ПОДГОТОВКА ОПТИЧЕСКИХ ВОЛОКОН К СВАРКЕ
Процесс сварки оптического волокна содержит следующие основные этапы.
Снятие защитного покрытия с концов сращиваемых оптических волокон. Выполняется с помощью стриппера для зачистки оптоволокна, который позволяет быстро и просто удалять защитное покрытие с оптического волокна любого типа с внешним диаметром оболочки от 0,25 до 0,9 мм, а затем зачищенный конец обезжиривается салфеткой смоченной специальной жидкостью или спиртом. Для осуществления успешной сварки необходимо как можно реже допускать контакты с волокном.
Подготовка торцов оптического волокна (скалывание). Скалывание оптического волокна осуществляется прецизионным скалывателем, который скалывает волокно на необходимую длину таким образом, чтобы угол по перпендикулярности торцов соединяемых волокон составлял не более 0,3 градуса. Скалыватель применяется для работы с одномодовым и многомодовым волокном, особенно в случаях, когда предъявляются повышенные требования к сварным соединениям.
Установка оптического волокна в сварочный аппарат и их юстировка. Юстировка оптических волокон осуществляется в автоматическом режиме, хотя метод управления процессом в режиме реального времени позволяет оператору вмешаться в режим сварки с целью получения наилучшего результата.
Сварка оптического волокна электрической дугой между двумя электродами. Режим сварки с выравниванием нагретых сердечников для одномодовых волокон с коррекцией эксцентриситета, обеспечивает стабильную центровку волокон и их последующую сварку.
|
|
Контроль качества сварки оптического волокна. Информация волокон обрабатывается численными методами и отображается на дисплее, что дает оператору возможность следить за процессом сварки. По тепловым изображениям, которые получаются в процессе сварки, вычисляется профиль показателя преломления сердцевины, градиент деформации сердцевины и диаметр модового пятна. Все значения даются по двум осям и используются для оптимизации результата сварки. Такой метод оценки потерь на сварном шве позволяет оценить затухание с высокой точностью.
Защита и укладка сварного соединения оптического волокна. Для механической защиты волокна в месте сварки используют восстановители покрытия или термоусаживаемые гильзы – втулки из термоусаживаемого материала с упрочняющим элементом (металлический стержень или кварцевая оправка) для предотвращения изгиба волокон. Гильза надевается на одно из волокон до сварки, а затем сдвигается на нужное место и нагревается (до 90–150 градусов в течение одной минуты) во встроенной в сварочный аппарат печке для усадки гильз. Затем остывшую гильзу помещают в специальный паз сплайс-пластины оптического кросса или муфты для дополнительной защиты, а волокна укладываются вокруг гильзы.
|
|
Снятие защитного покрытия
Снятие защитного покрытия сращиваемых оптических волокон выполняется с помощью стриппера для зачистки оптического волокна, который позволяет быстро и просто удалять защитное покрытие с оптического волокна любого типа с внешним диаметром оболочки от 0,125 до 0,9 мм.
При зачистке стриппер держат под углом 45° к волокну и снимают защитное покрытие с конца волокна, оставляя при этом оголенное волокно длиной до 4 см.
Механическая зачистка нашла широкое применение при подготовке торцов волокон в полевых условиях. Но при таком методе очистки нельзя исключить возможность повреждения волокон режущими лезвиями.
Вследствие плохой зачистки волокна в зоне сварки могут возникнуть инородные вкрапления, что может ослабить механическую прочность шва, а если оно расположено в области сердцевины, то привести к дополнительным потерям.
Для химической зачистки применяются растворители красок, которые содержат в качестве активного вещества метилен хлорид. После замачивания концов стекловолокон в емкости с растворителем в течение минуты происходит размягчение первичного защитного покрытия, которое при незначительных усилиях снимается с волокна. При заводском способе зачистки в качестве активного вещества с соответствующими предосторожностями применяют горячую серную кислоту.
|
|
Применение химических стрипперов обеспечивает наивысшую прочность сварки до 25 Н.
Применение термо-стрипперов обеспечивает высококачественную зачистку оптического волокна, включая ленточное волокно, от защитного покрытия. В отличие от механических стрипперов не повреждает волокно, что значительно повышает надежность сварного соединения. Возможность регулировки температуры позволяет устанавливать оптимальный режим в зависимости от типа волокна и внешних условий.
После зачистки с волокна необходимо удалить остатки защитного покрытия, что можно сделать с помощью безворсовой салфетки, смоченной спиртом, или ультразвукового очистителя волокна.
Подготовка торцов волокон
Необходимым подготовительным мероприятием для соединения оптических волокон между собой является подготовка торцов волокон (скалывание), применяющееся для получения торцевой поверхности световода с отклонением от перпендикуляра не более 0,5-1° и минимальной шероховатостью. Наличие такой поверхности является необходимым условием для достижения малой величины потерь в сростке неразъемного соединителя.
|
|
Существует три основных метода: метод засечки и обламывания, использование автоматического устройства скола и метод шлифовки и полировки. Методика засечки и обламывания и автоматический скол используются для соединения стеклянных волокон, тогда как шлифовка и полировка применяется для пластиковых волокон и коннекторов.
Метод засечки и обламывания.
На очищенной стеклянной оболочки делается засечка с помощью твердого режущего материала, обычно алмаза, сапфира или лезвия их карбида вольфрама. Волокно удерживается под умеренным давлением пока по нему проходит режущее лезвие, затем давление возрастает и волокно обламывается. К такому методу относят пластину и ручку-скалыватель. Свое название последний получил из-за внешнего сходства с авторучкой. Он снабжается обычным или завинчивающимся колпачком, защищающим резак и имеющим зажим для крепления в кармане. Наиболее распространенные ручки выпускаются в двух модификациях: с ножевидным жалом из твердосплавного металла или керамики и с острием из синтетического корунда [1].
Ручки-скалыватели не позволяют получить высокое качество скола, и потому были разработаны более сложные и точные устройства.
Автоматическое устройство скола.
Скалывание выполняется полуавтоматическим или ручным инструментом. Принцип действия прецизионного скалывателя основан на нанесении на поверхность волокна, предварительно очищенную от защитных оболочек и обезжиренную спиртом, неглубокой насечки с последующим приложением к этой области растягивающего или изгибающего усилия. Под воздействием создаваемой нагрузки происходит рост трещины и образуется ровный перпендикулярный оси световода скол в месте насечки.
Известны электронные, ультразвуковые и механические устройства скола волокна, причем существуют варианты для обработки как одиночного волокна, так и группы волокон ленточного кабеля сразу. На практике получили распространение механические устройства, которые обрабатывают один световод, они реализованы по двум основным кинематическим схемам: с поворотным и продольно-скользящим резаками.
Скалыватели с поворотным резаком имеют две основные конструктивные разновидности.
В первой из них использовано гибкое пластинчатое основание и скрепленная с ним на оси подпружиненная крышка с резаком. Для получения скола волокно, очищенное от защитных покрытий на длину 20...30 мм, укладывают на основание в V-образную направляющую канавку, фиксируют прижимом, опускают крышку, делая при этом насечку на оболочке, после чего изгибают пластинку основания для получения скола.
Во втором варианте скалывателей с поворотным резаком световод фиксируют зажимами в двух точках. Второй зажим выполнен подвижным. После надсекания волокна этот зажим тянут в осевом направлении. Необходимая для нормальной работы прибора ориентация волокна задается трубчатой направляющей.
В конструкциях с продольно-скользящим резаком разделанное волокно сначала укладывают в V-образную канавку с двумя концевыми опорами, фиксируют на этих опорах и в V-образной канавке вспомогательной и основной опускающимися крышками (последняя снабжена магнитным фиксатором), надсекают снизу между опорами дисковидным резаком из твердосплавного материала, закрепленным на подвижных салазках, а потом обламывают верхним подвижным прижимом. Для создания оптимальных условий удержания волокна в рабочем положении использован магнитный фиксатор основной крышки. Скалыватель снабжен также открывающим механизмом, срабатывающим после скола волокна при дальнейшем нажатии на подвижный прижим. В некоторых конструкциях для открывания основной крышки используется дополнительный рычаг.
Дата добавления: 2018-11-24; просмотров: 411; Мы поможем в написании вашей работы! |
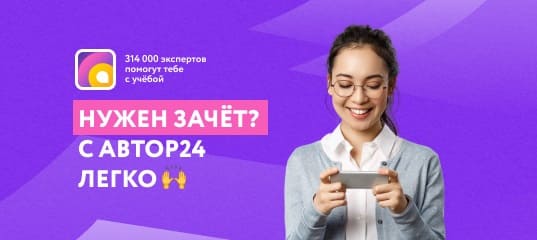
Мы поможем в написании ваших работ!