СПИСОК ИСПОЛЬЗОВАННЫХ ИСТОЧНИКОВ
Учреждение образования
«БЕЛОРУССКИЙ ГОСУДАРСТВЕННЫЙ ТЕХНОЛОГИЧЕСКИЙ УНИВЕРСИТЕТ»
Факультет ТТЛП
Кафедра Материаловедения и технологии металлов
Специальность 1-36 05 01 «Машины и оборудование лесного комплекса»
Специализация 1-36 05 01 01 «Машины и оборудование деревообрабатывающей промышленности»
ПОЯСНИТЕЛЬНАЯ ЗАПИСКА
КУРСОВОЙ РАБОТЫ
по дисциплине «Технология машиностроения»
Тема «Технологический процесс механической обработки детали № 4/6 (колесо зубчатое) с технико-экономическим обоснованием выбранного варианта техпроцесса»
Исполнитель |
| ||
Студент 4 курса группы 6 | ______________________ (подпись, дата) | Машталер В.В. | |
Руководитель |
| ||
Доцент | _______________________ (подпись, дата) | Куис Д.В. | |
Курсовой работа защищена с оценкой ______________ | |||
Руководитель | ______________________ (подпись) | Куис Д.В. | |
Минск 2009
Реферат
Пояснительная записка 33 с., 30 рис.,9 табл., 4 источника, 1 приложение
КЗО, ГОДОВОЙ ФОНД ВРЕМЕНИ, ШЕРОХОВАТОСТЬ, ТЕХНОЛОГИЧНОСТЬ КОНСТРУКЦИИ, КОЛЕСО ЗУБЧАТОЕ, ПЕРЕХОД, ОПЕРАЦИЯ, ЧЕРНОВАЯ ОБРАБОТКА, ЧИСТОВАЯ ОБРАБОТКА, ТВЕРДОСТЬ, ЗУБОШЕВИНГОВАНИЕ, ТРУДОЕМКОСТЬ, ЗАКАЛКА, ТЕХНИКО-ЭКОНОМИЧЕСКИЕ ПОКАЗАТЕЛИ
Целью выполнения курсового работы является разработка технического процесса механической обработки детали с учетом экономических и технологических факторов.
|
|
В курсовой работе описан расчет КЗО, выбор станков при обработке детали исходя из предварительно выбранного типа производства, разработан технологический процесс обработки детали который обеспечивает высокую производительность и малые трудозатраты, также выбран метод получения заготовки с экономическим обоснованием, рассчитаны припуски на механическую обработку обеспечивающий малое снятие материала и высокую точность обработки и в заключение курсовой работы по рассчитанным данным составлена техническая документация.
Графическая часть включает
- Чертеж детали «Колесо зубчатое» – 1 лист А3;
- Чертеж заготовки «Колесо зубчатое» – 1 лист А3;
- Операционные эскизы – 1 лист А1.
Содержание
Задание 2
Реферат 3
1. Введение 5
|
|
2. Определение типа производства 6
3. Выбор метода получения заготовки 12
4. Анализ технологичности конструкции детали 14
5. Разработка маршрутного технологического процесса 16
6. Разработка операций 17
7. Расчет припусков 20
8. Расчет режимов резания 24
9. Технологическое нормирование 27
10. Расчет технико-экономических показателей 29
Заключение 32
|
|
Список литературы 33
ПРИЛОЖЕНИЕ А «Комплект документов на технологический процесс механической обработки зубчатого колеса» 34
1.
Изм.
Лист
№ докум.
Подпись
Дата
Лист
1
КП ТМ 01 00 ПЗ
Разраб.
Машталер В.В.
Провер.
Куис Д.В.
Реценз.
Н. Контр.
Утверд.
Куис Д.В.
Введение
Лит.
Листов
1
ВВЕДЕНИЕ БГТУ 02 08 13 15 09
Основные направления развития машиностроения предусматривают дальнейшее повышение его эффективности, интенсификации, уменьшение сроков создания, освоения производства новой прогрессивной техники. Организационно-методической основой выполнения поставленной задачи является конструирование машиностроительных изделий с учетом требований технологичности конструкции.
|
|
Рассматривая современное состояние проектирования и изготовления изделий с учетом требований технологичности, можно наметить несколько направлений решения этой проблемы, которые непосредственно способствуют повышению технологичности конструкции в соответствии с требованиями современного производства. К ним относят: непрерывно возрастающий объем агрегатного монтажа сборочных единиц, развитие системы модульного проектирования на базе унификации и стандартизации; широкое использование ЭВМ, обеспечивающее более высокий уровень анализа конструктивных решений и различных вариантов использования; организация широкого обмена опытом в области создания технологичных конструкций между различными областями машиностроения. Таким образом, генеральная линия развития машиностроения – комплексная автоматизация проектирования и производства, освоение современных методов проектирования.
Эффективность производства, его технический прогресс, качество выпускаемой продукции во многом зависит от опережающего развития производства; от внедрения технико-экономического анализа, обеспечивающего решение технических вопросов и экономическую эффективность технологических и конструкторских разработок.
Значимость всех этих вопросов при подготовке специалистов, очевидно. В связи с этим в учебном процессе значительное место отводится самостоятельным работам, выполняемыми студентами, в том числе и курсовому проектированию по технологии машиностроения.
Курсовое проектирование закрепляет, углубляет и обобщает знания, полученные во время лекционных и практических занятий. В процессе выполнения курсового проекта приобретаются навыки пользования справочной литературой, ГОСТами, таблицами, номограммами, нормами и расценками, умело сопоставлять справочные данные с теоретическими знаниями, полученными в процессе изучения курса.
При выполнении проекта принятие решений по выбору вариантов технологических процессов, оборудования, оснастки, методов получения заготовок производится на основании технико-экономических расчетов, что дает возможность предложить оптимальный вариант производство данного изделия.
Изм. |
Лист |
№ докум. |
Подпись |
Дата |
Лист |
1 |
КП ТМ 02 00 ПЗ |
Разраб. |
Машталер В.В. |
Провер. |
Куис Д.В. |
Реценз. |
Н. Контр. |
Утверд. |
Куис Д.В.
|
Определение типа производства |
Лит. |
Листов |
6 |
БГТУ 02 08 13 15 09 |
Тип производства по ГОСТ 3.1108 – 74 характеризуется коэффициентом закрепления операций КЗ.О., который показывает отношение всех различных технологических операций О, выполняемых или подлежащих выполнению подразделением в течение месяца, к числу рабочих мест Р. Определяем согласно [1] с. 13 формула 3.4
, (1.1)
В данном проекте необходимо расчленить процесс изготовления детали на различные операции. После чего для каждой операции подсчитать норму времени, а также предвариельно задавшись типом производства в зависемости от массы детали и выпускаемой партии по [1] с.15 таблица 3.3, необходимое число станков . Результаты вычислений занесём в таблицу 1.1.
Масса детали составляет 2.332 кг. подробное описание определение массы заготовки будет представлена в следующем разделе. Масса детали нам необходима для предворительного выбора типа производства и определение коэффициента φк котрый необходим для определения Tшт.-к по [2] с. 147 приложение 1.
Согласно заданию на курсовую работу:
1. годовая программа выпуска деталей – N=24000 штук
2. коэффициент загрузки оборудования –ηз.н.=0.75 согласно [1] с. 15
3. действительный годовой фонд времени – F=4154 ч согласно [1] с. 15
Необходимое число станков на каждую операцию будем рассчитывать согласно [1] с. 15 формула 3.1
, (1.1)
Норму времени для каждой операции определим согласной [2] c.146 приложение 1
, (1.2)
Количество операций выполняемых на рабочем месте определяем согласно [1] с. 13 формула 3.3
, (1.3)
Таблица 1.1. Сводная таблица для расчета типа производства.
Оперция | d, м | l, м | T0, мин | φк | Tшт.-к, мин | mp | P | ηз.ф. | О |
005. Фрезерная | 168 | - | 0.672 | 1.51 | 1.015 | 0.1299 | 1 | 0.1299 | 5.7737 |
010. Зенкерная | 60 | 32 | 0.4032 | 1.51 | 0.609 | 0.078 | 1 | 0.078 | 9.6154 |
015. Развертывание | 60 | 32 | 1.6512 | 1.51 | 2.493 | 0.319 | 1 | 0.319 | 2.3511 |
020. Токарная черновая | 168 | 70 | 1.9992 | 1.5 | 2.9988 | 0.3838 | 1 | 0.3838 | 1.9541 |
025. Токарная черновая | 110 | 38 | 0.7152 | 1.5 | 1.0728 | 0.1373 | 1 | 0.1373 | 5.4925 |
030. Токарная чистовая + снятие фасок | 168 | 70 | 1.9992 | 1.5 | 2.9988 | 0.3838 | 1 | 0.3838 | 1.9541 |
035. Токарная чистовая + снятие фасок | 110 | 35 | 0.6545 | 1.5 | 0.98 | 0.1254 | 1 | 0.1254 | 6 |
040. Зубофрезерная | - | 70 | 0.49 | 1.27 | 0.622 | 0.08 | 1 | 0.08 | 9.375 |
045. Зубодолбёжная | - | 38 | 3.5 | 1.27 | 4.45 | 0.57 | 1 | 0.57 | 1.316 |
050. Шлифовальная | 40 | 70 | 12.88 | 1.55 | 19.96 | 3.929 | 4 | 15.617 | 0.05 |
055. Шлифовальная | 55 | 35 | 8.855 | 1.55 | 13.725 | 1.7568 | 1 | 1.7568 | 0.427 |
060. Зубохонинговальная | 40 | 70 | 1.68 | 1.27 | 2.13 | 0.273 | 1 | 0.273 | 2.75 |
065. Зубохонинговальная | 55 | 35 | 1.155 | 1.27 | 1.4669 | 0.1878 | 1 | 0.1878 | 3.9936 |
070. Шлифовальная | 60 | 30 | 0.27 | 1.55 | 0.42 | 0.054 | 1 | 0.054 | 13.89 |
18 | 63.9425 |
Изм. |
Лист |
№ докум. |
Подпись |
Дата |
Лист |
2 |
КП ТМ 02 00 ПЗ |
Согласно ГОСТ 3.1121-84 такой коэффициент соответствует крупносерийному производству. Исходя из этого определим такт выпуска по формуле 1.4
, (1.4)
Также нам необходимо определить размер партии деталей n по формуле 1.5
, (1.5)
где Ф-количество рабочих дней в году(Ф=257 дней). Принимаем число деталей в партии 654 шт..
Рисунок 1.1. Зубчатое колесо
005. Фрезерная операция (горизонтально- фрезерный станок марки 6Р81Г) То = 0,004∙d = 0.004∙168 = 0.672 мин где То- основное время, мин; d- наибольший диаметр заготовки, мм. | ![]() | ||||||||
То = 0,00021∙d∙l = 0,00021∙60∙32= 0.4032 мин | ![]() | ||||||||
015. Развёртывание (вертикально сверлильный станок марки 2М112) То = 0.00086∙d∙ l=0.00086∙60∙32=1.6512 мин | ![]() | ||||||||
020. Черновое точение (токарно- копировальный многорезцовый полуавтомат 1Н713) То = 0,00017·d·l = 0,00017·168·70 = 1.9992 мин. | ![]() | ||||||||
025. Черновое точение + точение канавки (токарно- копировальный многорезцовый полуавтомат 1Н713). То = 0,00017·d·l = 0,00017·(35·110+119·3)= 0.7152 мин | ![]() | ||||||||
То = 0,00017·d· l = 0,00017·168·70 = 1.9992 мин | ![]() | ||||||||
035. Чистовое точение + снятие фасок (токарно- копировальный многорезцовый полуавтомат 1Н713). То = 0,00017·d· l = 0,00017·110·35 = 0.6545 мин | ![]() | ||||||||
040. Зубофрезерная операция (вертикальный зубофрезерный станок для цилиндрических колес 5В312). То = 0,007·1 = 0,007·70 = 0.49мин. | ![]() | ||||||||
045. Долбление (зубодолбежный полуавтомат марки 5В12) То = 0,1·1 = 0,1·35 = 3.5 мин | ![]() | ||||||||
То = 0.0046·z·1 = 0,0046·40·70 =12.88 мин где l – длина зуба; z – число зубьев | ![]() | ||||||||
055. Зубошлифовальная (плоскошлифовальный станок с круглым столом марки 3Д740В) То = 0.0046·z·1 = 0,0046·55·35 =8.855 мин | ![]() | ||||||||
060. Зубохонинговальная (зубохонинговальный полуавтомат 5В913) То = 0.0006·z·1 = 0,0006·40·70 =1.68 мин | ![]() | ||||||||
065. Зубохонинговальная (зубохонинговальный полуавтомат 5В913) То = 0.0006·z·1 = 0,0006·55·35 =1.155 мин | ![]() | ||||||||
То = 0.00015·d·1 = 0,00015·60·30 =0.27 мин | ![]() |
Изм.
Лист
№ докум.
Подпись
Дата
Лист
1
КП ТМ 03 00 ПЗ
Разраб.
Машталер В.В.
Провер.
Куис Д.В.
Реценз.
Н. Контр.
Утверд.
Куис Д.В.
Выбор метода получения заготовки
Лит.
Листов
2
3. ВЫБОР МЕТОДА ПОЛУЧЕНИЯ ЗАГОТОВКИ БГТУ 02 08 13 15 09
Метод выполнения заготовок для деталей машин определяется назначением и конструкцией детали, материалом, техническими требованиями, масштабом и серийностью выпуска, а также экономичностью изготовления. Выбрать заготовку – значит установить способ ей получения, наметить припуски на обработку каждой поверхности, рассчитать размеры и указать допуски на неточность изготовления.
Для рационального выбора заготовки необходимо одновременно учитывать все вышеперечисленные исходные данные, так как между ними существует тесная взаимосвязь. Окончательное решение можно принять только после экономического комплексного расчёта себестоимости заготовки и механической обработки в целом.
Заготовку для зубчатого колеса наиболее целесообразно получать двумя методами: вытачиванием из цельного проката и штамповкой на ГКМ. Для окончательного определения способа изготовления рассчитаем стоимость заготовки по каждому методу. Стоимость одной тонны сортового проката и стоимость одной тонны заготовок полученных на ГКМ возьмем согласно [2] с 25 раздел «Выбор заготовки».
3.1. Расчет себестоимости заготовки полученной на ГКМ
Найдем массу готовой детали – зубчатого колеса по 3.1.
, (3.1)
где – плотность стали, для стали 15ХГТ
;
Массу заготовки примем равной .
Себестоимость заготовки согласно [1] с.18 формула 3.6 равна
, (3.2)
где – базовая стоимость 1 тонны заготовок:
руб. ;
– масса заготовки, кг;
– коэффициент, зависящий от класса точности заготовки:
;
– коэффициент, зависящий от группы сложности заготовки:
, табл. 2. 12. [2];
– коэффициент, зависящий от массы заготовки:
, табл. 2. 12. [2];
– коэффициент, зависящий от марки материала заготовки:
;
– коэффициент, зависящий от объема производства заготовок:
;
– цена 1 тонны отходов:
руб.;
3.2. Расчет себестоимости заготовки, полученной точением
Себестоимость заготовки будет определятся по формуле, аналогично как и для ГКМ:
, (3.2)
где – базовая стоимость 1 тонны материала:
руб. ;
– масса заготовки, кг;
– коэффициент, зависящий от класса точности заготовки:
;
– коэффициент, зависящий
от группы сложности заготовки: , табл. 2. 10. [2];
– коэффициент, зависящий от
Изм. |
Лист |
№ докум. |
Подпись |
Дата |
Лист |
2 |
КП ТМ 03 00 ПЗ |





– цена 1 тонны отходов:
руб.;
Исходя из расчетов, можно сделать вывод, что заготовка, полученная на ГКМ дороже, чем заготовка, полученная точением. Это объясняется тем, что поковку сложнее получить чем сортовой прокат, но при вытачивании детали из сортового проката идет более больший расход режущего инструмента и увеличивается мощность на силу резания. Также исходя из существующих технологических процессов наиболее целесообразно принять штампованную заготовку.
Определим годовой экономический эффект при использовании заготовок полученных штамповкой согласно [1] с.18
Таким образом, в качестве метода получения заготовки примем штамповку на ГКМ. Заготовка при этом будет иметь следующие параметры:
1. точность размеров заготовки соответствует 13 квалитету по СТ СЭВ144 – 75
2. шероховатость поверхности равна Rz 200.
Изм.
Лист
№ докум.
Подпись
Дата
Лист
1
КП ТМ 04 00 ПЗ
Разраб.
Машталер В.В.
Провер.
Куис Д.В.
Реценз.
Н. Контр.
Утверд.
Куис Д.В.
Анализ технологичности конструкции детали
Лит.
Листов
2
4. АНАЛИЗ ТЕХНОЛОГИЧНОСТИ КОНСТРУКЦИИ ДЕТАЛИ БГТУ 02 08 13 15 09
Отработка конструкции на технологичность – комплекс мероприятий по обеспечению необходимого уровня технологичности конструкции изделия по установленным показателям. Она направлена на повышение производительности труда, снижение затрат и сокращение времени на изготовление изделия при обеспечении необходимого качества. Поэтому технологический анализ – один из важнейших этапов технологической обработки, в том числе и курсового проектирования.
Зубчатые колёса – массовые детали машиностроения, поэтому вопросы технологичности приобретают для них особенно важное значение. При анализе технологичности зубчатых колёс следует определить возможность высокопроизводительных методов формообразования зубчатого венца с применением пластического деформирования в горячем и холодном виде. Конструкция зубчатого колеса должна характеризоваться следующими признаками:
1. простой формой центрального отверстия, так как сложные отверстия значительно усложняют обработку, вызывая необходимость применения револьверных станков и полуавтоматов;
2. простой конфигурацией наружного контура зубчатого колеса;
3. симметричным расположением перемычки между ступицей и венцом для зубчатых колёс, подлежащих термической обработке, как по отношению к венцу, так и по отношению к ступице;
4. правильной формой и размерами канавок для выхода инструментов;
5. возможностью многорезцовой обработки в зависимости от соотношения диаметров венцов и расстояний между ними.
Данная деталь полностью соответствует всем вышеперечисленным условиям и поэтому в качественном смысле является технологичной.
Из чертежа детали видно, что она имеет достаточно простую форму, на ней нет сложных переходов и это позволяет обрабатывать ее на многорезцовых станках. Также в этой детали удачно совмещена конструкторская и технологическая база, что уменьшает количество переходов и повышает точность обработки. Нетехнологичным моментом в этой детали является нарезания зубьев на поверхности Б. Также на чертеже указана поверхностная твердость детали HRC 45÷50 которую можно получить закалкой ТВЧ, цементацией, азотированием либо объемной закалкой без отпуска, что нежелательно так как остаются внутренние напряжения но с другой стороны закалка повышает устойчивость к короблению, что увеличивает срок службы детали.
Количественная оценка технологичности производится в соответствии с ГОСТ 14.202-73. В качестве количественных показателей технологичности в данном случае могут рассматриваться: масса детали, коэффициент использования материала, коэффициент точности обработки, коэффициент шероховатости поверхностей, уровень технологичности конструкции по технологической себестоимости.
![]() | ![]() | ![]() | ![]() | ![]() | ![]() |
8 | 2 | 16 | 1.25 | 2 | 2.5 |
11 | 2 | 22 | 2.0 | 1 | 2 |
7 | 1 | 7 | 3.2 | 3 | 9.6 |
Коэффициент точности:
Изм. |
Лист |
№ докум. |
Подпись |
Дата |
Лист |
2 |
КП ТМ 04 00 ПЗ |

где Шср – средняя шероховатость поверхности.
Коэффициент использования материала:
Исходя из вышеизложенного анализа технологичности детали и полученных необходимых показателей, можно сделать вывод о том, что технологический процесс изготовления данной детали эффективен и рационален, а деталь в свою очередь соответствует предъявляемым к ней технологическим требованиям.
5.
Изм.
Лист
№ докум.
Подпись
Дата
Лист
1
КП ТМ 05 00 ПЗ
Разраб.
Машталер В.В.
Провер.
Куис Д.В.
Реценз.
Н. Контр.
Утверд.
Куис Д.В.
Разработка маршрутного технологического процесса
Лит.
Листов
1
Разработка маршрутного технологического процесса БГТУ 02 08 13 15 09
Изготовление изделий на машиностроительных предприятиях осуществляется в результате производственного процесса, т.е. совокупности всех действий людей и орудий производства, необходимых для превращения сырья и полуфабрикатов в готовое изделие. Важнейшим элементом производственного процесса является технологический процесс, содержащий целенаправленные действия по изготовлению и последующему определению размеров, формы, взаимного расположения, а также состояние предмета труда. Каждый технологический процесс состоит из операций.
Выполним разработку последовательности операций технологического процесса обработки заданной детали – зубчатого колеса. При выборе варианта обработки будем исходить из возможности достижения заданной шероховатости.
Последовательность выполнения операций механической обработки:
005 – фрезерная операция (фрезерование торцов) (Ra 3.2);
010 – Зенкерная операция (внутреннего отверстия) (Ra 3.2);
015 – Развертывание (внутреннего отверстия) (Ra 1.6);
020 – Черновое точение (наружная цилиндрическая поверхность) (Ra 3.2);
025 – Чистовое точение + снятие фасок (наружная цилиндрическая поверхность) (Ra 1.6);
030 – Черновое точение + точение канавки для выхода долбяка (внутренней цилиндрической поверхности) (Ra 3.2);
035 – Чистовое точение + снятие фасок (внутренней цилиндрической поверхности) (Ra 1.6);
040 – Зубофрезерование (нарезание зубьев А цилиндрической фрезой) (Ra 1.6);
045 – Зубодолбление (нарезание зубьев Б при помощи долбяка) (Ra 3.2).
050 – Предварительное шлифование зубьев А
055 – Предварительное шлифование зубьев Б
056 – Объемная закалка без отпуска (получаем необходимую твердость детали)
060 – Шлифование внутреннего отверстия
065 – Зубохонингование зубьев А
070 – Зубохонингование зубьев Б
Изм.
Лист
№ докум.
Подпись
Дата
Лист
1
КП ТМ 06 00 ПЗ
Разраб.
Машталер В.В.
Провер.
Куис Д.В.
Реценз.
Н. Контр.
Утверд.
Куис Д.В.
Разработка операций
Лит.
Листов
3
6. Разработка операций БГТУ 02 08 13 15 09
Выполнение любой технологической операции требует затрат времени работы оборудования и рабочих. Интервал календарного времени от начала до конца периодически повторяющейся технологической операции независимо от числа одновременно изготовляемых или ремонтируемых изделий называют циклом технологической операции.
Штучное время – отношение времени выполнения технологической операции к числу изделий, одновременно изготовляемых на одном рабочем месте.
Основное время (часть штучного времени) – время непосредственного технологического воздействия на предмет труда.
Основное и штучное время для конкретного технологического процесса – механической обработки детали – зубчатое колесо, было определено в первом разделе курсовой работы. В этом разделе будут показаны схемы базирования при обработке.
![]() | ![]() | ||||||||
005 Фрезерование торцов | 010 Зенкерная операция | ||||||||
![]() | ![]() | ||||||||
015 Развертывание | 020 Черновое точение | ||||||||
![]() | ![]() | ||||||||
025 Чистовое точение | 030 Черновое точение | ||||||||
![]() ![]() | ![]() | ||||||||
035 Чистовое точение | 040 Зубофрезерование | ||||||||
![]() | ![]() | ||||||||
045 Зубодолбление | 050 Предварительное шлифование | ||||||||
![]() | ![]() | ||||||||
055 Предварительное шлифование | 060 Шлифование | ||||||||
![]() | ![]() | ||||||||
065 Зубохонингование | 070 Зубохонингование | ||||||||
Изм. |
Лист |
№ докум. |
Подпись |
Дата |
Лист |
1 |
КП ТМ 07 00 ПЗ |
Разраб. |
Машталер В.В. |
Провер. |
Куис Д.В. |
Реценз. |
Н. Контр. |
Утверд. |
Куис Д.В.
|
Расчет припусков |
Лит. |
Листов |
4 |
БГТУ 02 08 13 15 09 |
Припуск – слой металла, который необходимо удалить с поверхности заготовки для получения детали с заданным качеством поверхности. На величину припуска оказывает следующие факторы: материал заготовки, вид заготовки, размер заготовки, величина дефектного слоя на обрабатываемой поверхности, сложность процесса механической обработки, величина погрешности установки.
Для размера определим припуск расчетно-аналитическим методом.
Исходные данные: сталь 15ХГТ, метод получения заготовки – штамповкой на ГКМ , ,
.
По табл. 4.6 и табл. 4.3 с.63-65 [1] определим параметры ,
, достигаемые после механической обработки, и занесем их в табл. 7.1.
Таблица 7. 1. Качество поверхности после механической обработки.
Вид обработки | ![]() | ![]() |
Заготовка (штамповка) | 150 | 200 |
Зенкерование | 50 | 50 |
Развертывание | 5 | 10 |
шлифование | 1 | 7 |
Определим суммарное отклонение расположения поверхностей и формы поверхностей по переходам:
Зенкерование. Базирование производиться в самоцентрирующем патроне по наружному диаметру с прижимом к торцевой поверхности:
, мкм (7.1)
где ρсм – смещение оси отверстия, мкм; принимается равным допуску на толщину стенки поковки, по ГОСТ 26645-85 , ρкор – коробление отливки по длине и по диаметру, мкм
Таким образом, получаем что:
Зенкерование:
Развертывание: .
Погрешность установки при зенкеровании :
где - погрешность закрепления, мкм. Определяется согласно [1] с. 77 табл. 4.11
Погрешность установки при чистовом растачивании:
где - погрешность индексации, мкм. Принимается равной 50мкм
Расчетный припуск определим по формуле:
, мкм (7.2)
где – шероховатость поверхности на предшествующей операции, мкм;
– глубина дефектного поверхностного слоя на предшествующей операции, мкм;
– суммарное отклоне
Изм. |
Лист |
№ докум. |
Подпись |
Дата |
Лист |
2 |
КП ТМ 07 00 ПЗ |
Зенкерование:
Развертывание:
Шлифование:
Определим расчетный максимальный размер:
Шлифование:
Развертывание: .
Зенкерование:
Заготовка:
Допуски выбираем из [3] с. 335 приложение 2 таблиц в зависимости от квалитета точности получаемого размера.
Определим минимальные и максимальные размеры по переходам:
, мм (7.3)
где – допуск, мм. При 7 квалитете
, при зенкеровании при 9 квалитете
, полученная заготовка имеет 14 квалитет с допуском
.
Шлифование:
Развертывание:
Зенкерование:
Заготовка:
Определим предельные припуски
, мм (7.4)
Шлифование:
Развертывание:
Зенкерование:
, мм (7.5)
Шлифование:
Развертывание:
Зенкерование: .
Максимальные размеры по переходам получаем путем округления расчетного максимального размера до порядка допуска.
Полученные результаты занесем в табл. 7.2.
Таблица 7.2. Полученные значения припусков.
Технологические операции и переходы обработки | Элементы припуска, мкм | Расчётный припуск Zmin, мкм | Расчетный размер, мм | Допуск ТА, мкм | Предельный размер, мм | Предельные значения припусков, мм | |||||
Rz | T ( H ) | ρ | ε | min | max | min | max | ||||
Заготовка | 200 | 200 | 470 | - | - | 58.3949 | 104 | 60 | 60.042 | - | - |
Зенкерование | 50 | 50 | 91.9 | 140 | 2×654.5 | 59.7039 | 104 | 59.9689 | 60.0109 | 1.309 | 1.309 |
Развертывание | 5 | 10 | 0.94 | 51 | 2×153.5 | 60.0109 | 42 | 59.5999 | 59.7039 | 0.307 | 0.369 |
Шлифование | 1 | 7 | - | - | 2×15.55 | 60.042 | 42 | 58.2909 | 58.3949 | 0.0311 | 0.0311 |
Итого: | 1.6471 | 1.7091 |
Изм. |
Лист |
№ докум. |
Подпись |
Дата |
Лист |
3 |
КП ТМ 07 00 ПЗ |
, мкм (5.5)
где – суммарный минимальный припуск, мкм;
– допуск на заготовку, мкм;
– допуск на деталь, мкм;
.
.
По полученным результатам строим схему расположения межоперационных припусков и допусков на заданную поверхность – отверстие диаметром 60Н7(рис. 7.1).
Рис. 7.1. Схема графического расположения припусков и допусков на обработку отверстия
Для остальных поверхностей припуски выберем по ГОСТ 26645-85 и занесем их в табл. 5.2.
Изм. |
Лист |
№ докум. |
Подпись |
Дата |
Лист |
4 |
КП ТМ 07 00 ПЗ |
Обозначение размера | Размер по чертежу, мм | Припуск, мм | Пред. отклонения | Размер заготовки | |
Табличный | Расчётный | ||||
1 | 70 | 2×1 | - | - | 72 |
2 | 168 | 2×1.45 | - | - | 170.9 |
3 | 110 | 2×2.0 | - | - | 114 |
Изм.
Лист
№ докум.
Подпись
Дата
Лист
1
КП ТМ 08 00 ПЗ
Разраб.
Машталер В.В.
Провер.
Куис Д.В.
Реценз.
Н. Контр.
Утверд.
Куис Д.В.
Расчет режимов резания
Лит.
Листов
3
8. РАСЧЕТ РЕЖИМОВ РЕЗАНИЯ БГТУ 02 08 13 15 09
Наиболее выгодными режимами резания являются такие, которые обеспечивают наименьшую себестоимость обработки при условии удовлетворения качества продукции и заданной производительности.
Режимы резания могут определяться двумя методами: расчетно-аналитическим и табличным методом.
Последовательность назначения режимов резания следующая:
1. Выбор глубины резания. Всегда надо стремиться удалить весь припуск за один проход, но получить высокую точность и качество поверхности при этом невозможно. Следовательно, надо назначать дополнительные чистовые операции. В таких случаях глубина резания выбирается по таблицам межоперационных припусков.
2. Выбор подачи. Вначале выбирают подачу по таблицам в зависимости от обрабатываемого материала, диаметра детали, глубины резания и материала резца. Следует учитывать, что при чистовом точении величина подачи ограничена требованиями, предъявляемыми к шероховатости и точности размеров детали.
3. Назначение скорости резания. Исходя из выбранной: глубины резания и подачи резания назначают скорость резания, которая в данных условиях работы режущего инструмента обеспечит необходимый период его стойкости. Период стойкости выбирается из таблиц и зависит от числа режущих инструментов в наладке.
Рассмотрим подробно расчет режима резания на примере фрезерной операции 005 обработки торцевых поверхностей. Так как два торца обрабатываются одновременно, то расчет будем вести по любому торцу, так как он имеют одинаковую площадь поверхности.
1. Расчет длины рабочего хода и средней ширины фрезерования
:
(8.1)
где – длина резания, равная длине обработки, измеренной в направлении резания, мм:
;
– длина подвода, врезания и перебега инструмента, мм. Выбирается в зависимости от ширины фрезерования
:
(8.2)
где – площадь фрезеруемой поверхности:
;
.
Диаметр фрезы: . Из [3] выбираем длину подвода, врезания и перебега инструмента:
.
– дополнительная длина хода, вызванная в ряде случаев особенностями наладки и конфигурации детали, мм:
.
.
Определение рекомендуемой подачи на зуб фрезы по нормативам . Обработка ведется торцовой фрезой из твердого сплава ВК6:
.
Определяем стойкость инструмента по нормативам в минутах резания:
(8.3)
Изм. |
Лист |
№ докум. |
Подпись |
Дата |
Лист |
2 |
КП ТМ 08 00 ПЗ |






(8.4)
Таким образом, получаем что стойкость инструмента равна:
Определение рекомендуемой нормативами скорости резания:
(8.5)
где , [3];
– коэффициент, зависящий от размеров обработки. Определяется в зависимости от
следовательно
;
– коэффициент, зависящий от обрабатываемого материала:
;
– коэффициент, зависящий от стойкости и материала инструмента:
;
.
Расчет числа оборотов шпинделя, соответствующего рекомендуемой скорости резания.
(8.6)
Уточнение числа оборотов шпинделя по паспорту станка: .
Уточнение скорости резания по принятому из паспорта станка числу оборотов шпинделя:
(8.7)
.
Расчет минутной подачи по принятому значению числа оборотов шпинделя:
(8.8)
где – число зубьев фрезы:
;
.
Уточняем минутную подачу по паспорту станка: .
Расчет основного времени резания:
(8.9)
Сведем основные характеристики режимов резания для оставшихся операции в таблицы. Расчёт будем вести по формулам, [3].
010 – зенкерная, табл. 8.1
Изм. |
Лист |
№ докум. |
Подпись |
Дата |
Лист |
3 |
КП ТМ 08 00 ПЗ |
№ операции | Наименование операции | t, мм | Lр, мм | S, мм/мин | nр /nп, мин-1 | Vр /Vп, м/мин | T0, мин |
005 | Фрезерная | 2.8 | 227 | 400 | 74.5/125 | 70.2/118 | 0.5675 |
010 | Зенкерная | 1.1 | 36 | - | 106/180 | 9.9/16.96 | 0.23 |
015 | Развертывание | 0.5 | 36 | 200 | 91/180 | 8.6/16.96 | 0.18 |
020 | Токарная | 1.45 | 73 | 80 | 77/250 | 25.14/81.64 | 0.9125 |
025 | Токарная чистовая | 0.3 | 73 | 120 | 105/250 | 34.29/81.64 | 0.61 |
030 | Токарная | 1.5 | 32 | 80 | 77/250 | 13.6/42.39 | 0.4 |
035 | Токарная чистовая | 0.1 | 32 | 120 | 72/250 | 12.21/42.39 | 0.27 |
040 | Зубофрезерная (червячной фрезой D=80 мм) | 4.5 | 121 | 250 | 97/160 | 24.36/40.19 | 0.644 |
045 | Зубодолбежная | 2.5 | 34 | - | - | 16 | 4.2 |
050 | Предварительное шлифование зубьев | 0.01 | 121 | 600 | 342/1200 | 128.8/452.2 | 0.23 |
055 | Предварительное шлифование зубьев | 0.01 | 34 | 400 | 145/1200 | 13.7/113.4 | 1.23 |
060 | Шлифовальная | 0.005 | 36 | 350 | 910/1200 | 85.72/113.1 | 2.09 |
065 | Зубохонингование | - | - | 150 | 750 | - | 0.4 |
070 | Зубохонингование | - | - | 150 | 750 | - | 0.4 |
Изм.
Лист
№ докум.
Подпись
Дата
Лист
1
КП ТМ 09 00 ПЗ
Разраб.
Машталер В.В.
Провер.
Куис Д.В.
Реценз.
Н. Контр.
Утверд.
Куис Д.В.
Технологическое нормирование
Лит.
Листов
2
9. ТЕХНОЛОГИЧЕСКОЕ НОРМИРОВАНИЕ БГТУ 02 08 13 15 09
Технические нормы времени в условиях массового производства устанавливаются расчетно-аналитическим методом.
В массовом производстве определяется норма штучного времени:
(9.1)
где – основное время, мин;
– вспомогательное время, мин;
(9.2)
где – время на установку и снятие детали, мин;
– время на закрепление и открепления детали, мин;
– время на приемы управления, мин;
– время на измерение детали, мин;
– время на обслуживание рабочего места, мин;
(9.3)
где – время на техническое обслуживание рабочего места, мин;
– время на организационное обслуживание рабочего места, мин;
– время перерывов на отдых и личные надобности, мин;
В массовом производстве время на техническое обслуживание станка определяется по следующим формулам:
- для токарных, фрезерных и сверлильных операций:
(9.4)
- для шлифовальных операций:
(9.5)
- для остальных операций:
(9.6)
где – время на смену инструмента и подналадку станка, мин;
– время на одну правку шлифовального круга, мин;
– затраты на техническое обслуживание рабочего места в процентах от основного;
– период стойкости при работе одним инструментом или расчётный период стойкости лимитирующего инструмента при многоинструментальной обработке, мин;
Для всех операций данные о времени сведем в табл. 9.1.
Таблица 9.1.Определение норм штучного времени.
Операция |
|
|
|
мин |
| |||||||||||
![]() | ![]() | ![]() | ![]() | ![]() | ||||||||||||
Фрезерование | 0.672 | 0.5 | 0.18 | 0.21 | 0.07 | 0.03 | 0.09 | 1.752 | ||||||||
Зенкерование | 0.4032 | 0.5 | 0.14 | 0.21 | 0.05 | 0.14 | 0.41 | 1.8532 | ||||||||
Развертывание | 1.6512 | 0.5 | 0.14 | 0.27 | 0.05 | 1.36 | 1.03 | 5.0012 | ||||||||
Черновое точение | 1.9992 | 0.5 | 0.18 | 0.23 | 0.02 | 0.02 | 0.09 | 3.032 | ||||||||
Чистовое точение | 1.9992 | 0.5 | 0.14 | 0.79 | 0.09 | 0.03 | 1.25 | 4.7992 | ||||||||
Черновое точение | 0.7152 | 0.5 | 0.14 | 0.22 | 0.09 | 0.03 | 0.12 | 1.8152 | ||||||||
Чистовое точение | 0.6545 | 0.5 | 0.07 | 0.79 | 0.03 | 0.15 | 1.25 | 3.4445 | ||||||||
Зубофрезерование | 0.49 | 0.5 | 0.22 | 0.33 | 0.09 | 0.45 | 0.47 | 2.55 | ||||||||
| 3.5 | 0.5 | 0.22 | 0.33 | 0.12 | 0.56 | 0.21 | 5.44 | ||||||||
Предворительное шлифованиезубьев А | 12.88 | 0.5 | 0.12 | 0.8 | 0.05 | 0.03 | 3.41 | 17.79 | ||||||||
Предворительное шлифованиезубьев Б | 8.855 | 0.5 | 0.12 | 0.33 | 0.05 | 0.03 | 3.41 | 13.325 | ||||||||
Шлифование | 0.27 | 0.5 | 0.1 | 0.33 | 0.07 | 0.02 | 0.09 | 1.38 | ||||||||
Зубохонингование | 1.68 | 0.5 | 0.62 | 0.33 | 0.09 | 0.03 | 0.09 | 3.34 | ||||||||
Зубохонингование | 1.155 | 0.5 | 0.62 | 0.33 | 0.09 | 0.03 | 0.09 | 2.815 |
Суммарное время:
Среднее штучное время:
Количество деталей в партии для одновременного запуска допускается определять упрощённым способом по формуле:
(9.7)
где a – периодичность запуска в днях; a=3
Корректировка размера партии состоит в определении расчётного числа смен на обработку всей партии деталей на основных рабочих местах:
(9.8)
Определим число деталей в партии, необходимых для загрузки оборудования на основных операциях в течение целого числа смен:
(9.9)
Изм. |
Лист |
№ докум. |
Подпись |
Дата |
Лист |
1 |
КП ТМ 10 00 ПЗ |
Разраб. |
Машталер В.В. |
Провер. |
Куис Д.В. |
Реценз. |
Н. Контр. |
Утверд. |
Куис Д.В.
|
Расчет технико-экономических показателей |
Лит. |
Листов |
3 |
БГТУ 02 08 13 15 09 |
Прежде чем принять решение о методах и последовательности обработки отдельных поверхностей детали и составить технологический маршрут изготовления всей детали, необходимо произвести расчеты экономической эффективности отдельных вариантов и выбрать из них наиболее рациональный для данных условий производства. Критерием оптимальности является минимум приведенных затрат на единицу продукции.
При выборе варианта технологического маршрута приведенные затраты могут быть определены в виде удельных величин на 1 ч. работы оборудования. В качестве себестоимости рассматривается технологическая себестоимость, которая включает изменяющиеся по вариантам статьи затрат.
Рассчитаем технологическую себестоимость операций выбранного технологического маршрута изготовления детали – зубчатого колеса.
В качестве примера рассмотрим токарную многорезцовую черновую операцию.
020 -. токарная черновая операция.
Определяем часовые приведенные затраты:
, (10.1)
где - основная и дополнительная зарплата, коп/ч.
где =1.53 – коэффициент, учитывающий дополнительную зарплату;
=56.6 - часовая тарифная ставка. Принимаем условия работы - нормальные, оплата повременная по 3 разряду;
=0.15 - нормативный коэффициент экономической эффективности капитальных вложений; К=1 - коэффициент учитывающий зарплату наладчика, т.к. принимаем, что наладка производится самим рабочим; у=1 - коэффициент учитывающий оплату рабочего при многостаночном обслуживании. Тогда:
SЧЗ - часовые затраты на рабочем месте, коп/ч, определим по следующей формуле
, (10.2)
где - практические часовые затраты на базовом рабочем месте. Так как производство - крупносерийное, то принимаем
= 36,1 коп/час;
- коэффициент показывающий во сколько раз затраты, связанные с работой данного станка больше чем аналогичные затраты у базового станка. Для выбранного типа станка Км=1.4. Тогда:
Определяем удельные часовые капитальные вложения в станок
, (10.3)
где Ц - цена станка, в руб. принимаем Ц = 6450 руб., [2] с 347; Фоб - действительный годовой фонд времени работы станка, ч.. Принимаем Фоб =3987ч.; ηз=0.3838- коэффициент загрузки станка (см. раздел 1). Тогда:
Определяем удельные часовые капитальные вложения в здание
, (10.4)
где F - площадь станка в плане, м2;
, (10.5)
где f = 3.043 м2 - площадь станка; kf - коэффициент учитывающий дополнительную производственную площадь, kf = 2,45. Тогда площадь необходимая под станок
Изм. |
Лист |
№ докум. |
Подпись |
Дата |
Лист |
2 |
КП ТМ 10 00 ПЗ |
Определяем технологическую себестоимость операции:
, (10.6)
где =1.3 - коэффициент выполнения норм;
= 1.092 мин - штучно-калькуляционное время. Тогда:
Такие же действия проделываем и для других операций. Полученные результаты заносим в таблицу 10.1.
Таблица 10.1. Расчет капитальных вложений.
№ | | | | | | | Ц | | a | b | F | | | | |
005 | 86,598 | 1,1 | 39,71 | 0,15 | 3987 | 0.1299 | 2550 | 492,3623 | 2,12 | 1,4 | 7,27 | 110,05 | 216,67 | 1.015 | 2,82 |
010 | 86,598 | 0,7 | 25,27 | 0,15 | 3987 | 0.078 | 290 | 93,251786 | 0,73 | 0,355 | 0,63 | 15,88 | 128,24 | 0.609 | 1,001 |
015 | 86,598 | 0,7 | 25,27 | 0,15 | 3987 | 0.319 | 290 | 22,801377 | 0,73 | 0,355 | 0,63 | 3,88 | 115,87 | 2.493 | 3,7 |
020 | 86,598 | 1,4 | 50,54 | 0,15 | 3987 | 0.3838 | 6450 | 421,51061 | 2,435 | 1,25 | 7,46 | 38,22 | 206,1 | 2.9988 | 7,92 |
025 | 86,598 | 1,4 | 50,54 | 0,15 | 3987 | 0.1373 | 6450 | 1178,2649 | 2,435 | 1,25 | 7,46 | 106,84 | 329,92 | 1.0728 | 4,54 |
030 | 86,598 | 1,4 | 50,54 | 0,15 | 3987 | 0.3838 | 6450 | 421,51061 | 2,435 | 1,25 | 7,46 | 38,22 | 206,1 | 2.9988 | 7,92 |
035 | 86,598 | 1,4 | 50,54 | 0,15 | 3987 | 0.1254 | 6450 | 1290,07792 | 2,435 | 1,25 | 7,46 | 116,98 | 348,2 | 0.98 | 4,37 |
040 | 86,598 | 2,4 | 86,64 | 0,15 | 3987 | 0.08 | 9400 | 2947,078 | 2,05 | 1,64 | 8,24 | 202,54 | 645,68 | 0.622 | 5,15 |
045 | 86,598 | 1,7 | 61,37 | 0,15 | 3987 | 0.57 | 2610 | 114,846937 | 2,05 | 1,64 | 8,24 | 28,43 | 169,46 | 4.45 | 9,67 |
050 | 86,598 | 2,6 | 93,86 | 0,15 | 3987 | 15.617 | 16840 | 27,0457 | 2,3 | 1,95 | 10,99 | 1,38 | 184,72 | 19.96 | 47,27 |
055 | 86,598 | 2,6 | 93,86 | 0,15 | 3987 | 1.7568 | 16840 | 240,42163 | 2,3 | 1,95 | 10,99 | 12,3 | 218,37 | 13.725 | 38,42 |
060 | 86,598 | 2,5 | 90,25 | 0,15 | 3987 | 0.273 | 11750 | 1079,51575 | 1,79 | 1,425 | 6,25 | 45,02 | 345,53 | 2.13 | 9,44 |
065 | 86,598 | 2,6 | 93,86 | 0,15 | 3987 | 0.1878 | 11750 | 1569,26411 | 2,16 | 1,6 | 8,47 | 88,69 | 429,15 | 1.4669 | 8,07 |
070 | 86,598 | 2,6 | 93,86 | 0,15 | 3987 | 0.054 | 17840 | 8286,18938 | 2,16 | 1,6 | 8,47 | 308,43 | 1731,82 | 0.42 | 9,33 |
Определяем суммарную технологическую себестоимость механической обработки:
Технологическая себестоимость детали определяется по выражению:
, (10.7)
где - цена одной заготовки.
Определяем число рабочих-станочников:
, (10.8)
где F=4154 - годовой фонд времени рабочего, ч.; N = 24000 - годовой объем выпуска, шт.
Определяем число наладчиков из условия, что один наладчик за смену может обслуживать 8-10 станков, поскольку число станков по технологическому процессу принято - 18, то число наладчиков принимаем Н=2.
Определим годовой фонд зарплаты на одну операцию:
, (10.9)
Полученные результаты заносим в табл. 10.1
Определим среднемесячную зарплату рабочих:
, (10.10)
Изм. |
Лист |
№ докум. |
Подпись |
Дата |
Лист |
3 |
КП ТМ 10 00 ПЗ |
Таблица 10.1. Основные технико-экономические показатели разработанного технологического процесса.
Наименование показателя | Величина показателя |
Наименование и номер детали | Колесо зубчатое 4/6 |
Годовой объем выпуска деталей NГ, шт | 24000 |
Эффективный годовой фонд времени работы оборудования FЭ, ч | 3840 |
Эффективный годовой фонд времени рабочего FР, ч | 3840 |
Число смен работы i | 2 |
Масса готовой детали q, кг | 7.271 |
Масса заготовки Q, кг | 9.452 |
Коэффициент использования материала заготовки КU | 0,77 |
Стоимость заготовки SЗАГ, коп | 383.88 |
Себестоимость мех. обработки детали ΣС Oi, коп | 159.621 |
Технологическая себестоимость детали СТ, коп | 543.501 |
Годовой выпуск продукции по технологической себестоимости В, коп. | 13044024 |
Основное время по операциям ΣТ Oi, мин | 36,9245 |
Штучно-калькуляционное время по операциям ΣТШ-К I, мин | 54.9413 |
Трудоемкость годовой программы выпуска деталей ТГ, часов | 21976.52 |
Количество единиц производственного оборудования Σ mПР i, шт. | 18 |
Число рабочих-станочников на две смены, R | 12 |
Число наладчиков на две смены, Н | 4 |
Годовой фонд зарплаты, коп. | 1903122.679 |
Среднемесячная зарплата рабочих, тыс. руб | 237890.3349 |
ЗАКЛЮЧЕНИЕ
В ходе выполнения курсовой работы был разработан технологический процесс изготовления зубчатого колеса, осуществлен анализ технологичности конструкции которая должна удовлетворять требование высокой эффективностью производства и минимальным количеством переместительных операций, выбор метода получения заготовки с экономическим обоснованием в ходе расчетов было определении что при использовании заготовок полученных на ГКМ более целесообразно чем изготовление детали из круглого проката, это объясняется те что при изготовлении детали из круглого поката мы получаем больший выход стружки и более больший расход режущего инструмента. Так же было выполнено назначение припусков на механическую обработку, отметим что на одну поверхность припуски назначались расчетным методом, этот метод обеспечивает малое снятие материала и высокое качество и точность обработки, а на остальные поверхности припуски назначены при помощи таблиц. Входе курсовой работы также были определены технико-экономические показатели они определяют трудозатраты на изготовление одной детали, а также величину капитальных вложений в технологический процесс.
В ходе курсовой работы также были подобраны станки под данный тип производства и технологический процесс, которое обеспечивает не высокие материальные затраты капитальных вложений и высокую производительность.
СПИСОК ИСПОЛЬЗОВАННЫХ ИСТОЧНИКОВ
1. А. Ф. Горбацевич, В. А. Шкред. Курсовое проектирование по технологии машиностроения: – Мн.; Выш. школа, 1983. – 256с., ил.
2. В. Ю. Барановский. Режимы резания металлов. Справочник:– М.; Машиностроение, 1972. – 407с., ил.
3. И.С. Серый. Взаимозаменяемость стандартизация и технические измерения: – Москва ВО «Агропромиздат» 1987 г..
Дата добавления: 2018-11-24; просмотров: 198; Мы поможем в написании вашей работы! |
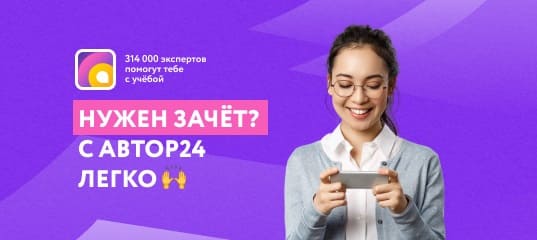
Мы поможем в написании ваших работ!