Заполнители из камыша и костры
В разных районах нашей страны имеются большие заросли камыша. Сечку камыша применяют в качестве заполнителя для арболита. Её готовят из зрелых стеблей камыша наиболее благоприятной зимней заготовки. Стебли камыша сначала режут на силососоломорезке и затем дополнительно измельчают на молотковой дробилке. Частицы полученной сечки имеют длину 7-35 мм, ширину 2-6 мм и толщину 1-2 мм. По техническим требованиям наибольшая крупность сечки 5 мм.
Перед применением сечки её, подобно некоторым древесным наполнителям, минерализуют.
Конопляная костра – это отход первичной переработки стеблей конопли на пеньку. Она представляет собой мелкие частицы (раздробленной одревесневшей части стебля) неправильной формы длиной 10-70 мм и в поперечнике 2-2,5 мм.
До первичной обработки стебли конопли вымачивают 20-30 суток в естественных водоёмах или в заполненных водой ямах, или же в бассейнах с горячей водой на пенькоперерабатывающих заводах. Биохимические процессы происходят с вымыванием из костры водорастворимых веществ – сахаров, органических кислот, минеральных солей. Ввиду небольшого диаметра стеблей конопли и большой их пористости экстрактивные вещества удаляются из них быстрее и более полно, чем из древесины. Такая обработка конопли защищает цементный камень от коррозии. Поэтому при производстве арболита из конопляной костры её не замачивают в воде с минерализаторами.
|
|
Влажность конопляной костры, применяемой для арболита, должна быть не более 20% по массе. Её хранят в закрытом складе или под навесом.
Льняная костра состоит из узких тонких пластин длиной до 50 мм, шириной до 3 мм и толщиной до 3 мм. В ней содержится больше, чем в конопляной костре, вредных для цемента веществ. В случае применения с цементом её минерализуют.
Использование древесных и других растительных заполнителей для изготовления искусственных строительных конгломератов даёт возможность получать большой экономический эффект, а также уменьшает загрязнённость окружающей природной среды.
Пустотелый заполнитель для лёгкого бетона на основе торфа и минерального сырья
Традиционно в качестве заполнителей лёгких бетонов используют керамзит – продукт, получаемый при обжиге легкоплавких вспучивающихся глинистых пород. От качества и состава глинистого сырья зависят свойства получаемого заполнителя. В настоящее время многие предприятия по производству керамзита отмечают значительное ухудшение одной из основных его характеристик – теплопроводности. Увеличение теплопроводности связано с недостаточной вспучиваемостью глин и, как следствие, с низкой пористостью получаемого заполнителя.
|
|
Пустотелый заполнитель на основе торфа и глинистого сырья позволяет существенно продвинуться в решении этой проблемы. Разработанная схема технологического процесса его производства состоит из следующих операций:
1) добыча торфяного сырья;
2) его механическая переработка (дробление);
3) окатывание торфа на грануляторе тарельчатого типа;
4) искусственная подсушка окатышей;
5) добыча глинистого материала;
6) приготовление шликера;
7) нанесение минерального покрытия на торфяные ядра;
8) сушка композиционных гранул;
9) обжиг гранул;
10) охлаждение материала;
11) складирование полученного продукта.
Определённые трудности в реализации предлагаемого способа возникают при нанесении минерального покрытия на торфяные гранулы, а также при сушке и обжиге композиционных гранул.
Дробление торфяной крошки поводится на молотковой дробилке с колосниковой решёткой. Полученная масса при влажности 82-86% окатывается на тарельчатом грануляторе. Размер гранул после окатывания составляет приблизительно 15 мм.
Для минерального покрытия применяется глина. Из неё готовится суспензия с влажностью 50-55%, в которой смачиваются торфяные гранулы. К преимуществам мокрого способа нанесения покрытия можно отнести:
|
|
1) достижение однородности минеральной пульпы;
2) сравнительную простоту удаления из глинистого сырья посторонних включений;
3) отсутствие энергоёмкого процесса первоначального помола.
Прочностные характеристики формованной продукции на основе торфа зависят от его влажности. Чем меньше содержание влаги в материале, тем выше его прочность.
После нанесения минерального покрытия композиционные гранулы высушиваются при температуре 100-120°С до полного обезвоживания. Обжиг гранул проводится при температуре до 1000°С. При обжиге торфяное ядро выгорает, а минеральная оболочка спекается. В результате получается гранула пустотелого заполнителя.
Полученный заполнитель характеризуется большой межзерновой пустотность, обладает высокой открытой пористостью. Пустотность достигает 72%. Плотность зёрен в сухой сыпучей среде составляет 400 кг/м3, в цементном тесте – 1400 кг/м3. Коэффициент Фомы зёрен – 1,04. Водопоглощение по массе – 20%. Прочность при сдавливании в цилиндре – 0,9 МПа.
Экономия расхода цемента на 1 м3 бетона составляет 100-150 кг. Теплофизические характеристики бетона улучшаются по сравнению с традиционным керамзитобетоном за счёт снижения средней плотности и мелкопористой структуры прослоек цементного камня.
Дата добавления: 2022-06-11; просмотров: 33; Мы поможем в написании вашей работы! |
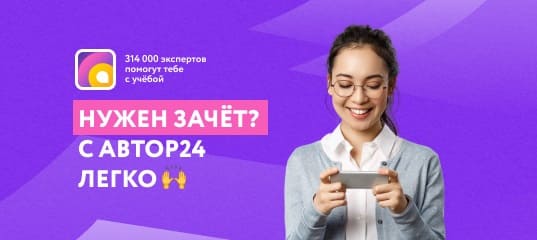
Мы поможем в написании ваших работ!