Воздушная строительная известь (страница 2 из 3)
Показатели качества и свойства
К основным нормируемым показателям качества воздушной извести относят: активность, количество непогасившихся зерен (недожог и пережог) и время гашения.
Активность – процентное содержание оксидов, способных гаситься. Чем выше содержание основных оксидов в извести (CaO+MgO), тем выше её сорт и пластичнее известковое тесто.
В зависимости от содержания MgO в обожженном продукте воздушную известь подразделяют на:
кальциевую: MgO ≤ 5%;
магнезиальную: 5% < MgO ≤ 20%;
доломитовую: 20% < MgO ≤ 40%.
Частицы недожога и пережога снижают качество извести. Частицы недожога (неразложившиеся при обжиге зерна сырья) отощают известковое тесто, снижают его пластичность. Частицы пережога (остеклованные плотные трудногасящиеся оксиды кальция и магния) крайне медленно гидратируются с увеличением своего объема, что может вызвать растрескивание известковой штукатурки. Воздушная известь должна выдерживать испытание на равномерность изменения объема.
По активности, содержанию непогасившихся зерен и другим показателям химического состава воздушная строительная известь делится на 3 сорта (таблица 6.1).
Таблица 6.1
Требования к химическому составу негашеной извести
Наименование показателя | Норма для извести, %, по массе | ||
сорт | |||
1 | 2 | 3 | |
Содержание активных (CaO+MgO), % по массе, не менее | 90 (85) | 80 (75) | 70 (65) |
Содержание непогасившихся зерен, % по массе, не более | 7 (10) | 11 (15) | 14 (20) |
Содержание CO2 в составе извести, % по массе, не более | 3 (5) | 5 (8) | 7 (11) |
Примечание. В скобках указаны характеристики магнезиальной и доломитовой извести.
|
|
Степень дисперсности порошкообразной воздушной извести должна быть такой, чтобы при просеивании пробы извести сквозь сито с сетками № 02 (200 мкм) и №008 (80 мкм) проходило соответственно не менее 98,5 и 85 % массы просеиваемой пробы.
Истинная плотность негашеной извести колеблется в пределах 3100…3300 кг/м3. Насыпная плотность молотой негашеной извести в рыхлонасыпном состоянии 900…1100 кг/м3, в уплотненном – 1100…1300 кг/м3; для гидратной извести в рыхлонасыпном состоянии – 400…500 кг/м3, в уплотненном – 600…700 кг/м3.
Воздушную негашеную известь в зависимости от времени гашения подразделяют на 3 группы (таблица 6.2).
Таблица 6.2
Классификация извести по времени гашения
Группа извести | Время гашения извести |
Быстрогасящаяся | не более 8 мин. |
Среднегасящаяся | не более 25 мин. |
Медленногасящаяся | более 25 мин. |
Влажность гидратной извести не должна быть более 5%. Содержание гидратной воды в негашеной извести не должно быть более 2%.
Ценнейшее свойство воздушной извести – высокая пластичность и водоудерживающая способностьизвесткового теста, обусловленные огромной удельной поверхностью частиц.
|
|
Прочность известковых растворов невысока: предел прочности при сжатии в возрасте 28 суток воздушного твердения составляет 0,4…1,0 МПа у растворов на гашеной извести и до 5,0 МПа у растворов на молотой негашеной извести. Поэтому в отличие от других вяжущих известь не делится на марки по прочности; прочность воздушной извести не нормируется. При длительном твердении (годы и десятки лет) прочность известковых растворов может увеличиваться до 7…10 МПа вследствие дальнейшей карбонизации и образования гидросиликатов кальция.
В строительстве известь из-за большой усадки при твердении и возможного растрескивания применяют только в виде растворов и бетонов, т.е. в смеси с заполнителями.
Воздушная строительная известь (страница 3 из 3)
Применение
Воздушная строительная известь используется при производстве силикатного кирпича и камней, силикатобетонных блоков, плит, панелей автоклавного твердения, изделий из автоклавных ячеистых бетонов, как составная часть смешанных вяжущих (известково-шлаковые, известково-пуццолановые и др.), при производстве сухих строительных смесей, для изготовления известковых красок.
|
|
Гипсовые вяжущие вещества (страница 1 из 3)
Общие сведения
Гипсовые вяжущие вещества – это воздушные вяжущие вещества, состоящие в основном из полуводного гипса CaSO4·0,5H2O или ангидрита CaSO4.
Сырьем для производства гипсовых вяжущих служат мономинеральная горная порода гипс, состоящая из двуводного сульфата кальция СаSO4·2H2O, и природный ангидрит СаSO4, а также отходы химической промышленности, содержащие двуводный или безводный сернокислый кальций, например, фосфогипс (отход при производстве фосфорной кислоты).
Производство гипсовых вяжущих состоит в измельчении и последующей тепловой обработке сырья. В зависимости от температуры обжига, гипсовые вяжущие подразделяются на 2 группы:
Низкообжиговые (температура обжига 110…180°С), составляют более 95% объема производства гипсовых вяжущих веществ;
Высокообжиговые (температура обжига 600…1000°С).
Низкообжиговые гипсовые вяжущие состоят преимущественно из полуводного гипса CaSO4·0,5H2O. Дегидратация сырья в процессе термической обработки происходит по реакции:
CaSO4·2H2O → CaSO4·0,5H2O + 1,5Н2О↑.
Существуют две технологии получения низкообжиговых гипсовых вяжущих:
|
|
Обжиг сырья в открытых агрегатах – варочных котлах или печах, когда вода в процессе обжига удаляется в виде пара. По такой технологии получают строительный гипс, который состоит в основном из мелких кристаллов β-CaSO4·0,5H2O и обладает высокой водопотребностью. В строительном гипсе может содержаться небольшое количество ангидрита CaSO4 (пережог) и частицы неразложившегося сырья CaSO4·2H2O (недожог). Прочность при сжатии образцов из строительного гипса достигает 10…12 МПа.
Обжиг сырья в герметически закрытых аппаратах в среде насыщенного пара под давлением. В этом случае вода из гипсовой породы удаляется в капельно-жидком состоянии, а получаемый продукт обжига состоит из крупных плотных кристаллов в виде игл или призм. Эта модификация гипса α-CaSO4·0,5H2O называется высокопрочным гипсом. Он отличается от β-модификации меньшей водопотребностью, а, следовательно, изделия из такого гипса имеют пониженную пористость и высокую прочность (15-25 МПа).
Высокообжиговые гипсовые вяжущие (ангидритовые вяжущие) состоят преимущественно из ангидрита СаSО4 и 3…5% СаО, образующегося при разложении СаSО4 и выполняющего роль активизатора твердения СаSО4. Ангидритовое вяжущее получают обжигом СаSО4·2Н2О при температуре 600…1000°С, либо помолом природного ангидрита СаSО4 с добавками–активизаторами твердения (известью, обожженным доломитом и др.). Высокообжиговый гипс имеет прочность 10…20 МПа, по сравнению с низкообжиговыми гипсовыми вяжущими медленно схватывается и твердеет, но обладает повышенной водостойкостью.
Твердениеα- и β-модификаций гипса обусловлено переходом их при взаимодействии с водой в двугидрат по реакции:
CaSO4·0,5H2O + 1,5Н2О → CaSO4·2H2O + Q.
Процесс твердения гипса впервые описал французский ученый А. Ле-Шателье (H . Le Chatelier) в 1887 г. При смешивании с водой полуводный гипс растворяется до образования насыщенного раствора, в котором он гидратируется с образованием двугидрата. Поскольку растворимость в воде двугидрата в 4 раза меньше, чем полугидрата (2 г/л против 8 г/л), раствор оказывается пересыщенным по отношению к двугидрату, и он в виде кристаллов CaSO4·2H2O выделяется из раствора. По мере накопления двугидрата происходит схватывание (загустевание) гипсового теста. После схватывания начинается твердение, обусловленное ростом кристаллов, их срастанием, образованием кристаллического сростка из достаточно крупных кристаллов двуводного гипса. Твердение гипса сопровождается выделением теплоты – 133 кДж/кг для β-модификации.
Дата добавления: 2018-11-24; просмотров: 834; Мы поможем в написании вашей работы! |
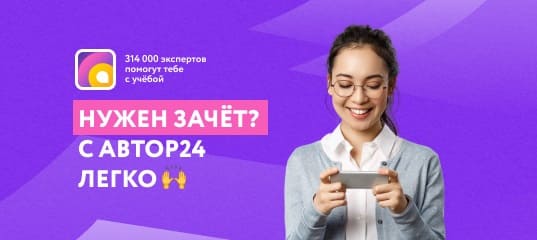
Мы поможем в написании ваших работ!