Объем отстойной зоны реактора
В этой зоне происходит разделение выходящих из пятой секции реактора углеводородов и серной кислоты.
Зная массовые количества жидких компонентов, покидающих пятую секцию (таблица 1.13), и их плотности, найдем объемное количество смеси. Оно составит Rm 5 = 257,2 м3/ч. Принимая время отстоя τ0 = 60 мин и степень заполнения φ = 0,7, найдем объем зоны отстоя:
; (1.25)
Тогда длина зоны будет
; (1.26)
Объем реактора
Найдем общую длину цилиндрической части реактора
, (1.27)
где - длина реакционной зоны.
Объем цилиндрической части реактора (практически равный его объему) будет равен
; (1.28)
Расчет процесса изомеризации УГЛЕВОДОРОДОВ
Возможность изомеризации парафиновых углеводородов на хлориде алюминия была впервые обнаружена в 1933 г. К. Ненитцеску и А. Драганом. В 1935 г. Б.Л. Молдавский открыл возможность промотирования реакции изомеризации хлористым водородом, что предопределило практическое применение этой реакции. Ранние промышленные процессы изомеризации были предназначены для получения изобутана из н-бутана на хлористом алюминии при мягком температурном режиме (90-120 °С). Изобутан далее алкилировали бутиленами и в результате получали изооктан.
Целевым назначением процессов каталитической изомеризации в современной нефтепереработке является получение высокооктановых изокомпонентов автобензинов или сырья нефтехимии, прежде всего изопентана для синтеза изопренового каучука [10]. Высокая эффективность процессов изомериации зпаключается в том, что в качестве сырья используются низкооктановые компоненты нефти – фракции н.к.-62 °С и рафинаты каталитического риформинга, содержащие в основном н-пентан и н-гексан. Это сырье (а также фракции С5 и С6, получаемые с ГФУ) изомеризуется в среде водорода в присутствии бифункциональных катализаторов.
|
|
Нормальный пентан, который характеризуется октановым числом 62 (ИОЧ), превращается в изопентан, ИОЧ которого 92. В случае гексана изменение ИОЧ в результате изомеризации еще более значительно от 25 до, примерно, 75. Стандартная смесь, содержащая нормальные и изо-пентаны и гексаны, облагораживается в этом процессе (ИОЧ меняется от 73 до 91) [11].
Процессы изомеризации парафиновых углеводородов играют значительную роль в нефтеперерабатывающей и нефтехимической промышленности. Наличие установки изомеризации на НПЗ позволяет увеличить долю высокооктановых бензинов с 60 до 86%. Лёгкий изомеризат, с экологической точки зрения, гораздо менее вреден, чем ароматика и различного рода присадки, повышающие детонационную стойкость. Также наличие лёгких фракций в автобензинах определяет стабильную работу двигателей внутреннего сгорания на стадии пуска, особенно при пониженных температурах в зимних условиях эксплуатации.
|
|
Высокие детонационная стойкость и испаряемость продуктов изомеризации углеводородов С5 и С6 обусловливают их исключительную ценность в качестве низкокипящих высокооктановых компонентов неэтилированных автобензинов.
В настоящее время в России и за рубежом работает более 100 установок изомеризации парафиновых углеводородов с использованием различных бифункциональных катализаторов. В последние годы изомеризация легких бензиновых фракций становится по существу стратегическим «бензиновым» процессом, обеспечивающим октановые характеристики суммарного бензинового фонда [12].
Ввод в эксплуатацию установки изомеризации одновременно решает следующие задачи:
- снижение доли автомобильного бензина с низким октановым числом в «бензиновом пуле» с 41,7 до 9,8% масс.;
- снижение содержания бензола в тяжелом риформате до 1 % масс.;
- производство стабильного изомеризата с ОЧ=86 пунктов и использование его в качестве компонента автомобильных бензинов с улучшенными характеристиками;
|
|
- организация производства экологически чистых автобензинов по нормам Евро-4 и Евро-5 в объеме 90,2 % масс. [13].
Рисунок 2.1 – Схема установки изомеризации «за проход»
Исходные данные
В таблице 2.1 представлены варианты исходных данных для расчета реактора изомеризации.
Таблица 2.1 – Варианты заданий для расчета реактора изомеризации
Вариант | Производитель-ность установки, тыс.т/год | Время работы установки, дни | Массовый расход ВСГ, % масс. на сырье | Температура процесса, оС | Давление, МПа |
1 | 100 | 330 | 0,1 | 450 | 3,0 |
2 | 70 | 350 | 0,2 | 350 | 3,5 |
3 | 80 | 340 | 0,15 | 400 | 4,0 |
4 | 120 | 300 | 0,3 | 430 | 4,5 |
5 | 150 | 320 | 0,25 | 360 | 5,0 |
6 | 140 | 340 | 0,1 | 370 | 3,8 |
7 | 80 | 330 | 0,2 | 430 | 4,3 |
8 | 110 | 350 | 0,15 | 420 | 5,2 |
9 | 200 | 360 | 0,3 | 480 | 3,9 |
10 | 160 | 320 | 0,25 | 380 | 4,6 |
11 | 180 | 330 | 0,1 | 400 | 4,8 |
12 | 200 | 350 | 0,2 | 350 | 5,0 |
13 | 220 | 340 | 0,15 | 450 | 4,0 |
14 | 150 | 300 | 0,3 | 350 | 3,7 |
15 | 100 | 320 | 0,25 | 400 | 3,0 |
16 | 210 | 340 | 0,1 | 430 | 3,5 |
17 | 150 | 330 | 0,2 | 360 | 4,0 |
18 | 180 | 350 | 0,15 | 370 | 4,5 |
19 | 250 | 360 | 0,3 | 430 | 5,0 |
20 | 240 | 320 | 0,25 | 420 | 3,8 |
21 | 140 | 330 | 0,1 | 480 | 4,3 |
22 | 150 | 350 | 0,2 | 380 | 5,2 |
23 | 230 | 340 | 0,15 | 400 | 3,9 |
24 | 160 | 300 | 0,3 | 350 | 4,6 |
25 | 70 | 320 | 0,25 | 450 | 4,8 |
26 | 80 | 340 | 0,1 | 350 | 5,0 |
27 | 90 | 330 | 0,2 | 400 | 4,0 |
28 | 110 | 350 | 0,15 | 430 | 3,7 |
29 | 100 | 360 | 0,3 | 360 | 5,2 |
30 | 200 | 320 | 0,25 | 370 | 5,3 |
|
|
По данным об имеющимся сырье принимаем производительность установки 100 тыс. тонн в год. Сырьём является фракция нк-62оС каталитического риформинга (таблица 2.2). Число рабочих дней установки принимаем 300 дней в году.
Таблица 2.2 – Состав сырья блока изомеризации
Сырьё | % масс. | кг/ч | т/сут | тыс. т/г |
пропан | 0,904 | 125,556 | 3,013 | 0,904 |
i-бутан | 6,024 | 836,667 | 20,08 | 6,024 |
н-бутан | 14,971 | 2079,306 | 49,903 | 14,971 |
i-пентан | 37,425 | 5197,917 | 124,75 | 37,425 |
н-пентан | 25,265 | 3509,028 | 84,217 | 25,265 |
2,2-ДМБ | 1,497 | 207,917 | 4,99 | 1,497 |
ц-пентан | 4,104 | 570 | 13,68 | 4,104 |
i-гексаны | 5,083 | 705,972 | 16,943 | 5,083 |
н-гексан | 1,762 | 244,722 | 5,873 | 1,762 |
ц-гексан | 0,091 | 12,639 | 0,303 | 0,091 |
бензол | 1,491 | 207,08333 | 4,97 | 1,491 |
толуол | 0,992 | 137,778 | 3,3067 | 0,992 |
С7+ | 0,391 | 54,306 | 1,3033 | 0,391 |
Всего | 100 | 13888,889 | 333,333 | 100 |
2.2 Расчёт реактора изомеризации
По данным с существующих установок с использованием катализатора СИ-2 принимаем степень конверсии н-парафинов:
- н-пентана – 98,4%,
- н-гексана – 98,7%.
Также принимаем выход побочных продуктов в % масс. на продукт:
- углеводороды ниже С5 – 2,2%,
- углеводороды выше С6 – 1,3%,
- потери 0,004%.
Материальный баланс реактора
Аналогично по данным с существующих установок принимаем, что блок подготовки сырья изомеризации обеспечивает выделение фракции, содержащей 90,32% н-пентана. Состав сырья реактора Р-2 представлен в таблице 2.3.
Таблица 2.3 – Состав сырья реактора Р-2
Состав | Массовые доли | кг/ч | M, г/моль | моль/ч | Мольные доли
|
i-пентан | 0,016 | 62,038 | 72 | 861,64 | 0,0153 |
н-пентан | 0,903 | 3509,028 | 72 | 48736,497 | 0,864 |
i-гексан | 0,061 | 236,52 | 86 | 2750,234 | 0,049 |
н-гексан | 0,018 | 69,792 | 86 | 811,544 | 0,0144 |
ВСГ | 0,002 | 7,755 | 2,4 | 3231,149 | 0,057 |
Всего | 1,000 | 3885,134 |
| 56391,064 | 1 |
По принятым степеням конверсии и выходу побочных продуктов рассчитаем состав продуктов процесса:
G(iC5)=G(iC5)сыр+G(нС5)·к(С5), (2.1)
где G(iC5) – суммарный выход изопентана, кг/ч; G(iC5)сыр – содержание изопентанов в сырье, кг/ч; G(нС5) – содержание н-пентанов в сырье, кг/ч; к(С5) – степень конверсии н-пентанов.
G(iC6)=G(iC6)сыр+G(нС6)·к(С6), (2.2)
где G(iC6) – суммарный выход изогексанов, кг/ч; G(iC6)сыр – содержание изогексанов в сырье, кг/ч; G(нС6) – содержание н-гексанов в сырье, кг/ч; к(С6) – степень конверсии н-гексанов.
Состав продуктов реактора представлен в таблице 2.4.
Таблица 2.4 – Состав продуктов реактора
Состав | Массовые доли | кг/ч | r204 |
Газы до С4 | 0,0213 | 82,579 | 0,5 |
i-пентан | 0,874 | 3395,928 | 0,659 |
Н-пентан | 0,014 | 54,244 | 0,62 |
i-гексан | 0,076 | 295,066 | 0,656 |
Н-гексан | 0,00023 | 0,876 | 0,659 |
ВСГ на регенерацию | 0,001928 | 7,492 | - |
Газы выше С7 | 0,0126 | 48,797 | 0,7 |
Потери | 3,86·10-05 | 0,15 | - |
Всего | 1,000 | 3885,134 | 0,654 |
Тепловой баланс реактора
Основная задача расчета теплового баланса заключается в нахождении температуры сырья на входе в реактор. Так как процесс изомеризации происходит с выделением тепла от 6 до 8 кДж/моль, то для поддержания температуры реакции необходимо найти количество тепла, выделавшегося в процессе реакций изомеризации.
Примем конечную температуру продуктов изомеризации 130оС, теплоту реакции изомеризации 7 кДж/моль.
Принимая, что в процессе изомеризации подвергаются только пентаны и гексаны, с учетом количества молей углеводородов (таблица 2.3) общее количество тепла, выделяющееся при изомеризации пентанов и гексанов составит
Qреак=(Gm(C5)·k(C5)+Gm(C6)·k(C6))·qэф, (2.3)
где Gm – количество углеводорода, поступающего с сырьём, моль/ч; qэф – тепловой эффект реакции (7 кДж/моль).
Qреак= 48736,5·0,984·7/1000+811,544·0,987·7/1000=335,697+ 5,607= =341,304 МДж/ч.
По известным конечной температуре процесса и составу продукта, рассчитаем теплосодержание продукта на выходе из реактора. Теплосодержание жидкой фазы углеводородов определим по уравнению
qпр=(1,689·t2+0,0017·(t22))·((0,9943·r204+0,00915)0,5)-1, (2.4)
где t2 – конечная температура процесса (130 оС); r204 – средняя плотность компонентов сырья.
Плотность смеси рассчитаем исходя из массовых долей компонентов (таблица 2.4)
, (2.5)
где ri – мольная доля i- компонента.
Тогда
qпр=305,709 кДж/кг.
Теплосодержание ВСГ при температуре t2 определим по формуле
qВСГ=10,976·t2 + 492,68, (2.6)
qВСГ=1919,63 кДж/кг.
Общее теплосодержание смеси на выходе из реактора
Qпр= qВСГ·GВСГ+ qпр·Gпр, (2.7)
где GВСГ – расход ВСГ на выходе из реактора, кг/ч; Gпр – расход смеси углеводородов без ВСГ и потерь на выходе из реактора, кг/ч.
Qпр= 1919,63·7,492+(3885,134-0,15-7,492)· 305,709=1199,767 МДж/ч.
Зная тепловой эффект реакции, а также энтальпию продуктов на выходе из реактора можно определить теплосодержание сырьевой смеси (Q0c) поступающей в реактор по формуле
Q0c= Qпр - Qреак, (2.8)
Q0c=1199,767 - 341,304=858,463 МДж/ч.
Методом подбора температуры на входе сырья в реактор и рассчитывая значение энтальпии смеси, необходимо добиться, чтобы значение рассчитанной энтальпии было равно ранее полученному, исходя из теплового баланса (Q0c).
Пусть температура сырья на входе в реактор составит t0=93,7оС. Рассчитаем, зная компонентный состав сырья (таблица 2.3), его теплосодержание при t0 по формуле (2.4). Среднюю плотность углеводородов сырья рассчитаем исходя из их массовых долей (таблица 2.4).
Теплосодержание углеводородной смеси на входе в реактор составит
qсыр=(1,689·93,7+0,0017·(93,72))·((0,9943·0,6235+0,00915)0,5)-1=218,342 кДж/кг.
Таблица 2.5 – Расчёт плотности углеводородов в сырье
Состав | Массовые доли | кг/ч | Плотность относительная |
i-пентан | 0,016 | 62,03806 | 0,659 |
н-пентан | 0,905 | 3509,028 | 0,62 |
i-гексан | 0,061 | 236,5201 | 0,656 |
н-гексан | 0,018 | 69,79282 | 0,659 |
Сырье |
| 3877,379 | 0,6235 |
Теплосодержание ВСГ находим по (2.6)
qВСГ=10,976·93,7 + 492,68=1521,183 кДж/кг.
Общее теплосодержание углеводородов с ВСГ с учётом массового расхода рассчитаем по (2.7)
Q¢ºс=218,342·3877,379+1521,183·7,755= 858,389 МДж/ч.
Для определения правильности выбранной температуры определим расхождение теплосодержания сырья реактора, рассчитанного по тепловому балансу (Qºс), и теплосодержания сырья, рассчитанного по принятой температуре t0 на входе в реактор (Q¢ºс).
DQ=100% · (Qºс - Q¢ºс )/Qºс (2.9)
DQ=(858,463-858,389)·100/858,463»0,01%.
Таким образом, температура t0 принята с достаточной точностью и может использоваться для дальнейших расчётов.
Дата добавления: 2019-01-14; просмотров: 848; Мы поможем в написании вашей работы! |
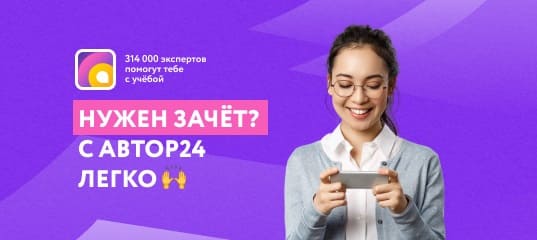
Мы поможем в написании ваших работ!