Clearing of Occurrence Counters
SVT Messages at GECB 1.1. Blinking messages The following messages are blinking in each status display of the Service Tool: Blink-Message Description related setup Wrong Board The software cannot identify the board. à replace the GECB. SCN Error Wrong Software à order a new software with correct partnumber (refer to Baseline Release Document). ES Wiring ES Safety chain wiring fault (PES not wired in series) à check safety chain wiring. After correction of the wiring the error is cleared by switching off/on à For GCS222MRL, the SP function “Tools – Safety Wiring” must be executed. SAF Wiring SAF Safety chain wiring fault (DS/GS not wired in series) à check safety chain wiring. After correction of the wiring the error is cleared by successful door operation or by unlocking the landing door. à For GCS222MRL, the SP function “Tools – Safety Wiring” must be executed. Learn Run a) The drive package is performing its Learn Run to learn the hoistway situation. b) The drive package is adjusting the encoder. à wait until the learn run has completed. DRV-TYP=0 Door Bridge DW or DFC input has not been low while the door was opened. Reason is a bridged door lock. à check safety chain à This event is stored into EEPROM so that the ONLY way to bring the elevator into operation again is by using INS. Switch INS Landing door was opened for longer than 4 seconds or the car door is bridged. Elevator is taken out of service. à This event is stored into EEPROM so that the ONLY way to bring the elevator into operation again is by using INS. à For Multidrop door systems, the cause of this error could be a failure of the RS-board for the output signals F_SFO (IO 1092) or R_SFO (IO 1093). TCI-lock The sequence to leave TCI-mode was not correctly followed: 1. operate TES 2. open door 3. leave car roof 4. switch TCI off 5. release TES 6. close door No 110VAC! The power supply of the safety chain is missing. à Check connection. à Check fuses. 1LS+2LS on Limit switches 1LS and 2LS are active (low) at the same time. à Check power supply of the position reference system. Adr-Check / TCI-Check Some RSL I/Os have to be programmed to a valid address and are not allowed to be set to 00-0 or 01-0. Currently only one I/O is checked: 691 – TCI à Set I/O 691 to a valid address TCI(691) DOL alw.on The signal DOL RDOL is low while the door is closed. à Check Event log to find out whether the front or the rear door signal is wrong. à Check door fuses. à Check 24V power supply DOL (000) RDOL(544) SE-Fault The car cannot start due to missing SE-signal à Check the door bypass 1TH-Fault The DBR-contact which is connected to the input 1TH is opened. The drive is powered down to allow cooling. 2TH-Fault One of the contacts which is connected to the 2TH is opened. 2SE-Fault The 2nd Start Enable input was opened (e.g. active BID) PowerSave The drive package is currently switched off to save energy. PDR-D start DCS! a) Normal operation is not allowed until the Door Check Sequence has been completed successfully. b) The DCS is required again if one of the parameters TOP or BOTTOM is changed. à Enter M-1-3-5 to start the DCS! Shutdown The drive reports a Shutdown or CAN-Communication not working à See event logging of MCB. à check CAN-wiring à check CAN-LEDs Car Light Car Light Relay on top of car is dropped. Note: This message has been renamed in AAE. CLR (1000) LBG/CSP-2 Light Beam Gate has been active. LBG (967, 968) SPB: HTS Hall Temperature Sensor from Service Panel Board is activated. Car is shutdown at next committable floor and taken out of service until the temperature is lower than parameter SPB-Temp. SPB-Temp SPB-Comm. CAN-Communication to SPB is not working. à check CAN-wiring à check CAN-LEDs MRO active The SPB requests to ignore the inputs at Manual Rescue Run. OmuPresent A wrong procedure was used to plug the OMU. It must be ensured that TCI is switched OFF while the controller is powered down: à While the controller is on, switch TCI off (NOR or ERO) à switch the controller off à switch the controller on TCI (691) UCM Detect Unintended Car Movement was detected. UCM-TYP=1, 3 ETSD-Fault ETSD Circuit has triggered. This is the case if DFC+uib+dib is seen during run. PX2.1=2 UP(576) DN(577) ETSC-Fault ETSD Selftest has failed. PX2.1=2 UP(576) DN(577) ETSD-Fault ETSD with reed switch monitor function has detected a problem. This is the case if the ET_P1-4 signals do not match their expected value in a doorzone, or if the ET_S1-4 signals do not match their expected values during the run. à check relays OR Inconsistent configuration of ETSD-related parameters or IOs. If you want to disable the ETSD function, you must disable all ETSD parameter and unprogram all IOs mentioned under “Related setup”. Additionally, if the factory has programmed the ETSD pattern into the EEPROM, then the function cannot be disabled. à disable all ETSD parameters and IOs PX2.1=4 or 5 PX2.2=1 ET_P1(1257) ET_P2(1258) ET_S1(1259) ET_S2(1260) ET_P3(1261) ET_P4(1262) ET_S3(1263) ET_S4(1264) ETSD-Comm The ET_S1-4 expectation message from the Drive was not received for 3 seconds. à check CAN-wiring à check CAN-LEDs PX2.1=4 or 5 PX2.2=1 ET_P1(1257) ET_P2(1258) ET_S1(1259) ET_S2(1260) ET_P3(1261) ET_P4(1262) ET_S3(1263) ET_S4(1264) 6LS-TYP! The parameter “6LS-TYP” at GECB has a different value than the parameter “6LS-TYP” at the drive. à Check GECB Parameter “6LS-TYP” à Check MCB3/MCB3x/GDCB Parameter “6LS-TYP” 6LS-TYP No UIB DIB The safety chain stayed open at UIB and DIB for longer than 5 seconds. à In Low Overhead Installations (OHLOW), check KS contact LOPIT cfg! Low Pit: The parameter HWY-TYP is not configured for Low Pit (4 for APS, 8 for RAPS, or 12 for APS and RAPS) although the E²PROM has been configured in the factory to require Low Pit to be configured. à Set APS and RAPS according to the factory setup. OR HWY-TYP is set to 4, 8, or 12 but the Ultra Drive installation parameter Low Pit is set to 0. à For a Low Pit configuration set Ultra Drive Low Pit to 1 and for a normal pit configuration set HWY-TYP accordingly (e.g. 0). OR HWY-TYP is set to 0 but Ultra Drive Low Pit is set to 1. à For a Low Pit configuration set HWY-TYP according to the present APS/RAPS and for a normal pit configuration set HWY-TYP accordingly (e.g. 0). OR RSL IOs KS-L, DS1, PMSI, APS (if present), RAPS (if present), PBUZ do not have valid addresses. à Set RSL IOs to valid addresses.. HWY-TYP RSL IOs KS-L (1251) DS1 (1252) PMSI (1253) APS (1254) RAPS (1256) PBUZ (1255) Ultra Drive parameter Low Pit KS-L fault Low Pit: KS-L is stuck closed (KS-L=off) although the bottom landing door is open (DS1=off) for > 4 s while the car is not at the bottom floor or at the bottom floor outside DZ. à Check KS-L and DS1 switches and wiring. HWY-TYP KS-L (1251) DS1 (1252) APS fault Low Pit: Front or rear Toe Guard is “folded” above 1LS (APS=off or RAPS=off) for > 2 s or front or rear Toe Guard is “unfolded” at bottom floor (APS=ON or RAPS=ON) for > 2 s. à Check APS and RAPS switches and wiring. Note: If the car has been moved since detection of the error (e.g. by ERO) the car must be moved back into the area where the error occurred: “car is above 1LS” or “car is at bottom floor” in order to reset the error. HWY-TYP APS (1254) RAPS (1256)
|
|
|
|
|
|
Event logging
The table below lists all possible event logging messages of the Service Tool. The events are devided into the following classes:
I | Information |
W | Warning |
F | Fault |
E vent | C lass | R eason | R elated setup | ||
total runs | total number of runs since last power on | - | |||
minutes on | minutes since last power on | - | |||
Operating System | |||||
0000 Task Timing | W | Dummy task has not been called within timeout. Software has been restarted. | - | ||
0001 S/W Reset | W | watchdog circuit on GECB was triggered. Software has been restarted. | - | ||
0002 Illegal Int | W | illegal interupt was executed | - | ||
0003 CcanTxFull | W | Car bus CAN messages cannot be sent | - | ||
0004 CcanBusOff | F | Car bus CAN communication failure | - | ||
0006 StackCheck | F | Stack Violation was detected. Software has been restarted. | - | ||
0007 SCN Error | F | Wrong Software. à order a new software with correct partnumber. | - | ||
0008 TimerSync | F | Internal software timers have not been updated correctly. Software has been restarted. | - | ||
0009 Task Fail | F | Application software doesn’t run properly. Software has been restarted. | - | ||
0010 McbCommErr | F | No CAN connection to the drive | - | ||
0011 SpbCommErr | W | No CAN connection to the SPB | - | ||
0012 Power On | I | Board has been powered on. | - | ||
0013 Event Fail | W | - | |||
0014 PowerOffOn | I | Short Failure of PowerSupply. | - | ||
0016 S/W Restart | W | Reset with unknown reason | - | ||
0017 Trace Error | F | bad value in the eventTraceControl buffer | - | ||
0018 Bad E2P | W | Different addresses found for “mirrored I/Os” (e.g. IO0032 and IO3000) à Check all level- and opening-related I/Os | I/O | ||
0019 MissedLvInt | F | lv1 and lv2 edge was missed | - | ||
0020 RemoteReset | I | System was reset by Elite Service expert | - | ||
0021 Time Adjust | I | Time was changed using SVT function | - | ||
0022 Time Summer | I | Time was adjusted for summer time | - | ||
0023 Time Winter | I | Time was adjusted for winter time | - | ||
0024 Time NotSet | W | Time has not yet been set | - | ||
0025 ExternReset | W | The external watchdog caused a reset | - | ||
0026 Time NmsAdj | I | Time was adjusted by NMS | - | ||
0027 PowerReturn | I | Power returned after ARO | - | ||
0028 CcanSndFail | W | Sending car bus CAN message failed | - | ||
0029 CcanPubFail | W | Publishing car bus CAN message failed | - | ||
0030 CCanError | W | Disturbances on the car CAN bus have been detected. à Check termination, wiring, shielding | - | ||
0031 GcanTxFull | W | Group bus CAN messages cannot be sent | - | ||
0032 GcanBusOff | F | Group bus CAN communication failure | - | ||
0033 GcanSndFail | W | Sending group bus CAN message failed | - | ||
0034 GcanPubFail | W | Publishing group bus CAN message failed | - | ||
0035 GCanError | W | Disturbances on the group CAN bus have been detected. à Check termination, wiring, shielding | - | ||
0036 GwCommErr | W | Gateway communication failure | REM-TYP=6,7,8 | ||
0037 Time Fault | W | The real time clock was corrupted and has now been reset to 01.01.2004. à Use M-1-3-8-1 to set the correct date/time | - | ||
0038 Time Nms>1h | W | Time synchronization between NMS and Controller greater than 1h | - | ||
0039 ZKIP Div0 | W | Numerical division by 0 during ZKIP authentication | - | ||
Operational Control Sub System
| |||||
0100 OpMode NAV | F | OCSS is not available due to drive fault (e.g. drive-fault (NR). This mode is also active after INS before the COR starts | - | ||
0101 EPO shutd. | W | The car is not able to run during EPO (e.g. because it is switched to ERO); the next car is allowed to recover. | NU (017) NUSD (018) NUSG (019) | ||
0102 OpMode DTC | W | door was not able to close (missing DCL, DFC or DW) within timeout | DCL (694) RDCL (695) DOOR, REAR DTC-T | ||
0103 OpMode DTO | F | door was not able to open (missing DOL) within timeout | DOL (000) RDOL (544) DOOR, REAR DTO-T | ||
0104 OpMode DCP | W | car was not able to answer a call within timeout (e.g. door was held open manually) | DCP-T | ||
0106 PDS active | I | partition door switch is opened | PDD (784) | ||
0107 DS bypass | F | Malfunction of Disable Door Switch Relays (DDSR) for Generic Firemen Service. | DDSRC (970) | ||
0108 EEC bypass | F | Malfunction of Disable Emergency Exit Contact Relay (DEMERC) for Generic Firemen Service. | DEMERC (971) | ||
0109 Stuck DCB | F | Door Close Button contact permanent active | DCB (003) | ||
0110 Stuck RDCB | F | Rear Door Close Button contact permanent active | RDCB (547) | ||
0111 Stuck CB | I | Car Call Button contact permanent active | |||
0112 Stuck HB | I | Hall Call Button contact permanent active | |||
0113 NoCarLight | F | The light within the car has failed. | |||
0121 OpMode ARO | F | ||||
0122 SP:en.Feat! | I | One of the following features is programmed in the E2PROM but not yet enabled by Service Panel:
| EFO-POS EPO-POS IO1000 CLR HBP-POS | ||
0124 Stuck WDCB | F | Wheel Chair Door Close Button contact permanent active | WDCB(1167) | ||
0125 Stuck RWDCB | F | Rear Wheel Chair Door Close Button contact permanent active | RWDCB(1171) | ||
Motion Control Sub System | |||||
0200 DrvPosInval | W | Drive set the position invalid, resulting in COR run | - | ||
0201 Correct.Run | I | A correction run was performed (e.g. after INS, NAV) | - | ||
0202 /ES in FR | W | ES-input was activated during Fast Run | - | ||
0203 /ES in SR | W | ES-input was activated during Slow Run | - | ||
0204 TCI/ERO on | I | TCI or ERO has been switched on | ERO-TYP | ||
0205 SE-Fault | F | The car cannot start due to missing SE-signal à Check the door bypass | - | ||
0210 /DZ in NST | F | DZ-signal was lost or not detected at all after having stopped | DZ-TYP | ||
0211 /DFC in FR | W | car door has been opened during Fast Run | - | ||
0212 /DFC in SR | W | car door has been opened during Slow Run | - | ||
0213 DrvPrepErr | W | PrepareToRun expected from Drive (e.g. missing loadweighing information for ABL) | - | ||
0214 DrvStuckPtr | W | Drive stuck in PrepareToRun | - | ||
0215 DrvStuckRtr | W | Drive stuck in ReadyToRun(NoAbl) | - | ||
0216 DrvBrakeErr | F | Brake not lifted. | - | ||
0217 DrvCreepErr | F | Drive Creeptime too long. | - | ||
0218 DrvShutdown | F | The drive reports a Shutdown à See event log of Drive. | - | ||
0219 DrvStartErr | F | ||||
0220 DrvService | W | The drive requested “Request For Service” (REM). à See event log of Drive. | - | ||
0222 1TH-Fault | W | The DBR-contact which is connected to the input 1TH is opened. The drive is powered down to allow cooling. | - | ||
0223 2TH-Fault | F | One of the contacts which is connected to the 2TH is opened. | - | ||
0224 DrvEndRun | F | Drive did not end the run. | - | ||
0225 110VAC dead | F | 110VAC is dead for 5 seconds | - | ||
0227 110VacOffOn | F | 110VAC died and came back before complete power down | - | ||
0228 1LS+2LS on | F | Limit switches 1LS and 2LS are active at the same time. à Check power supply of the position reference system. | - | ||
0230 RSL Adr Chk | F | Some RSL I/Os have to be programmed to a valid address and are not allowed to be set to 00-0 or 01-0. Currently only one I/O is checked: 691 – TCI à Set I/O 691 to a valid address | TCI(691) | ||
0231 Drv SC Err | F | Indicates that ADO is enabled and the conditions were met to begin an ADO run, but the DriveSpeedCheck signal did not toggle on this run à Check CAN bus connection | EN-ADO=1 | ||
0232 UCM Welded | F | The UCM relay is stuck. à Check hardware | EN-UCMK=1 | ||
0233 PowerSave | I | The drive package has been powered on | PDR-D | ||
0234 UCM Detect | F | Unintended Car Movement was detected. | UCM-TYP=1, 3 | ||
0235 ABL Abort | W | Advanced Brake Lift was aborted because the door was not fully closed 10 seconds after the brake was lifted. | EN-ABL=1, DRV-TYP=1 | ||
0237 /DW in FR | W | landing door has been opened during Fast Run | - | ||
0238 /DW in SR | W | landing door has been opened during Slow Run | - | ||
0242 ETSC Fault | F | Emergency Terminal Slowdown Circuit has failed. Refer to Gxx30780DAC_Fsd for a description of this function | PX2.1=2 UP(576) DN(577) | ||
0243 ETSC Block | F | System is blocked after ETSD Failure to prevent further runs. | PX2.1=2 UP(576) DN(577) | ||
0244 2SE-Fault | F | The input 2nd Start Enable opened (e.g. active BID). | - | ||
0245 /UIB/DIB FR | W | The safety chain opened at UIB or DIB during a run while accelerating or at constant velocity. | |||
0246 /UIB/DIB SR | W | The safety chain opened at UIB or DIB during a run while decelerating. | |||
0247 No UIB DIB | F | The safety chain stayed open at UIB and DIB for longer than 5 seconds. à In Low Overhead Installations (OHLOW), check KS contact | |||
0248 ES Wiring | F | ES Safety chain wiring fault (PES not wired in series) à check safety chain wiring. After correction of the wiring the error is cleared by switching off/on. à For GCS222MRL, the SP function “Tools – Safety Wiring” must be executed. | |||
0249 SAF Wiring | F | SAF Safety chain wiring fault (DS/GS not wired in series) à check safety chain wiring. After correction of the wiring the error is cleared by successful door operation or by unlocking the landing door. à For GCS222MRL, the SP function “Tools – Safety Wiring” must be executed. | |||
0250 6LS-TYP! | W | The parameter “6LS-TYP” at GECB has a different value than the parameter “6LS-TYP” at the drive. à Check GECB Parameter “6LS-TYP” à Check MCB3/MCB3x/GDCB Parameter “6LS-TYP” | 6LS-TYP | ||
0255 No RLV/ABL | F | An error occurred during releveling on a system with EN-required UCM. Further relevel runs will be prevented at the floor where the problem occurred. Relevel runs will be re-enabled when the car moves to another floor. | UCM-TYP=3 | ||
0256 EtsdCommErr | F | The ET_S1-4 expectation message from the Drive was not received for 3 seconds. à check CAN-wiring à check CAN-LEDs | PX2.1=4 or 5 ET_P1(1257) ET_P2(1258) ET_S1(1259) ET_S2(1260) ET_P3(1261) ET_P4(1262) ET_S3(1263) ET_S4(1264) | ||
0257 Etsd Block | F | ETSD with reed switch monitor function has detected a problem. This is the case if the ET_P1-4 signals do not match their expected value in a doorzone, or if the ET_S1-4 signals do not match their expected values during the run. à check relays | PX2.1=4 or 5 ET_P1(1257) ET_P2(1258) ET_S1(1259) ET_S2(1260) ET_P3(1261) ET_P4(1262) ET_S3(1263) ET_S4(1264) | ||
0258 /UIB/DIB ET | W | The safety chain opened between DFC and UIB/DIB within the first step ETSD zone, as indicated by ET_P1 and ET_P2. à verify Drive ETSD settings, “ETP Spe %DutySpe” and “ETP2 Spe %Duty” à verify ET_P1-4 sensor adjustment | PX2.1=4 or 5 ET_P1(1257) ET_P2(1258) ET_S1(1259) ET_S2(1260) ET_P3(1261) ET_P4(1262) ET_S3(1263) ET_S4(1264) | ||
0259 LateET_S2/4 | W | The ASCB-controlled relays, ET_S2 and/or ET_S4 switch open too late during acceleration in comparison to the GECB-controlled relays, ET_S1 and/or ET_S3. à readjust ASCB settings | PX2.1=4 or 5 ET_P1(1257) ET_P2(1258) ET_S1(1259) ET_S2(1260) ET_P3(1261) ET_P4(1262) ET_S3(1263) ET_S4(1264) | ||
Door Control Sub System | |||||
0300 DBP: dfc_SE | F | While the door was opening or fully opened, the door bypass was found to be inactive (DFC low or SE high) | EN-RLV, EN-ADO | ||
0301 DCL in [ ] | F | (R)DCL was active while the door was fully opened | DCL (694) RDCL (695) | ||
0302 DoorBridge | F | DW or DFC was not low during the last door cycle, that means that the safety chain is bridged or the Door Bypass is defect. | - | ||
0304 DOL:alw. on | F | DOL was active while the door was fully closed. This event is also logged when the fuses of the door system are burned or if the DOS input is not programmed. This event is not logged within the first 40 seconds after system startup. | DOL (000) | ||
0306 Hwy Access | F | Landing Door was opened or the car door is bridged. à See description for blinking message 'Switch INS' | - | ||
0307 RDOL:alw.on | F | RDOL was active while the door was fully closed. This event is also logged when the fuses of the door system are burned or if the RDOS input is not programmed. This event is not logged within the first 40 seconds after system startup. | RDOL (544) | ||
0308 DOOR sync | F | Multidrop synchronization error | - | ||
0309 DOOR adr. | F | Multidrop unused message origin | - | ||
0310 FDOOR chk | F | Multidrop front door checksum error | - | ||
0311 RDOOR chk | F | Multidrop rear door checksum error | - | ||
0312 FDOOR Tout | F | Multidrop front door communication timeout (>200ms) | - | ||
0313 RDOOR Tout | F | Multidrop rear door communication timeout (>200ms) | - | ||
0314 GDS noPull | F | GDS relay not pulled | - | ||
0315 GDS noDrop | F | GDS relay not dropped | - | ||
0317 Ext LV Err | F | The external door zone sensor X1LV or X2LV was active outside of a doorzone. | X1LV (1039) X2LV (1040) | ||
0318 SP: en.DBP! | I | ADO or /& RLV must be enabled via SP menu (installation without SVT) | EN-ADO, EN-RLV | ||
0319 FGSM Error | F | GSM input error Front door | - | ||
0320 RGSM Error | F | GSM input error Rear door | - | ||
0321 FDOOR stuck | W | Front door is stuck reversing | - | ||
0322 RDOOR stuck | W | Rear door is stuck reversing | - | ||
0323 FDOOR /Deen | W | disable PowerSave mode after deenergized front door could not kept closed | - | ||
0324 RDOOR /Deen | W | disable PowerSave mode after deenergized rear door could not kept closed | - | ||
0334 KS-L fault | F | Please refer to blinking message “KS-L fault” | Low Pit | ||
0335 APS fault | F | Please refer to blinking message “APS fault” | Low Pit | ||
Signaling Sub System | |||||
0400 RSL parity | W | Two remote stations with the same address are connected to the same link | - | ||
0401 RSL sync | W | Synchronisation lost on remote serial link. à Check whether there is a shortcut on the link. | - | ||
0402 RSL reinit | F | RSL driver has reported a problem. RSL was reinitialized. | - | ||
0403 RSL Fail | F | Application has detected that the RSL driver doesn't run anymore. Software has been restarted. | - | ||
0404 RSL Hrtbeat | F | RSL driver has detected that the application doesn't run anymore. Software has been restarted. | - | ||
0405 RSL Board | F | RSL board mismatch! | - | ||
0406 Group RSL | F | Group RSL has failed | - | ||
Group | |||||
0500 RNG1 msg | W | data error on Duplex/Triplex ring | - | ||
0501 RNG1 time | W | no ring messages received from other car for a specific time | GROUP | ||
0502 RNG1 sio | W | framing error on Duplex/Triplex ring | - | ||
0503 RNG1 tx | W | ring messages couldn't be sent in an appropriate time | - | ||
0504 RNG1 rxOff | W | No messages are received within a timeout, and NO BREAK is detected. | - | ||
0505 RNG1 reset | W | Reinitializing RING Service (stm_ring_run expired) | - | ||
0506 DES offline | F | DES is not present | - | ||
0507 GCB offline | F | no GCB is present | - | ||
0508 GCB fail | F | For Compass, the primary GCB has failed and the secondary GCB is used. à Check GCB boards | - | ||
System | |||||
0600 SPB-Alert | W | The Service Panel Board detected a malfunction which hinders a manual rescue operation with SPB and SDI. Possible reasons are: - defective speed encoders for SDI - defective E2PROM on SPB - Missing battery for SPB Press the SPB-buttons REB + DDO simultaneously to locate the error. | - | ||
0601 SPB:TempHTS | W | The Service Panel Board detected an overtemperature. | SPB-Temp | ||
0602 LwssService | W | The LWSS requested “Request For Service” (REM). | - | ||
0604 S/W Changed | I | Informational event that new software was installed. The events are automatically cleared. No action necessary. | - | ||
0605 Update S/W! | W | New subsytem software was installed that requires new GECB software. | - | ||
0606 SpbService | W | The SPB requested “Request For Service” (REM). | - | ||
0607 /TUM1 | F | TUM1 missing after run at TOP or active during standstill; (reduced overhead: trigger modul contacts) | TUM1 (1047) HWY-TYP | ||
0608 /TUM2 | F | TUM2 missing after run at TOP or active during standstill; (reduced overhead: trigger modul contacts) | TUM2 (1048) HWY-TYP | ||
0609 /TDM | F | TDM missing after run at BOTTOM or active during standstill; (shallow pit: trigger modul contacts) | TDM (1049) HWY-TYP | ||
0610 /TUPS | F | TUPS missing during run; (reduced overhead: trigger modul power supply) | TUPS (1050) HWY-TYP | ||
0611 /TDPS | F | TDPS missing during run; (shallow pit: trigger modul power supply) | TDPS (1051) HWY-TYP | ||
0612 SOS up | F | Safety Operated Switch Up triggered | SOSU (1054) HWY-TYP | ||
0613 SOS down | F | Safety Operated Switch Down triggered | SOSD (1055) HWY-TYP | ||
0614 PRBB BatLow | W | The battery of the PRBB board is weak: During PowerOff, the battery only provides power for less than 10 seconds. | EN-PRBB=1 | ||
0615 PCB Certi | W | Korea Only. | - | ||
0619 HWY-TYP | F | Please refer to blinking message “LOPIT cfg!” | Low Pit | ||
Rescue | |||||
0701 SP missing | F | Node Guarding does not detect the SP at the CAN bus. Check CAN_OK LED at SP; Check CAN wiring between GECB & SP; | - | ||
0702 BCB missing | F | Node Guarding does not detect the BCB at the CAN bus. Check CAN_OK LED at BCB_II; Check CAN wiring between GECB & BCB_II; | - | ||
0703 BcbIoFail | F | The state of inputs were not received every second or the output command were not acknowledged. CAN bus overload? Defect BCB_II? | - | ||
0704 BcbHwFail | F | The BCB published an EEPROM error. Exchange BCB_II; | - | ||
0705 BcbSwFail | F | The BCB published a task timing problem. Exchange BCB_II; | - | ||
0706 EncoderFail | F | The rescue encoder generates no signals during a normal run. Check rescue encoder wiring; Replace rescue encoder or GECB_II; | - | ||
0707 OCB fail | F | The OCB auxiliary contacts are wired incorrectly. Check wiring to OCB; Check OCB; Check GECB_II inputs; | - | ||
0708 Overspeed | W | The measured rescue encoder speed is 15% faster than the nominal speed. The OS contact or the safeties could be activated. MRO is prevented. Reset OS contact; Check Encoder / Speed parameter; | SPEED / Encoder | ||
0710 No Battery | F | The BCB misses the rescue battery. Check RPS / battery; | - | ||
0711 BatTempErr | W | The BCB indicates that the battery cannot be charged, because the temperature is out of range. Check battery temperature sensor; | - | ||
0712 BatFault | F | The BCB indicates a battery charge failure or a defect battery. Replace battery; | - | ||
0713 NoBatSignal | F | The BCB has not charge unit signals. It could be defect BCB or a missing charge power supply. Replace BCB_II; | - | ||
0714 Low Battery | I | The battery voltage is to low for ARO or MRO with drive. Charge battery or replace it; | - | ||
0715 BatCharged | I | The BCB indicates a fully charged battery. | - | ||
0716 BatPower | I | The BCB is powered by battery, caused by lost main power supply. | - | ||
0717 NormalPower | I | The BCB operates by the main power supply. | - | ||
0719 No3runNoAro | I | The main power is lost, but there where less than 3 runs before power fail and after ERO or after operating the OCB. These 3 runs are needed to execute ARO. | - | ||
0720 AroStarted | I | ARO were initialized | - | ||
0721 AroAborted | W | The OCSS ARO mode was aborted (e.g. by INS, timeout, invalid position, drive shutdown). If no other event was additional logged (as ARO abort indicator), the failure must be found in the drive (shutdown). | - | ||
0722 AroFinished | I | ARO sequence was finished. | - | ||
0723 AroNoDrive | F | Drive does not communicate at the beginning of ARO. Check wiring between drive / RR relays / BCB_II; | - | ||
0724 AroTimeout | W | ARO didn’t reached the target and opened the door during 5 minutes. | - | ||
0725 NoPreferDir | F | ARO or MRO: Drive did not send its preferred direction. Check CAN connection to the drive; Check if drive is powered by battery; Check drive events; | - | ||
0726 BothDirFail | F | MRO with drive: the car didn’t move / both directions tested. Check rescue encoder & drive; Check Drive events; | - | ||
0727 DrvLineFail | W | The drive indicates a line failure. | - | ||
0728 /RRI_IN | F | The read back contacts of the RR relays were missed during ARO or MRO. | - | ||
0729 /ARO_IN | F | The read back contacts of the ARO relays were missed during ARO or MRO. | - | ||
0730 MroWithDrv | I | MRO with drive were started. | - | ||
0731 Mro w/o Drv | I | MRO without drive were started. | - |
2. SVT Messages at GDCB
Event Log
General Description
All events detected by the drive software are stored in an event log that is accessible through the service tool. There are two event logs: the current log contains information about events which have been detected since the most recent POR, and the saved log which is the EEPROM backup of the events from before the most recent POR.
· Both the current log and the saved log have the same format. Each entry in the log contains the event code, the name of the event, and the elapsed time since POR that the event was detected:
705 E2 Invalid 0000:00:00:00.04 |
The time is in the format: DDDD:HH:MM:SS.SS.
· Enter M- 2-1 to access the current log, events that have occurred since the most recent POR.
· Enter M- 2-2 to access the saved log, events that occurred before the most recent POR.
· Enter M- 2-3 to clear the current event log.
Clear Log? Enter to clear. |
Hit SHIFT-ENTER to clear.
· Enter M- 2-4 to clear a blockage of the drive that occurs when certain events are detected.
Event-Specific Data
When viewing an event, event-specific data can be accessed by using the following service tool keys:
Key Sequence | Description | Example: Before Key Sequence | Example: After Key Sequence |
SHIFT- ENTER | Navigates down one level in the event tree to access event-specific data. | Power On 0000:00:00:00.04 | Drive State @Evt IDLE |
If the fault is: 705 E2 Invalid | 705 E2 Invalid 0000:00:00:00.04 | Go to XX Invalid Param | |
GO ON | Scrolls forward through event-specific data. | Drive State @Evt IDLE | Number of Runs 12 |
GO ON | Scrolls forward through event-specific data. | Number of Runs 12 | Event Response Emergency Stop |
SHIFT– GO BACK | Scrolls in reverse through event-specific data. | Event Response Emergency Stop | Number of Runs 12 |
CLEAR | Navigates up one level in the event tree. | Number of Runs 12 | Power On 0000:00:00:00.04 |
Event-specific data that is available is shown in the table:
Service Tool Display | Description |
Drive State @Evt IDLE | This shows the state of the drive when the event was logged. Note that this is the state when the event is logged rather than the state when the event is detected. |
Number of Runs 12 | This counter is incremented if the last run had no events logged other than “001 New Run”. |
Event Response Emergency Stop | The response of the drive when the event was detected. |
Event Count: 12 | The number of times the fault was logged since the event log was cleared. The counter is incremented each time the fault is logged. Note, the counter is incremented (and event logged) only once in a run even if the event is detected multiple times during this run. 1. This count is different from the occurrence count that is used to block the drive. See section 3) Shut Down Error handling for a description of the occurrence counters that cause blocking. 2. The event counters and logs are cleared via M26. 3. The event count is not cleared at POR. |
Shut Down Error Handling
Some error events cause a shut-down (immediate stop) with an additional inverter blockage immediately or after repeated occurrences in sequence. In case of an inverter blockage, the DC –link will be disconnected from the mains supply.
WARNING! Before starting the drive again, the error reason must be found and solved. Otherwise, the inverter can be seriously damaged.
In case of blockage, do the following:
1. Establish service tool connection to the drive.
2. Find out the reason that caused the blockage by viewing the event log menu 2-1.
3. Clear the blockage by going to menu 2-4 and following the prompt:
Clear Block? Enter to clear. |
Hit SHIFT-ENTER to clear.
· Note that the error “517 DDP Error” cannot be cleared using this option. It must be cleared by the power-reset method (POR) or by software-reset M-2 -5.
· Some errors cause blockage only as long as the failure is still present, e.g., if an over heat occurs then the drive is allowed to do runs again as soon as the drive has cooled down.
Occurrence Counters
As stated above, some errors have an internal counter that is incremented every time that error occurs in succession. When the counter has reached a limit, the drive will block itself. The specific errors that have such counters and the corresponding limits are indicated in the detailed event descriptions in Section 6). For example, “E4” means that 4 occurrences in series lead to a drive blockage.
Applicability
· The counters are applicable only when the drive is in CAN mode (Interface Type = 1). They are not applicable when the drive is in MCSS mode.
· The counters are not applicable during TCI and ERO runs; all the counters are reset to zero when the car is set to TCI or ERO.
Clearing of Occurrence Counters
The occurrence counters are cleared automatically after several consecutive runs without error. The detail action taken is:
· Two successful runs without error are required before any counters are decremented. After two successful runs, all the counters are decremented by one for each successful run. The only exceptions to this are for the events “512 Missing Vane” and “513 No PRS Trans”. For these two events, five successful runs without error are required before these counters are decremented (this is so because these faults result in correction runs, but these faults are not checked during correction runs).
The occurrence counters are manually cleared by any of the following actions:
o The car is placed on TCI or ERO.
o Clear Blockage, M- 2-4
o Software reset, M- 2-5.
o POR
Software Reset
The DSP on the control board can be reset through service tool commands. This is intended to be used when performing software upgrades to the control board.
The reset is accessed in M-2 -5. A confirmation is required:
Reset DSP? Enter to reset. |
Hit SHIFT-ENTER to reset.
Note, the reset is only allowed when the drive is in the IDLE state or less.
Event Response
Every event detected by the drive has a defined response, which is summarized in Table below.
Event Response | Abbreviation | Description |
INFO | I | The event is logged for information only and no action is taken by the drive. |
WARN | W | The event is logged for warning only and limited or no action is taken by the drive. |
COMP | C | The event is logged, the run is allowed to complete, and the drive enters the ShutDown state. This is used by the drive to communicate to the GECB that the drive had encountered a fault. The drive sets the Stop-an-Shutdown (SAS) flag until the fault condition clears. · In CAN mode, the drive will NOT attempt another run until the fault condition clears. · In MCSS mode, the drive will attempt another run if requested by the controller, except for thermal faults. |
NEXT-COMMITTABLE | NC | This response is applicable only for CAN–type controllers during normal runs. · The event is logged and the target is changed to the next committable. · PRS+LS signals are ignored for position corrections. · The drive sets the stop and shutdown (SAS) flag until the fault condition clears. · The run to the next committable will continue only if the fault is determined to be triggered by a failure of the GECB, a failure “both LS active” or a failure of the CAN communications. This is determined by checking if a follow-up event event “511 1LS & 2LS !” was also logged or the CAN message “DrHwySignals” has timed out (=event “906 No LS Msg”). Otherwise, the fault response will transition to a timed decel (DECEL). · When the run ends, the drive passes through SHUTDOWN and position is invalidated. During other run modes than NORMAL, the fault reaction is an immediate timed deceleration (DECEL). |
DECEL | D | This response is applicable only for CAN–type controllers. The event is logged, the run is terminated with a timed decel, and the drive enters the ShutDown state. The deceleration rate is 105% of contract deceleration rate with a minimum of 0.5 m/sec^2. · The drive remains in the ShutDown state until the fault condition clears. The drive will NOT attempt another run until the fault condition clears. · For momentary faults, the fault is automatically cleared after the sheave has stopped, subject to a minimum 250 ms. |
ESTOP | E | The event is logged and the run is immediately terminated by the drive. · In CAN mode, The drive enters the ShutDown state for certain faults. It remains in this state until the fault clears, the sheave has stopped, and a minimum of 100ms. Some faults will set the Stop-an-Shutdown (SAS) flag. The drive will NOT attempt another run until the fault condition clears. · In MCSS mode, the drive will attempt another run if requested by the controller. · When the estop was caused by a command to stop or by the safety chain opening, the drive enters Wait for Safety state. · In either case, if the fault was not a converter-related fault, the converter will remain active until the sheave has stopped. |
SERVICE | S | The event is logged, the run is immediately terminated by the drive, and the drive enters the Power Down state. The drive sets the Stop-an-Shutdown (SAS) flag. The drive is blocked from further runs. A power on reset (POR) is required for the drive to recover from this condition or must be reset through the service tool M-2-4. |
ENDRUN | ER | This response is applicable only for CAN–type controllers. The event is logged, the run or brake lift is aborted using a normal deceleration profile (jerk-in/out), and the drive does not enter the ShutDown state. |
ENDRUN + SHD | ERS | This response is applicable only for CAN–type controllers. The event is logged, the run or brake lift is aborted using a normal deceleration profile (jerk-in/out), and the drive enters the ShutDown state. · The drive remains in the ShutDown state until the fault condition clears. The drive will NOT attempt another run until the fault condition clears. · For momentary faults, the fault is automatically cleared after the sheave has stopped and a minimum of 250 ms time. |
Information Events
SVT Display | Description | |
000 Power On | I | Power was applied to the drive. |
001 New Run | I | A new run was initiated. |
002 SPARE | I | Not used. |
003 Stack Warn | W | The stack usage has exceeded an acceptable limit. |
004 Power Down | I | The power fail signal in the hardware was activated. |
005 Extern FLASH | W | The GDCB FLASH memory has failed. |
006 Extern RAM | W | The GDCB RAM memory has failed. |
007 OMU Present | I | Indicates that a valid OMU is plugged into the drive OMU port at power-up. |
008 OMU Prohibit | I | Indicates that an OMU software upgrade is prohibited because the previous run was TCI. The status of the permissive can be viewed in the SVT parameter OMU Prohibited. Solution If this fault occurs, it can be cleared by performing an ERO run (the ERO run confirms that the mechanic is in the hallway). |
009 Manual Mode | I | Indicates that the drive is in Manual Mode. |
010 B_MODE | I | Applicable only when Interface Type = 2 or 3. Applicable only when “ ARO Type ” = 2 or 3. Logged when the drive received “B_MODE signal” from Battery controller. |
011 Battery Mode | I | Applicable only when Interface Type = 1. Indicates the drive is in battery (ARO-EN) mode operating on 48Vdc battery supply. Logged when the drive received SpbMode message “BatteryMode” from SPBC3. |
012 LearnRun REQ | I | Applicable only when Interface Type = 1. Indicates that the floor table in the drive is invalid and that a new learn run is required. |
013 Reset DSP | I | The DSP was reset using the SVT menu 2-5. |
014 Log Cleared | I | The event log was cleared using SVT menu 2-3. |
015 AutoTun Mode | I | The drive is in Auto Tune mode. |
016 Earthquake | | | Applicable only when Interface Type = 2 or 3 . Indicates earthquake detection. This mode is initiated by the recovery signal from MCSS. In this mode, shock detection and the torque pulsation detection are activated. |
017 Block Cleard | I | Indicates that a blockage condition was cleared either via the service tool menu or by a CAN message. |
018 ALWA CONVRGD | I | Indicates that ALWA has converged with a fixed gain and offset. |
019 ALWA ERROR | I | Indicates that ALWA has an algorithmic error. |
020 ALWA RESET | I | Indiactes either an automatic reset by the algorithm or through the service tool was done. This resets the gain and the offset to 1 and 0 respectively. |
021 ALWA DIVERGD | I | Indicates that the ALWA algorithm has not converged. |
026 UCM-EN clear | I | Applicable only when Interface Type = 1 and UCM-EN on/off = 1. Indicates that a blockage according to 723 UCM in Run, 724 UCM in Slide or 725 UCM BrkBlock has been cleared. . |
Inverter Current Faults
SVT Display | Description | |
100 Inv SW Oct | E4 | The magnitude of the inverter current exceeded an allowed threshold. Possible Causes & Solutions · Incorrect motor phasing ® change parameter Motor Phase 0/1. · Shorted motor phase ® check motor wiring continuity. · The fault threshold can be temporarily adjusted by the parameter Inv I Limit %. Applicable when Interface Type = 0 or 1 : OCT(A) = Drive I fullscale * Inv I Limit %* 0.9 * 1.05 (Drive I fullscale: 402à 80A 404à110A) Applicable when Interface Type = 2 or 3: OCT(A) = Drive I fullscale * Inv I Limit %* 0.9 * 1.25 |
101 Inv I Imbal | E4 | The sum of the three motor currents exceeded 10% full-scale current. Possible Causes & Solutions · Ground fault ® check there are no motor phases shorted to ground. · Signal noise ® check that wiring guidelines are followed. |
102 Inv Id Error 103 Inv Iq Error | E4 | The indicated inverter current regulator error exceeded an allowable threshold. Possible Causes & Solutions · Current regulators are not tuned correctly ® check proper motor parameter settings. |
104 Inv Ix Offst 105 Inv Iy Offst 106 Inv Iz Offst | E | The indicated inverter phase current offset exceeded 5% of full-scale. Possible Causes & Solutions · Defective circuit ® change drive package (if occurs permanently). |
107 Inv Gate Flt | E4 | NOT applicable when Drive Type is 25A. An inverter IGBT gate supply voltage fault was detected. Possible Causes & Solutions · Defective or shorted gate power supply ® change drive package (if occurs permanently). |
108 Inv HW Oct | E4 | NOT applicable when Drive Type is 25A. For 60A V.2 - drives: The power section has detected a fault and set the discrete input (ERR1/INV_FLT: P1-12 ) to the GDCB. Because this input is shared by both HW Overcurrent and HW Overvoltage errors, the measured DC bus voltage is used to distinguish between them: - DC bus voltage is below a specified threshold --> this fault was declared. - DC bus voltage is above a specified threshold --> 116 Inv HW Ovt would have been declared. For all other drives except the 25A drive: The inverter current exceeded a preset level, detected via hardware, (ERR1/INV_FLT: P1-12 ) to the GDCB. Possible Causes & Solutions · Incorrect motor phasing ® change parameter Motor Phase 0/1. · Shorted motor phase ® check motor wiring continuity. |
109 Overload | E4 | An overload condition has been detected. The drive exceeded the maximum time allowed operating at the rated current of the motor. Possible Causes & Solutions · Excessive friction in system ® check for dragging brake or hoistway interference. · The drive is undersized for the installed duty ® confirm system inertia. · The fault threshold can be adjusted by the parameters: Overload sec, Rated mtr i Arms, and Rated Acc I PU, but should not be increased by more than 10%. |
110 Drive Limit | W | The drive is operating at its rated current limit. |
111 No Id fdbk 112 No Iq fdbk | E4 | An error has been detected with the current feedback of the inverter during magnetization of the motor at the beginning of the run. Possible Causes & Solutions · Open motor phase ® check motor wiring continuity. · Bad current sensor ® return unit for service. See parameters Vd out thresh PU and Vq out thresh PU. |
113 Inv IPM Flt | E4 | Applicable only when Drive Type is 25A or LCRD. Indicates a fault has been detected from the inverter Intelligent Power Module (IPM). Possible Causes & Solutions · Defective or shorted gate power supply ® change drive package (if occurs permanently). · Incorrect motor phasing ® change parameter Motor Phase 0/1. · Shorted motor phase ® check motor wiring continuity. |
114 Curr Ovrload | E4 | Not used (was applicable only for non-regen drives). |
115 Brk Chop Err | E4 | Not used (was applicable only for non-regen drives). |
116 Inv HW Ovt | E4 | Applicable only for 60A V.2 drives. The power section has detected a fault and set the discrete input (ERR1/INV_FLT: P1-12 ) to the GDCB. Because this input is shared by both HW Overcurrent and HW Overvoltage errors, the measured DC bus voltage is used to distinguish between them: - DC bus voltage is above a specified threshold --> this fault was declared. - DC bus voltage is below a specified threshold --> 108 Inv HW Oct would have been declared. |
117 Inv Pfai Flt | E4 | Applicable only for 60A V.2 drives. Inverter PWM activity has been detected during IDLE (when S1 & S2 are dropped): · after 2 seconds in IDLE the inverter PWM driver was still active; · or after 4 seconds in IDLE the signal PF_IGBT: P1-13 was LOW which indicated a still active IGBT power supply although it should be switched OFF. Possible Causes & Solutions · Defective gate driver or power supply ® change drive package (if occurs permanently). |
118 Overload WAR | E | See 109 Overload. |
119 Desat Err | E4 | The inverter current and the converter current exceeded a preset level, detected via hardware. |
120 Output Cur | E1 | This fault indicates the motor has currents while Sx dropped. This monitoring is a requirement for GB compliance. |
Converter Current Faults
SVT Display | Description | |
200 Cnv SW Oct | E4 | The magnitude of the converter current exceeded an allowed threshold. Possible Causes & Solutions · Defective hardware ® change drive package (if occurs permanently). · The fault threshold can be temporarily adjusted by the parameter Cnv I Limit %. Applicable when Interface Type = 0 or 1 : OCT(A) = Drive I fullscale * Cnv I Limit %* 0.9 * 1.05 (Drive I fullscale: 402à 80A 404à110A) Applicable when Interface Type = 2 or 3: OCT(A) = Drive I fullscale * Cnv I Limit %* 0.9 * 1.25 |
201 Cnv Id Error 202 Cnv Iq Error | E4 | The indicated converter current error exceeded 30% of full-scale. Possible Causes & Solutions · Current regulators are not tuned correctly ® check proper parameter settings (see parameter Cnv Custom 0/1). |
203 Cnv Ix Offst 204 Cnv Iy Offst | E | The indicated converter phase current offset exceeded 5% of full-scale. Possible Causes & Solutions · Defective circuit ® change drive package (if occurs permanently). |
205 Cnv Gate Flt | E4 | NOT applicable when Drive Type is 25A. An inverter IGBT gate supply voltage fault was detected. Possible Causes & Solutions · Defective or shorted gate power supply ® change drive package (if occurs permanently). |
206 Cnv HW Oct | E4 | NOT applicable when Drive Type is 25A. The converter current exceeded a preset level, detected via hardware. Possible Causes & Solutions · Defective hardware ® change drive package (if occurs permanently). |
207 Cnv Gnd Flt | S | Applicable only when Drive Type is 60A. A ground fault was detected on the converter. Possible Causes & Solutions · Ground fault ® disconnect drive from utility power and check that there are no phases shorted to ground. |
208 Bus Cap Fail | S | The estimated power loss in the drive exceeded a limit. This indicates that excessive power is being dissipated in the drive and is a strong indication that a DC link capacitor has failed. The threshold for this fault is set by the SVT parameters Ploss Thr pre %, Ploss Thr idle %, and Ploss Thr run %. |
209 DC Link OCT | S | Applicable only when Drive Type is 40A. Indicates excessive DC link current. Possible Causes & Solutions · Shorted motor phase ® check motor wiring continuity. · Ground fault ® disconnect drive from utility power and check that there are no phases shorted to ground. |
210 Cnv IPM Flt | E4 | Applicable only when Drive Type is 25A or LCRD. Indicates a fault has been detected from the converter Intelligent Power Module (IPM). Possible Causes & Solutions · Defective or shorted gate power supply ® change drive package (if occurs permanently). · Defective IPM hardware ® change drive package (if occurs permanently). · Ground fault ® disconnect drive from utility power and check that there are no phases shorted to ground. |
211 Battry Chrgd | E4 | Applicable only during ARO (EN) mode. The drive detected charging current into the battery during ARO, which is not allowed. The threshold for the charging currenmt is controlled by the parameter Max Bat Chrg I A. |
212 Cnv Vmag Flt | E | Generally, this fault occurs when power is removed from the drive AC input during a regenerative run. This fault may also occur in concert with certain loss of safety chain events, but this should not be a concern (loss of safety chain causes an estop anyways). This fault management is designed to protect other in-ciruit controller components when the AC line is lost during a regenerative run. If this fault occurs in such a way that interrupts normal elevator operation, then this condition should be reported, and the fault management can be disabled by increasing the Cnv Vmag Thrs PU parameter. This fault management is active only when the drive is regenerating and only when the nominal AC line voltage parameter AC Main Vrms is set <= 400. This fault management is not active when Low Volt Op 0/1 is set to 1. |
Voltage Faults
SVT Display | Description | |
300 DC Bus Over | E3 | The DC bus voltage was greater than 108% of the nominal bus voltage of 750 VDC. |
301 DC Bus Under | E6 | The DC bus voltage exceeded a limit. The limits are: For 415 < Vac <= 480, limit = 70% of nominal (750). For 380 <= Vac <= 415, limit = 309 Vdc. For Vac < 380, limit = 70% of nominal (750). The nominal ac voltage is determined by the EEPROM parameter: AC Main Vrms. |
302 VAC Over | C | The AC line voltage exceeded a limit. The limits are: For 415 < Vac <= 480, limit = 112% of nominal. For 380 <= Vac <= 415, limit = 477 Vrms. For Vac < 380, limit = 115% of nominal. The nominal voltage is determined by the EEPROM parameter: AC Main Vrms. |
303 VAC Under | C | This fault indicates the AC line voltage was below a limit. The limit value depends on whether the drive’s “brown-out” functionality is enabled or not: - For CAN interface (interface type 1), where profile generation is internal to the drive, the brown-out function is enabled. o If the AC line voltage falls 15% below nominal, the brown-out function is activated, the speed is reduced, and the “310 AC Brown-out” warning is logged. o If the AC line voltage falls to 30% below nominal, then additional speed reduction occurs and the “303 VAC Under” fault is logged. - For other interfaces, where profile generation is external to the drive, the brown-out function is disabled. o If the line voltage falls to 15% below nominal, then the “303 VAC Under” fault is logged. - In both cases, the fault response to “303 VAC Under” is: o complete the current run, o go to drive state shutdown, o exit shutdown as soon as the fault clears. The fault is self clearing. - “Nominal” voltage is defined as follows: o 380 Vrms for 380 <= Vac <= 415; Vac otherwise, where Vac = EEPROM parameter: AC Main Vrms |
304 VAC Imbal | C | The AC line input voltages differ from each other by more than 25%. |
305 PLL Unlock | E | The phase lock loop on the AC input voltage has unlocked. This is likely to occur when you try to run with a damaged IGBT. This fault sets the SAS flag. |
306 Single Phase | S | This fault is declared when the drive is set to single-phase mode, and the T phase is connected to a live input. The power during single-phase operation should be connected to R and S phases only and the T-phase should be left open. See EEPROM parameter: Single Phase 0/1 |
307 PLL Freq Rng | E | This fault is declared when the drive ac line frequency estimate is outside of a frequency band specified by the parameter PLL freq band Hz for a amount of time specified by the parameter PLL freq time ms, while there is no PLL unlock fault. This fault is logged whenever the AC line is disconnected. Repeated logging may be an indication of a problem with the AC line. |
308 Welded Mx/Px | S | When the drive enters the power down state, if the DC Bus voltage does not drop below a voltage threshold within a (drive-type depending) wait time, the system will declare that the MX and/or PX contacts may be welded. Warning: Do not cycle power to drive until fault is verified Check the “Inp:Vrms Vdc” SVT display to verify whether the Vdc is actually stuck to a high value (1.41 times the Vrms value) while the state of MX and PX in the “MX PX DX BX” SVT display is actually “0”. If these conditions are met (high Vdc and “0” for both MX and PX), then DO NOT ATTEMPT TO CYLE POWER TO THE DRIVE. This drive may have a real welded MX or PX condition that needs to addressed. For this condition, power down, lock out/tag out energy source, and ship drive back to factory. |
309 Vscales off | W | This fault is logged when the measured AC line voltage and measured DC bus voltage disagree significantly. This check is performed only after M1 is picked after the bus has had enough time to settle to its quiescent value. This fault may indicate that either of the following EEPROM parameters is not set correctly: DC Bus fscale V, AC Line fscale V. |
310 AC Brown-out | W | Applicable only for Interface Type 1. This warning indicates that the ac line has dropped 15% below the nominal value. The drive will continue to run under the "Brown Out" event with reduced motion profiles. When the ac line drops 30% below nominal, 303 VAC Under fault is logged, in which case speed will be further reduced and the drive will finish the current run and not accept any further runs until the fault clears. See event “303 VAC Under” for more details. |
311 AC All Err | E | This fault can occur for one of two reasons: 1. The AC line voltage exceeded a limit above the 302 VAC Over threshold. The limits are: For 415 < Vac <= 480, limit = 125% of nominal. For 380 <= Vac <= 415, limit = 519 Vrms. For Vac < 380, limit = 125% of nominal. The nominal voltage is determined by the EEPROM parameter: AC Main Vrms. OR 2. The following three faults occur at the same time while PTR is active: 302 VAC Over AND 304 VAC Imbal AND 307 PLL Freq Rng |
312 DBTR ShrtErr | C | Applicable only for ARO Type =NI ARO (JIS) and Generator Mode . This fault is set for detecting the short of DBTR. When using a generator, set Generator Mode for 1. When using NIARO mode, set ARO Type for 3. Check DBTR if it has broken. |
313 AC/DC Calib | I | Applicable only when Low Volt Op 0/1 = 1. This fault is active only in low voltage operation mode. This indicates that the calibration process ac voltage sensor versus dc voltage sensor resulted with a cross calibration factor that is either larger than 1.5 or less than 0.5. |
314 Cnv Res FltV | E | This fault management is active only when the event 304 VAC Imbal is active. This fault occurs when a converter voltage transient occurs that exceeds a threshold that is at least 25% greater than the AC Main Vrms parameter setting. If this fault occurs, then check that the 3 phase AC input is present and is reasonably balanced. |
315 Cnv Res FltF | E | This fault occurs when a voltage resonance occurs at the AC input of the drive due to an intermittent loss of an input phase. If this fault occurs, then check that the 3 phase AC input is present, connected well, and is reasonably balanced. This fault is active only for the 406R Version 2 drive. |
Brake Faults
SVT Display | Description | |
400 Brake S1 SAS 401 Brake S2 SAS | C4 | The indicated brake switch is in the wrong state. This is checked both when the drive is in the Idle state and when the drive is running. These faults result in complete the run fault response and set the SAS flag. Note: this event is also applicable when Brk Sw Type 0-4 is set to 0 or 4 where constant states are required on BS1 and BS2 inputs. Possible Causes & Solutions · Incorrect parameter value ® verify correct value of Brk Sw Type 0-4. · Incorrect brake switch wiring ® check brake switch wiring. · Brake not lifting ® check brake wiring & brake power supply. · Insufficient time allowed ® see parameters Brk Pick Time ms and Brk Setl Time ms. |
402 Brake Status | E4 | Applicable only when Brk Cnt Type 0-3 is set to 0. The brake status feedback from the brake module is not in the correct state. |
403 Brake BY | E4 | One or both of the normally-closed BY contacts are not in the correct state. The BY relays should be energized when PTR is active, before the lift brake command is initiated. Note: Actual name is BR relay but still referred here as BY relay for downward compatibility. Possible Causes & Solutions · Incorrect wiring to brake module ® check brake module wiring. · Incorrect brake power supply ® check brake power supply & wiring. · Adjust SVT parameter: SX Pick Time ms |
404 Brake I Off | E4 | Applicable only when Brk Cnt Type 0-3 is set to 2-3. When using the internal brake control, this fault is logged when the brake current feedback offset compensation exceeds a certain amount. The threshold is adjustable with Brk I Offset A. |
405 Brake I Drop | E4 | Applicable only when Brk Sw Type 0-4 is set to 4 and Brk Cnt Type 0-3 is set to 2-3. When the internal brake control drops the brake, this fault is logged if the brake current feedback exceeds a threshold specified by the service tool parameter Brk Min Hold I A. |
406 Brake I Hold | E4 | Applicable only when Brk Sw Type 0-4 is set to 4 and Brk Cnt Type 0-3 is set to 2-3. When the internal brake control picks the brake, this fault is logged if the brake current feedback is less than a threshold specified by the service tool parameter Brk Min Hold I A. |
407 Brake I Max | E4 | Applicable only when Brk Sw Type 0-4 is set to 4 and Brk Cnt Type 0-3 is set to 2-3. This fault is logged if the internal brake control current feedback exceeds a threshold specified by the service tool parameter Brk I Max A. |
408 Brk S1 ESTOP 409 Brk S2 ESTOP | E4 | The indicated brake switch is in the wrong state. This is checked both when the drive is in the Idle state and when the drive is running. These faults result in an immediate ESTOP and set the SAS flag. Note: this event is also applicable when Brk Sw Type 0-4 is set to 0 or 4 where constant states are required on BS1 and BS2 inputs. Possible Causes & Solutions · Incorrect parameter value ® verify correct value of Brk Sw Type 0-4. · Incorrect brake switch wiring ® check brake switch wiring. · Brake not lifting ® check brake wiring & brake power supply. Insufficient time allowed ® see parameters Brk Pick Time ms and Brk Setl Time ms. |
411 Brk S1 DECEL | D | See: 400 Brake S1 SAS, 401 Brake S2 SAS, 408 Brk S1 ESTOP 409, Brk S2 ESTOP |
412 Brk S2 DECEL | D | See: 400 Brake S1 SAS, 401 Brake S2 SAS, 408 Brk S1 ESTOP 409, Brk S2 ESTOP |
413 Bk Desat Err | E4 | The brake current exceeded a preset level, detected via hardware. |
414 Bk Bus Over | I | The brake bus exceeded threshold data. |
415 Bk Bus Under | I | The brake bus fell below threshold data. |
416 Bk fbk tmout | E4 | The brake exceeded threshold data. |
417 Bk SW Oct | E4 | The magnitude of the brake current exceeded an allowed threshold. |
418 Bk lft tmout | C4* | Applicable only when Brk Cnt Type 0-3 is 2-3 or Brk Sw Type 0-4 is 1-3.
This fault is logged if any of the following occur within the amount of time specified by Brk Pick Time ms after lifting the brake.
|
419 Bk drp tmout | C4* | Applicable only when Brk Cnt Type 0-3 is 2-3 or Brk Sw Type 0-4 is 1-3.
This fault is logged if any of the following occur within 3 seconds of dropping the brake.
|
*Note: For events 418 and 419, the drive state machine does not pass through the SHUTDOWN state.
Motion Faults
SVT Display | Description | |
500 Overspeed | E4 | The motor speed has exceeded a speed threshold. The speed threshold is determined by the operating mode of the drive: MCSS mode: adjustable perecentage of Duty Speed mm/s Manual Mode: adjustable percentage of Man Speed mm/s CAN Normal: 110% of Duty Speed mm/s CAN Relevel: fixed percentage of max relevel = 20 mm/sec CAN Learn: fixed percentage of max learn = 500 mm/sec CAN ERO/TCI: fixed percentage of Insp Speed mm/s CAN Rescue: fixed percentage of max rescue = 300 mm/sec For MCSS and manual modes, the percentage is adjusted by SVT parameters: MCSS Overspeed % and MAN Overspeed %. |
501 Pos Tracking | E4 | The position tracking error exceeded a threshold and indicates that the position feedback was not tracking the position reference from the profile generator. This fault is checked only when the drive uses its internal profile generator. See EEPROM parameter: Pos Err Lim mm |
502 Vel Tracking | E4 | The velocity tracking error exceeded a threshold. The velocity feedback was not tracking the velocity reference. Possible Causes & Solutions · Incorrect motor phasing ® change parameter Motor Phase 0/1. · Wrong encoder feedback ® check encoder wiring and attachment. · Incorrect parameter value ® verify correct value of Inertia kg-m2. · Excessive start jerk / improper pre-torque ® verify load weigh device; if no load weigh device present (as during inspection), try increasing parameter Start Gain Ot PU. See section 4.11 for further instruction. · Brake not lifting ® check brake wiring & brake power supply. · Hoistway obstructed ® check for obstruction (e.g. car or counterweight on buffer). · The fault threshold can be adjusted by parameter Track Error mm/s. When Manual Mode is active, this fault threshold is automatically increased by a factor of 3. |
503 LRT Motion | E4 | This fault indicates motion was detected while performing the Locked Rotor Test. The Locked Rotor Test is performed at the beginning of the first run after a power-up to determine the position of the magnets when using a PM motor. The threshold for the fault is specified by the parameter LRT mot err eDeg. If the fault occurs, the brake may not be set properly. |
504 Enc Pos Err | W | This fault indicates that the drive has lost track of the magnet position when using a PM motor. This fault is necessary to prevent a loss of torque production. This fault may be caused by the encoder physically slipping with respect to the motor, or by a bad magnet position calculation during the locked rotor test (LRT). This fault is detected by comparing the magnet position, derived from the encoder and the result of the LRT, to the estimated magnet position based on the back-EMF of the motor. Since the estimator is back-EMF based, the fault detection is enabled only when the motor operates above 30% of the rated motor speed. The default threshold for the fault is 20 electrical degrees. Another locked rotor test will be performed at the beginning of the next run to automatically re-determine the magnet position. See EEPROM parameter: Mag err thr eDeg See EEPROM parameter: Rated Motor rpm See display parameter: Mag Pos Err eDeg |
505 SPARE | D | Not used. |
506 Stopping Err | W | A time-out occurred because the stopping criteria at the end of the run were not satisfied. See EEPROM parameters: Pos Stop Tol mm and Vel Stop mm/sec |
507 Pos at 1LS | NC | Applicable only for Interface Type 1. Unexpected position at 1LS. The 1LS transition occurred at a position outside the expected range for 1LS, or the 1LS signal state is not consistent with hoistway position. Applicable only when landing table is valid and position is valid. |
508 Pos at 2LS | NC | Applicable only for Interface Type 1. Unexpected position at 2LS. The 2LS transition occurred at a position outside the expected range for 2LS, or the 2LS signal state is not consistent with hoistway position. Applicable only when landing table is valid and position is valid. |
509 Floor at 1LS | NC | Applicable only for Interface Type 1. Unexpected floor at 1LS. The 1LS transition occurred at a floor that is different from the expected floor. Applicable only when landing table is valid and limit switch signals are valid. |
510 Floor at 2LS | NC | Applicable only for Interface Type 1. Unexpected floor at 2LS. The 2LS transition occurred at a floor that is different from the expected floor. Applicable only when landing table is valid and limit switch signals are valid. |
511 1LS & 2LS ! | NC | Applicable only for Interface Type 1. Both LS signals are valid and active simultaneously. This fault is used to decide if the NEXT COMMITTABLE fault response shall continue. If this fault is not detected with a certain time, or the fault “906 No LS Msg” is not detected within a certain time, then the fault response is changed from NEXT COMMITTABLE to TIMED DECEL. If this fault persists at the end of a run, the drive will transition to (state, substate) = (IDLE AVAILABLE, RescueOnly). When the drive is in this substate, only commands for Rescue, ERO, ARO and MRO runs are accepted and LS are subsequently ignored. |
512 Missing Vane | NC3 | Applicable only for Interface Type 1. Expected vane is missing. Logged only when outside a vane and an expected transition onto a vane has not occurred. Not checked in Inspection or Correction runs. |
513 No PRS Trans | NC3 | Applicable only for Interface Type 1. Expected transition is missing. Logged only when on a vane and an expected transition has not occurred. Not checked in Inspection or Correction runs. |
514 Enc <> Vane | NC3 | Applicable only for Interface Type 1. An unexpected vane transition occurred. Possible causes could be: 1. Incorrect Car Dir 0/1 setting. 2. Wrong Vane Sensor Type parameter setting. 3. PRS sensor signal wiring mistake. 4. PRS is having false transitions. 5. Encoder is not firmly attached to rotor. 6. Magnet has moved since it was learned during the learn run. 7. Belts are slipping or creeping over the drive sheave excessively. 8. Belts are stretching excessvely. |
515 NTSD failed | W | Applicable only for Interface Type 1. During a normal run, the normal stopping profile did not decelerate the car in time to meet the target. The timed-decel is two-phased, containing a creep region. Only triggered at the terminal landings. The condition for triggering the fault is that the normal profile overshoots the target compared to a linear ramp-down of the speed at 110% of normal decel rate. Only triggered above a certain speed (presently 0.1 m/s). |
516 Corr failed | D | Applicable only for Interface Type 1. A correction run missed the target. This fault is triggered when a correction run terminates outside of the limit switches or outside a vane, or at a different landing other than the terminal landing. The fault is logged after the car has stopped. Note: There is a minor bug with the SVT display for this fault. The fault response in the SVT is shown as ESTOP, when it is actually DECEL. |
517 DDP Error | E1 | Applicable only for Interface Type 1. Delayed Drive Protection (DDP) fault. The time between vanes has exceeded a specified value. It is not checked during ERO or TCI runs. The fault is cleared only by a power cycle or software reset of the drive. The time is specified by the EEPROM parameter: DDP sec. This fault sets the SAS flag. |
518 BeltCmp Wrng | W | Applicable only for Interface Type 1. This indicates that the compensation factors for belt and traveling cable imbalance determined during the learn run were exceptionally large (specifically, the offset factor was greater than 25% rated torque). The compensation factors can be viewed in the SVT display: BeltCmp:Slp mA/m, BeltCmp:Offset A. |
519 RlvPermitErr | W | Applicable only when Interface Type is 1 and Load Weigh Type is 1. Controller has given permissive to relevel while load weighing system indicates overload condition. This contradictory situation has persisted for >200ms. |
520 Rllbck Start | W | Applicable only for Interface Type 1. Rollback of more than 5.0 mm at beginning of run |
521 Rllbck Stop | W | Applicable only for Interface Type 1. Rollback (reverse to direction of run) or overshoot (in direction of run) of more than 5.0 mm at ending of run |
522 ManualRescue | D | Applicable only for Interface Type 1. SPBC message reports that the car has been moved for manual rescue (drive powered off, SPBC lifts brake). The drive’s stored position is invalidated and a locked rotor test initiated before the next run. |
523 Moved at POF | W | Applicable only for Interface Type 1. The SPBC or GECB and the drive have contradictory position information (at power up): the SPBC’s or GECB’s position has been assumed by the drive. |
524 No Enc Signl | E | Applicable only when Encoder Type 0/1 is set to 0 (incremental, double-ended). Encoder channel A input is not detected. Encoder may not be connected, encoder power supply may have failed, or encoder may have failed. This fault sets the SAS flag. |
525 NoRlv SpdChk | D1 | Relevel speed is too high (>= 0.285 m/s). |
526 NoRlv TooMny | D1 | Attempt to relevel after 20 consecutive relevel runs have been performed without start of normal run. |
527 NoRlv LostDZ | D1 | Lost DZ signal or detecting UIS/DIS signal disagreeing with mm-position (on opposite side of target mm-position). |
528 Profile Err | W | The profile chosen is not compatible with the system environment: A) The LS1 or LS2 lengths (learned during learn run) are too short for the drive to be able to stop within. This can be caused by too large speeds in the profile setting or too small deceleration entered. The other possibility would be a really short LS magnet. Cause A can be identified in the vane monitor M-1-7 by comparing measured LS to minimum required. B) The Nom Speed is set too high for the LS signal latency reported by the ICD of the GECB/TCBC (e.g. Nom Speed > 1.8m/s with TCBC). This setting could lead to CORR runs not reaching the target vane. |
529 No enc fdbck | E4 | This fault indicates that the motor started moving without an encoder. This fault is triggered when the motor voltage exceeds a certain threshold defined by No Enc VThrs PU while the encoder speed feedback is below 1mm/s. Check the integrity of the encoder. Also, check motor parameters. |
530 No enc tmout | E4 | This fault indicates that the drive started commanding velocity profile and the motor speed feedback did not exceed 1mm/s for the time duration defined by the parameter No enc flt t sec (default value of the parameter is 0.4 secs). This fault detection is not active in Manual Mode. Possible Causes & Solutions · No encoder feedback signal ® check encoder wiring and mechanical attachment to the sheave. · Incorrect parameter value ® verify correct value of Inertia kg-m2, Man Acc mm/s2, Accel mm/s2, or any of the acceleration parameters in the (L)MCSS if operating in 422 mode. · Excessive start jerk / improper pre-torque ® verify load weigh device; if no load weigh device present (as during inspection), try increasing parameter Start Gain Ot PU. See section 4.11 for further instruction. · Brake not lifting ® check brake wiring & brake power supply. · Hoistway obstructed ® check for obstruction (e.g. car or counterweight on buffer). · The fault threshold can be adjusted by parameter No enc flt t sec |
531 PRS Sigs 1LS | NC | Applicable only for Interface Type 1. The transition into 1LS occurred with PRS signals that are not expected near the learned LS transition point. Applicable only when landing table is valid and limit switch signals are valid. |
532 PRS Sigs 2LS | NC | Applicable only for Interface Type 1. The transition into 2LS occurred with PRS signals that are not expected near the learned LS transition point. Applicable only when landing table is valid and limit switch signals are valid. |
533 ARO Overspd | E | Applicable only when Interface Type = 2 or 3. Applicable only when “ARO Type” = 2 (Interruptable ARO). This fault is declared when the motor speed has exceeded a speed threshold set by the parameter ARO Overspeed % as a percentage of ARO Speed mm/s. This fault is disabled with ARO Overspeed % =0. If this fault is logged, the run is immediately terminated by the drive. |
534 ABL Abort:LW | ER | Applicable only for Interface Type 1. A command for advanced brake lift was received and ignored because no valid load data was available. |
535 Timeout PTR | ERS | Applicable only for Interface Type 1. While in state “Prepare To Run” (during Advanced Brake Lift), the drive did not receive a command to leave this state and timed out after 60s. |
536 Timeout LB | ERS | Applicable only for Interface Type 1. While in state “Lift Brake” (during Advanced Brake Lift), the drive did not receive a command to leave this state and timed out after 16s. |
537 No EndRunCmd | ERS | Applicable only for Interface Type 1. While waiting for a DriveCommand EndRun in substate “STOPPED” the drive did not receive this command and timed out after 3s.. |
538 Abort:EndRun | ER | Applicable only for Interface Type 1. The run has been terminated with normally profiled deceleration by an OPB command (DriveCommand EndRun).. |
539 LvTransUnclr | NC3 | Applicable only for Interface Type 1. With a single-sensor PRS, an ambiguous sensor transition has been detected, could have been either one of two vane edges. Potential root cause: Uncertain mm-position (ESTOP sliding, Power Up recovery from GECB/SPBC, position recovery in LS) and transition occurs within first 5mm of travel. |
540 Shock Detect | W | Applicable only for Interface Type 2 or 3. The shock condition was detected for REI/REM and EAR. |
541 SinCos Warng | W | This fault will be logged for one of the following conditions: 1. When using a sin/cos encoder A. If any of the analog encoder signals fail, then this fault will be logged. Check the encoder connection. B. If the Encoder Type 0/1 SVT parameter has the wrong setting of "0", then this fault will be logged. 2. When using an incremental encoder If the Encoder Type 0/1 SVT parameter has the wrong setting of "1", then this fault will be logged. |
542 Decel Req Fl | D | Applicable to Interface Type = 3 only. A fault occurred and a timed decel is required, so a falsg is sent to the controller to request a timed-decel |
Note) This Timed Deceleration reaction does not lead to the SHUTDOWN state
Temperature Faults
SVT Display | Description | |
600 Inv Tmp Warn | W | The temperature of the inverter heat sink has exceeded 80C. |
601 Inv Tmp Over | C1 | The temperature of the inverter heat sink has exceeded 85C. The fault detection includes hysteresis, and will not clear until the temperature of the heat sink drops 5C below fault value. |
602 Inv Tmp Fail | C1 | Indicates the analog temperature sensor on the inverter heat sink is not connected or has failed. The fan will turn on and remain on when this condition is detected. |
603 Cnv Tmp Warn | W | The temperature of the converter heat sink has exceeded 80C. |
604 Cnv Tmp Over | C1 | The temperature of the converter heat sink has exceeded 85C. The fault detection includes hysteresis, and will not clear until the temperature of the heat sink drops 5C below fault value. |
605 Cnv Tmp Fail | C1 | Indicates the analog temperature sensor on the converter heat sink is not connected or has failed. The fan will turn on and remain on when this condition is detected. |
606 Mtr Tmp Over | C1 | The motor thermal contact has changed state indicating that either the motor is overheating or there is a problem with the contact circuitry. Check the motor temperature and the thermal contact. Although motor thermal contacts can be normally open or normally closed, the drive always expects a normally closed contact. If the thermal contact is normally open, a modification must be made to adapt it to the drive. |
607 Reactor Temp | C1 | The thermal switch in the line reactor has opened, indicating an over-temperature condition in the line reactor. |
608 DBR Tmp Over | C1 | Not used (was applicable only for non-regen drives). |
609 AC/DC Calibr | C | Applicable only when “ Low Volt Op 0/1 ” is set to 1. A calibration was performed to ensure that the AC voltage sense and the DC voltage sense are consistent. |
610 Batt Ovr Tmp | I | The thermal sensor at the charger battery unit is reading high temperatures or disconnected. This could be due to: · an error during the installation phase where the sensor is not connected · the charger spent excessive time in the charge pending phase · the battery ran into a hot condition. Since the installation initially needs to be done correctly, this fault would mean that either battery/charger got into a hot condition due to the ambient or due to overcharging. If it persists for a long time it needs to be checked (job site visit). This timer = TBD minutes. |
611 MTC/RTC Flt | C | Applicable to Ultra Drive only. This indicates that either the motor thermal switch openeded OR the line reactor thermal switch opened. |
Note 1) When these temperature faults occur in 422 mode, PTR is not accepted until the fault condition clears. When these temperature faults occur in CAN mode, the drive behaves as follows:
1. Normal runs are re-routed to the next committable landing.
2. Inspection runs (TCI+ERO) are terminated by timed deceleration.
3. All other runs (ARO, CORR, Rescue, MRO, Re-level) are completed to their regular end
Note 2) No new run is allowed until the condition clears.
Note 3) The fan is turned on 100%.
State Faults
SVT Display | Description | |
700 Safety Chain | E/W | The safety chain is not present. The opening of the safety chain will cause SX relays to drop, causing the drive to de-energized the motor and brake, thus causing an ESTOP.
|
701 No Man Input | E | Applicable only for Interface Type 0. This fault occurs if the drive is in manual mode and the manual mode jumper is removed. |
702 Prechrg Time | E3 | This fault is declared when the DC bus fails to reach the charge voltage threshold within a time limit. The time limit is approximately 2 seconds for 60A V.2 drives and 10 seconds for other regen drives. The timer starts when the drive enters the precharge state. For MCSS systems, the drive enters the powerdown state and waits 2 minutes, and then attempts again. For the regen drive, further precharge attempts are made only if the AC line voltage is within specification. There is no limit on the number of precharge attempts. For CAN systems, the drive enters the powerdown state and waits 30 seconds, and then attempts again. For the regen drive, further precharge attempts are made only if the AC line voltage is within specification. There is a limit of 3 consequtive precharge timeouts after which the drive will be blocked. The voltage threshold is 80% of the actual rectified AC line voltage. Note: There is a minor bug with the SVT display for this fault. The fault response in the SVT is shown as WARN, when it is actually ESTOP. |
703 S Rly Fault | E4 | The normally-open S1 contact was in the wrong state. See SVT parameter SX Pick Time ms. |
704 DBD Fault | E4 | One or more of the normally-closed contacts of S1, S2, BY1 and BY2 were in the wrong state. Three attempts are allowed before the drive is blocked. See SVT parameter SX Pick Time ms. |
705 E2 Invalid | E | The data in the EEPROM is set to values incompatible with the current SCN or new EEPROM parameters have not yet been set. The invalid or blank values must be corrected. Pressing SHIFT_ENTER tells which parameter is invalid and what menu it is located. |
706 E2 Write Lim | W | The allowable number of writes to the EEPROM have been exceeded: Metric writes: 100,000 maximum Event writes: 1,000,000 maximum |
707 ADC Offset | C | Not applicable to Ultra drive. |
708 Cmd to Abort | D | Applicable only for Interface Type 1. The run has been terminated with timed deceleration by an OPB command (DriveRunCommand dir=none). This fault does NOT result in SHUTDOWN. |
709 PRS SigNoise | D | Applicable only for Interface Type 1. Too many PRS signal transitions have occurred over a fixed period of time. |
710 UIB DIB Err | E | Applicable only for Interface Type 1. The UIB and DIB inputs were not consistent with the run command from TCBC-type controller. This fault sets the SAS flag. |
711 DBD Shutdown | S | Three attempts were made to try to correct a relay in the wrong state (one or more of the normally-closed contacts of S1, S2, BY1 and BY2 were in the wrong state). The drive is blocked from further runs. |
712 PostTrq Time | W | A log only fault is reported when the current is not ramped down to zero within a specified time. |
713 Block by xxx | S | The drive has been blocked from further runs. This occurs after certain critical faults have been detected, indicated by “S” in this table, or when certain faults have exceeded an allowed number of occurrences, indicated in this table by the number that follows the fault response category. The blockage must be cleared following the guidelines in Section 6.2.3. This fault sets the SAS flag. |
714 B_MODE Err | W | Applicable only when Interface Type = 2 or 3. Applicable only when “ARO Type” = 3 (NIARO). This fault is logged when “B_MODE” was not detected in less than 200ms from the time when the drive received some fault of "201 Cnv Id Error/ 202 Cnv Iq Error/208 Bus Cap Fail/305 PLL Unlock" or detected DC Bus voltage less than 650V. |
715 ARO BatPower | D | Applicable only in CAN-architecture. The power drawn from the battery during an MRO/ARO run was too high, e.g. > 15A * 48V for 800ms. |
716 Illegal Cmd | W | Applicable only for Interface Type 1 with systems using GECB where CarController ICD >= 10, see “ CAN ICD type ” in M- 1-8 ENGINEERING . An unexpected command has been received in a state where it could not be executed. It was ignored. Note it is possible that a GECB command coincides with a state change in the drive making execution of that command impossible. In such a case, this warning does not indicate a problem with the system. |
717 Triac Stuck | E | Applicable only for Interface Type 1. This fault is logged if both triacs are disabled and safety chain feedback is in the active state. It is not checked during ARO(EN) runs. |
718 PRS Config | C | Applicable only for Interface Type 1. This fault indicates illegal configuration of the PRS. Causes (see M-3-2): · “offset mm” for a sensor is outside “Vane Length mm” (<- Test Variable 2 = 1) · no DZ configured, i.e. "LV1 config 0/1/2"=0 and "LV2 config 0/1/2"=0, (<- Test Variable 2 = 2) · gap between 2 sensors configured <5mm or sequence of sensor positions violated. Required sequence UIS > LV1 > LV2 > DIS |
719 OARO Blocked | I | Applicable only for Optimized ARO. The pilot AR relay for AR1/AR2 contacts is welded ON. If this fault is reported, then optimized ARO functionality is blocked, but normal runs are enabled. The controller will parse this code and request service via REM. |
720 Welded BLV | I | Applicable only for Optimized ARO. The BLV contact is welded. This means that the drive will allow ARO runs and normal runs; however the drive will be unable to completely shut down power after an ARO run. This causes deep discharge of batteries if the power outage persists (shorter life time and unavailability of ARO) and it needs to be fixed. The controller will request service via REM. |
721 PwmExistsFlt | E | Applicable to Ultra Drive only. This fault indicates either PWM is acitve when there is no safety chain or PWM is blocked when safety is present. |
722 E2 Read CkSm | W | Applicable to Ultra Drive only. A checksum fault occurred while reading metrics from E2 at POR. If this occurs, metrics are reset to zero, current floor is set invalid, and floor position is set to zero. |
723 UCM in Run | C | Applicable only for Interface Type 1 and UCM-EN on/off = 1. Indicates that the car has run out of the door zone with open doors! Note: This fault triggers a blockage which may only be cleared by authorized personnel after appropriate investigation of the UCM fault causing the blockage. It cannot be cleared by a power cycle, it can be cleared by an ERO run or by SVT. |
724 UCM in Slide | C | Applicable only for Interface Type 1 and UCM-EN on/off = 1. Indicates that the car has slid out of the door zone with open doors after an ESTOP has aborted a run inside the DZ. Note: This fault triggers a blockage which may only be cleared by authorized personnel after appropriate investigation of the UCM fault causing the blockage. It cannot be cleared by a power cycle, it can be cleared by an ERO run or by SVT. |
725 UCM BrkBlock | C | Applicable only for Interface Type 1 and UCM-EN on/off = 1. Indicates that the UCM-EN brake monitoring has detected a fault potentially compromising the ability of the brake to hold the car. Note: This fault triggers a blockage which may only be cleared by authorized personnel after appropriate investigation of the brake fault causing the blockage. It cannot be cleared by a power cycle, it can be cleared by an ERO run or by SVT. |
726 Tmout SfcMsg | C | Applicable only for Interface Type 1 and UCM-EN on/off = 1. Indicates a timeout of the communication of the SafetyChainSignals (used by UCM-EN) from the GECB. No further run will be started until the communication is re-established. |
727 TOStp SfcMsg | D | Applicable only for Interface Type 1 and UCM-EN on/off = 1. Indicates that a timeout according to 726 has caused the abortion of a run by timed deceleration. This reaction is shown if 726 Tmout SfcMsg occurs while the the UCM monitoring is active (open door with DBP active). |
Task Overrun Faults
SVT Display | Description | |
800 1ms Task | S | The 1 ms task overran. Contact Engineering. |
801 10ms Task | S | The 10 ms task overran. Contact Engineering. |
802 40ms Task | S | The 40 ms task overran. Contact Engineering. |
803 Cnv Task | S | The Converter task overran. Contact Engineering. |
804 Inv Task | S | The Inverter task overran. Contact Engineering. |
805 200ms Task | S | The 200ms Task Overran. Contact Engineering. |
Communication Faults
SVT Display | Description | |
900 MCSS Timeout | E | Applicable only for Interface Type 0. Valid MCSS communication has not been received for 80 msecs. |
901 SVC Tool Err | W | Service tool communication error detected via the local service tool port. |
902 CAN Err | W | Applicable only for Interface Type 1. CAN communication error detected. |
903 E2 CommWrite | W | An error occurred when writing to the EEPROM device. |
904 LWSS Timeout | W | Applicable only for Interface Type 1 and Load Weigh Type is set to 1 or 2. The drive has not received a loadweigh message within a certain time. The fault is cleared when a valid LW message is received. |
905 LWSS Bad Val | W | Applicable only for Interface Type 1 and Load Weigh Type is set to 1 or 2. The drive received an erroneous value in the loadweigh message. Load Weigh Type = 1 : The drive received the full scale value for load percent from the LWB2. The load percent value can be checked in the SVT menu of the LWB2. Load Weigh Type = 2 : The drive received the full scale value for the hitch load measured in kg from the Hitch LW device. The value can be checked in the menu Monitor-Motion, it is the first value in the display “ HitchLW: Empty: “ The fault is cleared when a valid LW message is received. |
906 No LS Msg | NC | Applicable only for Interface Type 1.The drive has not receieved the DriveHoistwaySignal message for 3 seconds. This fault is used to decide if the NEXT COMMITTABLE fault response shall continue. If this fault is not detected with a certain time, or the fault “511 1LS & 2LS !” is not detected within a certain time, then the fault response is changed from NEXT COMMITTABLE to TIMED DECEL. |
907 Primary CRC | W | The drive application performs a CRC of the primary loader and this value does not match the value computed by the conversion utility. |
908 Drive CRC | S | The drive application performs a CRC of the drive software and this value does not match the value computed by the conversion utility. |
909 CAN BusOff | W | Applicable only for Interface Type 1. The CAN controller of the drive has shut itself down due to a persistent communication problem on the CAN bus or CAN power failure (broken connection). |
910 CAN OPB_Init | W | Applicable only for Interface Type 1. Initialization of the CAN communication software has failed. |
911 CAN TxQ Full | W | Applicable only for Interface Type 1. Overflow in the transmit queue of the CAN port, messages have been lost. |
912 No FloorInfo | W | Applicable only for Interface Type 1. Neither the SPBC nor the GECB have sent valid position in return to the request by the drive (timeout 200ms after request for SPBC, 200ms after its StartUp message for GECB). |
913 MCSS Warning | W | Applicable only for Interface Type 0. MCSS Communication error detected. It includes Checksum, Framing, Parity or invalid format. |
914 Power E2 Err | S | The power section could not be identified because bad or undefined drive code data has been read from the EEPROM on power section board 1 (DCPB). This check is only performed at power on. |
915 LWSS not cal | W | Applicable only when Interface Type = 1. Applicable only when Load Weigh Type = 2. Hitch load weighing device not calibrated. The calibration is done during a learn run. |
916 Power E2 Rng | S | Not applicable for ULTRA drives. Applicable only to drives with eI2C EEPROM storage capability. This fault is logged if the scaling parameters in one of the power section EEPROMs are out of range for the specified drive type. |
917 CPLD Ver Flt | E1 | Not applicable for ULTRA drives. The CPLD version is not compatible with either the HVIB EERPROM or the GDCB EEPROm parameter setting. See the attached table for erroneous combinations. |
918 ARO Ver Flt | E1 | This event indicates an incompatibility between the Primary Loader and the CPLD version in case of an optimized ARO system. The Primary Loader must be version AAA31013CAE or later and the CPLD must be version 9 or greater. This event occurs if either is not satisfied for an optimized ARO system. |
919 Powrbrd miss | S | Bad or no response from the DCPB EEPROM where the power board information is stored. This check is only performed at power on. |
920 Micro ChkSum | E | Applicable to Ultra Drive only. This fault indicates that the DSP is not communicating to the microprocessor. |
921 FPGA ChkSum | E | Applicable to Ultra Drive Only This fault indicates that the DSP is not communicating to the FPGA device. |
922 FLASH Warn | W | Applicable to Ultra Drive Only A communication fault was detected by the SPI FLASH test routine. This log only event indicates that the SPI communication or SPI FLASH device may have failed. |
923 FPGA Warn | W | Applicable to Ultra Drive0nly This warning indicates that DSP received one erroneous packet from the FPGA. |
924 Micro Warn | W | Applicable to Ultra Drive Only This warning indicates that the DSP received one or more consecutive erroneous packets from the microprocessor. Fault threshold is controlled by parameter Micro Wrn 0. |
925 No CAN-PRS | C | Requested PrsSignals CAN messages are not received. While the fault persists, only ERO and MRO runs are allowed. |
926 CAN PRS Msg | W | A discontinuity in the CAN PrsSignals was detected, a message may have been lost. |
927 DSP2FPGA Wrn | W | Applicable to Ultra Drive Only This warning indicates that FPGA received one packet with wrong checksum or stuff bits. |
928 DSP2FPGA Flt | E | Applicable to Ultra Drive only. This fault indicates that the FPGA received more than one packet with wrong checksum or stuff bits. |
Дата добавления: 2019-02-22; просмотров: 1395; Мы поможем в написании вашей работы! |
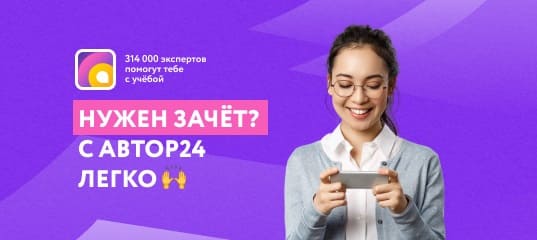
Мы поможем в написании ваших работ!