Ответ на домашнее задание (в виде сканкопий, фотографий или документов Microsoft Word)
МДК.03.04. ТЕХНОЛОГИЯ АВТОМАТИЧЕСКОГО И МЕХАНИЗИРОВАННОГО НАПЛАВЛЕНИЯ
Сварщик (электросварочные и газосварочные работы)
ПЛАН УРОКА № 6
Группа: СВ-4-18
Дата: 22.05.20 г.
Преподаватель ПТП: Л.Н.Иванова
Тема программы: НАПЛАВКА В СРЕДЕ ЗАЩИТНОГО ГАЗА.
ТЕМА УРОКА: СХЕМЫ НАПЛАВКИ ЦИЛИНДРИЧЕСКИХ ПОВЕРХНОСТЕЙ, ВНУТРЕННЕЙ ПОВЕРХНОСТИ ПРЕСС-ВТУЛКИ, ЛОПАСТИ ГИДРОТУРБИН
Цель урока: изучить схемы наплавки цилиндрических поверхностей, внутренней поверхности пресс-втулки, лопасти гидротурбин
Наплавка цилиндрических поверхностей весьма востребована, ведь это наиболее выгодный способ восстановления дорогостоящего оборудования. Износу подвержены рабочие валки прокатных и обжимных станов. Валы гидротурбин также нуждаются в реставрационных работах. А что уж говорить о машиностроении, где множество деталей имеют именно цилиндрическую форму.
Такие изделия работают в неодинаковых условиях, имеют разные габариты и отличаются по химическому составу. И чтобы подобрать оптимальные режимы, наплавочные материалы и способ восстановления, необходимо учитывать все эти факторы. Например, при восстановлении коленвалов необходимо одновременно решить несколько задач. Во-первых, восстановить размеры шеек. Во-вторых, обеспечить достаточную износостойкость. В-третьих, добиться высоких показателей усталостной прочности. В-четвертых, обеспечить правильную работу всех сопряженных деталей.
|
|
Схемы и примеры наплавки цилиндрических деталей приведены на рисунке 1. Скорость подачи проволоки, а соответственно и силу сварочного тока выбирают в зависимости от диаметра и формы изделия, подлежащего наплавке.
Наплавку цилиндрических деталей производят на специальных наплавочных установках или на токарных станках, приспособленных для этой цели.
Рис. 1. Схемы наплавки цилиндрических поверхностей по винтовой линии (а) и с поперечными колебаниями электрода (б)
Прежде чем приступать непосредственно к наплавочным работам, необходимо подготовить поверхность детали. При повторной наплавке изделия обтачивают на вальцетокарном станке. Если на поверхности детали есть мелкие вмятины, бороздки, растрескивания термического характера, тогда предварительную обточку не проводят. Еще обрабатываемую деталь проверяют на биение, оно не должно превышать 0,3 мм. Все шпоночные пазы необходимо закрыть графитовыми либо медными вставками. Причем последние должны выступать над наплавленным слоем минимум на 1 мм.
Далее по технологии наплавки валов следует предварительный подогрев. Температура зависит от ряда факторов, так, при использовании порошковых материалов изделие нагревают до 370 °C. Если осуществляют наплавку проволокой 30ХГСА, достаточно 250 °C. Флюс обязательно просушивают, если он влажный, тогда необходима перезакалка при температуре 300–400 °C.
|
|
Затем деталь зажимается в патроне и оборудование вращает ее с постоянной скоростью, а сварочная головка движется прямолинейно вдоль вала. Расплавленный металл подается капельно и формирует довольно плотный слой. Затем к месту наплавки подают охлаждающую жидкость, насыщенную ионизирующими солями, которые благоприятно влияют на горение дуги.
В таблице 1 приведены рекомендуемые режимы наплавки под слоем флюса цилиндрических деталей большого диаметра.
Таблица 1.
Режимы наплавки под флюсом цилиндрических деталей малого диаметра
Диаметр детали, мм | Диаметр электродной проволоки, мм | Сила тока, А | Напряжение дуги, В | Скорость наплавки, м/ч |
200 160 120 90 60 | 2,0 2,0 2,0 1,6 1,2 | 220…260 200…240 170…200 150…180 110…130 | 27…30 27…30 26…29 26…29 25…28 | 28…32 24…28 20…24 16…20 14…18 |
Теперь пришло самое время поговорить про оборудование, нужное для наплавки валов. Установка для восстановления прокатных валов состоит из:
|
|
· люнетов для поддержки изделия;
· механизма, обеспечивающего вращение вала и сварочной головки АБС;
· источников питания и электронагревателя.
Сварочную головку подвешивают на специальных направляющих и путем перестановки сменных шестерен регулируют скорость ее перемещения. Такое оборудование посредством специального пульта предусматривает управление процессом подачи наплавочного материала, скоростью передвижения головки, вылетом электрода.
А вот изменять угол наклона подачи сварочной проволоки, а также обеспечивать перемещение головки поперек валков оборудование позволяет только вручную. Флюс засыпают в специальный бункер, откуда он и подается. Электронагреватель состоит из двух полукорыт. Очень важно обеспечить свободное перемещение этого узла к любому участку. С этой целью нижнее полукорыто устанавливают на специальную тележку.
Правильно подобрать способ и наплавочный материал можно только после тщательного анализа условий работы и иных особенностей обрабатываемого изделия.
Для восстановления стальных валков для станов горячей прокатки нашла свое применение порошковая проволока ПП-Нп-35В9Х3СФ. Этот материал может обеспечить прекрасную износостойкость, однако его стоимость велика, так как в состав входит 10% дорогого вольфрама. А вот для ремонта рабочих элементов обжимных станов и наплавки коленчатых валов прекрасно подойдет и более дешевая проволока Нп-30ХГСА.
|
|
Рис.2 Установка для восстановления прокатных валов Рис. 3. Порошковая проволока
Просмотр фильма «Как заправить проволоку в полуавтомат», перейдя по ссылке https://www.youtube.com/watch?v=90KqnS7sn2I
АВТОМАТИЧЕСКАЯ ЭЛЕКТРОДУГОВАЯ НАПЛАВКА ПОД ФЛЮСОМ ВАЛА ГИДРОТУРБИНЫ
Детали оборудования, эксплуатируемого на электростанциях, подвергаются различным видам изнашивания.
Наиболее ответственными из них являются валы гидротурбин (рис. 4), основная причина выхода из строя которых — кавитационное и гидроабразивное изнашивание шеек валов, расположенных под подшипниками и сальниками.
До настоящего времени ремонт валов производили методом бандажирования. Бандаж изготавливают из листов нержавеющей стали 12Х18Н1 0Т толщиной 10-12 мм по достаточно сложной технологии, включающей вальцовку листов, их резку, сварку и механическую обработку. Время бандажирования вала диаметром около 1 м составляет две-три недели.
Рис. 4. Валя гидротурбин
Мы рассматриваем опыт восстановления крупногабаритного вала поворотно-лопастной гидротурбины (мощность агрегата 250 МВт) из стали 20ГЛ диаметром 1 м, длиной 4,5 м и массой около 12 т с помощью автоматической дуговой наплавки под флюсом.
Для наплавки деталей таких размеров необходимо было изготовить соответствующее оборудование, выбрать наплавочные материалы и разработать технологию наплавки. Специалистами Института электросварки им. Е. О. Патона для наплавки крупногабаритных валов был модернизирован токарно-винторезный станок РТ-166 (типа ДИП-500). На суппорт станка установили наплавочный автомат А1406, заднюю бабку и редуктор станка подняли на 160 мм, а электрическую схему станка дополнили частотным преобразователе, что обеспечило необходимую для наплавки скорость вращения вала гидротурбины. Это позволило производить наплавку деталей типа «вал» как по кольцу, так и по винтовой линии. В качестве источника питания использовали выпрямитель ВС-600.
В результате модернизации на установке, выполненной на базе токарного станка РТ-166, можно наплавлять и механически обрабатывать после наплавки валы гидротурбин диаметром от 400 до 1050 мм, длиной до 4500 мм и массой до 12 т.
Внешний осмотр изношенного вала гидротурбины показал, что длина участка вала, подлежащего восстановлению, составляет примерно 710 мм. Для устранения дефектов применили токарную обработку. Обработанную под наплавку поверхность проверили на наличие дефектов ультразвуковым контролем, который позволяет выявить трещины, поры, отслоения и т. п. Оставшиеся после токарной обработки дефекты устранили зачисткой абразивными кругами.
После механической обработки вал имел диаметр примерно 1000 мм. Номинальный диаметр восстановленного вала на этом участке 1020 мм. С учетом значительной величины износа было предложено выполнять сначала наплавку подслоя сплошной проволокой Св-08 под флюсом АН-348 (рис. 4). Минимальный диаметр вала после наплавки подслоя составлял 1018 мм.
Рис.5. Контроль температуры с помощью тепловизора AZ 8868
После полного остывания вала протачивали наплавленную поверхность до диаметра 1010 мм и производили ультразвуковой контроль. По техническим требованиям в подслое и в антикоррозионном слое, а также в зоне термического влияния и основном металле трещины не допускаются. В обеих наплавленных слоях допускаются отдельные поры диаметром не более 2,0 мм или скопления мелких пор диаметром не более 1,0 мм в количестве 3 шт. на площади 1 см2. Трещины и поры, которые превышают допустимые размеры, должны быть удалены механической обработкой. В результате ультразвукового контроля в наплавленном подслое никаких дефектов не было обнаружено.
Выполнили автоматическую наплавку под флюсом АН-26П слоя коррозионно-стойкой нержавеющей стали. Минимальный диаметр вала после наплавки коррозионно-стойкого слоя 1028 мм. Наплавленную поверхность вала протачивали до диаметра 1020 мм и производили ультразвуковой контроль. Как и в подслое, в основном наплавленном слое дефектов не было обнаружено. Шейка вала для посадки подшипника имеет жесткие допуски, поэтому окончательно наплавленную поверхность обрабатывали шлифованием.
Всего на изношенную поверхность вала было наплавлено около 320 кг металла, машинное время наплавки составило 60 ч. Учитывая, что процесс наплавки каждого из слоев (подслоя и коррозионностойкого слоя) шел практически непрерывно, вал нагревался, поэтому его деформации могли превысить допустимые пределы. С помощью тепловизора AZ 8868 контролировали температуру наплавляемого вала (рис. 5). Температура после наплавки последнего прохода коррозионностойкого слоя не превышала 150 °С. Замеры показали, что такой нагрев не привел к деформации вала.
ДОМАШНЕЕ ЗАДАНИЕ: написать краткий конспект по теме урока согласно плана:
1. Как подобрать оптимальные режимы наплавки?
2. Зарисовать схемы наплавки цилиндрических поверхностей.
3. Устройство установки для восстановления прокатных валов.
4. Принцип работы установки для наплавки.
5. Способы устранения дефектов наплавки.
Ответ на домашнее задание (в виде сканкопий, фотографий или документов Microsoft Word)
прислать на электронный адрес:
larisanikolaevna.epgl@yandex.ru
Дата добавления: 2022-06-11; просмотров: 26; Мы поможем в написании вашей работы! |
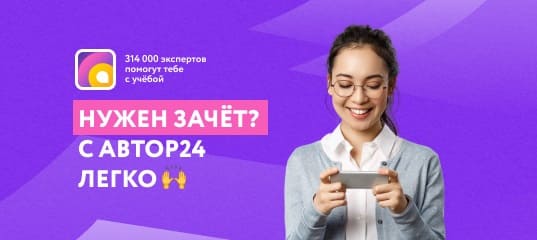
Мы поможем в написании ваших работ!