Системы контроля и управления, аппаратное и программное обеспечение
Http://de.dstu.edu.ru/CDOCourses/27.11.2015open/632/333/book.htm8.2 Измерение параметров режима управления при дуговой и контактной сварке
Использование большинства серийно выпускаемых датчиков и мерительных преобразователей для измерения параметров режима дуговой и контактной сварки затруднено. Это связано прежде его с наличием интенсивных электромагнитных помех, создаваемых сварочным оборудованием, которые вносят искажения в измеряемые сигналы.
Для измерения параметров режима дуговой и контактной сварки используются специально разработанные измерительные преобразователи (ИП).
В частности, ИП для контактных точечных машин типа МТВ-8001 и МТК-75 осуществляют измерение следующих параметров:
· сварочного тока от 10 до 100 кА;
· сварочного усилия сжатия от 1500 до 15000 кН;
· ковочного усилия сжатия от 5000 до 35000 кН;
· интегрального значения напряжения между электродами сварочной машины от 0,5 до 5 В;
· интегрального значения сварочного тока от 10 до 100 кА.
Последние два параметра используются в АСУ ТП для контроля качества сварного соединения. Погрешность измерения электрических параметров режима не более 2,5 %, а усилий сжатия – 5 %. Сигнал напряжения между электродами разделяется и интегрируется в ИП в течение времени, когда мгновенное значение тока сварки больше заданного порогового. Тем самым, с одной стороны, удается компенсировать помеху на измерительную цепь Uээ, которая может по амплитуде в десятки раз превышать информационный сигнал, а с другой, – выбрав соответствующим образом пороговые напряжения, исключить импульс после сварочного нагрева деталей, который не определяет размер сварной точки.
|
|
Для измерения усилия сжатия используют тензорезисторный датчик, встроенный в привод сжатия. Сварочный ток контролируют с помощью датчика производной тока по времени (пояса Роговского) и определяют в ИП как максимум интегрального значения сигнала с датчика тока.
Измеренные таким образом параметры процесса сварки в ИП запоминаются на время не менее 40 мс после окончания сварочного тока для их опроса ЭВМ. Временные параметры режима определяются ЭВМ с дискретностью 20 мс по стробу, который выдается ИП в течение сварочного тока, и сигналу ковки.
Для настройки, метрологической аттестации и периодической поверки ИП использовать универсальные измерительные приборы сложно. Учитывая возможности ЭВМ, эти работы со значительно меньшими затратами времени могут быть выполнены с помощью технических средств системы управления. При этом тестовый сигнал на вход ИП задают с помощью цифроаналогового преобразователя (ЦАП) и согласователя уровней напряжения, а выходной сигнал измеряется аналого-цифровым преобразователем (АЦП).
|
|
Согласователь используется для преобразования уровней сигналов с выходов ЦАП в диапазоны входных сигналов измерительных каналов: до 3 В по каналу тока сварки, 1 В по каналу напряжения между электродами и 20 мВ по каналу сварочного усилия сжатия.
В соответствии с диапазоном измеряемых параметров задаются в режиме диалога параметры тестовых сигналов: по каналу тока и напряжения (рис. 8.2) - минимальное и максимальное значения напряжения (U2) и длительности импульса (T2), а по каналу усилия сжатия – (U1и U3). Кроме того, указывается число точек испытания в заданном диапазоне m (обычно 5), число повторений испытаний в каждой точке n (30), а также период Т,с которым заданные m´n испытания должны повторяться.
Рис. 8.2. Тестовый сигнал на входе измерительного преобразователя параметров режима для контактной точечной сварки
Система последовательно во времени задает серию из n испытываемых сигналов со следующими параметрами:
где i = l, 3; j = 1, n.
Время моделирования сварочного усилия сжатия не влияет на работу ИП и равно 0,2 с. Аналогично время после сварочного сжатия T3выбрано равным 40 мс для всех испытаний. При этом через 20 мс после окончания импульса на входе каналов измерения тока и напряжения с помощью АЦП осуществляется опрос измеренных значений на выходе ИП. Заданная серия проверяется m раз. После чего по накопленным данным методом наименьших квадратов рассчитывается статическая характеристика преобразования ИП (СХП) в виде линейной зависимости где – напряжение па выходе ИП; xi – заданные тестовые сигналы; `x – среднее значение тестового сигнала; а, b – коэффициенты, полученные расчетом по МНК.
|
|
Доверительные границы погрешности СХП вычисляются по формуле
,
где – среднеквадратическое отклонение у; N = n´m – число испытаний; tN-2, g – квантиль распределения погрешности измерения для уровня значимости g.
Для оценки погрешности измерительного канала определяют среднеквадратические отклонения случайной погрешности yij в точках испытания:
,
а также среднеквадратическое отклонение нелинейности СХП
.
При постоянном значении погрешности ИП в различных точках испытания , заданную погрешность ИП (%) проверяют по зависимости e=Di×100/(Yконx), где Yкон – конечное значение измеряемой величины в заданном диапазоне; x=0,8 – технологический запас.
|
|
Обычно при периодической поверке ИП сравнивают построенную СХП с номинальной, вычисляя дисперсное отношение
V2=(m– 2)(Q2 – Q1)/(2Q1),
где – для построения СХП;
– для номинальной СХП.
Если V2 больше квантили распределения Фишера для уровня значимости g = 0,05, то поверяемому каналу должна приписываться построенная СХП.
В АСУ ТП при периодической поверке независимо от оценок дисперсного отношения ИП приписывают рассчитанную СХП.
Тем самым удается непрерывно контролировать техническое состояние измерительного преобразователя и поддерживать заданный уровень точности измерения. При этом на испытание одного ИП затрачивается время не более 5 мин. Аналогичные программно-технические средства используются для метрологической аттестации и поверки ИП параметров режима дуговой сварки, который предназначен для измерения:
· среднего сварочного тока в диапазоне 30-300 А и 60-600 А;
· среднего напряжения на дуге в диапазоне 8-30 В; средней скорости сварки в диапазоне 10-100 м/ч; средней скорости подачи присадочной проволоки 10-120 м/ч.
Учитывая степень влияния параметров режима сварки на качество сварного шва, электрические параметры режима контролируют с погрешностью не более 2,5%, а скорости – не более 5%. Принимая во внимание форму измеряемых сигналов, для каналов измерения тока и напряжения тестовый сигнал с ЭВМ задается напряжением в виде синусоиды с частотой 50 Гц и постоянным напряжением. Каналы измерения скорости проверяют только на тестовом сигнале постоянного тока. Значение синусоидального сигнала задают по амплитуде, а постоянного сигнала – по уровню. Напряжение на выходе ИП, учитывая динамические характеристики блока, измеряются через 1 с после передачи тестового сигнала. Расчеты СХП и погрешности измерения осуществляются так же, как и для ИП контактной сварки. Кроме того, для ИП дуговой сварки ЭВМ контролирует время установления измеренного значения при скачкообразном изменении тестового сигнала. Время определяется с дискретностью 20 мс по таймеру, встроенному в микропроцессор.
Кроме автоматизации метрологической аттестации ИП, их периодической поверки в составе АСУ ТП и уточнения СХП измерительных каналов с целью повышения точности контроля система может использоваться для наладки ИП. В этом случае в режиме проверки работы ИП на тестовом сигнале с постоянными параметрами осуществляется предварительная отладка и настройка измерительных каналов в характерных точках диапазона измерения. Далее настройка ИП осуществляется по СХП и погрешности преобразования, выводимой на экран дисплея. Тем самым в десятки раз удается повысить производительность труда при изготовлении и ремонте измерительного преобразователя.
Системы контроля и управления, аппаратное и программное обеспечение
Для разработки системы группового контроля и управления контактной и дуговой сваркой отечественной промышленностью выпускается комплекс технических средств, основанных на использовании различных типов мини- и микроЭВМ. Разрабатываются системы АСУ ТП контактной и дуговой сварки на основе современных ЭВМ. Следует заметить, что при практически одинаковых технических характеристиках ЭВМ предпочтение следует отдавать той машине, показатели надежности которой выше.
В качестве примера рассмотрим АСУ ТП контактной и дуговой сварки на основе управляющего вычислительного комплекса. Система состоит (рис.8.3) из процессора Ml, оперативно запоминающего устройства ПЗ, накопителя на магнитных дисках НГМД, подключенного к общей шине через плату сопряжения И4 с принтером через плату сопряжения И7, дисплея с клавиатурой, который связан с общей шиной через устройство последовательного обмена информацией УПО. Для ввода данных о параметрах режима используется 32-канальный аналого-цифровой преобразователь АЦП, устройства комбинированного быстродействующего блока УКБ, подключенного через согласователь к общей шине СОШ. Аналоговые датчики Д параметров режима через измерительный преобразователь ИП соединены с входами АЦП, а выходы модуля дискретных датчиков МВДИ технического состояния сварочного оборудования подаются на вход модуля ввода дискретной информации МВвДИ.
Рис. 8.3. Структурная схема АСУ ТП контактной и дуговой сварки
Измерительные преобразователи ИП осуществляют преобразования сигналов датчика к стандартным уровням (0+10 В). Кроме того, в них осуществляется первичная обработка измеренных сигналов (например, усреднение при дуговой сварке или интегрирование и выборки максимального значения тока, запоминание измеренных значений на время опроса при контактной сварке), а также подавление помех в измерительных цепях. Для периодической проверки ИП на его вход заводится выход цифроаналогового преобразователя ЦАП, входящего в состав УКБ. К АЦП подключены датчики напряжения и давления воздуха (для контактной сварки) или газа (для дуговой сварки) к магистралям питания сварочных установок (СМ1 – СМ3) электроэнергией и воздухом (защитным газом). Вывод информации о параметрах режима и данных о ходе технологического процесса выдается на сигнальные табло СТ, установленные на рабочем месте сварщика, через МВДИ и блок гальванического разделения и усиления сигналов БГР. Для связи с локальными системами управления (ЛСУ), а также АСУ ТП верхнего уровня зарезервировано второе устройство последовательного обмена. Состав математического обеспечения АСУ ТП дан на рис.8.4.
Рис. 8.4. Состав программного обеспечения АСУ ТП контактной и дуговой сварки
Программа «диспетчер» в основном осуществляет связь оператора с системой путем вызова в работу в режиме диалога требуемых модулей. Кроме того, независимо от оператора системы регулярно включаются в работу модули, контролирующие техническое состояние сварочной машины, а также на дисплей выводится оперативная информация о ходе процесса. При этом модуль контроля технического состояния сварочных машин и прогнозирование неисправностей включается с заранее заданным периодом времени Т, обычно Т равно 30 мин. Это связано с тем, что износ оборудования можно рассматривать как монотонный и медленно протекающий процесс.
Управляющая программа включает в работу модули, которые непосредственно осуществляют контроль и управление процессом сварки в реальном масштабе времени. Эти модули имеют высший приоритет. Поэтому диспетчер АСУ и модули, которые он непосредственно включает в работу, при запуске управляющей программы выполняются как фоновые задачи в режиме прерывания. Управляющая программа включается в работу в режиме прерывания от таймера с интервалом 20 мс. Синхронизация управляющей программы с напряжением сети диктуется особенностями задания циклограммы режима.
Управляющая программа после запуска в работу сигналом прерывания определяет, на каком участке циклограммы (фазы) находится сварочная установка. В соответствии со сварочным циклом для автоматов аргонодуговой сварки имеются фазы: продувки газа, включения осциллятора, нарастания тока до режима сварки, заварки кратера, выключения газа и паузы, а для контактной сварки – предварительного сжатия, сварки, проковки и паузы. В зависимости от фазы, в которой находится сварочная установка, управляющая программа включает в работу тот или иной модуль. Перед сваркой для соответствующей дуговой сварочной установки осуществляется отключение всех измерительных, сигнальных и управляющих цепей для защиты от помех, вызванных работой осциллятора. При контактной сварке анализируется возможность включения тока с целью оптимального распределения нагрузки электрической сети. В фазе сварки управляющая программа включает модули измерения параметров режима, а для дуговой сварки в этом случае включаются с заданным периодом, например 1 с, также модули контроля качества сварного шва, контроля качества сварной конструкции, контроля точности воспроизведения параметров режима и выдачи данных на сигнальное табло.
Для контактной сварки эти модули и контроль состояния электродов по числу сваренных точек после их зачистки включаются в фазе проковки. Адаптация регулятора и модуль передачи сообщений на локальную систему управления запускается только в двухуровневой системе. В фазе паузы управляющая программа находится в режиме ожидания. При отсутствии требований на контроль процесса от других сварочных установок управление передается программе «диспетчер».
При включении в АСУ ТП локальной системы управления работу верхнего уровня корректируют в зависимости от функций, выполняемых локальной системой. Прежде всего, исключаются измерения параметров режима и выдачи данных о процессе на табло сварщика (они выполняются на нижнем уровне). При этом резко сокращается число линий связи между центральной ЭВМ и сварочной установкой. Это не только повышает надежность системы, но и сокращает стоимость системы, время монтажа ее на объекте, упрощает внедрение и эксплуатацию АСУ ТП и локальных систем в целом.
Функциями локальных систем управления контактными машинами на основе микроЭВМ можно считать:
· управление режимом сварки по заданной циклограмме;
· измерение и контроль параметров режима;
· измерение и контроль cos j сварочной машины;
· контроль технического состояния сварочной машины;
· выдачу команды на зачистку электродов;
· регулирование процесса сварки;
· выдачу данных о ходе технологического процесса в ЭВМ верхнего уровня.
Структурная схема системы с условными обозначениями показана на рис.8.5 [9]. Остальные типовые обозначения элементов приведены в описании рис.8.3.
В системе обеспечиваются контроль и измерение до 8 параметров режима. Возможности системы по измерению параметров почти полностью зависят от наличия соответствующего датчика и измерительного преобразователя, поскольку быстродействие микроЭВМ составляет до 400 тысяч операций в секунду.
Рис. 8.5. Структурная схема локальной системы управления контактной точечной машиной на основе микропроцессора (СУФ – схема управления фазой включения тиристоров силового выпрямителя; УСС – устройство синхронизации с электрической сетью; К – коммутатор; ПИ – последовательный интерфейс; Рг – регистр; Кл – клавиатура для задания параметров режима сварки; ПИУ – алфавитно-цифровой дисплей; ЭПК – электропневматические клапаны; СВ – силовой выпрямитель; PI, P2 – порты 1 и 2; В – шина передачи данных; 1 – вход прерывания ЭВМ)
В зависимости от вида свариваемой конструкции, марки сплава, типа сварочной машины и заданной циклограммы режима сварки в системе может быть обеспечен контроль различных параметров режима:
· сварочного тока (амплитудного, действующего или среднего значения);
· сварочного усилия сжатия электродов;
· ковочного усилия сжатия электродов;
· времени сварки; времени приложения ковки и т. п.
Кроме того, осуществляется контроль обобщающих параметров процесса: напряжения между электродами; энергии, выделяемой между электродами за время сварки; сопротивления участка электрод–электрод; теплового расширения металла при сварке (дилатометрия) и т. п.
Измерительная часть системы, таким образом, может сильно изменяться в зависимости от ее назначения. При модульном принципе построения локальную систему легко перестроить для измерения, контроля и управления практически любым набором параметров путем замены соответствующей платы измерительного преобразователя и корректировки программы контроля и управления процессом. Принципиальная схема и конструкция остаются неизменными.
Блок управления электропневмоклапанами и различными переключателями (например, полярности импульса сварочного тока для машин МТК и МТПТ, сигнальными лампами) разработан с учетом максимально сложной универсальной контактной машины типа МТ, МТК, МТПТ, МТВ или типа клещей. В зависимости от типа сварочной машины и циклограммы режима часть управляющих разрядов может не использоваться.
С аппаратурной избыточностью разработан блок управления силовыми выпрямителями. На плату блока устанавливаются только те микросхемы, которые необходимы для управления рассматриваемого типа выпрямителя.
Технико-экономическая оценка показывает, что аппаратная избыточность такой системы незначительно увеличивает только конструкцию системы, а доступная гибкость и универсальность позволяет резко сократить время и стоимость работ по созданию системы для контактной сварочной машины.
В качестве сигнального табло используются алфавитно-цифровые индикаторные устройства типа ПИУ-1 или ПИУ-2. Это позволяет выдавать как текстовую информацию в режиме диалога сварщика с системой при задании режима сварки или сообщения о ходе технологического процесса, так и цифровую информацию о параметрах режима и показателях качества сварочного соединения, в частности диаметр литого ядра сварной точки или глубины проплавления шва.
Блок задания параметров режима и установок контроля и управления процессом может быть выполнен в виде клавиатуры или набора десятипозиционных переключателей. Второй вариант проще в эксплуатации и нагляднее для контроля заданной циклограммы работы сварочной машины и применим, когда число задаваемых уставок небольшое.
Устройство синхронизации с сетью обеспечивает формирование импульсов с интервалом 20 мс синхронизации ЭВМ с сетью питания сварочной машины. Блок имеет защиту от влияния высших гармоник, провалов и переходных процессов в сети.
На выносном пульте управления сварочной машины задаются команды опускание или подъем электродов при их зачистке, отработка сварочного цикла с током или без тока, проверка cosj и т.п. При включении питания ЛСУ управление передается программе диалога, с помощью которой осуществляют вывод и чтение с клавиатуры или включение десятипозиционных переключателей параметров режима и установок контроля и управления процессом. А также осуществляют опрос пульта и сигнала запроса на ввод уставок или вывод данных о ходе технологического процесса, который поступает от ЭВМ верхнего уровня (рис.8.6).
Рис. 8.6. Алгоритм работы локальной системы управления контактной сварочной машиной
При включении система проверяет техническое состояние сварочной машины по дискретным датчикам и в случае неисправности машины прекращает сварку. Если сварочная машина исправна, то с интервалом 20 мс осуществляется выдача управляющих сигналов на электропневмоклапаны, переключатели и силовой выпрямитель для отработки заданной циклограммы, а также измерение параметров режима. В зависимости от заданного алгоритма управления режим сварки корректируется. После окончания процесса осуществляются прогнозирование качества сварного соединения, адаптация алгоритма регулирования и выдача параметров режима и данных о качестве сварного соединения на табло.
При поступлении запроса на диалог от ЭВМ верхнего уровня локальная система по двухпроводной линии связи в последовательном ходе через последовательный интерфейс может считывать с ЭВМ верхнего уровня параметры режима и контроля, а также передать данные о параметрах режима сварки.
Локальная САУ для аргонодуговой сварки выполняет следующие функции:
· управление режимом сварки и позиционирование сварочной горелкой по сложной циклограмме;
· измерение параметров режима в ходе сварки, вывод их на сигнальное табло, контроль параметров по заданным допускам и индикацию недопустимых отклонений режима;
· контроль качества сварного соединения по математической модели процесса;
· регулирование параметров режима по сигналам ОС, в простейшем случае стабилизация режима;
· контроль технического состояния сварочного оборудования;
· печать сводки о ходе процесса сварки;
· отметка краской на изделии места шва, в котором произошло нарушение режима.
Структурная схема алгоритма работы ЛСУ и типовые условные обозначения элементов даны на рис.8.7. Другие условные обозначения приведены в описании рис.8.3 и рис.8.5.
Рис. 8.7. Структурная схема локальной системы управления автоматом для аргонодуговой сварки на основе микропроцессора (Пl-П5 – приводы для управления двигателями; СС – схема сопряжения; СИП – сварочный источник питания; СГ – сварочная головка и манипулятор)
ЛСУ разработана на основе однокристальной микроЭВМ К.1816ВЕ48, имеющей 64 байта оперативной и 1 Кбайт электрически перепрограммируемой памяти. Для обеспечения работоспособности системы в условиях мощных электрических помех предусмотрены как программные, так и аппаратные методы повышения надежности. Управление двигателями перемещения сварочной горелки и подачи присадочной проволоки осуществляется с помощью реверсивного транзисторного привода, который построен по принципу широтно-импульсной модуляции. Для уменьшения динамической погрешности задания частоты вращения двигателя применена отрицательная ОС по напряжению и положительная ОС по току якоря. Торможение двигателя осуществляется при подаче на якорь напряжения противоположной полярности. С помощью специальной схемы реализована защита привода от перегрузок, что повышает ее надежность.
Управление сварочным током осуществляется подачей через схему сопряжения задающего сигнала в блок управления источником питания. Для уменьшения статической погрешности задания параметров режима используется пропорционально-интегральный закон регулирования. Коэффициенты алгоритма регулирования выбраны таким образом, что время установления заданных значений параметров режима сварки составляет не более 0,2 с, а статическая погрешность определяется погрешностью измерения этих параметров (для сварочного тока – не более 2 %, для скоростей – не более 3 %).
В качестве датчика сварочного тока используется шунт, включенный в сварочную цепь, для измерения скорости применяют тахогенераторы. Напряжение дуги измеряют непосредственно на дуговом промежутке. В измерительных преобразователях осуществляются нормализация и функциональное преобразование сигналов с датчиков параметров режима и далее эти сигналы в схеме сопряжения преобразуются в код, пропорциональный среднему значению измеряемой величины. Время усреднения сварочного тока и напряжения составляет 20 мс, а скорости сварки и подачи присадочной проволоки – 1с.
Для хранения программы управления и уставок контроля кроме внутреннего ПЗ микроЭВМ используется также внешняя память емкостью 2 Кбайт. Таким образом, объем программной памяти составляет 3 Кбайт. Выбор параметров режима сварки и автономное управление перемещением горелки осуществляется с помощью клавиатуры. В качестве сигнального табло используется 16-позиционный алфавитно-цифровой дисплей. Для вывода на печать может применяться любая печатающая машинка, имеющая параллельный интерфейс и скорость печати не менее 16-20 символов в секунду.
С помощью последовательного интерфейса ЛСУ аргонодуговой сварки может быть подключена к ЭВМ верхнего уровня, что позволяет строить многоуровневые иерархические АСУ ТП сварочного цеха.
Работает система следующим образом. При включении питания САУ переходит в режим диалога оператора с ЭВМ (рис.8.8). При этом последовательно для каждого участка циклограммы на дисплей выдаются наименование параметра, его значение и размерность: время сварки, сварочный ток, напряжение на дуге, скорость сварки, скорость подачи присадочной проволоки, частота колебания сварочной горелки и координаты перемещения горелки.
Рис. 8.8. Алгоритм работы локальной системы управления автоматом для аргонодуговой сварки
Например, при сварке неповоротных стыков труб малого диаметра диапазон изменения параметров режима составляет: 255 А по току, 25,5 В по напряжению на дуге, 30 м/ч по скорости сварки и 60 м/ч по скорости подачи присадочной проволоки. При этом дискретность задания тока 1 А, напряжения 0,1 В и скорости 1 м/ч.
После нажатия клавиши «сварка» ЛСУ с дискретностью 20 мс контролирует время сварки и управляет режимом согласно заданной циклограмме. После каждого включения осциллятора компьютер проверяет зажигание дуги; если дуга не зажглась, то осуществляется повторный запуск осциллятора. Если сварочный ток не включается после 8-кратного цикла, то система прекращает отработку циклограммы и выдает диагностическое сообщение о неисправности сварочного оборудования. С момента включения сварочный ток увеличивается по линейному закону до заданного значения на первом участке сварки. Число возможных для программирования участков – 8, на каждом из которых оператор-сварщик может задать требуемые значения тока, напряжения на дуге, скорости сварки, скорости подачи проволоки и частоты колебания сварочной горелки. В процессе сварки по измеренным и заданным на каждом интервале параметрам режима осуществляется стабилизация режима.
В зависимости от вида свариваемой конструкции сварщик может ограничить число программируемых участков, задав нулевое значение их деятельности. По заданной программе на различных участках проведено проплавление образца из сплава АМг-6 толщиной 1,5 мм для выбора режима сварки. В ходе сварки на образец раз в секунду наносится метка, при этом на индикатор выдаются данные параметров режима. Кроме того, эти данные выводятся на печать. Таким образом, после проведения всего лишь одного эксперимента может быть выбран режим сварки, которому соответствуют требуемые геометрические размеры сварного шва. При выходе параметров режима из допусков на дисплей подаются соответствующие сообщения. Кроме того, на этом участке шва краскоотметчиком наносится отметка возможного дефекта сварки. В конце сварки осуществляется заварка кратера. При этом сварочный ток и скорость подачи присадочной проволоки уменьшаются по линейному закону. Вычислительные возможности и быстродействие однокристального компьютера позволяют усложнить алгоритм контроля и управления процессом с записью в память нескольких режимов аргонодуговой сварки. При возможности использования датчика ширины шва ЛСУ может работать по описанному выше адаптивному алгоритму регулирования глубины проплавления.
Необходимо отметить, что описанные локальные системы в зависимости от требований автоматизируемого производства могут выполнять только часть из перечисленных функций. Важно, что алгоритмы контроля и управления процессом достаточно просто и без значительных затрат могут быть изменены или скорректированы непосредственно после поставки и внедрения ЛСУ в производство.
http://rutube.ru/video/be0b43192edccfcda131d6dd24f1760f/?autoStart=true&bmstart=88 – автоматизированный сварочный цех
Автоматизация сварочных процессов. Ч.2
Дата добавления: 2020-11-23; просмотров: 76; Мы поможем в написании вашей работы! |
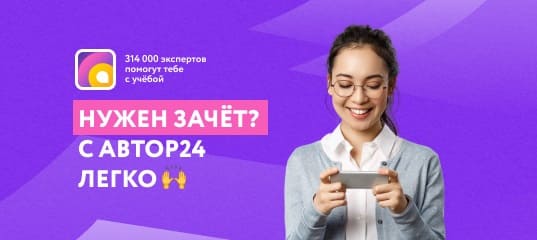
Мы поможем в написании ваших работ!