Теоретическая оценка свариваемости
БИЛЕТ № 11
1. Дефекты сварных соединений группы 5- нарушение формы шва, определения и причины их возникновения.
2. Аппараты ультразвукового контроля.
Для проверки понадобится дефектоскопы и преобразователи, набор эталонов, образцов, предназначенных для калибровки и настройки оборудования. Определение расположения, места дефектов производится с помощью линейки координатного типа, вспомогательные приспособления понадобятся для зачистки, смазки проверяемого шва.
Проверенный сварной шов гарантирует надежность, прочность конструкции при эксплуатации. Существуют определенные нормативы, по которым изделие вводится в эксплуатацию или дорабатывается дальше.
Для излучения и приема УЗ колебаний используются устройства, называемые преобразователями. Основным элементом в них являются пластинка пьезоэлемента. Толщину пластинки выбирают такой, чтобы собственная частота колебаний пластинки соответствовала частоте подводимых колебаний. Если к пьезоэлементу подвести частоту электрического поля, равную частоте его собственных колебаний, то наступает явление резонанса, сопровождаемое резким возрастанием амплитуды колебаний, что значительно увеличивает мощность излучаемых УЗ волн и улучшает возможности метода по чувствительности и глубине прозвучивания. В комплект дефектоскопа входят несколько преобразователей. Каждый из них предназначен для работы на определенной частоте, равной частоте собственных колебаний его пьезоэлемента. Различают два основных типа преобразователей: • прямые (нормальные) и • наклонные (призматические). Прямые преобразователи служат для ввода УЗ-волн перпендикулярно поверхности изделия. Наклонные преобразователи служат для ввода поперечных УЗ-волн под некоторым углом к поверхности изделия, который называют углом призмы. Конструктивно и функционально преобразователи могут быть: • совмещенные - излучатель и приемник ультразвуковых волн находятся в одном преобразователе, • раздельные - указанные функции выполняют два раздельных преобразователя, • раздельно-совмещенные - излучатель и приемник совмещены в одном корпусе, однако каждый из них может работать как в режиме излучения так и режиме приема. Конструкция преобразователя обеспечивает защиту пьезоэлемента от механических повреждений и износа. Чтобы излучаемую волну ввести в изделие, между ними должен быть акустический контакт. Его обеспечивают заполнением контактирующей жидкостью зазора между плоскостью преобразователя и поверхностью изделия. Для этого используют минеральные масла, солидол, глицерин, спирт, воду и т.д.
|
|
|
|
БИЛЕТ № 12
1. Визуальный и измерительный контроль качества сварных швов.
Самостоятельно !!!!!!
2. Магнитопорошковая дефектоскопия, сущность, область применения.
Смотри билет 3 вопрос 2
БИЛЕТ № 13
1. Дефекты сварных соединений группы 4-несплавления и непровары, определения и причины их возникновения.
2. Способы устранения дефектов сварки плавлением.
Смотри билет 8 вопрос 1
БИЛЕТ № 14
1. Капиллярная дефектоскопия, сущность, область применения.
Капиллярная дефектоскопия – является одним из основных методов неразрушающего контроля и предназначена для обнаружения поверхностных и сквозных дефектов в объектах контроля, определения их расположения, протяженности (для протяженных дефектов типа непроваров, трещин) и их ориентации на поверхности. Капиллярный метод неразрушающего контроля (ГОСТ 18442-80) основан на капиллярном проникновении внутрь дефекта индикаторных жидкостей, хорошо смачивающих материал объекта – поверхность контроля и последующей регистрации индикаторных следов (благодаря чему так же носит название цветная дефектоскопия). В соответствии с техническими требованиями в большинстве случаев необходимо выявлять настолько малые дефекты, что заметить их при визуальном осмотре невооруженным глазом практически невозможно. В то же время, применение оптических приборов, например лупы или микроскопа, не позволяет выявить поверхностные дефекты из-за недостаточной контрастности изображения дефекта на фоне металла и малого поля зрения при больших увеличениях. В таких случаях наиболее применим - капиллярный метод контроля. Капиллярная дефектоскопия позволяет контролировать объекты любых размеров и форм, изготовленные из различных материалов: черных и цветных металлов, сплавов, пластмасс, стекла, керамики и т.п. Капиллярный контроль широко востребован при дефектоскопии сварных швов.
|
|
При контроле красящий пенетрант наносится на контролируемую поверхность и благодаря своим особым качествам под действием капиллярных сил проникает в мельчайшие дефекты, имеющие выход на поверхность объекта контроля. Проявитель, наносимый на поверхность объекта контроля через некоторое время после осторожного удаления с поверхности пенетранта, растворяет находящийся внутри дефекта краситель и за счет диффузии “вытягивает” оставшийся в дефекте пенетрант на поверхность объекта контроля. Имеющиеся дефекты видны достаточно контрастно. Индикаторные следы в виде линий указывают на трещины или царапины, отдельные точки - на поры.
|
|
Процесс капиллярного контроля состоит из 5 этапов:
1 – предварительная очистка поверхности.
Чтобы краситель мог проникнуть в дефекты на поверхности, ее предварительно следует очистить водой или органическим очистителем. Все загрязняющие вещества (масла, ржавчина, и т.п.) любые покрытия (ЛКП, металлизация) должны быть удалены с контролируемого участка. После этого поверхность высушивается, чтобы внутри дефекта не оставалось воды или очистителя.
2 – нанесение пенетранта.
Пенетрант, обычно красного цвета, наносится на поверхность путем распыления, кистью или погружением объекта контроля в ванну, для хорошей пропитки и полного покрытия пенетрантом. Как правило, при температуре 5…50°С, на время 5…30 мин.
3 - удаление излишков пенетранта.
Избыток пенетранта удаляется протиркой салфеткой, промыванием водой, или тем же очистителем, что и на стадии предварительной очистки. При этом пенетрант должен быть удален только с поверхности контроля, но никак не из полости дефекта. Затем поверхность высушивается салфеткой без ворса или струей воздуха.
4 – нанесение проявителя.
После просушки сразу же на поверхность контроля тонким ровным слоем наносится проявитель (обычно белого цвета).
5 - контроль.
Выявление имеющихся дефектов начинается непосредственно после окончания процесса проявки. При контроле выявляются и регистрируются индикаторные следы. Интенсивность окраски которых говорит о глубине и ширине раскрытия дефекта, чем бледнее окраска, тем дефект мельче. Интенсивную окраску имеют глубокие трещины. После проведения контроля проявитель удаляется водой или очистителем.
Пенетрант — специальное индикаторное вещество, проникающее в дефекты материала под действием сил капиллярности. Используются при контрастной и люминесцентной дефектоскопии. Наносятся на поверхности контролируемых изделий. Пенетранты представляют собой несущую основу с цветным (чаще всего красным) красителем или люминофором[1]. Люминесцентные пенетранты под воздействием ультрафиолетового излучения имеют, как правило, желто-зеленый цвет свечения. Дефект становится виден при извлечении пенетранта из дефекта адсорбирующим слоем проявителя (он же служит контрастирующим фоном). В этом случае говорят, что пенетрант образует индикацию дефекта.
Различия пенетрантов
по способу наблюдения - контрастные и люминесцентные
по способу удаления - водосмываемые и удаляемые очистителем (пост-эмульгируемые)
по чувствительности (в порядке убывания - I, II, III и IV классы по ГОСТ 18442-80).
Следует отметить, что уровни чувствительности по стандартам MIL-I-25135E и AMS-2644 прямо противоположны ГОСТ 18442-80:
1/2 - ультранизкая чувствительность 1 - низкая 2 - средняя 3 - высокая 4 - сверхвысокая
Пенетранты поставляются в аэрозольных упаковках (считающихся наиболее удобными для автономной работы на объекте), канистрах и в бочках.
Метод испытания керосином
Этот метод, при котором в качестве проникающего вещества используют керосин (керосиновая проба), получил широкое распространение благодаря своей простоте и сравнительно высокой чувствительности. С помощью керосина контролируют открытые изделия – емкости, элементы гидравлических и газовых систем. В ряде случаев этот метод используют и при испытаниях закрытых систем – топливных отсеков, баков, а также сварных соединений различных изделий.
Высокая проникающая способность керосина обусловлена тем, что он не является полярно-активной жидкостью, имеет сравнительно низкую вязкость, хорошо растворяет пленки жира и устраняет пробки в неплотностях. В качестве индикатора течи используют меловую обмазку того же состава, что и при гидравлических испытаниях.
Различают четыре способа испытаний: керосиновый; керосинопневматический; керосиновакуумный; керосиновибрационный.
Контроль керосиновым способом выполняют следующим образом. На места контроля, предназначенного для осмотра, наносят меловую обмазку. Противоположную сторону изделия несколько раз смачивают керосином либо укладывают на нее ленту или кусок ткани, смоченные керосином. После выдержки, определяемой ТУ на изделие, его осматривают, выявляя места течей по пятнам керосина цвета ржавчины на меловой обмазке.
Иногда для повышения чувствительности контроля керосин окрашивают, растворяя в нем краски ярких цветов. Керосиновым способом могут быть выявлены течи диаметром до 0,1 мм в изделиях толщиной до 25 мм.
При керосинопневматическом способе контроля изделие после смачивания керосином обдувают струей сжатого воздуха под давлением 0,3...0,4 МПа, что повышает чувствительность контроля и ускоряет выявление дефектов.
Керосиновакуумный способ основан на применении переносных вакуумных камер, устанавливаемых на контролируемое изделие со стороны меловой обмазки. При этом так же, как и при керосинопневматическом способе, повышаются чувствительность и производительность контроля.
При керосиновибрационном способе на изделие, смоченное керосином, воздействуют ультразвуковыми колебаниями, что существенно ускоряет процесс проникновения керосина в неплотности и также повышает чувствительность и производительность контроля.
Чувствительность способов испытаний керосином существенно зависит от чистоты последнего. Примеси, растворяемые керосином, повышают его вязкость, что приводит к уменьшению потока через течь, которая при малых размерах может закупориться. Особое влияние на чувствительность испытаний оказывают компоненты смазок, применяемых при сборке гидро- и газовых систем и вымываемых керосином из объектов в процессе контроля. Использование загрязненной проникающей жидкости может привести к невыявлению скрытых дефектов, которые в дальнейшем, при эксплуатации изделия, могут проявиться в виде значительных течей.
2. Правила безопасности при УЗК.
Ультразвуковой контроль При выполнении контроля должны соблюдаться требования СанПиН 2.2.4/2.1.8.582-96 и требования безопасности, изложенные в технической документации на применяемую аппаратуру, утвержденной в установленном порядке. Запрещается непосредственный контакт работающих с рабочей поверхностью оборудования в процессе его обслуживания, жидкостью и обрабатываемыми деталями во время возбуждения в них ультразвука. Для исключения контакта с источниками ультразвука необходимо применять:
дистанционное управление оборудованием;
автоблокировку, т.е. автоматическое отключение оборудования при выполнении вспомогательных операций (загрузке и выгрузке продукции, нанесении контактных смазок и т.д.);
приспособления для удержания источника ультразвука или обрабатываемой детали.
Для защиты рук от возможного неблагоприятного воздействия контактного ультразвука в твердой или жидкой средах, необходимо применять две пары перчаток – резиновые (наружные) и хлопчатобумажные (внутренние) или только хлопчатобумажные.
Для защиты работающих от неблагоприятного воздействия воздушного ультразвука следует применять противошумы.
БИЛЕТ № 15
1. Свариваемость металла, расчетная оценка свариваемости.
Свариваемость сталей – свойство металла или сочетаний металлов образовывать при установленной технологии сварки соединение, отвечающее требованиям, обусловленным конструкцией и эксплуатацией изделия (ДСТУ 3761.1-98).
Свариваемость стали прежде всего зависит от содержания в ней основного (после железа) химического элемента – углерода. Низкоуглеродистые стали с содержанием С ≤ 0,25% свариваются хорошо. Это стали для строительных металлоконструкций. С повышением содержания углерода до 0,45% свариваемость стали ухудшается; плохо свариваются высокоуглеродистые стали – с содержанием до 0,9% углерода.
Ухудшают свариваемость многие химические элементы, применяемые в производстве легированных сталей: такие как марганецMn, хромCr, молибденМо, ванадийV, кремнийSi, медьCu, а также примесь – фосфорР.
С увеличением содержания в стали углерода, как наиболее изученного по влиянию на различные свойства стали химического элемента, повышается вероятность ликвационной неоднородности металла, выделение по границам зерен сульфидных включений, способствующих трещинообразованию; увеличивается склонность к образованию в зоне термического влияния (ЗТВ) весьма хрупкой структуры мартенсита, повышающей внутренние напряжения и склонность стали к образованию трещин. Аналогично действуют в большей или меньшей степени легирующие элементы в составе стали.
Вместе с тем, при соблюдении технологии сварки, свариваемость многих низколегированных строительных сталей хорошая и без специальных технологических мероприятий. Некоторые низколегированные стали для строительных конструкций свариваются удовлетворительно при применении дополнительных технологических приемов.
Оценка свариваемости стали
Оценка свариваемости стали осуществляется путем учета ряда важнейших факторов, определяющих технологические и потребительские свойства стального проката, сварных соединений и швов:
- химический состав металла;
- скорость охлаждения металла в процессе сварки;
- характер первичной кристаллизации и последующих структурных превращений при охлаждении;
- склонность металла сварного соединения к образованию закалочных структур;
- склонность сварного соединения из данной стали к образованию горячих и холодных трещин;
- получение сварного шва требуемых химического состава, механических и других свойств.
За многие десятилетия развития технологии сварки при изготовлении строительных и других конструкций выявлено наибольшее влияние на свариваемость соединения в ней углерода и меньшее – других химических элементов, в связи с чем приравнивают их влияние к соответствую количеству (эквиваленту) углерода.
Теоретическая оценка свариваемости
Такая оценка осуществляется на основе фактического химического состава стали по данным сертификата производителя.
Действующий стандарт на прокат для строительных стальных конструкций ГОСТ 27772-88, в соответствии с которым углеродный эквивалент Сэ, %, определяют по формуле
,
где C, Mn, Si, Cr, Ni, Cu, V, P– массовые доли углерода, марганца, кремния, хрома, никеля, меди, ванадия и фосфора, %.
В зависимости от углеродного эквивалента и связанной с этим склонностью к закалке и образованию холодных трещин, стали по свариваемости делят на:
- хорошо сваривающиеся без образования закалочных структур и трещин в широком диапазоне режимов, толщин и конструктивных форм;
- удовлетворительно сваривающиеся, мало склонные к образованию холодных трещин при правильном подборе режимов сварки, в ряде случаев требуется подогрев;
- ограниченно сваривающиеся стали, склонны к трещинообразованию, возможность изменения сопротивляемости образованию трещин за счет режимов сварки весьма ограничена, требуется подогрев;
- плохо сваривающиеся стали, весьма склонны к закалке и трещинам, требуют при сварке подогрева, специальных технологических приемов сварки и термообработки.
Этот метод используют чаще всего при разработке технологии сварки при изготовлении конструкций. Окончательная оценка свариваемости может быть дана после проведения рядов испытаний (металлографических, механических и т.д.), проводимых на образцах (экспериментальные испытания) в соответствии с рекомендациями ГОСТ, ТУ и т.д.
2. Виды механических испытаний сварных соединений.
Механические испытания металла сварных швов и околошовной зоны позволяют определить численное значение прочности, пластичности и вязкости материалов в различных условиях их работы.
В соответствии с характером действующих сил механические испытания делятся на три вида:
статические, когда усилие (нагрузка на образец) плавно возрастает или длительное время остается постоянным. К ним относятся испытания на растяжение, изгиб и ползучесть, определение твердости и микротвердости различных участков сварного соединения и наплавленного металла;
динамические, при которых усилие возрастает практически мгновенно и действует короткое время. К ним относятся испытания на ударный изгиб, на ударный разрыв и стойкость против механического старения;
испытание на выносливость, когда нагрузка на образец многократно изменяется по величине или по направлению.
Механические испытания в лабораторных условиях проводят в соответствии с ГОСТ как при нормальных (комнатных), так и при пониженных или повышенных температурах в зависимости от условий последующей работы конструкций.
Испытание на статическое растяжение проводят для определения: предела прочности или временного сопротивления разрыву; физического или условного предела текучести; относительного удлинения после разрыва или относительного сужения. Испытание на растяжение производят на разрывных и универсальных машинах всех систем при условии соответствия их ГОСТам.
Пределы прочности и текучести определяют по диаграмме растяжения, которая автоматически записывается в процессе испытания.
Относительное удлинение и относительное сужение определяют путем непосредственного измерения длины образца и площади его сечения до и после испытания.
Для испытания на растяжение металла шва, металла различных участков околошовной зоны и наплавленного металла при всех видах сварки плавлением применяют круглые образцы Гагарина.
Для определения прочности стыковых и нахлесточных соединений применяют специальные плоские образцы без снятия усиления шва, а для определения прочности металла шва в стыковых соединениях — плоские и круглые образцы со снятым усилением и специальной выточкой, предопределяющей место разрушения.
В ГОСТе даны чертежи и таблицы с размерами образцов и с указаниями по их вырезке.
Для перевода предела текучести и временного сопротивления в МПа необходимо соответствующие данные, полученные в кг/мм2, умножить на 10, т. е. 1 кг/мм2= 10 МПа.
Дата добавления: 2019-01-14; просмотров: 261; Мы поможем в написании вашей работы! |
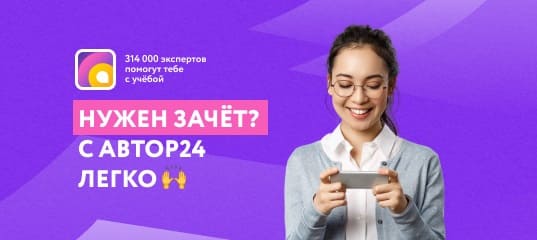
Мы поможем в написании ваших работ!