В.3 Инструментальное обследование и мониторинг трубопроводных систем и нагнетательных машин при пуске и эксплуатации
В.3.1 Инструментальные обследования вибрации
В.3.1.1 Целями обследования являются:
- измерение уровней вибрации трубопроводов, сравнение их с допускаемыми (см. В.4.2);
- определение степени опасности вибрации;
- анализ спектров вибрации, диагностика частотных спектров вибровозмущений и их интенсивности;
- оценка уровней вибрации элементов нагнетательных машин (таблицы В.3-В.9) как источников вибрации;
- измерение уровней пульсации давления, сравнение их с допускаемыми, определение необходимости их снижения;
- определение необходимости виброзащиты окружающих объектов;
- составление заключения о необходимости периодического или постоянного мониторинга вибрации трубопроводов и нагнетательных машин.
В.3.1.2 Измерения вибрации выполняют в следующем порядке:
Измерение в каждом намеченном сечении проводят по трем осям. Принимают следующие направления осей:
- Y - по оси вала машины;
- X - в горизонтальной плоскости;
- Z - нормально к плоскости XY.
Направление Y выдерживают по всей трассе для каждого участка.
Точки измерения:
- нагнетательная машина - торцы цилиндров, нагнетательные патрубки, фундаментные болты;
- опоры трубопровода;
- середина каждого пролета между опорами, при наличии в пролете между опорами отводов - на концах отвода.
Определяют частотный спектр вибрации. Измеряют размахи виброперемещений:
|
|
- общий (суммарный) уровень;
- для каждой частотной составляющей спектра.
Во время измерений фиксируют режим нагружения трубопровода:
- состав перекачиваемой среды;
- температура на каждом участке;
- давление;
- производительность;
- время и дата проведения измерений.
При меняющихся режимах эксплуатации требуются измерения на 3-4 режимах производительности. Результаты измерений протоколируются с указанием исполнителей.
В.3.2 Мониторинг системы
В.3.2.1 Вид мониторинга (периодический или постоянный) вибрации трубопроводных систем определяется проектной документацией или назначается по результатам инструментальных обследований.
При периодическом мониторинге выполняются все требования В.3.1. Периодичность измерений вибрации при опорных уровнях не выше 2 (согласно В.4.2) назначают не реже одного раза в месяц; при значениях вибрации, приближающихся к 3-му уровню - не реже одного раза в неделю. При стабилизации вибрации около 3-го уровня в течение 4 измерений (1 месяц) допустимо увеличить периодичность до одного месяца.
При возрастании уровня с 3-го до 4-го необходим ежедневный мониторинг, а при достижении средних значений размаха вибрации в полосе 3-го-4-го уровней требуется срочная остановка и реконструкция системы.
|
|
В.3.2.2 При стационарном мониторинге предусматривается:
- на нагнетательных машинах - не менее одной точки фиксации (по X, Y, Z);
- на трубопроводных системах - не менее чем в трех точках по трассе.
Допускается фиксация уровней вибрации для каждой точки по одному или двум наиболее виброопасным направлениям.
По максимальным уровням вибрации из всех намеченных точек по трассе и координатам выбирают не менее двух для включения сигнализации достижения аварийного уровня.
В.4 Нормирование пульсации потока и вибрации трубопроводов
В.4.1 Пульсация потока продукта
Неравномерность потока ограничивают в зависимости от рабочего давления (таблица В.1).
Таблица В.1 - Ограничения неравномерности пульсации потока
![]() | <0,5 | Св. 0,5 до 1,0 | Св. 1,0 до 2,0 | Св. 2,0 до 5,0 | Св. 5,0 |
![]() | 4-8 | От 4 до 6 | От 3 до 5 | От 2 до 4 | От 2 до 3 |
Для всасывающих линий нефтяного газа допускается большее значение пульсации давления.
|
|
В.4.2 Вибрации трубопроводов
Их нормируют по амплитуде виброперемещений в зависимости от частоты вибрации.
Различают четыре опорных уровня вибрации:
- расчетный при проектировании;
- допускаемый при эксплуатации;
- требующий исправления, реконструкции системы;
- уровень появления аварийных ситуаций.
В таблице В.2 даны дискретные значения допускаемых значений вибрации трубопроводов для фиксированных частот.
Таблица В.2 - Допускаемые значения амплитуд вибрации трубопроводов , мкм
Уровень | Частота, Гц | |||||||||
2 | 4 | 6 | 8 | 10 | 20 | 30 | 40 | 50 | 60 | |
1 | 120 | 115 | 100 | 90 | 85 | 60 | 50 | 45 | 40 | 35 |
2 | 250 | 230 | 200 | 180 | 165 | 120 | 95 | 85 | 75 | 70 |
3 | 500 | 450 | 400 | 360 | 330 | 230 | 180 | 145 | 135 | 130 |
4 | 1250 | 1100 | 950 | 800 | 750 | 500 | 420 | 350 | 320 | 300 |
Соответственно в диапазонах уровня:
1-2 - удовлетворительное состояние трубопроводов;
2-3 - допускаемое значение, контроль;
3-4 - повышенный контроль, возможны отказы, необходимы исправление, реконструкция;
выше 4 - экстренное исправление.
Практически для большинства трубопроводных обвязок насосов и компрессоров главные амплитудные составляющие процессов вибрации определены с диапазоном частот до 60 Гц.
|
|
При мониторинге вибросостояния трубопроводов в условиях эксплуатации с целью оценки и выявления причин повышенных уровней вибрации необходимо иметь, кроме уровней пульсации давления, информацию об уровнях вибрации компрессоров, насосов, фундаментов и т.п.
Оценку вибрационного состояния насосов и компрессоров, за исключением поршневых машин с номинальной скоростью от 120 до 15000 мин , проводят по средним квадратичным значениям виброскорости, мм/с, и виброперемещений, мкм, в соответствии с [22]. В остальных случаях, не предусмотренных в указанных стандартах, для оценки вибрации используют приводимые далее (таблицы В.3-В.10) допустимые амплитуды вибрации узлов и элементов нагнетательных машин.
Таблица В.3 - Насосы
Частота вращения вала, Гц | <12,5 | 12,5-16,5 | 16,5-25 | 25-50 | >50 |
Допустимая амплитуда вибрации ![]() | 120 | 100 | 80 | 60 | 50 |
Таблица В.4 - Фундаменты поршневых машин
Частота колебаний, Гц | <3,5 | 3,5-8 | 8-25 | 25-50 |
Допустимая амплитуда вибрации ![]() | 400 | 200 | 100 | 50 |
Таблица В.5 - Фундаменты электродвигателей
Частота колебаний, Гц | <8 | 8-12,5 | >12,5 |
Допустимая амплитуда вибрации ![]() | 200 | 150 | 100 |
Таблица В.6 - Фундаменты турбоагрегатов
Частота колебаний, Гц | <25 | 25-50 | >50 |
Допустимая амплитуда вибрации ![]() | 100 | 70 | 40 |
Таблица В.7 - Цилиндры и межступенчатые аппараты поршневых машин
Частота колебаний, Гц | <10 | >10 |
Допустимая амплитуда вибрации ![]() | 250 | 200 |
Таблица В.8 - Подшипники турбоагрегатов
Частота колебаний, Гц | 25-50 | 50-80 | 80-135 | >135 |
Допустимая амплитуда вибрации ![]() | 95 | 20 | 13 | 1,5 |
Таблица В.9 - Подшипники электродвигателей
Частота колебаний, Гц | <12,5 | 12,5-16,5 | 16,5-25 | 25-50 |
Допустимая амплитуда вибрации ![]() | 80 | 65 | 50 | 25 |
Таблица В.10 - Рабочее место машиниста
Частота колебаний, Гц | <3 | 3-5 | 5-8 | 8-15 | 15-30 | >30 |
Допустимая амплитуда вибрации ![]() | 300 | 200 | 75 | 25 | 15 | 5 |
Приложение Г
(обязательное)
Таблица Г.1 - Пределы применения, виды обязательных испытаний и контроля стали для фланцев, линз, прокладок и крепежных деталей для давления свыше 10 МПа (100 кгс/см )
Марка стали, стандарт или ТУ | Технические требования | Наименование детали | Предельные параметры | Обязательные испытания | Контроль | |||||||
Температура стенки, °С, не более | Давление номинальное, МПа (кгс/см ![]() | ![]() | ![]() | ![]() | f | KCU | HB | Дефек- тоско- пия | Неме- талли- ческие вклю- чения | |||
20 ГОСТ 1050 | ГОСТ 10493 | Линзы | От -40 до +200 | 32 (320) | + | + | + | - | + | + | + | + |
08, 10 ГОСТ 1050 | ОСТ 26-01-49-82 | Прокладки металлические | От -40 до +250 | 32 (320) | + | + | + | - | + | + | + | + |
35, 40, 45 ГОСТ 1050 | ГОСТ 9399 | Фланцы | От -40 до +200 | 32 (320) | + | + | + | + | + | + | + | - |
30Х ГОСТ 4543 | ГОСТ 9399; ГОСТ 10495 | Фланцы, гайки | От -50 до +200 | 63 (630) | + | + | + | + | + | + | + | - |
35Х, 38ХА, 40Х ГОСТ 4543 | ГОСТ 9399 | Фланцы | От -50 до +400 | 80 (800) | + | + | + | + | + | + | + | - |
ГОСТ 10494 | Шпильки | От -50 до +200 | 63 (630) | + | + | + | + | + | + | + | - | |
ГОСТ 10495 | Гайки | От -50 до +400 | 80 (800) | + | + | + | - | + | + | - | - | |
40ХФА ГОСТ 4543 | ГОСТ 10494 | Шпильки | + | + | + | + | + | + | + | - | ||
14ХГС ГОСТ 19281 | ГОСТ 10493 | Линзы | От -50 до +200 | 63 (630) | + | + | + | - | + | + | + | + |
15ХМ ГОСТ 4543 | От -50 до +400 | 40 (400) | + | + | + | - | + | + | + | + | ||
15ХМ ГОСТ 4543 | ОСТ 26-01-49-82 | Прокладки | От -40 до +350 | 32 (320) | + | + | + | - | + | + | + | + |
30ХМА ГОСТ 4543 | ГОСТ 10494 | Шпильки | От -50 до +400 | 80 (800) | + | + | + | + | + | + | + | - |
ГОСТ 10495 | Гайки | От -50 до +510 | 100 (1000) | + | + | + | - | + | + | - | - | |
ГОСТ 9399 | Фланцы | От -50 до +400 | 80 (800) | + | + | + | + | + | + | + | - | |
ГОСТ 10493 | Линзы | + | + | + | - | + | + | + | + | |||
35ХМ ГОСТ 4543 | ГОСТ 10494 | Шпильки | От -50 до +400 | 80 (800) | + | + | + | + | + | + | + | - |
ГОСТ 10495 | Гайки | От -50 до +510 | 100 (1000) | + | + | + | - | + | + | - | - | |
ГОСТ 9399 | Фланцы | От -50 до +400 | 80 (800) | + | + | + | + | + | + | + | - | |
25Х1МФ ГОСТ 20072 | ГОСТ 10494 | Шпильки | От -50 до +510 | 100 (1000) | + | + | + | + | + | + | + | - |
ГОСТ 10495 | Гайки | От -50 до +510 | + | + | + | - | + | + | - | - | ||
ГОСТ 9399 | Фланцы | От -50 до +510 | + | + | + | + | + | + | + | - | ||
25Х2М1Ф ГОСТ 20072 | ГОСТ 10494 | Шпильки | От -50 до +510 | + | + | + | + | + | + | + | + | |
ГОСТ 9399 | Фланцы | От -50 до +510 | + | + | + | + | + | + | + | + | ||
18Х3МВ ГОСТ 20072 | ГОСТ 10493 | Линзы | От -50 до +510 | + | + | + | - | + | + | + | + | |
20Х3МВФ ГОСТ 20072 | ГОСТ 9399 | Фланцы | От -50 до +510 | + | + | + | + | + | + | + | - | |
20Х3МВФ ГОСТ 20072 | ГОСТ 10493 | Линзы | От -50 до +510 | + | + | + | - | + | + | + | + | |
12Х18Н10Т ГОСТ 5632 | ГОСТ 10493 | Линзы | От -50 до +400 | 40 (400) | + | + | + | - | + | + | + | + |
ОСТ 26-01-49-82 | Прокладки металлические | От -40 до +350 | 32 (320) | + | + | + | - | + | + | + | + | |
10Х17Н13М3Т, 08Х17Н15М3Т ГОСТ 5632 | ГОСТ 10493 | Линзы | От -50 до +400 | 40 (400) | + | + | + | - | + | + | + | + |
ОСТ 26-01-49-82 | Прокладки металлические | От -40 до +350 | 32 (320) | + | + | + | - | + | + | + | + | |
ХН35ВТ ГОСТ 5632 | ГОСТ 10494 | Шпильки | От -50 до +650 | 40 (400) | + | + | + | + | + | + | + | - |
ГОСТ 10495 | Гайки | От -50 до +600 | + | + | + | - | - | + | - | - | ||
ХН35ВТ ГОСТ 5632 | ГОСТ 9399 | Фланцы | От -50 до +540 | + | + | + | + | + | + | + | - | |
45Х14Н14В2М ГОСТ 5632 | ГОСТ 10494 | Шпильки | От -70 до +600 | + | + | + | + | + | + | + | - | |
ГОСТ 10495 | Гайки | + | + | + | - | - | + | - | - | |||
ГОСТ 9399 | Фланцы | От -50 до +540 | + | + | + | + | + | + | + | - | ||
08Х15Н24В4ТР ГОСТ 5632 | ГОСТ 10494 | Шпильки | От -270 до +600 | + | + | + | + | + | + | + | - | |
ГОСТ 10495 | Гайки | От -270 до +600 | + | + | + | - | - | + | - | - | ||
ГОСТ 9399 | Фланцы | + | + | + | + | + | + | + | - | |||
31Х19Н9МВБТ ГОСТ 5632 | ГОСТ 10494 | Шпильки | От -50 до +625 | + | + | + | + | + | + | + | - | |
31Х19Н9МВБТГОСТ 5632 | ГОСТ 10495 | Гайки | От -50 до +600 | + | + | + | - | - | + | - | - | |
ГОСТ 9399 | Фланцы | От -50 до +540 | + | + | + | + | + | + | + | - |
Таблица Г.2 - Поковки для давления свыше 10 МПа (100 кгс/см )
Марка стали, стандарт или ТУ | Технические требования | Предельные параметры | Обязательные испытания | Контроль | |||||||||
Температура стенки, °С, не более | Давление номинальное, МПа (кгс/см ![]() | ![]() | ![]() | ![]() | f | KCU | HB | Макро- струк- тура | Дефек- тоско- пия | Неме- талли- ческие вклю- чения | МКК | ||
20 ГОСТ 1050 | ГОСТ 22790; СТО 00220227-006-2010 | От -40 до +450 | 32 (320) | + | + | + | + | + | + | + | + | - | + |
20ЮЧ ТУ 26-0303-1532-84 | ГОСТ 22790 | + | + | + | + | + | + | + | + | - | + | ||
10Г2 ГОСТ 4543 | От -50 до +450 | 50 (500) | + | + | + | + | + | + | + | + | - | + | |
15ГС ОСТ 108.030.113-87 | ГОСТ 22790; СТО 00220227-006-2010 | От -40 до +400 | 63 (630) | + | + | + | + | + | + | + | + | - | + |
16ГС ГОСТ 19281 | ГОСТ 8479, группа IV; СТО 00220227-006-2010 | От -40 до +450 | + | + | + | + | + | + | + | + | - | + | |
09Г2С ГОСТ 19281 | ГОСТ 22790; СТО 00220227-006-2010 | От -50 до +400 | + | + | + | + | + | + | + | + | - | + | |
14ХГС ГОСТ 19281 | От -50 до +400 | + | + | + | + | + | + | + | + | - | + | ||
30ХМА ГОСТ 4543 | От -50 до +475 | 80 (800) | + | + | + | + | + | + | + | + | - | + | |
15ХМ ГОСТ 4543 | ГОСТ 8479, группа IV | От -40 до +560 | 40 (400) | + | + | + | + | + | + | + | + | - | + |
12Х1МФ ОСТ 108.030.113-87 | ОСТ 108.030.113-87 | От -20 до +560 | 63 (630) | + | + | + | + | + | + | + | + | - | + |
15Х1М1Ф ОСТ 108.030.113-87 | От -20 до +510 | 80 (800) | + | + | + | + | + | + | + | + | - | + | |
20Х2МА, 22Х3М СТО 00220227-006-2010 | ГОСТ 22790; СТО 00220227-006-2010 | От -40 до +475 | + | + | + | + | + | + | + | + | - | + | |
18Х3МФ ГОСТ 20072 | От -50 до +475 | + | + | + | + | + | + | + | + | - | + | ||
20Х3МВФ ГОСТ 20072 | От -50 до +510 | 100 (1000) | + | + | + | + | + | + | + | + | - | + | |
15Х5М ГОСТ 20072 | От -40 до +540 | 40 (400) | + | + | + | + | + | + | + | + | - | + | |
03Х17Н14М3, 10Х17Н13М2Т, 10Х17Н15М3Т, 08Х17Н15М3Т, 08Х18Н10Т, 08Х18Н12Т ГОСТ 5632 | От -50 до +510 | + | + | + | - | - | - | + | + | + | + | ||
12Х18Н10Т, 12Х18Н12Т ГОСТ 5632 | ГОСТ 22790; СТО 00220227-006-2010 | От -50 до +510 | 40 (400) | + | + | + | - | - | - | + | + | + | + |
Примечания
1 Нормируемые показатели и объем контроля должны соответствовать указанным в нормативно-технической документации.
2 Контроль механических свойств при испытаниях на растяжение и ударный изгиб производится в соответствии с нормативной документацией. Испытания на ударный изгиб на образцах с концентратором типа V (KCV) проводятся по требованию. 3 Испытанию на склонность к МКК должны подвергаться поковки из коррозионно-стойких сталей при наличии требований в технической документации. |
Таблица Г.3 - Объемы входного контроля металла сборочных единиц и элементов трубопроводов для давления свыше 10 МПа (100 кгс/см )
Материалы и элементы | Вид контроля | Объем контроля |
Трубы | Анализ сертификатных данных | |
Осмотр наружной и внутренней поверхностей | 100% | |
Проверка маркировки | ||
Контроль наружного диаметра и толщины стенки | ||
Магнитная дефектоскопия по наружной поверхности | 100% труб с наружным диаметром менее 14 мм | |
Проверка стилоскопом наличия хрома, вольфрама, никеля, молибдена, ванадия, титана в металле труб из легированных марок стали | 100% | |
Контроль твердости по Бринеллю с обоих концов трубы | 100% труб с толщиной стенки 5 мм и более | |
Испытание на растяжение | 2 трубы от партии | |
Испытание на ударный изгиб | 2 трубы от партии с толщиной стенки более 12 мм | |
Контроль загрязненности неметаллическими включениями (при отсутствии документа на данный вид контроля) | 2 трубы от партии | |
Испытание на раздачу (по требованию проекта) | ||
Испытание на сплющивание (по требованию проекта) | 2 трубы от партии с наружным диаметром 45 мм и более | |
Испытание на изгиб (по требованию проекта) | 2 трубы от партии с наружным диаметром менее 45 мм | |
Испытание на межкристаллитную коррозию (по требованию проекта) | 2 трубы от партии | |
Поковки | Анализ сертификатных данных | |
Внешний осмотр | 100% | |
Проверка маркировки | ||
Проверка размеров | ||
Магнитопорошковый или капиллярный (цветной) контроль | Выборочно, в местах, где внешним осмотром трудно определить дефекты, а также в местах исправления поверхностных дефектов | |
Ультразвуковой контроль | Каждая поковка деталей D 32 мм и более | |
Проверка стилоскопом наличия хрома, вольфрама, молибдена, никеля, ванадия, титана в металле поковок из легированных марок стали | 100% | |
Контроль твердости по Бринеллю | ||
Испытание на растяжение | 2 поковки от партии | |
Испытание на ударный изгиб | ||
Контроль загрязненности неметаллическими включениями (при отсутствии документа на данный вид контроля) | Каждая поковка деталей DN<250 мм | |
Испытание на стойкость к МКК (по требованию проекта) | 2 поковки от партии | |
Электроды | Проверка наличия сертификатов | |
Проверка наличия ярлыков на упаковке и соответствия их данных сертификатам | 100% | |
Проверка соответствия качества электродов требованиям ГОСТ 9466 | По одному электроду из 5 пачек от партии | |
Проверка сварочно-технологических свойств электродов сваркой тавровых соединений ГОСТ 9466 | 1 пачка из партии | |
Проверка ГОСТ 9466 химического состава и (при наличии требований) содержания ферритной фазы и стойкости к МКК | ||
Сварочная проволока | Проверка наличия сертификатов и соответствия их данных требованиям ГОСТ 2246 или ТУ | 100% |
Проверка наличия бирок на мотках и соответствия их данных сертификатам | 100% | |
Проверка соответствия поверхности проволоки требованиям ГОСТ 2246 или ТУ | 100% мотков | |
Проверка стилоскопом химического состава проволоки | 1 моток от каждой партии | |
Сварочный флюс | Проверка наличия сертификата и соответствия его данных требованиям ГОСТ 9087 или ТУ | 100% |
Проверка наличия ярлыков на таре и соответствия их данных сертификату | ||
Защитный газ | Проверка наличия сертификата | |
Проверка наличия ярлыков на баллонах и соответствия их данных сертификату | 100% | |
Проверка чистоты газа на соответствие сертификату | 1 баллон от партии | |
Фасонные детали (тройники, переходы, угольники и т.п.) | Анализ паспортных данных | |
Проверка соответствия маркировки техническим условиям на поставку | Каждая деталь | |
Проверка визуальным осмотром наружных и внутренних поверхностей на отсутствие коррозии, трещин, раковин, забоин, повреждений от транспортировки и разгрузки | ||
Проверка качества обработки уплотнительных мест и кромок под сварку | Каждая деталь | |
Магнитопорошковый или капиллярный (цветной) контроль | Выборочно, в тех местах, где внешним осмотром трудно определить дефекты, а также в местах исправления поверхностных дефектов | |
Проверка качества резьбы на присоединенных концах и в гнездах под упорные шпильки (внешним осмотром, резьбовыми калибрами, прокручиванием резьбовых фланцев, шпилек) | Каждая деталь | |
Проверка габаритных и присоединительных размеров | ||
Проверка стилоскопом наличия хрома, никеля, молибдена, вольфрама, ванадия, титана | Каждая деталь из легированной марки стали | |
Металлические уплотнительные прокладки | Анализ паспортных данных | |
Проверка соответствия маркировки ТУ на поставку | Каждая прокладка | |
Визуальный осмотр уплотнительной поверхности | ||
Магнитопорошковый или капиллярный (цветной) контроль | В сомнительных случаях | |
Проверка геометрических размеров | 2 прокладки от партии | |
Колена и отводы гнутые | Анализ паспортных данных | |
Проверка соответствия маркировки ТУ на поставку | Каждая деталь | |
Проверка визуальным осмотром наружных и внутренних поверхностей на отсутствие коррозии, трещин, раковин, забоин и повреждений от транспортировки и разгрузки | ||
Измерение ультразвуковым методом толщины стенки в месте гиба | ||
Измерение овальности | ||
Ультразвуковой контроль сплошности металла в месте гиба (при отсутствии документа на данный вид контроля) | ||
Магнитопорошковый или капиллярный (цветной) контроль | Выборочно, в местах исправления поверхностных дефектов | |
Проверка качества обработки уплотнительных мест и кромок под сварку | Каждая деталь | |
Проверка качества резьбы на присоединительных концах резьбовыми калибрами или прокручиванием резьбовых фланцев | ||
Проверка габаритных и присоединительных размеров | ||
Проверка стилоскопом наличия хрома, никеля, молибдена, вольфрама, ванадия, титана | Каждая деталь из легированной марки стали | |
Шпильки, гайки | Анализ паспортных данных | |
Проверка типа шпилек | Каждая шпилька | |
Проверка соответствия маркировки техническим условиям на поставку | Каждая деталь | |
Проверка длины шпилек | Каждая шпилька | |
Проверка визуальным осмотром поверхностей шпилек и гаек на отсутствие коррозии, трещин, раковин, забоин и повреждений | Каждая деталь | |
Проверка качества резьбы резьбовыми калибрами | ||
Проверка качества и толщины покрытия | Каждая шпилька | |
Сварные соединения | Внешний осмотр | 100% |
Магнитопорошковый или капиллярный (цветной) контроль (при отсутствии документации на данный вид контроля) | ||
Радиография или ультразвуковая дефектоскопия (при отсутствии документации на данный вид контроля) | ||
Измерение твердости основного металла, металла шва, зоны термического влияния (при отсутствии документации на данный вид контроля) | 100% соединений из хромомолибденовых, хромомолибденованадиевых и хромомолибденованадиевольфрамовых сталей; 2 соединения из остальных марок стали | |
Проверка стилоскопом наличия основных легирующих элементов, определяющих марку стали в основном и в наплавленном металле | 100% | |
Определение содержания ферритной фазы для сварных соединений из аустенитных сталей, работающих при температуре свыше 350°С (при отсутствии документации на данный вид контроля) |
Приложение Д
(обязательное)
Дата добавления: 2018-09-23; просмотров: 351; Мы поможем в написании вашей работы! |
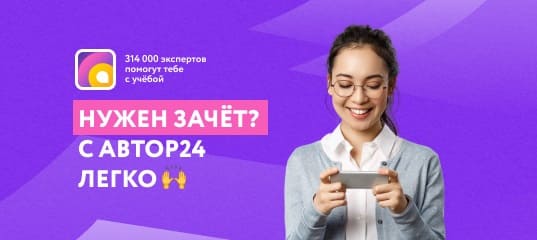
Мы поможем в написании ваших работ!