Соотношение твердостей металлов и сплавов (ориентировочное)
МАШИНОСТРОИТЕЛЬНЫЕ МАТЕРИАЛЫ
7.1. СТАЛЬ
Рекомендации по выбору марки стали. По возможности необходимо шире использовать стали: углеродистые обыкновенную Ст3, автоматную А12 и конструкционные 15, 35 и 45. Автоматная сталь хорошо обрабатывается, но склонна к красноломкости, т. е. к хрупкости, при горячей механической обработке. Из сталей Ст3 и А12 изготовляют детали, для которых не требуется большая прочность.
В сварных конструкциях целесообразно применять углеродистые стали марок Ст0, Ст3, Ст5, Ст6, 15, 35, 45, 50Г. Сварка легированных сталей несколько затруднена из-за склонности к закалке околошовной зоны и образования в ней хрупких структур.
Марганцовистым сталям в состоянии проката или после нормализации свойственны повышенные прочность и упругость. Они относительно дешевые и пригодны для изготовления деталей, которые должны иметь повышенные прочность, вязкость и износостойкость.
Легированные термически обработанные стали обладают более высокими механическими свойствами, чем углеродистые, и лучше прокаливаются. Их подвергают закалке с охлаждением в масле, что значительно уменьшает опасность образования закалочных трещин. Стали, содержащие никель, молибден и вольфрам, следует применять в тех случаях, когда их нельзя заменить сталями, содержащими кремний, марганец и хром.
Основные термины и определения. Отжиг-нагрев стали до температур закалки в интервале превращений, выдержка при этой температуре и медленное охлаждение. Применяют для уменьшения остаточных напряжений в деталях после отливки или обработки давлением, а также для понижения твердости и улучшения обрабатываемости.
|
|
Нормализация - нагрев стали, как при отжиге, и охлаждение на воздухе с целью улучшения механических свойств и обрабатываемости резанием.
Закалка - нагрев стали до температуры выше или в интервале превращений, выдержка при этой температуре и охлаждение с большой скоростью в воде, растворах солей, масле, на воздухе. Применяют для повышения прочности, твердости и износостойкости деталей. Закалка может быть общей (объемной) и поверхностной.
Отпуск - нагрев после закалки или нормализации до температуры ниже интервала превращений, выдержка и последующее охлаждение. Применяют для снижения остаточных напряжений и твердости, а также повышения вязкости и пластичности закаленных деталей.
Улучшение - закалка и высокотемпературный отпуск. Применяют для повышения прочности деталей с целью сохранения или увеличения вязкости.
Цементация, нитроцементация (науглероживание) - насыщение поверхностного слоя стали углеродом для повышения твердости и прочности этого слоя после термической обработки, износостойкости и усталостной прочности деталей.
|
|
Азотирование - насыщение поверхностного слоя стали азотом с целью повышения твердости и прочности поверхностного слоя, износостойкости, коррозионной стойкости и усталостной прочности деталей в целом.
Цианирование - насыщение поверхностного слоя стали одновременно углеродом и азотом для повышения твердости и прочности этого слоя после термической обработки, износостойкости и усталостной прочности деталей.
Наклеп - упрочнение поверхностного слоя механическим способом (накаткой гладкими роликами, дробеструйной обработкой и т. д.).
Условные обозначения.
НВ - твердость по Бринеллю;
HRC - твердость по Роквеллу;
HV - твердость по Виккерсу;
σВ - предел прочности при растяжении (временное сопротивление);
σТ - предел текучести;
σ -1 - предел выносливости при изгибе с симметричным циклом нагружения;
[σр] - допустимое напряжение при растяжении;
σ -1р - предел выносливости при растяжении;
[σИ] - допустимое напряжение при изгибе;
[σсж] - то же при сжатии;
[σсм] – при смятии;
[τср] - при срезе;
[τкр] – при кручении;
I - статическая нагрузка;
II - переменная нагрузка от нуля до максимума (пульсирующая);
|
|
III - знакопеременная нагрузка (симметричная). В учебниках и справочниках твердость материалов часто указывают в разных единицах измерения. В таблице 7.1 дано соотношение между этими единицами.
Соотношение твердостей металлов и сплавов (ориентировочное)
НВ | HRC | HV | НВ | HRC | HV | НВ | HRC | HV | НВ | HRC | HV |
143 | - | 144 | 207 | 18 | 209 | 321 | 35 | 320 | 555 | 56 | 649 |
146 | - | 147 | 212 | 19 | 213 | 332 | 36 | 335 | 578 | 58 | 694 |
149 | - | 149 | 217 | 20 | 217 | 340 | 37 | 344 | 600 | 59 | 746 |
153 | - | 152 | 223 | 21 | 221 | 351 | 38 | 361 | 627 | 61 | 803 |
156 | - | 154 | 229 | 22 | 226 | 364 | 39 | 380 | 652 | 63 | 867 |
159 | - | 159 | 235 | 23 | 235 | 375 | 40 | 390 | - | 65 | 940 |
163 | - | 162 | 214 | 24 | 240 | 387 | 41 | 401 | - | 67 | 1021 |
166 | - | 165 | 248 | 25 | 250 | 402 | 43 | 423 | - | 69 | 1114 |
170 | - | 171 | 255 | 260 | 255 | 418 | 44 | 435 | - | 72 | 1220 |
174 | - | 174 | 262 | 27 | 261 | 430 | 45 | 460 | |||
179 | - | 177 | 269 | 28 | 272 | 444 | 47 | 474 | |||
183 | - | 183 | 277 | 29 | 278 | 460 | 48 | 502 | |||
187 | - | 186 | 287 | 30 | 285 | 477 | 49 | 534 | |||
192 | - | 190 | 293 | 31 | 291 | 495 | 51 | 551 | |||
196 | - | 197 | 302 | 33 | 305 | 512 | 52 | 587 | |||
202 | - | 201 | 311 | 34 | 312 | 532 | 54 | 606 |
Примечание. С достаточной степенью точности для большинства сталей (углеродистых, никелевых, хромистых и др.) можно считать, что σВ = 0,35 НВ.
|
|
Углеродистую сталь обыкновенного качества (ГОСТ 380-71) поставляют трех групп: А - по механическим свойствам; Б - по химическому составу; В - по механическим свойствам и химическому составу.
Сталь изготовляют следующих марок: группы А – Ст0, Ст1, Ст2, Ст3, Ст4, Ст5, Ст6; группы Б – БСт0, БСт1, БСт2, БСт3, БСт4, БСт5, БСтб; группы В - ВСт1, ВСт2, ВСт3, ВСт4, ВСт5. Букву А в обозначении марки не указывают.
Механические свойства углеродистой стали обыкновенного качества приведены в таблице 7.2.
Дата добавления: 2019-02-22; просмотров: 87; Мы поможем в написании вашей работы! |
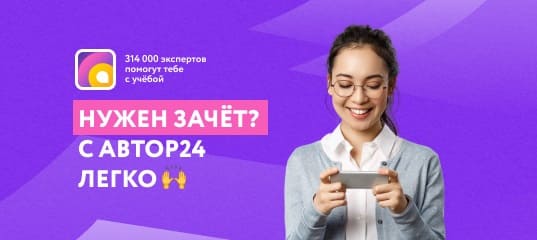
Мы поможем в написании ваших работ!