Устройство монтажных соединений
10.10 В фрикционных соединениях для обеспечения расчетных коэффициентов трения по контактным поверхностям требуется специальная подготовка. В таблице 20 приведены значения коэффициентов трения
и надежности
в зависимости от способов подготовки контактных поверхностей.
Таблица 20
Способ подготовки контактных поверхностей во фрикционных соединениях | Значение коэффициента трения ![]() | Значение коэффициента надежности | ||
2-4 | 5-19 | 20 и более | ||
1 Дробеструйный или пескоструйный двух поверхностей с шероховатостью Rz=50-80 мкм без нанесения фрикционной грунтовки или с последующим нанесением цинконаполненной грунтовки на этилсиликатной основе на обе поверхности толщиной по 60-80 мкм | 0,58 | 1,4 | 1,3 | 1,2 |
2 Дробеструйный или дробеметный двух поверхностей без нанесения фрикционной грунтовки или с последующим нанесением грунтовки на этилсиликатной основе на обе поверхности толщиной по 60-80 мкм с последующим их газопламенным нагревом (до температуры 250°С-300°С) на кольцевых зонах вблизи отверстий площадью не менее площади шайбы (диаметр 60 мм) | 0,60 | 1,4 | 1,3 | 1,2 |
3 Очистка стальными механизированными щетками двух поверхностей (без эффекта шлифовки) | 0,35 | 2,5 | 1,8 | 1,4 |
Таблица 20 (Измененная редакция, Изм. N 1 ).
Вид обработки контактных поверхностей фрикционных соединений должен быть указан в чертежах КМ.
|
|
10.11 Перед обработкой контактных поверхностей фрикционных соединений с них необходимо удалить наждачным кругом все неровности, в том числе заусенцы вокруг отверстий, препятствующие плотному прилеганию элементов и деталей. Заусенцы на краях отверстий должны быть удалены без снятия фасок.
Подготовку контактных поверхностей фрикционных соединений с защитным покрытием цинконаполненными грунтовками следует выполнять в заводских условиях дробеструйным способом колотой стальной или чугунной дробью фракцией 0,3-0,8 мм. При дробеструйной обработке сопло располагают на расстоянии 30-40 см и под углом 50°-75° к очищаемой поверхности, а затем наносят защитно-фрикционную грунтовку. При нанесении защитной грунтовки сопло распылителя располагают перпендикулярно контактной поверхности на расстоянии не более 30 см.
Заводу-изготовителю следует осуществлять контроль подготовки контактных поверхностей фрикционных соединений на образцах-свидетелях при запуске в производство нового объекта, но не реже одного раза в год. Протокол испытаний следует направлять заказчику металлоконструкций.
Для пескоструйной обработки следует применять сухой кварцевый песок фракций 0,6-2,5 мм. Сжатый воздух, используемый для обработки, должен быть очищен от влаги и масла.
|
|
(Измененная редакция, Изм. N 1 ).
10.12 Контактные поверхности болтовых соединений перед сборкой должны быть осмотрены и очищены от грязи, льда, масла, неогрунтованные поверхности - от рыхлой ржавчины, отстающей окалины и краски. Способ очистки назначается в зависимости от характера загрязнения.
(Измененная редакция, Изм. N 1 ).
10.13 "Черные" метизы (болты, гайки, шайбы), т.е. высокопрочный крепеж без покрытия, перед постановкой в соединения необходимо очищать от заводской консервирующей смазки.
Расконсервацию метизов осуществляют кипячением в воде или выдержкой в течение 15-20 мин в подогретом до 80-100 °С щелочном растворе следующего состава, в частях по массе: каустической соды (натрий едкий по ГОСТ Р 55064 ) - 3; кальцинированной соды (натрий углекислый по ГОСТ 5100 ) - 2; тринатрийфосфата (натрий фосфорнокислый по ГОСТ 201 ) - 3; жидкого стекла (натрий кремний-кислый по ГОСТ 13078 ) - 2; воды - 90. Остатки щелочного раствора удаляют промывкой метизов в воде, после чего выполняют их сушку. После сушки выполняют очистку резьбы болтов металлической щеткой и после контрольной прогонки выполняют смазку резьбы.
|
|
(Измененная редакция, Изм. N 1 ).
10.14 Для смазки резьбы болтов, гаек и шайб после контрольной прогонки и окончательной очистки резьбы рекомендуется опустить их в решетчатой таре в емкость объемом 0,4 м
с составом из 80% неэтилированного бензина по ГОСТ Р 51866 и 20% моторного масла М8В по ГОСТ 10541 или трансмиссионного масла ТСп-10 по ГОСТ 23652 . После извлечения метизов из этой емкости бензин испаряется, а на поверхности высокопрочного крепежа остается тонкий слой смазки. Время испарения бензина при положительной температуре составляет
2 ч; ориентировочный расход бензина на 100 кг метизов составляет 2 л, масла - 0,4 л.
(Измененная редакция, Изм. N 1 ).
10.15 Допускается смазывать резьбу высокопрочного крепежа путем опускания после очистки металлической щеткой резьбы каждого болта на 5-7 мм в моторное масло М8В ГОСТ 10541 или трансмиссионное масло ТСп ГОСТ 23652 . После стекания излишков масла выполняют навинчивание гайки на этот болт по всей длине его резьбы.
(Измененная редакция, Изм. N 1 ).
10.16 Очищенные и смазанные болтокомплекты (болт+2 шайбы+гайка) следует хранить в закрытой таре.
|
|
При комплектации болтов гайками последние не должны иметь большого люфта и в то же время должны свободно навинчиваться на болт "от руки", т.е. каждую пару "болт + гайка" проверяют при комплектации на наличие люфта в резьбе.
На болтах с защитным покрытием возможна тугая резьба, когда гайки навинчивают с помощью стандартного рожкового ключа.
Комплектование обработанных болтов двумя шайбами и гайкой выполняют одновременно с сортировкой болтов по длинам. На монтаж подготовленные высокопрочные болты отправляют в металлических емкостях с отсеками для болтов разной длины.
Высокопрочные метизы с защитным антикоррозионным покрытием поставляют в соответствии с нормативными положениями производителя этих метизов.
(Измененная редакция, Изм. N 1 ).
10.17 Период времени от смазки метизов до их установки в соединение не должен превышать 10 сут, а до натяжения на расчетное усилие - 20 сут. Более длительное хранение увеличивает коэффициент закручивания. При превышении срока хранения (более 10 сут) укомплектованные метизы должны быть повторно смазаны.
Временной период хранения метизов с защитным покрытием указан в нормативных положениях производителя, но не более 12 месяцев после их поставки.
(Измененная редакция, Изм. N 1 ).
10.18 Во фрикционном соединении ставить невысокопрочные болты в процессе монтажа не допускается.
Конструкции с болтовыми соединениями класса В и класса А точности вначале следует собирать на временных болтах и пробках. Для достижения точного совпадения отверстий и плотной стяжки пакета пробками заполняется 10% (но не менее 3 шт.), а болтами - 20% общего числа отверстий. При числе отверстий менее 10 устанавливаются 2-3 пробки и 1-2 болта.
Если по условиям монтажа развертывание (райберование) отверстий и постановка в них постоянных болтов невозможны сразу же за сборкой соединения, допускается число пробок определять расчетом на действие строительных нагрузок, при этом число временных болтов должно быть не менее 40% расчетного числа пробок. Пробки следует рассчитывать на срез и смятие по СП 35.13330 в зависимости от прочности стали, из которой они изготовлены. Диаметр временных (сборочных) болтов допускается назначать на 1-6 мм меньше диаметров отверстий. Временные болты принимают, как правило, точности класса С по ГОСТ 15589 . Они должны обеспечить плотное стягивание элементов в соединении с затяжкой, как правило, гайковертами на усилие не менее 49 кН (5 тс).
10.19 Во фрикционном соединении, собираемом на пробках и болтах, высокопрочные болты должны свободно - без усилий - проходить в отверстия собранного пакета. При затруднениях в постановке болтов из-за черноты, овальности или косины отверстий следует развертывать их коническими развертками, диаметр которых не должен быть менее номинального диаметра болтов и не более проектного диаметра отверстий. Развертывание допускается только в плотно стянутых пакетах без применения смазочно-охлаждающих жидкостей и воды.
В болтовых соединениях несущего типа повышенной класса А или нормальной класса В точности развертывание или прочистку отверстий следует производить коническими развертками, диаметр которых соответствует принятому в проекте диаметру отверстий с соответствующими допусками.
10.20 Каждый высокопрочный болт фрикционного соединения комплектуется одной гайкой и двумя круглыми шайбами - под головку болта и под гайку по ГОСТ Р 53664 .
Если в стесненных местах при ремонте и усилении старых мостов установить две шайбы невозможно, допускается установить одну шайбу под деталь, которая при натяжении болта будет вращаться при разности диаметров болта и отверстия не более 3 мм и размерах головки болта и гайки по ГОСТ Р 53664 .
Постоянные цилиндрические болты класса В и класса А точности соединений несущего (нефрикционного) типа комплектуют одной гайкой, одной шайбой под головку и одной - двумя шайбами под гайку. В соединениях, где болты работают на срез и смятие, резьба болта должна находиться вне отверстия, а гладкая часть стержня не должна выступать из шайб.
В каждом затянутом болте со стороны гайки должно оставаться не менее одного полного витка резьбы.
10.21 Гайки высокопрочных болтов, натянутых до расчетных усилий, ничем дополнительно закреплять не следует. В болтовых соединениях без контролируемого натяжения, выполняемых крепежными изделиями по ГОСТ 1759.0 гайки закрепляют от раскручивания с помощью пружинных шайб по ГОСТ 6402 или контргаек. Пружинные шайбы не следует применять совместно с круглыми и при разности болта и отверстия более 3 мм.
(Измененная редакция, Изм. N 1 ).
10.22 В болтовых и фрикционных соединениях при монтаже металлоконструкций точное совпадение отверстий обеспечивается постановкой монтажных точеных пробок номинальным диаметром на 0,2 мм меньше проектного диаметра отверстий. Длина цилиндрической части пробки должна быть на 10-15 мм больше толщины собираемого пакета.
Пробки для сборки конструкций в обычном и северном исполнениях должны быть изготовлены из сталей марки ВСт5пс2 по ГОСТ 535 или марки 295-6 по ГОСТ 19281 .
10.23 Натяжение высокопрочных болтов на расчетные усилия по СП 35.13330 следует производить завинчиванием за гайку или головку болта до требуемой расчетной величины крутящего момента , определяемого по формуле
,
где - коэффициент закручивания, равный 0,175 для "черных" болтов без покрытия. Для болтов с защитным покрытием коэффициент закручивания принимается по нормативным положениям производителя этих метизов;
- расчетное усилие натяжения высокопрочного болта. Для болтов диаметром 22, 24 и 27 мм принимаются соответственно расчетные усилия 220 кН (22,5 тс); 258 кН (26,3 тс) и 334 кН (34,2 тс) по ГОСТ Р 53664 , для болтов класса 10.9 из стали марки 40Х "селект" - по ГОСТ 4543 ;
- номинальный диаметр резьбы болта.
Болты чисто фрикционных соединений необходимо, как правило, вначале затягивать гайковертом от 50% до 90% расчетного усилия, затем дотягивать динамометрическим ключом до расчетного усилия с контролем натяжения по величине прикладываемого крутящего момента после геодезического контроля собранного фрикционного соединения.
(Измененная редакция, Изм. N 1 ).
10.24 Натяжение болтов необходимо производить от участков с плотным прилеганием деталей соединяемого пакета к участкам с зазорами. Болты, расположенные рядом с пробками, следует затягивать повторно после удаления пробок. В соединениях с затянутыми болтами не допускаются зазоры между плоскостью конструкции, шайбами, гайками и головками болтов. При остукивании молотком болт не должен дрожать и смещаться.
10.25 Болты комбинированных соединений (в узле сочетаются сварные и болтовые соединения) натягивают в несколько этапов:
1) установленные высокопрочные болты на первом этапе затягивают с помощью гайковертов до усилий, равных 60-70% проектного. Проверяют плотность стягивания пакета, при этом определенные ряды болтов по технологическому регламенту затягивают обычным "рожковым" ключом от руки;
2) проводят весь комплекс сварочных работ и выполняют геодезическую съемку данного комбинированного узла;
3) ослабляют натяжение болтов до нулевого значения с одной стороны стыка. Если болты "закусывает", то развинчивать и вторую сторону стыка;
4) выполняют дотяжку всех болтов до контрольного усилия натяжения;
5) сдают фрикционное соединение на высокопрочных болтах представителю заказчика;
6) выполняют антикоррозионную защиту фрикционного соединения на высокопрочных болтах по технологическому регламенту. В соединениях с огрунтованными контактными поверхностями допускается совмещать временную антикоррозионную защиту с окончательной окраской металлоконструкции, если период между изготовлением конструкции и окраской на монтаже не превышает 20 мес.
(Измененная редакция, Изм. N 1 ).
10.26 Натяжение высокопрочных болтов на проектные усилия следует производить, как правило, после окончания проверки проектного геометрического положения конструкции или ее части. Гайки или головки болтов, натянутых на проектные усилия, отмечают светлой масляной краской. Затянутые высокопрочные болты на проектное усилие принимает представитель технадзора заказчика. Все работы по натяжению и контролю регистрируют в журнале постановки высокопрочных болтов (ВПБ).
При приемке смонтированных конструкций с фрикционными соединениями строительной организацией должна быть предъявлена следующая документация:
журнал контроля качества подготовки контактных поверхностей;
журнал контрольной тарировки динамометрических ключей;
журнал постановки высокопрочных болтов;
сертификаты завода-изготовителя на метизы.
10.27 "Чернота" (несовпадение отверстий в деталях собранного пакета) не должна превышать разности номинальных диаметров отверстия и болта.
10.28 При подборе болтов по длине применяют специальный щуп для промера толщины пакета, а для удобства узлы размечают мелом с выделением участков, на которых устанавливают болты одинаковой длины.
При сборке конструкций из ПКМ длина болтов определяется из условия соединения конструктивных элементов без захода резьбовой части на элементы из ПКМ.
Допускается по согласованию с проектной организацией устанавливать в отверстие втулку из нержавеющей стали с фланцем или без фланца в зависимости от ее конструкции с размерами:
внутренний диаметр на один миллиметр больше диаметра болта;
наружный диаметр цилиндрической части втулки на 2 мм больше ее внутреннего диаметра;
диаметр фланца не менее удвоенного наружного диаметра цилиндрической части втулки.
Втулки следует устанавливать на клее холодного отверждения.
10.29 Каждый болт устанавливают в соединении с двумя шайбами (одна ставится выпуклой стороной к головке болта, а другая - выпуклой стороной к гайке). Ставить более одной шайбы с каждой стороны пакета запрещается.
При сборке конструкций из ПКМ используются 2 вида шайб:
при контакте с элементом из ПКМ устанавливаются шайбы по ГОСТ 6958 (увеличенные);
при контакте с металлическим элементом устанавливаются шайбы по ГОСТ 11371 (обычные).
10.30 В момент установки высокопрочных болтов гайки должны свободно (от руки) навинчиваться по резьбе и в тоже время не иметь большого люфта. В противном случае гайку или болт следует заменить, а отбракованные болты и гайки отправить на повторную подготовку и комплектацию.
10.31 Длины болтов назначают в соответствии с суммарной толщиной собираемых деталей, высотой гайки и двух шайб с округлением до 10 мм. При этом выступающая за пределы гайки часть болта (за исключением соединения элементов из ПКМ) должна иметь не менее одного витка резьбы.
10.32 Все поставленные высокопрочные болты затягивают сначала пневматическими гайковертами. Причем, вначале затягивают гайковертами стяжные болты, которые должны быть равномерно распределены по полю соединения и в непосредственной близости от пробок.
10.33 Болты затягивают окончательно специально протарированным контрольным динамометрическим ключом или динамометрическими гайковертами. Усилие натяжения для поверхностей без защитного покрытия 100% от расчетного; для поверхностей с антикоррозионной зашитой 110% от расчетного (10% на релаксацию от обжатия поверхностей).
При контроле затяжки высокопрочных болтов представителем заказчика фактический момент закручивания должен быть не менее проектного и не превышать его более чем на 20% с учетом того, что период от натяжения болтов до их контроля не превышает 5 дней, с увеличением этого периода возрастает крутящий момент страгивания.
(Измененная редакция, Изм. N 1 ).
10.34 Динамометрические ключи, гидравлические и электроаккумуляторные гайковерты следует тарировать.
Динамометрические ключи подвергают тарировке в начале и в середине каждой рабочей смены.
Динамометрические гайковерты следует тарировать перед первым их применением (или после ремонта), повторно - после натяжения первой и второй тысячи болтов, а затем периодически после натяжения каждых 5000 болтов.
Результаты тарировки заносят в журнал ("Журнал тарировки динамометрических ключей и гайковертов").
(Измененная редакция, Изм. N 1 ).
10.35 При натяжении высокопрочных болтов необходимо строго следить за тем, чтобы болты не получали недопустимой перетяжки гайковертами. При этом должна обеспечиваться возможность дотягивания болтов динамометрическими ключами путем поворота гайки на небольшой угол (до 30-60°).
10.36 Применяемые для натяжения высокопрочных болтов на проектные усилия (на 100% и 110%) динамометрические ключи и гайковерты должны обеспечивать регистрацию крутящих моментов с погрешностью не более 5%. Передаваемые ключом (гайковертом) крутящие моменты регистрируют во время движения ключа в направлении, отвечающем увеличению натяжения. Затяжку болтов следует производить плавно и без рывков.
(Измененная редакция, Изм. N 1 ).
10.37 Сварные монтажные соединения следует выполнять в соответствии с требованиями приложения М, настоящего свода правил, проекта конструкции, технологических регламентов и ППР. Перед сваркой металл следует прогревать пламенем газовой горелки. Монтажную сварку разрешается производить при температуре металла не ниже минус 20 °С.
(Измененная редакция, Изм. N 1 ).
10.38 При комплектации сварочных постов мостостроительной организации необходимо выполнить ревизию каждого источника питания сварочной дуги, сварочных автоматов, полуавтоматов и цепей управления, при этом особое внимание следует обратить на качество изоляции всех проводов, а также на надежность выполнения всех электрических соединений силовых, сварочных кабелей и цепей управления указанным оборудованием.
10.39 Приготовление металлохимической присадки - МХП (смешивание "крупки" с химической добавкой) следует выполнять в специальном смесителе. Равномерное обволакивание ("опудривание") химической добавкой металлических гранул ("крупки") достигают при перемешивании в течение 4-5 мин. После опудривания крупку необходимо просеять на сите с ячейкой 1 1 мм для удаления излишков химической добавки.
10.40 Обрезку технологических припусков элементов монтируемых металлоконструкций следует выполнять полуавтоматами кислородной резки, обеспечивающими необходимое качество резки. После этого требуется зачистка поверхности только от окалины и грата без снятия основного металла.
Для обрезки припусков небольшой протяженности ( 500 мм) допускается ручная резка, при этом должны быть обеспечены требования к качеству кромок по чертежам КМ после зачистки их абразивным инструментом с удалением всех дефектов поверхности на глубину не менее 1 мм.
10.41 Для удаления отдельных дефектных участков стыкового или углового шва рекомендуется применять газопламенные резаки с внутрисопловым смешением газов. Для вырезки дефектов шва небольшой протяженности, а также для зачистки и механической обработки швов рекомендуется применять механизированный инструмент (шлифовальные машинки) различного типа и шлифовальные круги различного типа и толщин согласно паспортным данным применяемого оборудования.
10.42 Удалять шлак с поверхности шва и/или слоев шва рекомендуется малогабаритными пневмомолотками различного типа.
10.43 Для снабжения воздухом пневмоинструмента и пескоструйного оборудования рекомендуется применение высокопроизводительных компрессоров, оснащенных блоками подготовки воздуха (влаго- и маслоотделителями).
10.44 Монтажную сварку конструкций стальных мостов надлежит выполнять в соответствии с требованиями технологического регламента, устанавливающего последовательность сборочно-сварочных операций на конкретном объекте, применяемую оснастку, инструмент, оборудование, сварочные материалы, режимы сварки и порядок наложения швов, операции по контролю качества.
10.45 Монтажная сварка мостовых конструкций при температуре воздуха минус 20 °С и ниже должна выполняться с применением технологических (защитных) укрытий, установленных с лицевой и обратной сторон монтажного соединения, обогреваемых калориферами или теплогенераторами. Температура воздуха внутри укрытий должна быть не ниже минус 10 °С на расстоянии 1 м от кромки стыка (по вертикали).
10.46 Переноска и перекантовка краном собранных на прихватках крупногабаритных монтажных блоков без применения специальных приспособлений, обеспечивающих неизменяемость их формы, не допускаются.
10.47 При сборке элементов под сварку на клетках, стендах, стапелях следует обеспечить проектный строительный подъем пролетного строения. Необходимо также предусматривать предварительные переломы и сдвиги в стыках для компенсации сварочных деформаций, влияющих на окончательные размеры и форму конструкций. Величины их назначаются в ППР и проверяются при сварке первых блоков. При сборке и сварке крупных блоков необходимо учитывать также их деформации и взаимные смещения в стыках от воздействия солнечной радиации.
Соединения, собранные под сварку, должны быть предъявлены руководителю сварочных работ. Если подготовленные стыки в течение 24 ч не были сварены, перед сваркой их вновь необходимо предъявить.
Номер каждого выполненного стыка по маркировочной схеме и дату сварки заносят в Журнал сварочных работ с росписями сварщика и руководителя сварочных работ.
10.48 Элементы, свариваемые на монтаже двусторонними швами с перекантовкой, допускается перекантовывать только после остывания шва ( 20 мм) первого прохода до температуры не выше 100 °С с принятием мер против динамических нагрузок, а для стыков толщиной 25-40 мм - не более 40 °С.
10.49 При автоматической сварке под флюсом, в том числе и с применением МХП, механизированной сварке в смеси защитных газов и ручной дуговой сварке стыковых соединений с односторонними швами в нижнем положении следует применять съемные (несплавляющиеся) подкладки, обеспечивающие формирование обратной стороны шва без последующей его подварки и, как правило, без механической обработки.
Рекомендуются следующие формирующие подкладки:
стекло-медные - для автоматической сварки под флюсом и с МХП металла толщиной до 16 мм включительно;
медные со стеклотканью - для автоматической сварки под флюсом и с МХП металла всех толщин;
медные со стеклотканью - для автоматической сварки под флюсом по ручной или механизированной подварке корня шва, для односторонней ручной дуговой сварки на 100% сечения шва в нижнем положении, а также для односторонней механизированной сварки в смеси защитных газов в нижнем положении;
керамические - для механизированной сварки в смеси защитных газов и ручной дуговой сварки.
Для медных подкладок следует применять листовую или полосовую медь марок М0, M1, M1p, М2, М2р, М3, М3р (ГОСТ 859 и ГОСТ 1173 ).
10.50 При сборке и сварке монтажных соединений металлоконструкций пролетного строения следует проводить пооперационный контроль качества выполнения требуемой цепочки технологических операций в последовательности выполнения сначала сборки монтажного соединения и затем его сварки.
10.51 К неразрушающему ультразвуковому контролю качества монтажных сварных стыковых соединений допускаются специалисты, аттестованные в установленном порядке на второй уровень квалификации по ультразвуковой дефектоскопии (УЗД) сварных соединений на объектах (металлоконструкции технических устройств, зданий и сооружений) перечня объектов контроля; они обязаны иметь при себе во время контроля швов действительные удостоверения, а копии указанных удостоверений следует вложить в журналы сварочных работ.
10.52 Исполнительной документацией по качеству сварных конструкций являются: журналы монтажных работ; общий журнал работ; постановки и натяжения высокопрочных болтов; сварочных работ; журнал ультразвукового контроля качества (УЗК) монтажных сварных соединений; журнал пескоструйной очистки; журнал тарировки динамометрических ключей; журнал контроля подготовки высокопрочных болтов, гаек и шайб; технологический регламент по сборке и сварке монтажных соединений; заключения по результатам неразрушающих методов контроля качества швов с указанием всех обнаруженных дефектов (допустимых и недопустимых); заключения и протоколы испытаний контрольных сварных технологических проб; акты проверки соблюдения технологии монтажной сварки; материалы по выявлению причин появления дефектов в швах и т.п.
10.53 Для создания сквозной системы контроля за качеством сборочно-сварочных работ мостостроительная организация разрабатывает маркировочную схему монтажных сварных швов, в которой присваивается наименование и порядковый номер каждому сварному шву, выполненному на монтаже, а также наименование, порядковый номер швам и плитам, прошедшим укрупнительную сборку. Марки швов и элементов, принятые в маркировочной схеме, едины для записи во всей исполнительной документации. Маркировочную схему разрабатывают на каждое пролетное строение и прикладывают к исполнительной документации.
10.54 Входной контроль качества охватывает:
проверку полноты проектно-технологической документации и ее соответствие требованиям норм;
контроль качества поступающих на монтаж основных металлоконструкций;
контроль качества поступающих в производство сварочных материалов путем проверки наличия и срока годности свидетельств об их аттестации и проверки каждой партии сварочных материалов в установленном порядке;
проверку состояния сварочного оборудования, наличие и срок годности свидетельств об аттестации оборудования;
контроль качества поступающих в производство сварочных технологий и режимов сварки путем аттестации технологий сварки в АЦ НАКС;
проверку срока годности документов (аттестационных удостоверений) у электросварщиков, инженерно-технических работников и дефектоскопистов, выданных в соответствующих аттестационных центрах.
10.55 Перед началом монтажных сварочных работ на конкретном объекте, а также перед передачей каждой новой партии одного из сварочных материалов на монтаж их качество проверяется путем сварки и испытания контрольных технологических проб с определением механических свойств. Сварка контрольных технологических проб выполняется на стройплощадке конкретного строящегося объекта в реальных условиях монтажа. По результатам испытаний таких контрольных сварных проб для мостостроительной организации должны быть выданы протоколы испытаний и заключения по возможности применения конкретных партий аттестованных сварочных материалов в определенной их комбинации на стройплощадке при монтаже металлоконструкций конкретного пролетного строения. Данные испытания и выдачу указанных документов должны осуществлять специализированные организации. Изготовление и испытание образцов из указанных контрольных сварных технологических проб следует производить в соответствии с указаниями ведомственных нормативных документов.
10.56 При приемке сварных швов проводят визуально-измерительный контроль, ультразвуковой контроль (УЗД) по ГОСТ Р 55724 и технологическому регламенту на монтажную сварку конкретного объекта, а при необходимости уточнения данных ультразвукового контроля выполняют радиографический контроль по ГОСТ 7512 (просвечивание проникающим излучением), а также металлографические исследования макрошлифов на торцах соединений и механические испытания контрольных сварных соединений по ГОСТ 6996 .
(Измененная редакция, Изм. N 1 ).
10.57 Швы монтажных сварных соединений должны удовлетворять следующим условиям:
а) иметь гладкую или равномерно чешуйчатую поверхность с плавными переходами к основному металлу, без наплывов и не допускаемых подрезов (см. таблицу 21);
б) в многопроходных швах облицовочные валики должны перекрывать друг друга на 1/3 ширины, а глубина межваликовых впадин не должна превышать 0,5 мм;
в) все кратеры должны быть заварены;
г) не должны иметь недопустимых поверхностных дефектов;
д) механическая обработка шва и околошовной зоны должна соответствовать чертежам КМ и требованиям документации на неразрушающий контроль. Радиусы сопряжений в зонах сплавления при механической обработке угловых швов должны быть не менее 3 мм, стыковых швов - не менее 10 мм.
Таблица 21
Номинальный размер катета углового шва в тавровых, угловых и нахлесточных соединениях, мм | Предельные отклонения катета, мм, при способе сварки | ||
автоматическая и механизированная под флюсом ГОСТ 8713 , ГОСТ 11533 | механизированная в смеси защитных газов ГОСТ 14771 , ГОСТ 23518 | ручная ГОСТ 5264 , ГОСТ 11534 | |
До 5 включительно | +1 | +1; -0,5 | +1; -0,5 |
Св. 5 до 8 включительно | +2 | +2; -1 | +2; -1 |
Св. 8 до 12 включительно | +2,5 | +2,5; -1,5 | +2,5; -1,5 |
Свыше 12 | +3 | +3; -2 | +3; -2 |
Допускаемая вогнутость углового шва | До 30% катета, но не более 3 мм |
При несоблюдении хотя бы одного из требований сварные швы подлежат ремонту до проведения ультразвукового контроля и повторному визуально-измерительному контролю.
10.58 При металлографическом исследовании макрошлифов на торцах сварных швов после срезки выводных планок проверяют возможные дефекты в виде непроваров, пор и шлаковых включений, трещин. На сварных технологических пробах, кроме того, определяют коэффициент формы провара, ширину и очертание зон термического влияния (ЗТВ), измеряют твердость различных зон сварного шва. В случае получения неудовлетворительных результатов металлографического исследования макрошлифов исследуют микроструктуру на полированных и травленых шлифах при сильном увеличении (в 50-2000 раз) сварного шва и околошовной зоны с определением размеров зерна.
Швы сварных соединений не могут быть признаны годными, если по одному из использованных методов контроля получены отрицательные результаты.
10.59 Соответствие усилий натяжения высокопрочных болтов проектным контролируют путем выборочной проверки крутящих моментов. Для этого проверяемый болт затягивают специально протарированным контрольным динамометрическим ключом, отсчеты по которому берут после начала поворота гайки, т.е. в движении гайки.
Усилие при контроле и натяжении прикладывают с одной и той же стороны болта, отмечаемой мелом, ведя поворот за гайку.
Количество болтов, подлежащих контролю - по таблице 22.
Таблица 22
Количество болтов в соединении, шт. | Количество болтов, подлежащих контролю, шт. |
До 5 включительно | 2 |
От 6 до 20 | 3 |
21 и более | 15% |
При несоответствии результатов контроля хотя бы для одного болта контролируют все болты данного фрикционного соединения.
При натяжении болтов за их головку величину указанных крутящих моментов следует увеличить на 5%.
Натяжение болтов, при контроле которых крутящие моменты не выходят из указанных пределов, должно быть доведено до требуемого значения.
(Измененная редакция, Изм. N 1 ).
10.60 Конструкции мостов со сварными монтажными соединениями после их сборки и сварки подлежат поэтапной комиссионной приемке с составлением "Акта промежуточной приемки ответственных конструкций".
Периодичность приемки следует указывать в проекте производства работ (ППР) в зависимости от способа монтажа конструкций и объемов выполняемых монтажно-сварочных работ.
При конвейерно-тыловой сборке и продольной надвижке неразрезных стальных пролетных строений приемку осуществляют перед надвижкой каждого очередного смонтированного и сваренного участка пролетного строения. При наводке наплаву - перемещаемыми секциями, при навесной сборке - попролетно или перед каждым очередным перемещением монтажного крана по пролетному строению.
10.61 Допустимые отклонения линейных размеров и геометрической формы смонтированных конструкций пролетных строений стальных мостов приведены в таблице 23.
Таблица 23
Наименование отклонения | Значение предельного отклонения, мм |
1 Отклонение длины каждой главной балки или фермы пролетного строения от проектной при длине ![]() | |
до 50 включительно | ±10 |
свыше 50 | 0,0002 ![]() |
2 Отклонение расстояний между соседними узлами главных ферм и связей при расстоянии ![]() | |
до 9 включительно | ±3 |
свыше 9 | 0,0003 ![]() |
3 Отклонение от проектных ординат строительного подъема пролетного строения, смонтированного целиком или частично при ординатах ![]() | |
до 100 включительно | ±10 |
выше 100 | ±0,1 ![]() |
4 Отклонение в плане оси главной балки или фермы от проектной оси при пролете ![]() | 0,0002 ![]() |
5 Отклонение в плане одного из узлов от прямой, соединяющей два соседних с ним узла при длине панели ![]() | 0,001 ![]() |
6 Отклонение расстояний между осями вертикальных стенок сплошностенчатых балочных и коробчатых пролетных строений | ±4 |
7 Отклонение расстояний по длине балок и коробок между смежными вертикальными ребрами жесткости, к которым прикрепляются поперечные балки ортотропных и ребристых плит; соответствующие расстояния между поперечными балками ортотропных и ребристых плит | ±2 |
8 Отклонение расстояний между осями продольных ребер ортотропных плит: | |
в зоне стыков и пересечений с поперечными балками | ±2 |
на других участках | ±4 |
9 Отклонения по высоте сплошностенчатых балок и коробок в зоне цельносварных или комбинированных | ±2 |
10 Допускаемая стрела выгиба осей элементов длиной ![]() | |
отдельных элементов главных ферм, балок, коробок, балок проезжей части | 0,001 ![]() |
элементов связей | 0,0015 ![]() |
11 Грибовидность, перекос, грибовидность с перекосом поясов сварных балок, коробок, ортотропных плит (для коробок и ортотропных плит ![]() | ![]() |
11.1 В стыках, в местах сопряжения балок с другими элементами, в зонах установки опорных частей и железобетонных плит с закладными деталями | ![]() |
11.2 На других участках | ![]() ![]() |
12 Выпучивание стенки балок и коробок при свободной высоте стенки ![]() | ![]() |
12.1 Для балок и коробок с поперечными ребрами жесткости | 0,006 ![]() |
12.2 Для балок без поперечных ребер жесткости | 0,003 ![]() |
13 Остаточные угловые деформации в сварных стыковых соединениях ("домики"), определяемые стрелой прогиба ![]() ![]() | ![]() |
до 20 включительно | ![]() |
свыше 20 | 2 |
14 Допускаемая разность (в поперечном направлении) отметок узлов пролетного строения: | |
а) после установки его на опорные части | |
на опорах | 0, 001 ![]() |
в пролете | 0,002 ![]() |
( ![]() | |
б) при сборке на подмостях, стапеле, насыпи | 0,001 ![]() |
( ![]() |
Таблица 23 (Измененная редакция, Изм. N 1 ).
Дата добавления: 2019-09-13; просмотров: 349; Мы поможем в написании вашей работы! |
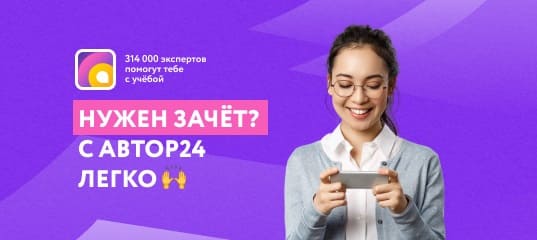
Мы поможем в написании ваших работ!