Токсикологическая оценка основных видов сырья 10 страница
Рецептура анодной массы состоит из различных по размеру частиц кокса — от самых крупных (более 4 мм) до пылевидных (менее 0,08 мм) частиц. Такая рецептура позволяет создавать
смесь с наиболее плотной упаковкой частиц, т.е. с минимальным объемом пустот между зернами кокса. Эта пустота при произ- водстве массы заполняется пеком, который впоследствии кок- суется.
Кокс-наполнитель перед использованием проходит прокал- ку при температуре выше 1150 °С, и потому его реакционная способность (способность окисляться кислородом и анодными газами) хуже, чем таковая у кокса из связующего, поскольку он образуется при температуре электролиза. Вследствие изложен- ного кокс из связующего окисляется с большей скоростью, и при этом зерна кокса-наполнителя выпадают в пену. Отсюда понятно, что при подборе рецептуры массы стремятся снизить до возможного минимума содержание пека.
Однако недостаточно только заполнить пеком пустоты между зернами кокса, ибо в таком случае масса окажется малотекучей и не заполнит пустоты при замене штырей. Поэтому на практике количество пека превышает (а иногда и значительно) необходимый минимум, определяемый объемом пустот между зернами кокса. Повышенное содержание пека вызывает сегрегацию (расслоение) жидкой анодной массы и образование пека, что обычно приводит к протекам массы и повышенному выходу смолистых веществ в атмосферу.
|
|
Содержание пека, а следовательно, и текучесть массы выше для электролизеров ВТ, чем для
что предопределяет большее количество пены и больший выход смолистых веществ в атмосферу на электролизерах ВТ. Кроме того, на электролизерах ВТ столб анода меньше, и потому, например, на температура верха жидкой анодной массы допускается до
160 °С против °С на анодах с БТ. Увеличить столб анода на электролизерах ВТ невозможно, так как это повлечет за собой увеличение не только длины штырей и расхода электро- энергии, но и высоты здания корпуса электролиза.
Радикальное снижение выхода смолистых веществ в атмо- сферу можно обеспечить двумя путями: а) применением сухой анодной массы и/или б) использованием пека с повышенной температурой размягчения. Рассмотрим оба способа подробнее. Содержание пека в массе при использовании кокса достигает
но, как показала работа А Дмитриева
по: необходимое и достаточное количество пека составляет
а весь оставшийся пек теряется не-
производительно. Поэтому применение анодной массы с пони- женным содержанием пека (так называемая сухая масса) может обеспечить заметное снижение выхода смолистых веществ.
|
|
Действительно, работы, проведенные компанией
на ряде зарубежных заводов, оборудованных электролизе- рами ВТ, и опыт на электролизерах полностью подтвердили эту точку зрения. Так, на [25] применение сухой анодной массы, содержащей 22,5 % пека, по сравнению с типовой массой с 25,7 % пека обеспечило снижение выброса смолистых веществ в атмосферу в 7,3 раза, а содержание смолистых веществ в воздухе рабочей зоны при перестановке штырей сократилось более чем в 420 раз. По- ложительные результаты при использовании сухой массы уда- лось получить и на электролизерах ВТ, однако из-за отсутствия необходимой механизации внедрить эту технологию не удалось.
Таким образом, важным путем снижения выброса смолистых веществ является применение сухой анодной массы.
Второй путь уменьшения выброса смолистых веществ — использование пека с повышенной температурой размягчения. Не являясь кристаллическим веществом, он не имеет строго определенной температуры плавления и потому переходит из жидкого состояния в твердое не сразу, а постепенно. При уменьшении содержания в составе пека так называемой
или, иными словами, летучих веществ температура его размягчения повышается, а следовательно, выход смолистых веществ в атмосферу сокращается. В настоящее время в России применяется каменноугольный пек по
который подразделяется на четыре марки с различной температурой
|
|
размягчения (°С): А - 65-70; Б - 67-73; Б1 - 72-76 и В -
Наиболее распространенными марками пека при про- изводстве анодной массы для являются Б и Б1, выход летучих веществ у которых составляет соответственно до 62 и менее 59
Поэтому применение пека марки позволяет заметно повысить вязкость массы и снизить выход смолистых веществ в атмосферу. Пек марки В используется при изготов- лении обожженных анодов и имеет выход летучих веществ в пределах
Испытания этого пека при получении анодной массы на НКАЗе показали его перспективность, но потребность полной реконструкции и замены основного техно-
логического оборудования цеха анодной массы не позволили внедрить данный вид сырья.
Дальнейшее повышение температуры размягчения пека, что без особых проблем могут выполнить коксохимики, наталкива- ется на необходимость перевода цехов анодной массы на применение пара давлением до 15 в то время как сейчас
|
|
используют пар давлением до 7 Однако такой путь весьма перспективен и не только с экологической точки зрения, поскольку позволит снизить расход анода и перепад напряжения в нем. Но применение пека с повышенной температурой размягчения
и снижение содержания связующего в анодной массе могут не дать желаемого результата, если не будут соблюдаться основные технологические требования при эксплуатации самообжигающихся анодов. Для того чтобы в полной мере получить экологический эффект от применения пека с ПТР и низким содержанием связующего, необходимо строго следить за своевременной загрузкой анодной массы, не допуская снижения уровня жидкой части анодной массы
в центре анода менее 50 см для электролизеров и 35 см для электролизеров ВТ. Главная цель повышения уровня ЖАМ в центре анода — уменьшение ее температуры, которая не должна
превышать для анодов с БТ и 150 — для анодов с ВТ. Необходимо помнить, что решающее влияние на температуру ЖАМ оказывает минимальное расстояние от конца штыря до подошвы анода — чем это расстояние больше, тем выше температура ЖАМ.
Соблюдение регламентированных приемов обслуживания анодов и поддержание оптимальных параметров являются залогом низкого выброса смолистых соединений в окружающую среду.
Выделение пены. Основные причины образования пены следующие: негомогенность структуры анода, т.е. наличие коксов с различной реакционной способностью, термическое расширение анода и механические воздействия на него (при перестановке штырей и перетяжке анодной Главной из перечисленных причин следует считать разную реакционную способность кокса-наполнителя и кокса из связующего. Однако снизить эту разницу за счет радикального уменьшения темпе- ратуры прокалки кокса-наполнителя очень рискованно, так как наряду со снижением реакционной способности возрастет его
электросопротивление и снизится механическая прочность ано- да. Поэтому на практике не уменьшают температуру прокалки ниже °С. С целью сокращения выхода пены не следует применять смесь коксов с разной температурой прокалки, поскольку их коэффициенты объемного расширения могут быть различны, что приведет к формированию трещин внутри анода и увеличению образования пены. Безусловно недопустимо
использовать предварительно прокаленный кокс без его под- сушки, так как наличие гигроскопической влаги в нем вызовет повышенное образование фтористого водорода.
Различные нарушения технологии анода (шейки, конуса на подошве и которые обусловят местный перегрев анода, обязательно скажутся на увеличении образования пены. Боко- вую поверхность анодов любого типа следует тщательно обере- гать от контакта с воздухом во избежание ее окисления и повышенного
Особенно осторожно надо вы- полнять операции по перестановке штырей и перетяжке анод- ной рамы, поскольку могущие возникнуть перекосы приведут к вмятинам и сколам на аноде.
На практике способность к образованию пены проверяется при анализе анодной массы на в атмосфере углекислого газа [5], в ходе которого выявляются потери массы при ее окислении
и количество осыпавшихся зерен кокса. Выделение пыли. Как было указано ранее, практически все виды сырья, применяемого при электролизе, весьма мел- кодисперсны, что способствует его распылению. В процессе разгрузки и транспортировки сырье распыляется, загрязняя территорию завода, а затем атмосферными осадками смывается
в ливневую канализацию.
Одна часть сырья в виде пыли попадает в систему организо- ванного отсоса газов от электролизеров и затем — при мокрой очистке газов — уходит в отвал или шламовое а при сухом способе очистки газов возвращается в ванну; другая — воздуш- ными потоками общеобменной вентиляции уносится через фонари в окружающую атмосферу.
Количество потерянного сырья зависит от принятой систе- мы обслуживания ванн, состояния укрытий, используемых механизмов, частоты обработки корки, количества анодных эффектов и дисперсности сырья. По данным фирмы
содержание пыли в отходящих газах составляет: для элект- ролизеров —
для ВТ — и для — кг/т Подавляющая часть этих твердых отходов улавливается в
системах газоочистки и возвращается в производство.
Радикально снизить выбросы пыли в систему газо- очистки или окружающую среду можно лишь применением систем регулирования концентрации глинозема при помощи механизмов автоматической подачи глинозема в электролит, которые резко сокращают частоту вмешательства в работу ванны.
Отходы футеровки электролизеров. Количество отходов футе- ровки зависит от многих факторов, но в первую очередь от анодной плотности тока, производительности ванны за межре- монтный период и длительности работы катодного устройства. Как показывают результаты расчетов, масса угольной части изношенной футеровки электролизеров приблизительна равна
55
а масса огнеупорной футеровки — 45
Например, для электролизера С8БМ масса отработанной угольной части поди- ны составляет около 52 т, а огнеупорной — ориентировочно 43 т. Содержание же фтористых соединений в пересчете на фтор в общем объеме отходов будет около 16 т. Расчетами показано, что с увеличением силы тока от 50 до 200 удельный объем
![]() |
футеровки

Решающее влияние на количество образующихся отходов оказывает срок службы катодного устройства — чем он выше, тем меньше отходов.
На заводе производительностью 100 тыс. т/год и при сроке службы катодного устройства 4 года ежегодно образу- ется более 6 тыс. т, в которых содержится более 1000 т фтора. Учитывая, что в обеих фракциях присутствуют раст- воримые в воде фториды и цианиды, футеровка представляет потенциальную экологическую опасность в случае разме- щения ее в отвалах из-за возможности выщелачивания водой фторидов и цианидов. Это — важная проблема для алюминиевой промышленности, и решается она по-разному в странах, про- изводящих алюминий.
5.3. Методика расчета количества изношенной футеровки катода
Футеровка катодного устройства алюминиевых электролизеров состоит из углеродистых (подовые и бортовые блоки), огне- упорных и теплоизоляционных (шамот и материалов.
В процессе пуска и дальнейшей эксплуатации угольная и огнеупорная части футеровки, пропитываясь компонентами электролита, увеличиваются в объеме и создают дополнитель- ные механические усилия на металлический катодный кожух, что в конечном итоге выводит ванну из строя.
Как показали исследования Раппопорта [18], основной фактор, влияющий на разбухание и деформацию углеродистых блоков, — наличие натрия и его соединений в электролите, которые, не вступая в химическое взаимодействие с углеродом, проникают в его промежутки, не нарушая струк- туры углеродных сеток. Данное явление, открытое и впервые изученное М.Б. Раппопортом, и есть основная причина выхода из строя угольной части катодного устройства электролизера.
Результаты исследований [18], в дальнейшем подтвержден- ные
H.A.
[26], показали, что количество погло- щенных углеродом компонентов расплава обратно пропорцио- нально температуре, т.е. их содержание по зонам футеровки не одинаково и составляет от 0,6 до 30,8 % [18]. Согласно исследованиям с сотрудниками
по: в среднем материал изношенной футеровки электролизера со- держит около 30 % углерода, 30 огнеупоров и 40 % солей фторидов (или около 20 % в пересчете на чистый фтор), т.е. конечная масса футеровки ИФЭ
превышает первоначальную
приблизительно в 1,7 раза.
Утилизация изношенной футеровки электролизеров, кото- рая содержит ценные компоненты, — серьезная экологическая проблема для алюминиевой подотрасли. Как правило, ИФЭ частично или полностью направляется в отвал, что может повлечь за собой загрязнение водных источников за счет выщелачивания атмосферной влагой фтористых и иных вредных для окружающей природы соединений. Поэтому разработка методики оценки количества ИФЭ и содержания в ней вредных соединений представляет практический интерес.
[19,
для подовых блоков значение
лежит в пределах
а для бортовых блоков — Действительно, химический состав угольной части содержит всего около 30 % углерода, 26 -
13 - 3NaF
8 -
3 -
Дата добавления: 2022-01-22; просмотров: 21; Мы поможем в написании вашей работы! |
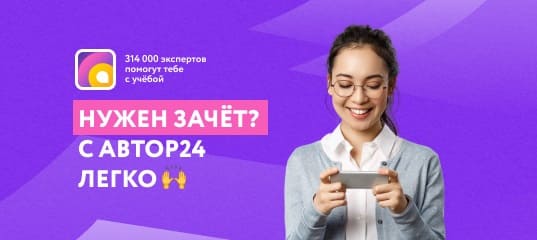
Мы поможем в написании ваших работ!