МЕТОДЫ ОБЕСПЬЧЕНИЯ ТРЕБУЕМОЙ ТОЧНОСТИ СБОРКИ
193
|
|
|
Рис. 133. Схема статической балансировки деталей
Рис. 134. Схема динамической балансировки деталей
ким образом, чтобы выполнялось условие
Наиболее часто балансировку проводят путем удаления некоторой массы металла с утяжеленной стороны детали (сверлением, фрезерованием). Статической балансировке подвергают детали, имеющие небольшую длину и относительно большой диаметр (шкивы, маховики, диски сцепления).
Для деталей, длина которых значительно превышает диаметр (коленчатые и карданные валы), применяют динамическую балансировку. Пусть деталь статически отбалансирована грузами массой т1 и т2 (рис. 134), расположенными диаметрально противоположно. При вращении вокруг оси 00 на концах детали возникнут две противоположно направленные центробежные силы 1Х и /,, образующие пару сил на плече /. Под действием центробежных сил возникнет момент, который будет выворачивать деталь из опор, создавая на них дополнительные нагрузки. Момент будет тем больше, чем длиннее деталь.
Для динамического уравновешивания детали необходимо в точках, противоположных участкам размещения грузов массой пг1 и т2, установить равные им по массе т\ и т'2. При вращении детали эти грузы создадут момент центробежных сил Г\ и /г, который уравновесит момент от уравновешивающих грузов массой т1 и т2.
Динамическую балансировку проводят при вращении детали на упругих опорах. Измеряют амплитуду максимальных колебаний одной из опор. К деталям прикрепляют пробный груз и, изменяя его массу, добиваются прекращения колебаний этой опоры. Те же операции повторяют для другой опоры.
|
|
§ 38. МЕТОДЫ ОБЕСПЕЧЕНИЯ ТРЕБУЕМОЙ ТОЧНОСТИ СБОРКИ
Сборкой завершается процесс ремонта. От качества ее выполнения зависит качество отремонтированного автомобиля, его надежность и долговечность. Технологический процесс сборки заключается в соединении деталей в узлы. Из узлов и отдельных деталей собирают агрегаты, а из агрегатов и узлов — автомобили.
Требуемая точность сборки может быть обеспечена следующими методами: полной взаимозаменяемости; неполной взаимозаменяемости; групповой взаимозаменяемости; регулирования; пригонки.
Метод полной взаимозаменяемости — это метод, при котором требуемая точность сборки узла, т. е. требуемая точность замыкающего звена размерной цепи достигается у всех изделий путем включения в нее составляющих звеньев баз вы-
7 Зак. 483
194
КОМПЛЕКТОВАНИЕ ДЕТАЛЕЙ . СБОРКА И ИСПЫТАНИЕ АВТОМОБИЛЕЙ
бора, подбора или изменения их размеров. Требуемая точность сборки изделия при этом методе зависит только от точности собираемых деталей. К преимуществам этого метода следует отнести простоту процессов комплектования и сборки изделий.
|
|
Применение метода полной взаимозаменяемости целесообразно при сборке узлов, состоящих из небольшого числа деталей. При большом числе деталей возникает необходимость обработки деталей с меньшими допусками, что не всегда достижимо и экономически целесообразно.
Метод неполной взаимозаменяемости — метод, при котором требуемая точность сборки без выбора, подбора или изменения размера деталей достигается не у всех узлов, а лишь у определенной их части. При этом методе сборки часть узлов не будет удовлетворять установленной точности и их придется разбирать и собирать повторно. В этом случае дополнительные затраты, связанные с введением сплошного контроля узлов и выполнением разборочно-сборочных работ, у некоторой части узлов значительно меньше затрат на обработку деталей с более узкими допусками, обеспечивающими получение требуемой точности сборки у всех изделий (узлов).
Преимуществами этого метода сборки являются простота процессов комплектования и сборки узлов, так как отсутствует необходимость подбора и подгонки деталей но размерам, а также более низкие требования к точности их обработки. К числу недостатков следует отнести введение сплошного контроля точности сборки для выявления изделий, имеющих отклонения от требуемой точности и дополнительные расходы, связанные с устранением этих недостатков.
|
|
Метод групповой взаимозаменяемости предусматривает предварительную сортировку деталей на размерные группы в пределах более узкого поля допуска. В пределах каждой размерной группы требуемая точность сборки достигается методом полной взаимозаменяемости.
Данный метод является наиболее эффективным. Он позволяет обеспечить высокую точность сборки при экономической точности и стоимости обработки сопрягаемых деталей. Причем высокую точность сборки изделий можно получить при использовании деталей с пониженной точностью. Например, большинство двигателей внутреннего сгорания по условиям надежности и долговечности работы требуют обеспечения допуска посадки поршневого пальца (допуск по наружному диаметру 0,010 мм) в бобышках поршня и во втулке верхней головки шатуна (допуск отверстий 0,010 мм), равного 0,005 мм. Сборка методом полной взаимозаменяемости обеспечит допуск 0,010+0,010=0,020 мм, что недопустимо. В этом случае действительный допуск посадки будет в 4 раза больше, чем требуется по техническим условиям. Поэтому для достижения требуемого допуска посадки сопрягаемые детали сортируют на четыре размерные группы с допуском 0,0025 мм в каждой. К недостаткам этого метода следует отнести более сложный процесс комплектования (сортировка деталей на размерные группы) и сложность процесса сборки.
|
|
Метод регулирования позволяет обеспечить требуемую точность сборки путем изменения размеров одной детали размерной цепи (компенсирующего звена) без удаления слоя материала. Например, требуемая точность осевого зазора (натяга) в соединении с коническими подшипниками качения (дифференциал, главная передача, механизм рулевого управления и др.) обеспечивается изменением толщины неподвижного компенсатора (группа колец, прокладок, регулировочных шайб и т. п.), а точность зазора между торцом клапана и болтом толкателя достигается путем изменения положения подвижного компенсатора — регулировочного болта в осевом направлении.
СБОРКА ТИПОВЫХ СОЕДИНЕНИИ
195
Этот метод широко применяется при сборке узлов из деталей с допустимым износом. Износ деталей при этом компенсируется установкой компенсаторов (шайб, прокладок и т.п.).
Методом пригонки требуемая точность сборки достигается путем изменения размера компенсатора со снятием слоя металла. Например, требуемая точность посадки плунжера в гильзе или клапана в корпусе форсунки, а также герметичность в соединении клапан — гнездо головки цилиндров обеспечивается притиркой.
СБОРКА ТИПОВЫХ СОЕДИНЕНИЙ
Процесс сборки узлов состоит из операций по сборке типовых соединений. Соединения деталей в зависимости от характера разделяются на подвижные и неподвижные, а в зависимости от возможности разборки — на разъемные и неразъемные. Детали подвижных соединений при работе могут перемещаться друг относительно друга. Разъемными являются соединения, которые могут быть разобраны без повреждения деталей. Разборка неразъемных соединений, полученных клепкой, сваркой и пайкой, обычно сопровождается повреждением детали.
При сборке автомобилей наибольшее применение нашли следующие виды разъемных соединений: прессовые; конусные; резьбовые; шлйцевые; шпоночные; зубчатые.
Прессовые соединения при сборке автомобилей применяются достаточно часто. Для запрессовки деталей с натягом в холодном состоянии применяют гидравлические прессы. Качество сборки прессового соединения зависит от многих факторов: материала сопрягаемых деталей; геометрических размеров; формы и шероховатости поверхностей; соосности деталей и прилагаемого усилия запрессовки и др.
При сборке деталей с большим натягом или деталей, изготовленных из материалов с различными коэффициентами линейного расширения, для облегчения сборки применяют нагрев или охлаждение.
Минимальная температура нагрева (°С) охватывающей стальной детали может быть определена по формуле
где А — диаметр отверстия в охватывающей детали, мм.
Нагревать деталь рекомендуется в масляной ванне.
Если коэффициент линейного расширения материала охватываемой детали больше, чем материала охватывающей детали, то перед сборкой рекомендуется охлаждать охватываемую деталь. Температура охлаждения (°С) детали может быть найдена по формуле
т — б+Д
Ыд '
где б — величина натяга, мкм; Ал—диаметр охватываемой детали, мм; к — коэффициент линейного расширения материала детали; Д — минимальный зазор для введения детали в отверстие (для А ^ 30 мм А ■-■- 0,0006^).
Для охлаждения детали до Т'-- — 75 "С можно использовать сухой лед (твердую углекислоту); при охлаждении деталей до более низких температур применяют жидкий воздух или азот.
Конусные соединения собирают таким образом, чтобы обеспечивалось плотное прилегание конусных поверхностей. Это достигается развертыванием отвер-7*
196
Дата добавления: 2019-01-14; просмотров: 630; Мы поможем в написании вашей работы! |
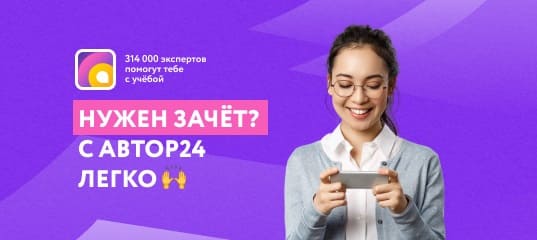
Мы поможем в написании ваших работ!