Лабораторная работа № 9. Изучение зависимости между структурой и свойствами чугунов
ГОСУДАРСТВЕННОЕ УЧРЕЖДЕНИЕ
ВЫСШЕГО ПРОФЕССИОНАЛЬНОГО ОБРАЗОВАНИЯ
«БЕЛОРУССКО-РОССИЙСКИЙ УНИВЕРСИТЕТ»
Кафедра «Технологии металлов»
Материаловедение.
Материаловедение и технология конструкционных материалов. Материаловедение и технология материалов
Лабораторный практикум для студентов технических специальностей
Часть 2
Могилев 2012
УДК 669.01
ББК 30.3
М 34
Рекомендовано к опубликованию
учебно-методическим управлением
ГУ ВПО «Белорусско-Российский университет»
Одобрено кафедрой «Технологии металлов» «31» августа 2012 г.,
протокол №
Составители: д-р техн. наук, проф. Ф. Г. Ловшенко,
канд. техн. наук., доц. А. И. Хабибуллин.
Рецензент канд. техн. наук, доц. А.В. Капитонов
В первой части лабораторного практикума содержатся основные теоретические положения и методические указания к выполнению лабораторных работ по курсу «Материаловедение».
Учебное издание
МАТЕРИАЛОВЕДЕНИЕ. МАТЕРИАЛОВЕДЕНИЕ И ТЕХНОЛОГИЯ КОНСТРУКЦИОННЫХ МАТЕРИАЛОВ. МАТЕРИАЛОВЕДЕНИЕ И ТЕХНОЛОГИЯ МАТЕРИАЛОВ
Часть 2
Ответственный за выпуск Д. И. Якубович
Технический редактор А. Т. Червинская
Компьютерная верстка И. А. Алексеюс
Подписано в печать . Формат 60х84/16. Бумага офсетная. Гарнитура Таймс.
|
|
Печать трафаретная. Усл.-печ. л. . Уч.-из. л. . Тираж 180 экз. Заказ №
Издатель и полиграфическое исполнение
Государственное учреждение высшего профессионального образования
«Белорусско-Российский университет»
ЛИ № 02330/375 от 29.06.2012 г.
212005, г. Могилев, пр. Мира, 43
© ГУ ВПО «Белорусско-Российский
университет», 2012
Содержание
8 Лабораторная работа № 8. Структура и свойства углеродистой стали в равновесном состоянии……………………… | 4 | |
9 Лабораторная работа № 9. Изучение зависимости между структурой и свойствами чугунов…………………………….. | 11 | |
10 Лабораторная работа № 10. Закалка стали………………..... | 18 | |
11 Лабораторная работа № 11. Отпуск закаленной стали……. | 25 | |
12 Лабораторная работа № 12. Изучение зависимости между структурой и свойствами стали после различных видов термической обработки…………………………………………. | 30 | |
13 Лабораторная работа №13. Пластические массы………….. | 40 | |
Список литературы……………………………………………… | 48 |
Часть 2
Лабораторная работа № 8. Структура и свойства
Углеродистой стали в равновесном состоянии
|
|
Цель работы: изучение диаграммы состояния железоуглеродистых сплавов; анализ превращений, происходящих в сплавах при охлаждениях и нагревах; определение фазового и структурного состояния сплавов в зависимости от их состава и температуры; установление зависимости между структурой и свойствами стали.
Под равновесным понимается такое состояние, при котором все фазовые превращения в сплаве полностью закончились в соответствии с диаграммой состояния. Это имеет место только при очень малых скоростях охлаждения (нагрева). Равновесное состояние соответствует минимальному значению свободной энергии и не подвергается самопроизвольному изменению во времени. Поэтому оно называется стабильным.
Превращения, протекающие в сталях в равновесном состоянии, описываются диаграммой «железо-цементит», представленной на рисунке 8.1.
Рисунок 8.1 – Диаграмма «железо-цементит»
В железоуглеродистых сплавах могут присутствовать следующие твердые фазы: феррит, аустенит, цементит.
Феррит – твердый раствор внедрения углерода в a-железе, имеющем объемноцентрированную кубическую решетку. На диаграмме «железо-цементит» существуют две области феррита – высокотемпературная область АNН и низкотемпературная область GPQ. Максимальная растворимость в высокотемпературной области составляет 0,10 % – точка Н, в низкотемпературной области 0,02 % – точка Р. Содержание углерода при комнатной температуре – 0,01 %. Феррит мягок и пластичен (sВ = 200–300 МПа, d = 20–50 %, 80–100 НВ).
|
|
Аустенит – твердый раствор внедрения углерода в g-железе, имеющем гранецентрированную кубическую решетку. На диаграмме «железо-цементит» аустенит занимает область NJESG. Максимальная растворимость углерода в аустените 2,14 % – точка Е. По механическим свойствам аустенит близок к ферриту. Горячую обработку давлением проводят в области существования аустенита (однофазный твердый раствор характеризуется высокой пластичностью).
Цементит – химическое соединение железа с углеродом – карбид железа, химическая формула которого Fe3С. Содержание углерода в цементите равна 6,67 %. Цементит обладает высокой твердостью (» 800 HV) и хрупкостью. Он имеет сложную ромбическую решетку. Она состоит из ряда октаэдров, оси которых расположены под некоторыми углами друг к другу.
Кристаллизация сплавов, содержание углерода в которых меньше 0,5 % (точка В), начинается с выделения из жидкого раствора кристаллов феррита. При содержании углерода больше 0,5 % стали кристаллизуются с выделением аустенита.
|
|
Сплавы, содержащие углерод от 0,1 % (точка Н) до 0,5 % (точка В), претерпевают при температуре 1499 oC (линия НJB) перитектическое превращение, заключающееся в том, что жидкий раствор, имеющий при этой температуре концентрацию, соответствующую точке В (0,5 % С), взаимодействуя с выделившимися из него кристаллами феррита концентрации точки Н (0,1 % С), образует новую фазу – кристаллы аустенита концентрации точки J (0,16 % С):
ФН + ЖВ ® АJ.
При дальнейшем снижении температуры в сплавах с содержанием углерода от 0,1 до 0,16 % феррит, оставшийся после перитектического превращения, перекристаллизовывается в аустенит. В сталях с содержанием углерода больше 0,16 % оставшаяся жидкость затвердевает с образованием аустенита. Ниже линий NJ и JE сплавы имеют однородную аустенитную структуру.
Все сплавы с содержанием углерода более 0,02 % (точка Р) при температуре 727 oС (линия PSK) претерпевают эвтектоидное превращение. При эвтектоидном превращении аустенит, имеющий при этой температуре концентрацию углерода, соответствующую точке S (0,8 % С), распадается с образованием эвтектоидной смеси – перлита (феррита состава точки Р (0,02 % С) и цементита):
AS ® ФР + Ц.
Эвтектоидная смесь феррита и цементита, образующаяся в результате эвтектоидного распада аустенита называется перлитом.
В сплавах с содержанием углерода менее 0,8 % (точка S) эвтектоидному превращению предшествует выделение из аустенита феррита, которое протекает в интервале температур, ограниченных линиями GS и РS. При этом в оставшемся аустените концентрация углерода изменяется по линии GS. В сплавах с содержанием углерода более 0,8 % (точка S) эвтектоидному превращению предшествует выделение из аустенита цементита. Выделение цементита протекает в интервале температур, ограниченных линиями ES и SK. В этом случае концентрация углерода в оставшемся аустените изменяется по линии ES.
Железоуглеродистые сплавы в зависимости от содержания углерода делятся на три группы: техническое железо, стали, чугуны.
Техническое железо – это сплавы с содержанием углерода менее 0,02 % (точка Р). Как следует из диаграммы «железо-цементит», техническое железо имеет структуру феррита или феррита и цементита третичного, который в виде отдельных мелких включений располагается по границам зерен феррита (рисунок 8.2, а). Третичный цементит выделяется из феррита в результате снижения растворимости углерода при уменьшении температуры от эвтектоидной (727 оС) до комнатной. Предельная растворимость углерода в феррите ограничивается линией GPQ. По свойствам техническое железо подобно ферриту.
Стали – это сплавы с содержанием углерода от 0,02 % (точка Р) до 2,14 % (точка Е). В структуре стали по мере увеличения содержания углерода возрастает доля цементита и соответственно уменьшается доля феррита. Это приводит к повышению твердости и прочности стали и снижению ее пластичности, изменению физических и технологических свойств. В зависимости от содержания углерода стали по своей структуре делятся на доэвтектоидные, эвтектоидные и заэвтектоидные.
Доэвтектоидные стали содержат от 0,02 % углерода (точка Р) до 0,8 % углерода (точка S). Она имеет структуру феррита (светлые зерна) и перлита (темные зерна) (рисунок 8.2, б, в). Количественное соотношение между перлитом и ферритом зависит от содержания углерода. С увеличением содержания углерода прямо пропорционально увеличивается содержание перлита. При концентрации углерода в стали 0,8 % количество перлита равно 100 %. Зная площадь, занимаемую перлитом, с достаточной для практики точностью можно определить содержание углерода в углеродистой стали:
С = ,
где А – площадь, занимаемая перлитом.
Эвтектоидная сталь содержит 0,8 % углерода (точка S) и состоит из перлита (рисунок 8.2, г).
Рисунок 8.2 – Микроструктура технического железа (а), доэвтектоидных сталей с содержанием углерода 0,20 % (б) и 0,45 % (в), эвтектоидной (г) и заэвтектоидной (д) сталей
Заэвтектоидная сталь содержит от 0,8 % углерода (точка S) до 2,14 % углерода (точка Е). Заэвтектоидная сталь состоит из перлита и цементита (рисунок 8.2, д).
Таким образом, структура, а следовательно, и свойства стали определяются количеством углерода в ней. Доэвтектоидные стали, содержащие до 0,8 % углерода, являются конструкционными, предназначенными для изготовления деталей машин (машиностроительные стали), конструкций и сооружений (строительные стали). В значительной мере свойства углеродистых сталей, а, следовательно, и область их применения зависят от содержания в них вредных примесей серы и фосфора. Чем меньше их в стали, тем выше ее качество.
Стали обыкновенного качества, наиболее дешевые, являются конструкционными сталями общего назначения и содержат до 0,07 % фосфора, 0,06 % серы, 0,06–0,49 % углерода. По гарантируемым свойствам они подразделяются на три группы – А, Б, В. В сталях группы А – гарантируются механические свойства, группы Б – химический состав; в сталях группы В гарантируются механические свойства и химический состав.
Сталь группы А маркируется буквами Ст и номером 0, 1, 2, ... 6, например, Ст1. В сталях группы Б перед буквами Ст ставится буква Б, например, БСт2. В сталях группы В перед буквами Ст ставится буква В, например, ВСт3. С увеличением условного номера повышается содержание углерода в стали, что приводит к увеличению прочностных свойств, к снижению пластичности и свариваемости.
Стали группы А применяются для изготовления рядового проката (швеллеров, уголков, листов, прутков, труб и др.) используемого для клепанных и болтовых конструкций, а также для малонагруженных деталей машин (валов, осей, зубчатых колес, болтов и т. д.) не подвергаемых нагреву в процессе обработки. Стали группы Б применяются для изготовления изделий, подвергаемых нагреву (горячей обработке давлением, сварке, термической обработке). Стали группы В применяются для изготовления сварных конструкций, подвергаемых расчетам на прочность.
В конце марки стали ставятся буквы «кп», «пс», «сп». Буквы «кп» показывают, что сталь кипящая, «пс» – полуспокойная, «сп» – спокойная.
Качественнаяконструкционная сталь по сравнению со сталью общего назначения содержит вдвое меньше серы и фосфора и отличается более высокими механическими свойствами. Она маркируется цифрами, например, 08, 10, … 80, показывающими содержание углерода в сотых долях процента.
Низкоуглеродистые стали, содержащие углерода до 0,25 %, обладают невысокой прочностью и высокой пластичностью и применяются для изготовления изделий листовой холодной штамповкой (05кп…10), а также для деталей, упрочняемых цементацией, и для различных сварных соединений (Сталь 15, Сталь 20). Кроме того, из последних сталей изготавливают болты, шпильки, гайки, валики неответственного назначения и т. п.
Среднеуглеродистые стали марок 30-50 предназначаются для ответственных деталей высокой прочности с вязкой сердцевиной (зубчатые колеса, шатуны, коленчатые валы, распределительные валы, винты, оси, втулки, рычаги и др.). Как правило, детали из этих сталей подвергаются улучшению (вид термической обработки).
Высокоуглеродистые стали 55-85 применяются для пружин, рессор, а также деталей высокой прочности: прокатных валков (сталь 60), крановых колес (сталь 75), дисков муфт сцепления (сталь 85) и др. Детали из этих сталей подвергаются закалке и отпуску (виды термической обработки).
Для изготовления различных инструментов применяется углеродистая инструментальная сталь, содержащая углерода от 0,7 до 1,3 %. Она имеет пониженное содержание вредных примесей: фосфора – до 0,035 % и серы – до 0,03 % (качественная сталь) или фосфора – до 0,03 % и серы – до 0,02 % (высококачественная). Эта сталь производится следующих марок: У7 - У13 (качественная) или У7А - У13А (высококачественная). Здесь «У» означает «углеродистая инструментальная сталь», число после «У» - содержание углерода в десятых доля процента (например, У12 содержит углерода 1,2 %). Буква «А» в конце марки означает – высококачественная сталь.
Стали марок У7 и У8 вязче других, так как не имеют в структуре цементита, и они идут на изготовление ударных инструментов – молотков, зубил, топоров, кернеров, стамесок, долот, штампов и т. д.
Стали У10 и У11 имеют несколько меньшую вязкость и немного большую твердость (т.к. в их структуре содержится небольшой количество цементита) и используются для изготовления резцов, сверл, метчиков, лерок.
Стали У12 и У13 обладают низкой вязкостью и высокой твердостью и используются для изготовления инструмента, не испытывающего ударных нагрузок (напильников, бритв, рашпилей и т. п.).
Контрольные вопросы
1. Описать превращения, протекающие в сталях при нагреве или охлаждении, указать их температуры.
2. Дать определение фазам, присутствующим в сталях и указать содержание углерода в них.
3. Дать классификацию углеродистых сталей по качеству, содержанию углерода и назначению.
4. Изучить маркировку сталей и указать области применения перечисленных сталей:
Ст2, БСт3, ВСт4, Ст6;
08кп, 10, 15, 20, 25, 30, 40, 50, 60, 75, 80;
У7, У8, У10А, У11, У12, У13.
Задание по работе
1. Зарисовать диаграмму «железо-цементит».
2. Дать определение: фазам и структурным составляющим в сталях (доэвтектоидной, эвтектоидной, заэвтектоидной).
3. Определить содержание углерода в образце доэвтектоидной стали.
4. Изучить и зарисовать микроструктуру предложенных шлифов; указать вид материала и расставить структурные составляющие фазы.
5. Указать марки сталей, применяемых для изготовления деталей машин, сварных конструкций и инструментов согласно заданию преподавателя.
Лабораторная работа № 9. Изучение зависимости между структурой и свойствами чугунов
Цель работы: изучение микроструктуры чугунов разных марок, их свойств и области применения.
Чугунами называют железоуглеродистые сплавы, содержащие более 2,14 % углерода. В машиностроении чугун является одним из основных литейных материалов, что объясняется, прежде всего, его хорошими литейными и прочностными свойствами. Он не подвергается обработке давлением. Главным фактором, определяющим свойства, а, следовательно, и область использования чугуна, является его структура.
По структуре чугуны делят на белые (БЧ), серые (СЧ), ковкие (КЧ) и высокопрочные (ВЧ).
Основной особенностью белых чугунов является то, что в них углерод связан в химическое соединение – цементит (Fe3C). Структура белых чугунов описывается метастабильной диаграммой Fe–Fe3C (рисунок 9.1).
|
|
|
|
|

C
Рисунок 9.1 – Диаграмма Fe–C
(сплошные линии – диаграмма «Fe–Fe3C», штриховые – «Fe – графит»)
Белые чугуны подразделяются на доэвтектические (С = 2,14–4,3 %), эвтектические (С = 4,3 %) и заэвтектические (С = 4,3–6,67 %).
Высокая твердость и хрупкость цементита определяют свойства белого чугуна и не позволяют использовать его в качестве конструкционного материала.
В сером, ковком и высокопрочном чугунах весь углерод или часть его выделяется в виде графита. Причем в сером чугуне графит имеет пластинчатую форму, в ковком – хлопьевидную и в высокопрочном шаровидную (рисунок 9.2). Включения графита располагаются в металлической основе, которая в зависимости от условий получения материала может быть ферритной, перлитной или ферритно-перлитной. Схема структуры этих материалов приведена на рисунке 9.3.
а – пластинчатая в сером; б – хлопьевидная в ковком; в – шаровидная в высокопрочном
Рисунок 9.2 – Форма графитных включений в чугуне
Рисунок 9.3 – Классификация чугуна по структуре металлической основы и форме графитных включений
Установлено, что чем больше углерода и кремния в сплаве и чем ниже скорость его охлаждения, тем выше вероятность кристаллизации по диаграмме стабильного равновесия с образованием графитной эвтектики по схеме Ж(С’) ® А(Е’) + Г.
Обычно в серых чугунах содержится 3,0...3,7 % С; 1,2...2,6 % Si. Высокое содержание кремния в сером чугуне объясняется тем, что кремний является сильным графитообразующим элементом. Растворяясь в аустените, кремний способствует уменьшению растворимости углерода в нем, в результате жидкая фаза обогащается углеродом, и процесс образования графита облегчается.
При конструировании деталей машин следует учитывать, что серые чугуны работают на сжатие лучше, чем на растяжение. Они мало чувствительны к надрезам при циклическом нагружении, хорошо поглощают колебания при вибрациях, обладают высокими антифрикционными свойствами из-за смазывающей способности графита, хорошо обрабатываются резанием, дешевы и просты в изготовлении.
Отливки изготавливают из чугуна следующих марок: СЧ10…СЧ35. Цифры в обозначении марки соответствуют минимальному пределу прочности при растяжении sВ, кгс/мм2. Чугун СЧ10 – ферритный, СЧ15, СЧ18, СЧ20 – ферритно-перлитные, начиная с СЧ25 – перлитные.
Из ферритно-перлитных чугунов в автомобилестроении изготавливают тормозные барабаны, крышки и др.; из перлитных – блоки цилиндров, гильзы цилиндров, маховики и др. В станкостроении серый чугун является основным конструкционным материалом (станины станков, столы, шпиндельные бабки, и др).
Высокопрочный чугун получают модифицированием (микролегированием) жидкого чугуна присадками (0,1...0,5 % магния от массы чугуна, 0,2…0,3 % церия, иттрия). Модифицирование приводит к образованию графита шаровидной формы, негативное влияние которого на прочность материала значительно ниже, чем пластинчатого графита, так как концентрация напряжений в зоне надреза металлической основы графитовыми включениями обратно пропорциональна радиусу скругления (рисунок 9.4).
Рисунок 9.4 – Влияние формы надреза металлической основы на величину
растягивающих напряжений
Химический состав высокопрочного чугуна (2,7...3,7 % С; 0,5...3,8 % Si) выбирается в зависимости от толщины стенки отливки (чем тоньше стенка, тем больше скорость охлаждения, тем больше углерода и кремния во избежание образования цементита).
Отливки изготавливают из высокопрочного чугуна следующих марок: ВЧ35 …ВЧ100 (цифры соответствуют пределу прочности при растяжении sВ, кгс/мм2). Высокопрочный чугун широко применяется в практике взамен стального литья, поковок, штамповок, обеспечивая надежность и долговечность изделий в различных режимах эксплуатации. Отличительные особенности ВЧ в сравнении со сталью – более высокое отношение предела текучести к пределу прочности при растяжении, равное 0,70–0,80 (против 0,50–0,55 для стали); низкая чувствительность к концентраторам напряжений; повышенная (до 3,5 раз) циклическая вязкость и другие – позволяют считать этот конструкционный материал более эффективным, чем сталь, особенно в условиях действия динамических нагрузок. Широкое использование ВЧ в деталях машин наряду с их надежностью является мощным резервом снижения расхода материалов, себестоимости изделий и улучшения показателей их работы. В мировой практике ВЧ применяют для литья блоков цилиндров, шатунов, головок блоков, тормозных барабанов, дисков сцепления, суппортов тормозных систем, поршневых колец, коленчатых и распределительных валов, деталей трансмиссии, зубчатых колес и ряда других деталей. Столь широкое применение ВЧ обусловлено уникальным сочетанием физико-механических и литейных свойств, превосходящих свойства многих сталей. Например, стоимость коленчатого вала, изготовленного из ВЧ в 2 раза меньше, при 2-3 кратном увеличении срока службы.
Ковкий чугун получают путем отжига белого чугуна. Рекомендуемый химический состав сплава следующий: 2,4...2,9 % С; 1,0...1,6 % Si; 0,3...1,0 % Мn. При таком составе сплава и ускоренном охлаждении в отливке формируется структура белого доэвтектического чугуна (П + Л + ЦII). После охлаждения отливку подвергают графитизирующему отжигу, в процессе которого неустойчивая фаза – цементит – распадается с образованием графита хлопьевидной формы. Отжиг состоит из двух стадий (рисунок 9.5). Первая осуществляется выше температуры точки Ас1 при t ≈ 1000 °С. Длительность первой стадии отжига должна обеспечить полный распад цементита, входящего в состав ледебурита, на аустенит и графит. Металлическая основа чугуна формируется на второй стадии отжига при эвтектоидном превращении.
В случае непрерывного охлаждения отливки в области эвтектоидной температуры аустенит распадается на перлит пластинчатый. Получается ковкий чугун с перлитной металлической основой. Он обладает высокими твердостью (230...300 НВ) и прочностью (sВ = 650...800 МПа) в сочетании с небольшой пластичностью (d = 3,0...1,5 %). Для повышения пластичности при сохранении высокой прочности проводится непродолжительная (2–4 ч) изотермическая выдержка чугуна при температурах 690…650 °С. Это вторая стадия отжига, представляющая собой в данном случае отжиг на зернистый перлит. Перлит пластинчатый переходит в перлит зернистый путем сфероидизации (округления) пластин цементита.
Наряду с ковким чугуном, имеющим перлитную основу, широко распространен в машиностроении ферритный ковкий чугун, характеризующийся высокой пластичностью (d = 10...12 %) и относительно низкой прочностью (sВ = 370...300 МПа). Ферритная основа чугуна образуется в процессе длительной изотермической выдержки (≈ 30 ч) при 720...700 °С. Здесь цементит, входящий в состав перлита распадается на Ф + Г.
|
|
Рисунок 9.5 – График отжига белого чугуна на ковкий
Выпускаются следующие марки ковких чугунов: КЧЗ0–12, КЧ80–1,5. Первые две цифры соответствуют минимальному пределу прочности при растяжении sВ, кгс/мм2, цифры после тире – относительному удлинению d, %. Марки, имеющие повышенные значения d, относятся к ферритным чугунам, с низкими значениями – к перлитным.
Перечень литых изделий из КЧ весьма разнообразен (пробки, гайки, втулки, фланцы, кронштейны, ступицы, тормозные колодки, коленчатые валы и др.). Существенным недостатком технологического процесса получения КЧ является длительный отжиг отливок и ограничение толщины их стенок (до 50 мм).
Контрольные вопросы
1. Перечислить преимущества чугунов перед сталями..
2. Дать определение фазам, присутствующим в чугунах и указать содержание углерода в них.
3. Дать классификацию чугунов, описать процесс их структурообразования.
4. Изучить маркировку чугунов и указать области применения перечисленных марок:
СЧ10, СЧ15, СЧ18, СЧ20, СЧ25, СЧ28, СЧ3О, СЧ35;
КЧЗ0–12, КЧ35-10, КЧ45-7, КЧ50-5, КЧ60-3, КЧ80–1,5;
ВЧ40, ВЧ45, ВЧ50, ВЧ60, ВЧ70, ВЧ80, ВЧ120.
Задание по работе
1 Вычертить диаграмму состояния железоуглеродистых сплавов, ее участок, соответствующий чугунам.
2 Дать характеристику серым чугунам, зарисовать микроструктуру. Привести марки СЧ, назвать их механические свойства и область применения.
3 Дать характеристику ковким чугунам. Описать способ их получения, начертить график отжига. Объяснить формирование структуры КЧ с определенной (по заданию преподавателя) металлической основой. Зарисовать микроструктуру, указать свойства и область применения КЧ.
4 Дать характеристику высокопрочным чугунам. Объяснить способ получения, зарисовать микроструктуру. Назвать марки ВЧ, их свойства, область применения и преимущества перед другими чугунами.
10 Лабораторная работа № 10. Закалка стали
Дата добавления: 2018-02-28; просмотров: 1177; Мы поможем в написании вашей работы! |
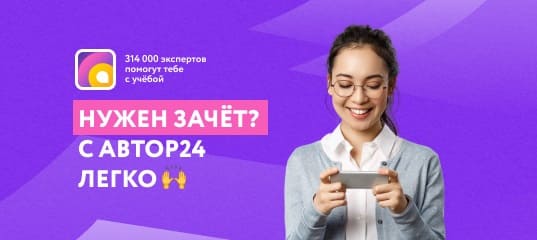
Мы поможем в написании ваших работ!