубок запыленного газа; 2 - корпус золоуловителя; 3 - оросительные сопла; 4 - выход очищенного газа; 5 - бункер; б - золоуловитель с коагулятором Вентури; 1 - входной патрубок запыленного газа; 2 - подача воды через оросительные сопла; 3, 4, 5 - конфузор, горловина и диффузор коагулятора Вентури; 6 - скруббер-каплеуловитель
Рисунок 12 - Мокрые золоуловители
В отличие от других золоуловителей для мокрых золоуловителей с коагулятором Вентури в формулу ( ) для расчета параметра золоулавливания не входит диаметр частиц d. В первом приближении можно принять, что все частицы от мелких до крупных улавливаются одинаково, и их дисперсный состав не учитывать.
В отечественной практике применение получили два тина мокрых золоуловителей с коагулятором Вентури: МВ-УО ОРГРЭС и МС-ВТИ. Первый тип золоуловителя выполняется с вертикальным и горизонтальным расположением коагулятора Вентури круглого сечения, второй только с горизонтальным расположением трубы прямоугольного сечения.
Основные характеристики золоуловителя МС-ВТИ представлены в таблице 4.
Расчет золоуловителей подобного типа ведется в следующей последовательности.
1. Определяется диаметр каплеуловителя, м, причем скорость газов в его сечении принимается в среднем w=5 м/с:
где Q - общий расход газа м3/с.
Затем по таблице 4 подбирают типоразмер аппарата.
2. В зависимости от принятой степени проскока e находят параметр золоулавливания П и выбирают q Ж и ur, таким образом, чтобы соблюдалось равенство
.
Обычно ur=50...70 м/с, q Ж=0,12...0,2 кг/м3.
Таблица 4 – Типоразмеры золоуловителей МС-ВТИ
Каплеуловитель | Горловина трубы Вентури | ||||
Диаметр, м | Высота, м | Активная площадь сечения, м2 | Сечение входного патрубка, м2 | Размеры, м | Площадь сечения, м2 |
2,8 | 9,66 | 5,72 | 1,37 | 0,39´1,17 | 0,455 |
3 | 10,32 | 6,6 | 1,67 | 0,43´1,23 | 0,53 |
3,2 | 10,98 | 7,54 | 1,95 | 0,48´1,4 | 0,644 |
3,6 | 12,2 | 9,62 | 2,41 | 0,45´1,8 | 0,81 |
4 | 13,61 | 11,93 | 3 | 0,50´2 | 1 |
4,5 | 15,25 | 15,2 | 3,88 | 0,57´2,28 | 1,3 |
3. Определяют площадь сечения горловины Вентури по выражению
Подбирают сечение горловины и корректируют соответственно действительную скорость газов.
По выражению уточняют значение П и, затем, степень проскока e.
4. Общее гидравлическое сопротивление коагулятора Вентури и каплеуловителя, Па, рассчитывается по формуле:
где r - плотность газа перед золоуловителем, кг/м3;
u ВХ - скорость газа при входе в каплеуловитель, равная
Обычно u ВХ=20 м/с.
5. Конечная допустимая температура очищенных газов, ОС, принимается исходя из известной точки росы водяных паров t ’’Р из соотношения:
t³ t ’’Р +21
Не рекомендуется применять мокрые золоуловители для топлив, содержащих в составе золы более 15...20 % оксида кальция СаО. Приведенная сернистость топлива должна быть не более 0,3 %×кг/МДж. Жесткость орошаемой воды не должна превышать 15 мг-экв/л.
В соответствии с п.5 температуру газов за мокрым золоуловителем следует поддерживать не менее чем на 21 0С выше точки росы для предотвращения коррозии газоходов.
Обязательным условием нормальной работы мокрого золоуловителя является предотвращение отложений в его орошающих устройствах. Чтобы обеспечить это условие, прежде всего, необходимо очистить орошающую воду от механических примесей, для чего применяются гравийные фильтры.
Основной причиной возникновения отложений является кристаллизация солей кальция из пересыщенной ими орошающей воды или пульпы, а также недостаточное по различным обстоятельствам орошение каких-либо участков стенок золоуловителя. Орошающая вода не должна быть пересыщена сернокислым кальцием (СаSO4), что можно достигнуть, например, добавкой к оборотной воде некоторого количества свежей воды.
При проектировании мокрых золоуловителей следует учитывать, что SO2 и SO3 содержащиеся в дымовых газах, частично растворяются в пульпе. При этом если диоксид серы улавливается в мокром золоуловителе до 25 %, то триоксид серы до 85 %. В результате рН пульпы снижается до 3,5 и требуется защита стенок золоуловителя от коррозии. Улавливание SO3 приводит также к изменению точки росы дымовых газов.
Электрофильтры
Одним из хорошо зарекомендовавших себя и перспективным типом золоуловителей для крупных ТЭС являются электрофильтры, которые могут обеспечить высокую степень очистки газов при аэродинамическом сопротивлении не более 150 Па практически без снижения температуры и без увлажнения дымовых газов.
В электрофильтрах запыленный газ движется в каналах, образованных осадительными электродами 1 (рисунок 13), между которыми расположены через определенное расстояние коронирующие электроды 2.
Сущность процесса электрической очистки газов заключается в следующем. Запыленный газ проходит через систему, состоящую из заземленных осадительных электродов 7 и размещенных на некотором расстоянии (называемом межэлектродным промежутком) коронирующих электродов 2, к которым подводится выпрямленный электрический ток высокого напряжения с отрицательным знаком.
1 - осадительный электрод; 2 - коронирующий электрод; 3 - частицы золы; 4 - электрическое поле; 5 - слой осевшей золы; 6 - заряженная зола
Рисунок 13 - Принцип работы электрофильтра
При достаточно высоком напряжении, приложенном к межэлектродному промежутку, у поверхности коронирующего электрода происходит интенсивная ударная ионизация газов, сопровождающаяся возникновением коронного разряда (ток короны).
Газовые ионы различной полярности, образующиеся в зоне короны, под действием сил электрического поля движутся к разноименным электродам, вследствие чего в электродном промежутке возникает электрический ток, который и представляет ток короны. Частицы золы из-за адсорбции на их поверхности ионов приобретают в межэлектродном промежутке электрический заряд и под влиянием сил электрического поля движутся к электродам, осаждаясь на них. Основное количество частиц осаждается на развитой поверхности осадительных электродов, меньшая их часть попадает на коронирующие электроды. По мере накопления на электродах осажденные частицы удаляются встряхиванием или промывкой электродов.
Процесс электрогазоочистки можно разделить на следующие стадии:
- зарядка взвешенных в газе частиц;
- движение заряженных частиц к электродам;
- осаждение частиц на электродах;
- удаление этих частиц с электродов.
Коронный разряд возникает при достижении определенной напряженности и электрического ноля, называемой критической или начальной, которая, например, для воздуха при атмосферном давлении н температуре 20 0С составляет около 15 кВ/см. При дальнейшем повышении напряженности нарушается электрическая прочность газового промежутка между электродами, наступает искровой или дуговой электрический разряд.
К коронирующим электродам подводится отрицательный заряд, так как подвижность отрицательных ионов выше положительных. Кроме того, при отрицательной короне удается поддержать более высокое напряжение без искрового пробоя между электродами.
Рабочая часть электрофильтра, в которой существует электрическое поле, называется активной зоной. Она разделена на несколько электрических полей, через которые очищаемый газ проходит последовательно. Электрофильтры бывают однопольными и многопольными.
На большинстве электростанций, оснащенных электрофильтрами, применены аппараты тина УГ (унифицированный горизонтальный). Запыленные газы после газораспределительной решетки 6 (рисунок 14) поступают в коридоры, образованные вертикально висящими широкополосными осадительными электродами С-образной формы. Коронирующие электроды представляют собой профильные ленточные элементы с штампованными иглами, укрепленные в специальной рамке. Для удаления осевшей на электродах золы предусмотрены встряхивающие устройства в виде молотков, ударяющих по наковальням электродов. Осевшая зола попадает в бункера и затем через гидравлические затворы направляется в систему ГЗУ. Расчетная температура газов до 250 ОС.
1 - корпус; 2 - электрод осадительный; 3 - электрод коронирующий; 4 - механизм встряхивания коронирующих электродов; 5 - механизм встряхивания осадительных электродов; 6 - газораспределительная решетка; 7 - бункер для золы; 8 - изолятор
Рисунок 14 - Электрофильтр типа УГ
На рисунке 14 показан трехпольный электрофильтр типа УГ. В первом поле оседает наибольшее количество золы, в последнем - минимальное.
Важным условием, определяющим эффективность работы электрофильтра, является агрегат электрического питания. Каждый агрегат обслуживает одно поле (или половину поля), состоит из трех узлов:
- повысительно-выпрямительного блока с высоковольтным распределительным устройством;
- блока магнитных усилителей;
- дросселей и пульта управления.
Для поддержания напряжения в любой момент работы электрофильтра на грани пробивного, когда обеспечивается наилучшая ионизация газов, применена автоматическая схема регулирования. Электрофильтры серии УГ имеют две разновидности: УГ2 - с высотой электрода 7,5 и активной длиной каждого поля 5 м и УГЗ - с высотой электрода 12,2 и длиной поля 4 м.
Число полей n в каждом электрофильтре может быть три и четыре. Поперечные сечения для прохода газов Fr, м2, для электрофильтров УГ2 имеют следующие значения: 26, 37, 53, 74; для электрофильтров УГЗ: 88, 115, 177, 230, 265. Параметры золоулавливания электрофильтра рассчитываются по выражению
П= J × f
где J - скорость дрейфа частиц, м/с (скорость движения частиц золы под действием сил осаждения);
f = A / V - удельная площадь поверхности осаждения на 1 м3/с очищаемого газа.
А - площадь поверхности канала золоулавливания, м2;
V - расход газа, м3/с.
Степень осаждения определяется двумя факторами - скоростью дрейфа частиц золы J и удельной поверхностью осаждения f . Увеличивая f, можно получить высокую степень улавливания, однако это связано с большими расходами металла и увеличением габаритов электрофильтров.
Скорость дрейфа J, м/с, определяется в основном электрическими характеристиками электрофильтра и пылегазового потока и выражается как:
где e0 - диэлектрическая проницаемость вакуума, Ф/м;
e - относительная диэлектрическая проницаемость вещества частицы;
ЕЗ - напряженность электрического поля зарядки, В/м;
ЕОС - напряженность электрического поля осаждения, В/м.
Из приведенного выражения следует, что скорость дрейфа пропорциональна произведению напряженностей полей зарядки и осаждения и диаметру частицы (влияние остальных факторов менее существенно). Однако определить теоретическим путем величины ЕЗ и ЕОС затруднительно, из-за чего расчет но приведенному выражению возможен при наличии опытных данных но электрическим характеристикам.
Основными факторами, определяющими скорость дрейфа, являются электрические свойства пылегазового потока и в первую очередь электрическое сопротивление золы. На рис.12, а показана зависимость удельного сопротивления летучей золы r, 0м×м, при работе электрофильтра от температуры. Максимум электрического сопротивления золы соответствует температуре 100...130 0С. Наибольшее r имеет зола углей с малым содержанием горючих в уносе, низким содержанием серы и влаги в топливе. К углям, зола которых имеет наиболее высокое электрическое сопротивление, относятся экибастузский и кузнецкий каменные угли.
На рисунке 15б показано изменение скорости дрейфа J от удельного сопротивления r. В области r =108...109 0м×м происходит резкое падение скорости дрейфа.
Анализ работы электрофильтров на ТЭС показал, что основная причина менее эффективной очистки заключается в высоком удельном электрическом сопротивлении (УЭС) r слоя золы, образующемся на осадительных электродах электрофильтра. Вследствие высокого УЭС проводимость слоя пыли уменьшается, что приводит к увеличению потенциала поверхности слоя, увеличению падения напряжения в слое при одновременном его уменьшении в газовом промежутке. При увеличении разности потенциалов между поверхностью слоя и заземленным электродом до значения, достаточного для пробоя газов, на некоторых участках поверхности слоя возникают относительно стабильные местные разряды. Это явление, вызывающее образование и выброс в межэлектродное пространство ионов со знаком, обратным знаку ионов, образующихся в основном процессе, принято называть обратной короной. Положительные ионы, образовавшиеся в зоне обратной короны, под действием электрического ноля двигаются к коронирующему электроду, встречают на своем пути частицы золы, заряженные отрицательно, и нейтрализуют их заряды. В результате этого прекращается движение золовых частиц к осадительному электроду и снижается степень очистки газов в электрофильтре. Устойчивая обратная корона характеризуется появлением в слое пыли точек локализованных разрядов голубого цвета.
Высокое УЭС летучей золы обусловлено как параметрами дымовых газов (концентрация серного ангидрида и зависящая от него кислотная точка росы, парциальное давление водяных паров, температура газов и др.), так и химическим составом самой золы, главным образом соотношением в ней алюмосиликатов (Al2O3+SiO2) и щелочных металлов, в первую очередь натрия и лития. При определенной комбинации низких содержании серы, водорода и влаги в угле с низкими концентрациями щелочных металлов в золе при общепринятых в котельной практике температурах уходящих газов 120...150 ОС удельное электрическое сопротивление золы вырастает до 1010...1012 0м×м. При таких параметрах обратная корона возникает и развивается в электрофильтре исключительно быстро.
На степень улавливания золы большое влияние также оказывает равномерность распределения поля скоростей дымовых газов по сечению электрофильтра. С целью создания достаточно равномерного поля скоростей газов на входе в электрофильтр устанавливают газораспределительные решетки.
а - зависимость удельного сопротивления летучей золы при работе электрофильтра от температуры; б - зависимость скорости осаждения от удельного сопротивления пыли; 1 - цементная пыль; 2 - зола уноса котлов
Рисунок 15 - Влияние удельного сопротивления летучей золы на работу электрофильтра
Современные электрофильтры серии ЭГА - горизонтальные, модификации А, изготавливаются в широком диапазоне типоразмеров при глубокой унификации узлов и деталей. Такие фильтры рассчитаны на максимальную температуру газов до 330 ОС. Электродная система - система, составленная из широкополосных (ширина элемента 40 мм) элементов открытого профиля и рамных коронирующих электродов с игольчатыми элементами. Шаг между одноименными элементами составляет 300 мм. В электрофильтрах по ширине размещается от 10 до 88 газовых проходов. Номинальная высота электродов принимается из ряда 6; 7,5, 9; 12 м.
В связи с повышением мощности энергоблоков потребовалось создание двухъярусного фильтра. Для энергоблоков 800 МВт Березовской ГРЭС-1 разработан и изготовлен на базе серии ЭГА электрофильтр типа ЭГД (горизонтальный, двухъярусный) (рис.13).
Электрофильтры серии УВ - унифицированные вертикальные пластинчатые сухие для очистки газов с температурой до 250 ОС, выпускаются взамен электрофильтров ДВП и ДВПН. Электрофильтры типа УВ имеют одно поле активной длины 7,4 м и разделены по газу на одну - три секции. Осадительные электроды - пластинчатые с нижним молотковым стряхиванием. Коронирующие электроды - рамные с верхним подвесом и молотковым встряхиванием.
Электрофильтры УВ рассчитаны на невысокую запыленность газов и скорость их в активном сечении до 1 м/с.
Расчет электрофильтра для ориентировочного определения его размеров ведется в следующем порядке.
Электрические поля имеют самостоятельное питание и систему встряхивания.
Достоинства: высокая степень улавливания, низкое гидравлическое сопротивление до 150 Па.
Недостатки: высокие капитальные затраты, металлоемкость, большая занимаемая площадь, необходимость в специальном повысительно-выпрямительном агрегате для электрического питания, высокая чувствительность к отклонениям технологического режима газа в котле, не используется для взрывоопасной пыли.
Тканевые фильтры
Фильтрующие элементы фильтра могут быть выполнены в виде тканевых рукавов, мешков, полотен. Запыленный газ пропускается через ткань, в результате чего на поверхности ткани и в ее порах осаждается пыль. По мере увеличения толщины слоя пыли возрастает сопротивление фильтра, поэтому осевшую на ткани пыль периодически удаляют.
Процесс фильтрации газа зависит от типа ткани и вида пыли. Гладкие и неворсистые ткани сравнительно легко пропускают запыленный газ. В порах таких тканей задерживаются только крупные частицы пыли. Фильтр начинает хорошо задерживать мелкую пыль только после накопления на поверхности фильтрующих элементов слоя пыли. Для ворсистых, шерстяных тканей с мелкими порами влияние начального слоя пыли менее заметно. Ворсистые ткани целесообразно применять при улавливании зернистой гладкой пыли, а при улавливании волокнистой пыли - лучше гладкие ткани.
Тканевые фильтры применяются для очистки больших объемов воздуха со значительной концентрацией пыли на входе (до 60 г/м3). В качестве фильтрующих элементов в этих аппаратах часто используются тканевые рукава, которые обеспечивают тонкую очистку воздуха от пылевых частиц, имеющих размер менее 1 мкм. Известны всасывающие и нагнетательные рукавные фильтры.
Всасывающие фильтры устанавливаются до вентилятора, т. е. на его всасывающей линии, нагнетательные - на нагнетательной линии. Воздух, очищенный в рукавах нагнетательных фильтров, поступает непосредственно в помещение, где установлены фильтры.
В настоящее время выпускается и эксплуатируется много разнообразных конструкций тканевых фильтров. По форме фильтровальных элементов и тканей они могут быть рукавные и плоские (полотняные), по виду опорных устройств - каркасные, рамные и т.д., по наличию корпуса и его форме цилиндрические, прямоугольные, открытые (бескамерные), по числу секций - одно- и многосекционные. Фильтры могут также различаться по способу регенерации (чистки) и ряду других признаков.
Фильтровальные ткани
Для тканевых фильтров применяются тканые или валяные материалы. Ткани для фильтров изготавливают из натуральных или синтетических волокон диаметром 10...30 мкм, скручиваемых в нити диаметром около 0,5 мм. Размеры пор между нитями обычно составляют 100...200 мкм.
При прохождении запыленного воздуха через ткань пылевые частицы задерживаются между нитями и ворсом. Наличие ворса повышает эффективность фильтрации.
Ворс должен быть обращен навстречу запыленному потоку. При движении запыленного потока воздух прижимает ворсинки к ткани. При обратной продувке происходит выпучивание ворсинок, и накопившиеся пылевые частицы удаляются.
Фильтровальные ткани, используемые в фильтрах, должны отличаться высокой пылеемкостью, воздухопроницаемостью, механической прочностью, стойкостью к истиранию, антистатическими свойствами, стабильностью свойств при повышенной температуре и агрессивном воздействии химических примесей, а также минимальным влагопоглощением и способностью к легкому удалению накопленной пыли.
Не все фильтровальные ткани удовлетворяют перечисленным требованиям, поэтому каждую ткань используют для определенных, наиболее благоприятных для нее условий. В фильтрах для улавливания древесных частиц, наиболее часто используют следующие фильтровальные ткани: «Ланит К», «Смог» (старое название «Ланит 500») плотностью 460 ± 23 г/м2, «Искра», «Искра 2». Это иглопробивной лавсановый материал. Ткань «Искра» - антистатический материал, имеющий металлические вкрапления для снятия статического электричества. Рукава из этой ткани используют для фильтрования пылевоздушной смеси, содержащей пыль, образующуюся при шлифовании древесины или лаковых покрытий. Материал «Искра 2» - каркасный, более долговечный. Каркасная основа повышает прочность ткани и сохраняет размеры изделия в течение всего срока службы. Физические параметры фильтровальных тканей, такие как плотность, толщина, объем пор варьируются в широких пределах, что позволяет эффективно фильтровать газопылевые смеси с различными характеристиками. Швы рукавных фильтров могут быть как тройными сшивными, так и термосварными. В зависимости от конструкции фильтра, рукавный фильтр снабжается металлическими кольцами, усилениями, донышком и прочими элементами.
Фильтровальные рукава имеют диаметр 90…450 мм и длину 2…10 м.
Надежность фильтра
Тканевые рукава - это наиболее изнашиваемые элементы фильтра, периодически требующие их замены. Заводы изготовители пылеулавливающих аппаратов гарантируют степень очистки воздуха до 99,9 %, а срок эксплуатации фильтровальной ткани устанавливают до 1…5 лет. Ткань фильтра в процессе работы изнашивается: истирается проникающим воздухом, истирается прилипшими древесными частицами, прокалывается иглообразными стружками, истирается налипшей «шубой» при регенерации фильтра встряхиванием или продувом, изнашивается при изменении влажности древесных частиц и температуры воздуха. По мере износа сопротивление ткани фильтра проникновению воздуха уменьшается, и ткань пропускает большее количество пыли, особенно после регенерации. Нормальная фильтрация наступит только после того, как на поверхности ткани осядет слой пыли. Чем толще слой осевшей пыли, тем выше степень очистки воздуха, тем выше сопротивление фильтра.
Изношенный фильтр, особенно после регенерации, пропускает мелкодисперсную пыль, которая возвращаться и накапливаться в цехе. Это можно обнаружить, если в цехе налажен контроль запыленности воздуха. Однако деревообрабатывающие предприятия не оснащены диагностическим оборудованием и не контролируют ни состояния воздуха, ни состояния ткани рукавов. Более того, конструкции выпускаемых фильтров таковы, что использовать современные средства диагностики невозможно. Неисправный рукав можно обнаружить только визуально и тогда, когда он фонтанирует крупную пыль, а чтобы заменить неисправный рукав, надо демонтировать почти все рукава. Для удобства диагностики и эксплуатации фильтры должны иметь блочную (секционную) конструкцию.
Регенерация ткани рукавов
Очистку тканевых рукавов производят несколькими способами: механическим встряхиванием, обратной струйной и импульсной продувкой рукавов. Механическое встряхивание вертикальных рукавов осуществляют волнообразным изменением натяжения ткани рукавов с помощью механических вибраторов. Изготовители фильтров рекомендуют выполнять встряхивание через каждый час работы в течение 15 с.
При обратной струйной продувке, применяемой при отложении пыли на внутренней поверхности рукава, изменяют направление дутья, подавая на регенерацию свежий или очищенный воздух. Для выполнения обратной продувки фильтр отключают посекционно или полностью. Расход воздуха на обратную продувку принимают до 10% от количества очищаемого газа.
Для продувки воздух от высоконапорного вентилятора подается в трубку-каретку с кольцевой щелью, надетой на рукав и перемещаемой вдоль него. Воздух, выходящий из щели со скоростью 10…30 м/с, проникает внутрь рукава, разрушает слой пыли, выдувает пыль.
Из-за сложности конструкции струйная продувка используется для регенерации только толстых фильтрующих материалов - войлоков, фетров.
Рукавные фильтры
Рукавные фильтры - надежные и эффективные пылеулавливающие аппараты, предназначенные для сухой очистки промышленных газов. Рукавный фильтр представляет собой металлический корпус, разделенный перегородками на секции, в каждой из которых размещена группа фильтрующих рукавов подвешенных на монтажных (опорных) решетках. Внизу рукавного фильтра находится бункер для сбора пыли, выгрузку пыли и герметичность обеспечивают шнек и шлюзовой питатель. Регенерация (очистка) рукавов фильтра происходит поочередно кратковременными импульсами сжатого воздуха. Управление регенерацией осуществляет контроллер, который задает частоту, и продолжительность импульсов по перепаду давления при помощи дифманометра.
Рукавные фильтры нашли широкое применение в различных отраслях промышленности: химической, целлюлозно-бумажной, деревообрабатывающей, теплоэнергетической, нефтеперерабатывающей, черной и цветной металлургии, производстве строительных материалов, пищевой, текстильной и многих других.
Фильтрующим элементом рукавных фильтров является фильтровальные рукава, сшитые из фильтрующего материала, который подбирается в зависимости от условий эксплуатации и состава пыли.
Существующие фильтровальные материалы могут применяться:
- при повышенной влажности;
- в кислотно-щелочной среде;
- при высоких температурах;
- в условиях высокой абразивности газопылевого потока;
Рукавные фильтры применяются для очистки промышленных газов от пыли при концентрации до 60 г/м3. Однако при применении специальных устройств, понижающих входную концентрацию пыли, рукавным фильтрам по силам противостоять концентрации до 200 г/м3. После рукавного фильтра очищенный воздух может содержать менее 10 мг/м3 пыли.
Рукавные фильтры чаще применяются при температуре очищаемого газа, в диапазоне температур 20-260 °С, но так же существуют материалы, рассчитанные на работу при температуре до 350 °С.
В зависимости от гранулометрического состава пыли и начальной запыленности степень очистки (КПД) может составлять 98-99,9 % при объеме фильтруемого газа 0,4 - 1,6 м3/м2мин.
Регенерация (очистка от осевшей пыли) рукавов в процессе работы фильтра осуществляется автоматически путем их встряхивания, с помощью импульсов сжатого воздуха, что является преимуществом данных газоочистных аппаратов или же методом обратной продувки и вибрационным способом, что менее эффективно. Имеются мембранные клапаны, которые позволяют провести процесс регенерации при помощи усовершенствованной импульсной электронной системы регенерации рукавов. В настоящее время самым эффективным является автоматическая продувка рукавного фильтра импульсами сжатого воздуха.
Классификация рукавных фильтров:
- фильтр рукавный
- фильтр ячейковый
- кассетный фильтр
Конструкции матерчатых фильтров весьма разнообразны. Наиболее распространенной классификацией рукавных фильтров является разделение по способу регенерации и форме фильтровальных рукавов.
Наибольшее распространение в настоящее время получили фильтры с цилиндрической формой рукава (рукавные фильтры). Однако к рукавным фильтрам иногда относят кассетные и другие типы матерчатых фильтров. В дальнейшем, под названием «Матерчатые фильтры» будут предполагаться конструкции фильтров, имеющих цилиндрическую или иную форму фильтровальных элементов, изготовленных из ткани, нетканого иглопропробивного, холостопрошивного, клееного, войлочного гибкого фильтровального материала. К данной категории не будут относиться фильтры с фильтровальными элементами из керамики, металлокерамики и других жестких, а также объемных фильтровальных материалов.
Рукавные фильтры с цилиндрической формой фильтровального элемента широко распространены в различных отраслях промышленности, имеют много преимуществ по сравнению с другими конструкциями матерчатых фильтров. Однако, наряду с достоинствами, они имеют существенный недостаток, заключающийся в сравнительно небольшой поверхности фильтрации, приходящейся на единицу объема рабочей камеры фильтра.
Стремление к более компактному размещению фильтровального материала в рабочей камере фильтра привело к созданию оригинальных конструкций, многие из которых нашли практическое применение в различных отраслях промышленности.
В процессе работы матерчатых фильтров происходит постепенное отложение пыли в порах фильтровального материала и на его поверхности. По мере роста слоя пыли растет и гидравлическое сопротивление аппарата.
Если периодически не удалять пылевой слой с поверхности материала и из его пор произойдет «запирание фильтра», т.е. тягодутьевой аппарат (обычно вентилятор) будет не в состоянии протягивать газ через забившуюся фильтровальную перегородку (производительность по воздуху будет снижаться). Для поддержания фильтра в работоспособном состоянии необходимо периодически удалять пыль с поверхности фильтровального материала из пор.
Однако, как известно, оседающий на поверхности фильтровального материала слой пыли одновременно является фильтрующей средой, препятствующей проскоку наиболее мелких частиц пыли. Поэтому с фильтровального материала необходимо удалить не весь слой пыли, а только часть, чтобы обеспечить приемлемое гидравлическое сопротивление аппарата и сохранить его высокую эффективность пылеулавливания. Процесс удаления части пылевого слоя снаружи и изнутри фильтровальной перегородки в матерчатых фильтрах принято называть регенерацией, т.е. частичным восстановлением первоначальных свойств фильтровальной перегородки.
В промышленной эксплуатации в настоящее время находится много конструкций, систем, устройств для регенерации фильтровального материала. Основные способы регенерации фильтровального материала: механическое встряхивание (в этом случае пыль удаляется с поверхности фильтровального материала), обратной продувкой (в этом случае пыль удаляется с поверхности и из пор фильтровального материала) и сжатым воздухом.
Достоинствами фильтров с механическим отряхиванием является стабильность удаления осадка пыли. В качестве основных недостатков следует отметить сложность встряхивающего механизма, который требует постоянного внимания обслуживающего персонала, истирание и изломы рукавов в одних и тех же местах, чувствительность системы к усадке и вытяжке рукавов, необходимость отключения фильтра или отдельной секции на время проведения регенерации.
Эффективным методом регенерации фильтровального материала является обратная продувка очищенным газом или напорным воздухом. Обратная продувка, как правило, применяется в сочетании с другими способами: механическим встряхиванием, перекручиванием, вибрацией, покачиванием рукавов и др. Такие фильтры довольно эффективны, удобны в эксплуатации и обслуживании. Однако производительность их несколько снижена за счет подсоса воздуха в период регенерации фильтровального материала. Обратная продувка обычно сопровождается плавной деформацией фильтровального материала, которая не действует так отрицательно на волокна как, например, механическое отряхивание.
Одним из наиболее эффективных способов регенерации фильтровального материала, который широко распространен в конструкциях каркасных фильтров, является импульсная продувка. Отечественные фильтры с импульсной продувкой типа ФРКИ, ФРКДИ, ФРИ, ФКИ, ФРМИ, ФРИА нашли применение почти во всех отраслях промышленности. Фильтры с импульсной продувкой отличаются тем, что в их конструкции нет встряхивающих механизмов, дросселей и обдувочных вентиляторов.
Большое разнообразие технологических процессов, требующих высокоэффективной очистки отходящих газов или улавливания высокодисперсных пылей вызвало необходимость разработки и производства специальных фильтров, предназначенных для конкретных условий применения. Так, например, специфика улавливания волокнистой пыли рукавными фильтрами несколько отлична от улавливания обычных пылей. Очистка взрывоопасных газов потребовала введения определенных конструктивных особенностей в аппараты фильтрации. В конструктивном оформлении матерчатые фильтры для очистки высокотемпературных газов отличаются и по применяемому фильтровальному материалу и по исполнению многих узлов и деталей от фильтров, предназначенных для очистки атмосферного воздуха. Для улавливания дорогостоящих пылей, ядовитых материалов требуются фильтры с повышенной гарантией от проскока их через фильтровальный материал. В одних случаях очистке подвергаются небольшие объемы газов, в других случаях необходимо очищать сотни тысяч и миллионы м3/ч.
Контрольные вопросы к практическим занятиям:
1. На каких явлениях основано улавливание золовых частиц?
2. Какой метод выделения золовых частиц из потока наиболее эффективный?
3. Типы золоуловителей.
4. На чем основан выбор золоуловителя и дымососа?
5. Достоинства сухих инерционных золоуловителей.
6. Назовите модификации батарейных циклонов.
7. Какая последовательность должна соблюдаться при расчете батарейного циклона?
8. Что относится к прочим инерционным золоуловителям?
9. Принцип улавливания в мокрых золоуловителях. Их отличие от сухих инерционных.
10. Принцип работы электрофильтра
11. Классификация рукавных фильтров, регенерация ткани рукавов.
Лекция 18-19-20 - Рассеивание выбросов. Условия работы дымовых труб
План:
1. Рассеивание выбросов.Условия работы дымовых труб
2. Расчет рассеивания
3. Получение полезных веществ из дымовых газов котлов
Контрольные вопросы
1 . Рассеивание выбросов.Условия работы дымовых труб
Меры по уменьшению образования токсичных веществ и по их улавливанию не решают полностью проблемы обеспечения безопасной концентрация вредных веществ в зоне выбросов. Даже при высокой эффективности подавления и улавливания в выбросах ТЭС содержится значительное количество вредных газообразных, аэрозольных золовых частиц.
Для уменьшения локальной концентрации вредных веществ в населенных пунктах прибегают к рассеиванию примесей в атмосфере.
Рассеивание примесей в атмосфере осуществляется с помощью высотных дымовых труб.
Дымовые трубы изготавливают из монолитных железо-бетонных стволов, выдерживающих ветровые и весовые нагрузки. Однако железобетон являясь прочным материалом, не способен противостоять воздействию сернистых соединений, влаги и повышенной температуре дымовых газов. Поэтому создается вторая внутренняя оболочка, которая предназначена как ограждающая поверхность для агрессивных дымовых газов. Внутренняя поверхность железо-бетонного ствола покрывается изоляцией – эпоксидным лаком и стеклотканью. Футеровка выполняется из красного кислотоупорного кирпича на диабазовой или андезитовой замазке, и опирается на железо-бетонные консоли, выполняемые через каждые 30-50 метров. На трубе предусмотрены светофорные площадки для светооградительнх огней, располагаемых на высоте трубы через каждые 15-30 метров. Трубу окрашивают полосами красного цвета, шириной 2-2,5 м. с интервалами 15 м. Срок службы 30-50 лет, для повышения надежности дымовых труб применяют разделение функций газоотводящего и несущего ствола. С этой целью между ограждающими и несущими стволами выполняют воздушный засор, размером 150-200 мм. В этом зазоре обеспечивается циркуляция воздуха для вывода просачивающихся через футеровку агрессивных газов.
Воздух засасывается из атмосферы и подогревается в калорифере паром из отбора турбины до температуры 50- 90 0С. Вентилятор устанавливают под газоходным каналам трубы, направляемый воздух в воздушный канал. В процессе эксплуатации трубы возникают условия, когда топочные газы проникают к железобетонному стволу и разрушают его. На тех участках трубы, где давление газов больше, чем давление окружающего воздуха, возможно их проникновение через оболочку трубы.
На ТЭЦ часто применяются многоствольные трубы, в которых внутри железобетонными оболочками устанавливаются несколько металлических стволов цилиндрической формы (3 - 4). Основное преимущество многоствольной трубы состоит в том, что имеется возможность обслуживать и ремонтировать каждый ствол независимо от других.
![]() | В процессе эксплуатации возникают условия, когда топочные газы проникают к железобетонному стволу и разрушают его. Это обусловлено распределением давления газов на высоту трубы. На тех участках трубы, где давление газов больше, чем давление окружающего воздуха, возможно их проникновение через оболочку трубы. Выражение для разности статических давлений между газами в стволе и окружающей атмосфере имеет вид: Dhст = hдо – hд +Dhтр – gDrl где hдо, hд – динамический напор в устье и рассматриваемом сечении; l = zo – z – расстояние от верха трубы до рассматриваемого сечения; Dr = rв - r - разница плотностей воздуха и дымовых газов; Dhтр – потери напора на трение от рассматриваемого сечения до верха. Если по ходу газов Dhст>0, то через футеровку – фильтрация дымовых газов. Для анализа рассеивания рассматриваются нижние слои атмосферы, непосредственно примыкающие к земной поверхности. |
Одна из характеристик атмосферы, которая влияет на эффективность рассеивания – устойчивость, т.е. способность препятствовать вертикальным движениям и сдерживать турбулентность воздушных масс. В зависимости от того, способствует или препятствует окружающая среда развитию вертикальных перемещений объемов в атмосфере, различают 3 типа состояния устойчивости или стратификации атмосферы:
- неустойчивая;
- равновесная (безразличная);
- устойчивая.
Состояние атмосферы при которой вертикально смещающиеся частицы воздуха получают ускорение, совпадающее с направлением движения, называют неустойчивое состояние.
Когда при движении частицы возникает отрицательное ускорение – устойчивое состояние.
При перемещении частиц без ускорения – состояние равновесное.
Неустойчивая стратификация способствует вертикальным перемещениям, устойчивая – их затуханию.
- неустойчивая стратификация
- равновесие
- устойчивая стратификация
Здесь: `Т – температура окружающей среды
Т – температура движущегося объема
При устойчивости атмосферы объем воздуха, перемещаясь адиабатически вверх, имеет большую плотность, чем окружающий воздух, и будет стремиться опуститься, т.е. вернуться в первоначальное положение. Аналогично при движении вниз.
- - - - - сухоадиабатический градиент температуры
- градиент температуры воздуха
Рисунок 17 - Профили скорости ветра, температурный профиль и форма дымовой струи для различных атмосферных условий
Когда с ростом высоты температура увеличивается, градиент температуры положительный, и атмосферные условия определяются как инверсия – весьма устойчивая атмосфера. Температура уменьшается в среднем на 0,65 К на каждые 100 м подъема. Выше 40 км температура неизменна.
Расчет рассеивания
Расчет рассеивания включает в себя расчет приземных концентраций вредных веществ, расчет дымовой трубы и опасной скорости ветра. Как известно, при всех способах очистки в дымовых газах остается определенное количество вредных веществ. Санитарные нормы требуют, чтобы максимальная концентрация каждого вредного вещества Сmi, мг/м3, в приземном слое атмосферы была не больше предельно допустимой концентрациикаждого вредного вещества в атмосферном воздухе (ПДК). То есть .
Величина Сm при эвакуации веществ из дымовых труб существенно зависит от характера турбулентного перемешивания с окружающим атмосферным воздухом. Этот процесс существенно зависит от высоты дымовой трубы Н и средней скорости выхода газов из трубы wo. С ростом Н и wo максимальная приземная концентрация уменьшается и может быть доведена до нормативных значений.
Максимальная приземная концентрация вредных веществ для выброса нагретой смеси газов из одиночного точечного источника с круглым устьем определяется по формуле, мг/м3:
где А – коэффициент, определяющий условия рассеивания в данном районе планеты (для Казахстана А = 200);
Мi – количество вредного вещества, выбрасываемого в атмосферу, г/с;
F – коэффициент, учитывающий скорость оседания вредных веществ в атмосфере; F = 1 для газообразных примесей; для пыли при степени улавливания более 90 % F = 2; менее 90 % - F = 2,5.
m и n – безразмерные коэффициенты, учитывающие условия выхода газовоздушной смеси из устья дымовой трубы;
V - объем выбрасываемых дымовых газов, м3/с;
DТ – разность температуры выбрасываемой газовоздушной смеси tг и температуры окружающего атмосферного воздуха tв, оС;
Н – высота дымовой трубы, м.
Коэффициент m находится в зависимости от параметра f:
здесь wo – средняя скорость выхода газов, м/с;
Dо – диаметр устья дымовой трубы, м.
Коэффициент n находится в зависимости от параметра
Если vм £ 0,3 n = 3; ________________
Если 0,3 < vм £ 2 n = 3 - Ö (vм – 0,3)(4,36 - vм) ,
Если vм > 2 n = 1.
Наибольшие концентрации в приземном слое обычно имеют место при некоторой скорости ветра um, называемой опасной скоростью ветра. При скорости ветра равной и меньше опасной не осуществляется должного рассеивания вредных выбросов. Она определяется в процессе расчета.
Если vм £ 0,5, um = 0,5 м/с;
Если 0,5 £ vм £ 2, um = vм; _
Если vм > 2, um = vм (1 + 0,12Öf ).
3 . Получение полезных веществ из дымовых газов котлов
В результате сгорания топлива из дымовых газов образуются окислы серы SO2 и SO3, окислы азота, углекислый газ, водяные пары, летучая зола и другие вещества. В зависимости от местных условий может оказаться целесообразно производство азота или углекислоты, но наиболее важно превратить токсичные вещества в полезные. Например, известняковый метод очистки дымовых газов от оксидов серы позволил получить сульфат кальция, который после обезвоживания и сушки превращается в гипс СаSO4. Аналогичный материал получают при использовании метода распылительной абсорбции для улавливания оксидов серы.
Применение магнезитового циклического метода дает возможность получить при обжиге сульфита и бисульфита магния товарный диоксид серы для производства Н2SO4, аммиачно-циклический метод сопровождается производством сниженного сернистого ангидрида и сульфата аммония (NH4)2SO4; внедрение озонного метода очистки дымовых газов от SOX и NOX приводит к получению нитрата и сульфита аммония NHNO3, которые используется в качестве удобрений как раздельно, так и в смеси.
В золе топлива содержится ряд ценных микроэлементов – стимуляторов роста растений (медь, марганец, бор, фосфор). Сланцевая зола может применяться при производстве строительных материалов.
Золы многих других энергетических топлив имеют в своем составе небольшое количество оксида кальция и используется для производства пористых заполнителей.
Летучая зола большинства топлив может быть использована как наполнитель углеводородных вяжущих веществ при подготовке покрытий в дорожном строительстве. В значительных количествах зола используется для возведения дамб на золоотвалах.
Шлак и зола ТЭС, сжигающих мазут, может использоваться как сырье для производства ванадия и никеля.
При нейтрализации едким натром сточных вод поле обмывки ВЗП получается обогащенный ванадием осадок, натриевый шлам с влажностью до 50 %; V205 = 11, 7 – 27,6 %; Fе общ = 27,8 – 34,2 % ; Ni = 0,4 – 0,9 %.
Из – за дефицита и высокой стоимости едкого натра наибольшее распространение получила нейтрализация известковым молоком, при котором получается кальциевый шлам с составом.
V2 05 = 1,7÷ 5,1 %; Ni = 0,3 ÷ 0,9 %
Ca = 5,6 ÷ 23,4 %; Fе общ = 13,2 ÷ 33,5 %; Sобщ = 2,7÷ 7,9%.
6. Контрольные вопросы:
1. Рассеивание выбросов, условия работы дымовых труб
2. В чем заключается расчет рассеивания?
3. Утилизация дымовых газов.
Дата добавления: 2019-01-14; просмотров: 810; Мы поможем в написании вашей работы! |
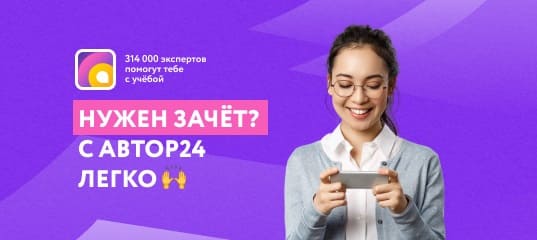
Мы поможем в написании ваших работ!