In this photo you can sort-of see the cellular structure of the rigid material.
Gaining Experience with a New Material
Posted November 29, 2012 10:00 AM by Alex Wilson
Related Categories: Energy Solutions, GreenSpec Insights
Using Foamglas instead of polystyrene to insulate beneath our basement slab and on the foundation walls.
Eli Gould cutting Foamglas for use under
our basement slab. Click to enlarge.
Photo Credit: Alex Wilson
In my role with Environmental Building News and our GreenSpec Product Database, I get plenty of opportunity to research and write about innovative building products. That’s one of the really fun aspects of my job.
On occasion I also get an opportunity to try out new or little-known materials. In the construction of our new home in Dummerston, Vermont—actually the rebuilding of a 200-year Cape—I’ve had opportunity to get some real experience with lots of products. One of these is a cellular glass insulation material known as Foamglas (check out Foamglas in GreenSpec).
Why we need a product like Foamglas
I’ve written often about the problems with extruded polystyrene from an environmental and health perspective. Relative to performance, extruded polystyrene (XPS) is a great product. It is water-resistant so can be used below-grade; it has high compressive strength so can be used beneath a concrete slab floor; it insulates very well (R-5 per inch); and it’s inexpensive. These properties make XPS the nearly universal choice for sub-slab and exterior foundation insulation today.
We installed 4"-thick Foamglas as sub-slab insulation.
Click to enlarge.
Photo Credit: Alex Wilson
But along with these benefits are some significant downsides. All XPS today (as well as expanded polystyrene, EPS) is made with the brominated flame retardant HBCD that has recently been added to the Stockholm list of Persistent Organic Pollutants (POPs) and is being banned in much of the world. HBCD provides some level of fire protection, though some studies suggest that its benefits are greatly exaggerated—and that that protection, if real, is irrelevant below grade.
In addition, XPS is currently made with the blowing agent HFC-134a, which is a potent greenhouse gas that contributes to global warming. And some of the petrochemical-derived raw materials, including benzene and styrene monomer, are carcinogenic—though once converted into polystyrene, that carcinogenicity is not present.
From a performance standpoint, XPS—like most other foam plastic insulation materials—is readily tunneled through by subterranean termites, carpenter ants, and other wood-boring insects.
|
|
In this photo you can sort-of see the cellular structure of the rigid material.
Click to enlarge.
Photo Credit: Alex Wilson
Foamglas to the rescue
Foamglas is a cellular glass, rigid boardstock insulation material. It has high compressive strength, excellent moisture resistance, and tremendous fire resistance without the use of flame retardants. It is moderately well-insulating at R-3.4 per inch (32% lower than XPS), and it’s made without environmentally damaging blowing agents. It is also about the only insulation material that is totally impervious to wood-boring insects—a useful property for below-grade applications—particularly in a warming planet with termites extending their ranges north.
Foamglas has actually been around a long time—since Pittsburgh Corning introduced it in the 1930s—but it is used primarily for high-temperature industrial applications, such as insulating steam pipes and furnaces. It’s use as an insulation material for buildings remains very uncommon, though this use is increasing in Europe.
Even though Foamglas is significantly more expensive than XPS and its per-inch insulating value is lower, the environmental and health benefits made me want to try it out on our own home.
We installed 6" Foamglas blocks on the exterior foundation walls
using a polymer-cement adhesive. Click to enlarge.
Photo Credit: Alex Wilson
Our use of Foamglas
We installed four inches of Foamglas under the basement floor slab and six inches on the exterior of the foundation walls. Our designer/builder, Eli Gould, and his six-person crew not only did admirably with this little-known material, but he came up with what I believe is a great option for adhering Foamglas to a foundation wall.
We were debating whether to use Pittsburgh Corning’s recommended solvent-based adhesive (“tar”) or their acrylic formula (a greener, water-based tar), which apparently doesn’t have quite as good performance properties as the solvent-based option. But the recommended solvent-based formulation sounded quite hazardous (it’s a two-component adhesive with one component consisting of three different types of diisocyanate and the other component consisting of petroleum asphalt, coal bitumen, naphthenic distillate, and hydrocarbon solvents). We wanted a well-performing adhesive, but the solvent-based option didn’t sound like something we wanted to expose workers to during installation or surround our home with.
|
|
Eli tested different engineered cement products, as modern polymers have dramatically changed the adhesive capabilities of cement in the last couple decades. They are also free of VOCs and sounded far safer from a health and environmental standpoint.
Дата добавления: 2018-05-02; просмотров: 239; Мы поможем в написании вашей работы! |
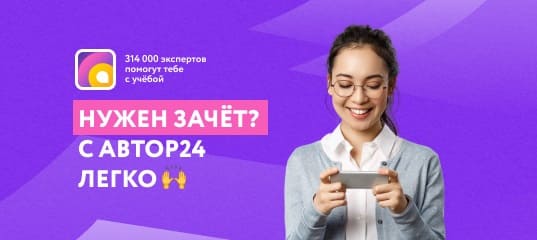
Мы поможем в написании ваших работ!