Анализ загрязнений и перспективных методов очистки выбросов и сбросов литейного производства
Литейное производство является основной заготовительной базой машиностроения и одним из наиболее экологически неблагоприятных. Для него характерны сложность и многообразие способов литья, технологических процессов, применяемых материалов.
В литейном производстве применяется более 100 технологических процессов, более 40 видов связующих, более 200 противопригарных покрытий, это привело к тому, что в воздухе рабочей зоны встречается до 50 вредных веществ, регламентированных санитарными нормами. Так, при производстве 1т чугунных отливок выделяется: 10.30 кг - пыли; 200.300 кг - оксида углерода; 1.2 кг - оксида азота и серы; 0,5.1.5 г - фенола, формальдегида, цианидов и др.; 3 м3 - загрязненных сточных вод может поступить в водный бассейн; 0,7.1,2 т - отработанных смесей в отвал.
Вредные вещества литейного производства, попадая в окружающую среду, представляют угрозу окружающей природе, что сказывается на урожайности сельхозкультур и продуктивности животных. Жидкие стоки представляют опасность для питьевого водоснабжения. Твердые отходы образуют ограниченную номенклатуру (3 категории).
Наличие и количество того или иного вещества в воздухе рабочих зон определяется применяемыми технологическими процессами, исходным материалом и другими факторами.
Выбросы в атмосферу. Пыль и твердые частицы возникают в той или иной степени на каждой стадии технологического процесса и состоят из минеральных оксидов, металлов (главным образом марганца и свинца) и оксидов металлов. Пыль выделяется при термических (например, плавильная печь) и физико-химических технологических процессах - например, формование и производство стержня, а также при механических действиях, таких, как погрузка/разгрузка сырья, в основном песка, а также процессы выбивки отливки и доводки.
|
|
Рекомендуемые меры по предотвращению и снижению неорганизованных выбросов пыли включают следующее:
использование пневматических конвейерных систем, в частности, для транспортировки и подачи присадок на производственный участок;
использование закрытых конвейеров с подавлением пыли в пунктах погрузки/разгрузки, особенно для подачи песка в формовочный цех;
очистку возвратной ленты в системе ленточных конвейеров для удаления сухой грязи;
использование складов для штабелей в помещениях или под крышей, а когда неизбежно открытое хранение, использование системы распыления воды, средств пылеподавления, ветрозащитных приспособлений и других методов штабельного хранения;
использование закрытых бункеров для хранения насыпных порошковых материалов;
проведение регулярного технического обслуживания установки и поддержание чистоты и порядка для сведения к минимуму небольших утечек и разливов.
|
|
В процессе плавления выбросы твердых частиц (ТЧ) в виде пыли, частиц металла и паров оксидов металла меняются в зависимости от типа печи, топлива, расплавляемого металла и характеристик плавки. Вагранки выбрасывают самые значительные количества твердых частиц (например, кокса, летучей золы, кремнезема, ржавчины и известняка). Электродуговые печи (ЭДП) также служат источником значительных количеств ТЧ при загрузке, в начале плавки, во время кислородного дутья и на стадии обезуглероживания. Другие типы плавильных печей обеспечивают более низкие выбросы, особенно индукционные электропечи. Выбросы при загрузке металла для плавки колеблются от незначительных величин для определенных цветных металлов до 10 кг/т и выше при плавке чугуна в вагранке.
Рекомендуются следующие методы, позволяющие предотвращать загрязнение:
Использование, по возможности, индукционных электропечей;
Применение мартеновских печей больше не считается надлежащим методом производства для плавки стали, и его следует избегать;
Необходимо избегать использования традиционной технологии вагранок. При использовании вагранок следует применять усовершенствованные технологии для повышения энергетической эффективности печи и уменьшения загрузки кокса, в том числе:
|
|
использование кислородного дутья или обогащение кислородом воздушного дутья;
перегрев воздуха дутья в вагранках на горячем дутье;
использование бескоксовых вагранок, в которых металлическая шихта нагревается с помощью сжигания природного газа;
использование в плавильных печах технологий, которые позволяют снизить потребление энергии (например, установка кислородо-топливных горелок, создание пенистости шлака в ЭДП или кислородное дутье, если это применимо);
установку вытяжных колпаков для отходящих газов вагранок, кожухов с вытяжными зонтами для электродуговых печей (ЭДП) и вытяжных крышек для электроиндукционных печей с целью снижения неорганизованных выбросов. Установка подходящих систем колпаков для печей обеспечивает улавливание до 98% пыли от печи;
использование технологий борьбы с пылью обычно включает установку рукавных фильтров и циклонов для снижения выбросов пыли в процессе плавки. Для улавливания водорастворимых веществ (таких как диоксид серы (SO2) и хлориды) можно использовать мокрые скрубберы. Использование циклонов для предварительной обработки и применение рукавных фильтров обычно позволяет снижать уровень выбросов до 10 мг/Нм3 и ниже.
|
|
Использование большого количества песка при литье в кокиль приводит к потерям и выбросам пыли на разных стадиях литья, способствуя образованию неметаллических твердых частиц, частиц оксидов металлов и металлического железа. Неметаллические твердые частицы выбрасываются при литье, выбивке и доводке.
Рекомендуются следующие методы предотвращения и контроля выброса твердых частиц при литье и отливке в кокиль:
использование сухой технологии пылеудаления (например, рукавные фильтры и циклоны) вместо мокрых скрубберов, особенно на предприятии приготовления сырой формовочной смеси. Сухие методики дают возможность легко удалять пыль, транспортировать ее и снова направлять в процесс приготовления формовочной смеси, что позволяет избежать стоков от мокрых скрубберов;
использование фильтров на выбросе вытяжки, особенно в литейных цехах и цехах доводки;
использование вакуумного пылеудаления в формовочном и литейном цехах;
установка агрегатов пылеудаления с замкнутым циклом на производственных участках.
Оксиды азота. Выброс оксидов азота (NOX) вызван высокой температурой печи и окислением азота.
Снижения выбросов можно добиться путем изменения основного технологического процесса и вторичной технологии очистки в месте выброса.
Методы предотвращения и контроля загрязнения включают в себя следующее:
минимизацию соотношения " воздух / топливо" в процессе сжигания;
использование обогащения кислородом в процессе сжигания;
использование, по возможности, горелок с низким выходом NOX в топливосжигающих печах;
введение вторичного контроля (в основном для вагранок, ЭДП и вращающихся печей), при необходимости, с помощью устройств для каталитического сжигания.
Оксиды серы. Присутствие оксидов серы (SOX) в отходящих газах из плавильных печей зависит от содержания серы в топливе и технологическом коксе. Выбросы диоксида серы (SO2) происходят в газах, отходящих от вагранок и вращающихся печей. К другим источникам выбросов относятся процессы закалки газовым пламенем при производстве форм истержней с химически связанным песком и при плавке магния (Mg).
Рекомендуемые методы предотвращения загрязнения и борьбы с ним для снижения выбросов SO2 включают следующее:
выбор сырья и металлолома с низким содержанием серы;
использование топлива с низким содержанием серы, например природного газа;
установку газовых мокрых скрубберов перед сухими скрубберами в рамках специализированной системы сбора пыли и пылеудаления.
Монооксид углерода. Наиболее значительным источником монооксида углерода (CO) служат отходящие газы от вагранок и ЭДП. Присутствие CO в отходящих газах из вагранок определяется самим ваграночным процессом. В ЭДП CO образуется в результате окисления графитовых электродов и углерода из металлической ванны на стадии плавки и рафинирования. Монооксид углерода также выбрасывается, когда песчаные формы и стержни входят в контакт с расплавом металла в процессе разливки металла.
Рекомендуемые методы предотвращения загрязнения и борьбы с ним для снижения выбросов CO включают следующее:
использование электроиндукционных печей;
повышение тепловой эффективности технологического процесса (например, введение кислородного дутья или кислородотопливных горелок в вагранках);
использование в ЭДП технологии вспененного шлака;
использование камер дожигания в установках пылеудаления из отходящих газов вагранок и ЭДП;
герметизацию линий разливки металла с установкой приданных вытяжных вентиляторов.
Хлориды и фториды присутствуют в малых количествах в отходящих газах из плавильных печей и образуются из флюса. Предотвращение и снижение выбросов хлоридов и фторидов следует проводить на стадии сухого пылеудаления или в процессе использования технологии мокрых скрубберов, устанавливаемых для борьбы с выбросами твердых частиц и оксида серы.
Летучие органические вещества (ЛОС) и другие опасные вещества, загрязняющие атмосферу. Выбросы ЛОС, состоящие в основном из растворителей (например, BTEX - бензол, толуол, этилбензол и ксилолы) и других органических веществ (например, фенолы и формальдегид) в первую очередь образуются при использовании смол, органических растворителей или покрытий на органической основе при изготовлении форм и стержней. Выбросы вредных органических веществ, загрязняющих воздух, могут также происходить при разливке, охлаждении и выбивке из сырых или самоотверждающихся литейных форм в результате термического разложения органических веществ (углеродсодержащих присадок, присутствующих в сырых литейных формах и различных связующих для стержней).
При изготовлении стержней в холодных ящиках с использованием органических растворителей выбросы ЛОС могут осуществляться в процессе производства и хранения стержней. Самую значительную часть выбросов составляют амины, которые могут представлять опасность в связи с их низким порогом обнаружения запаха и одновременно относительно низким пределом допустимого воздействия.
Выбросы потенциально вредных загрязнителей атмосферы происходят при использовании систем химических связующих в процессе затвердевания, нанесения покрытия и сушки. К таким веществам относятся формальдегид, метилендифенил диизоцианат (MDI), изопропиловый спирт, фенол, амины (например, триэтиламин), метанол, бензол, толуол, крезол и крезоловая кислота, нафталин и другие полициклические органические соединения, а также цианиды.
Рекомендуемые методы предотвращения и снижения загрязнения ЛОС и другими опасными загрязнителями атмосферы включают в себя следующее:
сведение к минимуму использования связующих и смол за счет оптимизации управления технологическим процессом и применения материалов в операциях смешивания и за счет регулирования температуры;
оптимизацию регулирования температуры при производстве стержней;
замену покрытий на основе спирта (например, изопропилового спирта) покрытиями на водной основе;
использование неароматических растворителей (например, метиловых эфиров растительных масел или силикатных эфиров) при производстве стержней в ящике;
сведение к минимуму использования отверждающих газов для получаемых в холодном ящике связующих;
герметизацию формовочных машин и машин для производства стержней, а также участков временного хранения стержней;
использование систем холодного ящика (например, поглощение на активированном угле, сжигание, химическая очистка в скруббере или биологическое фильтрование) для переработки отходящих аминов;
использование систем сбора (например, вытяжных зонтов) для удаления ЛОС, образующихся при приготовлении химически связанного песка, в дополнение к разливке, охлаждению и выбивке.
Использование, по мере необходимости, поглощения на активированном угле, каталитического окисления и обработки с помощью биологического фильтрования.
Диоксины и фураны. Выбросы полихлорированных дибензодиоксинов и дибензофуранов (диоксины и фураны, или ПХДД/ПХДФ) могут происходить в процессе плавки. При литье черных металлов диоксины могут образовываться в вагранках, ЭДП и вращающихся печах. ПХДД/ПХДФ могут возникать, когда в металлургическом процессе при определенном уровне температуры одновременно присутствуют хлоридные ионы, хлорированные соединения, органический углерод, катализаторы, кислород. Риск образования диоксинов при литье цветных металлов очень невелик.
Основные методы предотвращения выбросов диоксинов на стадии плавки сводятся к дожиганию отходящих печных газов при температуре около 1200°C и обеспечению максимального времени удерживания при этой температуре. Процесс заканчивается быстрым охлаждением, чтобы свести к минимуму время для вторичного образования диоксинов в соответствующем температурном диапазоне.
К другим рекомендуемым мерам относятся следующие:
использование для плавки чистого металлолома;
добавление порошковых присадок (например, активированного угля) в поток газа для поглощения диоксинов и удаление пыли с помощью фильтрования через тканевые фильтры;
установка тканевых фильтров с системой каталитического окисления.
Выбросы металлов следует держать под контролем в процессах плавки и литья. Выбросы металлов могут возникать в результате испарения и конденсации металла во время разливки расплава металла в формы. При литье черных металлов частицы могут содержать тяжелые металлы, такие как цинк (в основном при использовании оцинкованного стального лома), кадмий, свинец (например, из окрашенного металлолома), никель и хром (последние два металла выделяются при разливке легированных сталей) в зависимости от производимой марки стали и используемого металлолома.
При производстве цветных металлов твердые частицы могут содержать медь, алюминий, свинец, олово и цинк. Присутствие металлов в выбросах твердых частиц оказывается особенно существенным при получении сплавов и при введении присадок. Например, добавление магния к расплаву металла для получения ковкого чугуна может приводить к химической реакции с выделением оксида магния и паров металла.
Для борьбы с выбросами твердых частиц металла следует использовать высокоэффективные методы удаления пыли. С выбросами газообразных металлов следует бороться с помощью установки сухих и полусухих скрубберов в сочетании с методами удаления пыли.
Парниковые газы (ПГ). Процесс литья требует больших затрат энергии и приводит к существенным выбросам диоксида углерода (CO2), связанным в первую очередь со сжиганием топлива.
Основная доля энергии расходуется на процесс плавки (40-60% от общей расходуемой энергии). Подача энергии для литья колеблется в пределах от 500 до 1200 кВт·ч/т загрузки металла для черных металлов и от 400 до 1200 кВт·ч/т загрузки алюминия.
Рекомендуемые методы предотвращения выбросов диоксида углерода (CO2) и борьбы с ними включают следующее:
замена традиционных вагранок электроиндукционными, бескоксовыми вагранками или вагранками с кислородным дутьем. Использование среднечастотной мощности в электроиндукционных печах;
ограничение потребления энергии и увеличение энергетической эффективности с помощью первичных мер, включая приведенные ниже, но не ограничиваясь ими:
достаточной теплоизоляции поверхности для ограничения рассеяния тепла;
достижения надлежащего соотношения "воздух / топливо" со снижением избытка O2;
установки систем рекуперации тепла;
использования тепла отходящих газов с помощью подходящих теплообменников для производства горячей воды, горячего воздуха и/или пара;
использование наилучшей имеющейся технологии сжигания (например, обогащение кислородом воздушного дутья, предварительный подогрев загрузки и автоматическое регулирование параметров сжигания);
осуществление требуемого регламента эксплуатации и технического обслуживания оборудования и исключение частичной загрузки оборудования;
подогрев металлолома перед его использованием;
снижение расхода топлива на подогрев ковша и термическую обработку расплава металла с помощью введения рекуперации газа и/или регулирования сжигания;
выбор топлива с низким отношением содержания углерода к теплотворной способности (например, природного газа [CH4]). Выбросы CO2 при сжигании CH4 приблизительно на 60% меньше, чем выбросы из каменного угля или нефтяного кокса;
дополнительные данные о борьбе с парниковыми газами обсуждаются в Общем руководстве по ОСЗТ.
К твердым отходам относятся отработанный песок, шлак от сероочистки и плавки, пыль, собранная в системах снижения токсичности выбросов, отходы огнеупоров, а также жидкость и отстой из скрубберов.
Общие методы обращения с отходами, возникающими в литейном производстве, включают в себя выбор, проектирование и строительство участков хранения металла, пыли, получаемой при очистке фильтров, отходов огнеупоров, шлака и отработанного песка с должным учетом геологических и гидрогеологических условий, чтобы избежать возможного загрязнения за счет выноса тяжелых металлов. Места погрузки/разгрузки и участки хранения реактивов (например, смол и связующих) должны быть спроектированы так, чтобы сводить к минимуму риск их разлива.
Отработанный песок с литейного производства, в котором используют песчаные формы, составляет существенную часть совокупного объема отходов. Песок для форм и стержней составляет от 65 до 80% от общего количества отходов литейного производства черных металлов. Химически связанный песок для получения стержней или оболочковых форм трудно эффективно использовать вторично, и его обычно направляют в отходы после первого использования. Отходы песка при литье латуни и бронзы часто бывают опасными, и удалять их необходимо соответственным образом.
Рекомендуемые методы предотвращения загрязнения отходами песка и борьбы с ним включают следующее:
максимальное вторичное использование песка на предприятии;
следует рассмотреть возможность внешнего вторичного использования отработанного песка (например, в качестве материала для бетона и дорожного покрытия и для производства кирпича, бетонной отсыпки и строительной засыпки);
сырую формовочную смесь следует вторично использовать после отделения ее от металлической отливки и регенерации.
Метод регенерации песка состоит из первичной, например, с помощью вибрации, ротационного барабана и дробеструйной обработки и вторичной регенерации, например, переработка песка для удаления остаточного связующего, а также холодная механическая и термическая обработка либо обработка в мокром скруббере. Для восстановления химически связанного песка используют установки термической обработки.
Пыль из очистного оборудования (для борьбы с выбросами) может содержать цинк, свинец, никель, кадмий, медь, алюминий, олово, хром и другие металлы, и ее можно считать опасными отходами. Пыль из оборудования для борьбы с выбросами в литейном производстве цветных металлов часто содержит достаточно большие количества металлов, поэтому выделение этих металлов является экономически выгодным. Пыль из фильтров следует в максимально возможной степени направлять обратно в печь. Это позволяет с помощью вторичной переработки пыли выделять металлы и сводит к минимуму размещение пыли на полигонах.
Отходы шлака обычно имеют сложный химический состав и содержат разнообразные загрязняющие вещества из металлолома. Они могут составлять около 25% массы твердых отходов с литейного производства. К обычным составляющим шлака относятся оксиды металлов, расплавленные огнеупоры, песок и зола кокса (при использовании кокса). Для облегчения выемки шлака из печи могут добавляться флюсы. Шлак может быть опасным, если он содержит свинец, кадмий или хром из расплава стали или цветных металлов.
Рекомендуемые методы предотвращения загрязнения отходами шлака и борьбы с ним включают следующее:
необходимо сводить к минимуму производство шлака с помощью следующих мер по оптимизации технологического процесса:
сортировка металлолома повышает качество металла и снижает возможность образования и выброса загрязненного шлака. Металлолом электронного оборудования, окрашенный металлолом и металлолом отработавших свой срок автомобилей может оказаться источником загрязнения, и его следует тщательно осматривать и сортировать;
снижение температуры плавки металла;
оптимизация использования флюсов и огнеупорного покрытия;
необходимо вторично использовать шлак и извлекать из него ценные металлы. К вариантам вторичного применения могут, в зависимости от характеристик шлака, относиться: производство блоков, использование в качестве материала дорожного основания и крупного заполнителя.
Шлам от очистки сточных вод может содержать тяжелые металлы (например, хром, свинец, цинк и никель), а также нефтесмазочные материалы. Небольшую часть шлама от очистки сточных вод можно вторично использовать внутри предприятия, однако большую его часть направляют для захоронения на полигонах. Из него могут в существенных количествах выноситься металлы, и это необходимо учитывать при разработке варианта вторичного использования, а также при принятии решений в отношении применяемых изоляционных покрытий для полигонов и профилактических мероприятий по предотвращению выноса опасных веществ. Для вторичного использования шлама может потребоваться его предварительная обработка, которая обычно состоит в прессовании, сушке и гранулировании.
Технологические сточные воды. Самые большие количества воды используются в литейном производстве в системах охлаждения электрических печей (индукционных и дуговых), вагранок и в мокрых системах пылеудаления. На большинстве литейных предприятий мероприятия по рациональному использованию воды предусматривают ее повторное использование, что приводит к минимальному объему стоков.
Применение мокрых методов пылеудаления может увеличить использование воды и создать соответствующие проблемы при ее последующей очистке и удалении. При производстве стержней промывные растворы, сбрасываемые от холодных и горячих стержневых ящиков, содержат биологически разлагающиеся амины и фенолы. В процессе литья под давлением возникает поток сточных вод, требующий переработки для удаления органических веществ (например, фенола, масел) перед его сбросом.
Если форму охлаждают водой, могут образовываться сточные воды с содержанием металлов и взвешенных твердых частиц. Сточные воды с взвешенными и растворенными твердыми частицами и низким рН образуются также при использовании растворимых соляных стержней.
Сточные воды могут возникать при определенных операциях доводки, таких как закалка и зачистка, и они могут содержать в больших количествах масел и взвешенные твердые частицы.
Рекомендуемые методы предотвращения загрязнения стоками с литейных производств включают в себя следующее:
установку замкнутых контуров для охлаждающей воды, чтобы снизить потребление и сброс воды;
вторичное использование галтовочной жидкости с помощью удаления из неё взвешенных веществ осаждением либо центрифугированием с последующим фильтрованием;
хранение металлолома и других материалов (например, угля и кокса) на закрытых и/или защищенных от утечек площадках, чтобы ограничить загрязнение ливневых стоков и облегчить сбор дренажных стоков.
Методы очистки сточных вод с промышленных технологических процессов в этой отрасли включают раздельный сбор в зависимости от источников их образования и предварительную очистку потоков сточных вод для снижения содержания в них тяжелых металлов с помощью химического осаждения, коагуляции с флокуляцией и т.п.
К типичным методам очистки сточных вод относятся: нефтеловушки; устройства сбора с поверхности или отделения нефтепродуктов и всплывающих взвешенных твердых веществ; фильтрование для отделения фильтруемой фракции взвешенных твердых веществ; усреднение стоков по объему и составу; осаждение для снижения содержания взвешенных твердых частиц при использовании осветлителей; обезвоживание и размещение отходов очистки на специальных полигонах, предназначенных для захоронения опасных отходов.
Могут потребоваться дополнительные меры для дополнительного удаления металлов с помощью фильтрования через мембрану или с помощью других физико-химических методов очистки, удаления стойких органических веществ с помощью активированного угля или интенсивного химического окисления, удаления химических или биогенных веществ с целью снижения содержания азота и для снижения токсичности стоков с помощью надлежащей технологии (например, обратного осмоса, ионного обмена, активированного угля и т.п.).
Использование этих и других технологий и передовых практических методов обращения со сточными водами позволит предприятиям обеспечить соответствие сбросов сточных вод нормативным показателям, приведенным для данной отрасли промышленности в таблицах 1 и 2.
Загрязненные потоки необходимо направлять в систему очистки технологических сточных вод.
Ливневые стоки с участков открытого хранения угля могут быть загрязнены сильнокислотным фильтратом, содержащим полициклические ароматические углеводороды (ПАУ) и тяжелые металлы. Специальные рекомендации для отрасли включают следующее:
мощение технологических участков, разделение загрязненных и незагрязненных ливневых стоков, а также реализацию плана борьбы с разливами. Направление ливневых стоков с технологических участков в установку очистки сточных вод;
проектирование систем сбора фильтрата и расположения площадок для хранения угля так, чтобы предотвратить их воздействие на почву и водные ресурсы. Участки хранения угля в штабеле должны быть замощены, чтобы отделить ливневые стоки, которые могут быть загрязнены, и направить их для предварительной очистки и очистки в установке для очистки сточных вод.
В таблицах 1 и 2 приведены нормативы выбросов и сбросов в данной отрасли. Рекомендованные нормативы технологических выбросов и сбросов в данной отрасли соответствуют надлежащей международной отраслевой практике, которая зафиксирована в соответствующих стандартах стран с общепризнанной нормативно-правовой базой.
Таблица 1 - Уровни сбросов литейного производства
Загрязняющее вещество | Единицы | Нормативное значение |
pH | - | 6-9 |
Общее содержание взвешенных твердых частиц | мг/л | 35 |
Нефтепродукты | мг/л | 10 |
Повышение температуры | °С | 3a |
Химическое потребление кислорода | мг/л | 125 |
Фенол | мг/л | 1 |
Кадмий | мг/л | 0,01 |
Хром (общее содержание) | мг/л | 0,5 |
Медь | мг/л | 0,5 |
Свинец | мг/л | 0,2 |
Никель | мг/л | 0,5 |
Цинк | мг/л | 0,5 |
Олово | мг/л | 2 |
Аммиак | мг/л (в пересчете на N) | 5 |
Фториды | мг/л (в пересчете на F) | 5 |
Железо | мг/л | 5 |
Алюминий | кг/т | 0,02b |
Примечание.
a. На границе научно установленной зоны смешивания с учетом качества воды водных объектов, типа водопользования водоприёмника, возможных потребителей воды и ассимилирующей способности.
b. Выплавка и разливка алюминия.
Таблица 2 - Уровни атмосферных выбросов литейного производства
Загрязняющее вещество | Единицы | Нормативное значение |
Твердые частицы | мг/Нм3 | 20 (2) 50 (3) |
Масляный аэрозоль и туман | мг/Нм3 | 5 |
NOx | мг/Нм3 | 400 (4) 120 (5) 150 (6) |
SO2 | мг/Нм3 | 400 (8) 50 (9) 120 (7) |
ЛОС | мг/Нм3 | 20 (10) 30 150 (11) |
Полихлорированный и полифтори-рованный дибензодиоксин | нг токсического эквивалента/Нм3 | 0,1 |
CO | мг/Нм3 | 200 (12) 150 (13) |
Амины | мг/Нм3 | 5 (14) |
Хлор | мг/Нм3 | 5 (15) |
Pb, Cd и их соединения | мг/Нм3 | 1-2 (16) |
Ni, Co, Cr, Sn и их соединения | мг/Нм3 | 5 |
Cu и её соединения | мг/Нм3 | 5-20 (17) |
Хлориды | мг/Нм3 | 5 (18) |
Фториды | мг/Нм3 | 5 (19) |
H2S | млн-1 об. /об. | 5 |
Примечание.
1. Исходные условия для пределов. Для газов сгорания: сухие, температура 273 K (0°C), давление 101,3 кПа (1 атм.), содержание кислорода 3% по сухому весу для жидких и газообразных топлив, 6% по сухому весу для твердых топлив. Для других газов: без поправки на пары воды и содержание кислорода, температура 273 K (0°C), давление 101,3 кПа (1 атм.).
. Выбросы твердых частиц при наличии токсичных металлов.
. Выбросы твердых частиц в отсутствие токсичных металлов.
. Плавка черных металлов. Максимальное содержание в выбросах для наилучшей разработанной технологии для бескоксовых вагранок.
. Плавка цветных металлов (шахтные печи).
. Из системы термического восстановления песка и с установок регенерации.
. Максимальное содержание в выбросах для наилучшей разработанной технологии для вагранок на холодном дутье.
. Плавка цветных металлов (шахтные печи)
. Плавка черных металлов (вагранки)
. Плавка цветных металлов (шахтные печи).
. Плавка черных металлов (ЭДП). Для вагранок уровень выбросов может быть выше (до 1 000 мг/Нм3).
. Плавка цветных металлов (шахтные печи).
. Цех производства форм и стержней в холодном ящике.
. Плавка цветных металлов (алюминий).
. Системы термического восстановления песка и операции с растворителями для нанесения, скалывания и крепления огнеупорной смеси для выплавляемых моделей.
. Для литья цветных металлов из лома действуют более высокие значения.
. Для процесса производства меди и ее сплавов действуют более высокие значения.
. Выбросы из печей, в которых используют хлоридный флюс.
. Выбросы из печей, в которых используют фторидный флюс.
Итак, проблему охраны окружающей среды в литейном производстве необходимо решать комплексно: разрабатывать и использовать в производстве малотоксичные материалы, создать на всех участках цеха устройства по реализации и обезвреживанию газовыделений, эффективнее использовать материальные и топливно-энергетические ресурсы путем регенерации и утилизации отходов, не утилизируемые отходы складировать в отвалах, с наименьшим ущербом для окружающей среды.
Для предупреждения выделения вредностей, их локализации и обезвреживания, утилизации отходов применяется комплекс природоохранных мероприятий, включающий использование:
для очистки от пыли - искрогасителей, мокрых пылеуловителей, электростатических пылеуловителей, скрубберов (вагранки), тканевых фильтров (вагранки, дуговые и индукционные печи), щебёночных коллекторов (дуговые и индукционные электропечи);
для дожигания ваграночных газов - рекуператоры, системы очистки газов, установки низкотемпературного окисления СО;
для уменьшения выделения вредностей формовочных и стержневых смесей - снижение расхода связующего, окисляющие, связующие и адсорбирующие добавки;
для обеззараживания отвалов - устройство полигонов, биологическая рекультивация, покрытие изоляционным слоем, закрепление грунтов и т.д.;
для очистки сточных вод - механические, физико-химические и биологические методы очистки.
Список используемой литературы
1. Болдин, А.Н. Литейное производство с точки зрения экологии / А.Н. Болдин // Литейное производство. - 2005. - №3. - С.33-34.
2. Горкин, А.П. География. Современная иллюстрированная энциклопедия / А.П. Горкина. - М.: Росмэн-Пресс, 2006. - 624 с.
3. Инженерная экология: метод. указания к выполнению контрольной работы / сост. Л.А. Герасимова. - Красноярск: Сиб. гос. аэрокосмич. ун-т., 2006. - 50 с.
4. Николайкин, Н.И. Экология / Н.И. Николайкин, Н.Е. Николайкина, О.П. Мелехова. - М.: Дрофа, 2004. - 624 с.
. Орехова, А.И. Экологические проблемы литейного производства / А.И. Орехова // "Экология производства". - 2005. - №1. - С.2-3.
. Экология и безопасность жизнедеятельности: Учеб. пособие для вузов / Д.А. Кривошеин, Л.А. Муравей, Н.Н. Роева и др.; Под ред. Л.А. Муравья. - М.: ЮНИТИ-ДАНА, 2000. - 447 с.
. Экология литейного производства / под ред.А.Н. Болдина, С.С. Жуковского, А.Н.Поддубного и др. - Брянск: БГТУ, 2001. - 315 с.
Дата добавления: 2020-12-12; просмотров: 177; Мы поможем в написании вашей работы! |
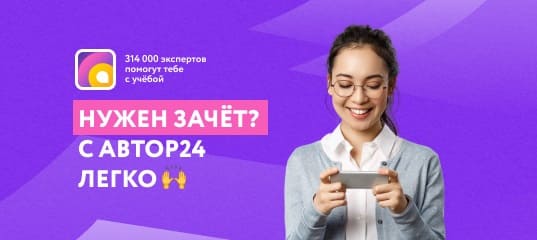
Мы поможем в написании ваших работ!