Методы юстировки оптических волокон
Перед началом сращивания концы волокон помещают в V-образные металлические или керамические направляющие канавки блока юстировки и фиксируют магнитными прижимами. Процесс установки, начальное сведение волокон и контроль качества сростка осуществляется под визуальным контролем. В качестве устройства визуального контроля может быть использован обычный или проекционный микроскоп, а также встроенный телевизионный монитор размером экрана по диагонали до 4 дюймов. В случае применения встроенного монитора, как правило, устанавливается стандартный телевизионный выход для подключения к внешнему видеоконтрольному устройству. Оптическая система контрольных устройств имеет коэффициент увеличения до 200 раз. Для получения более высокой точности юстировки может использоваться уголковое зеркало или две телекамеры, позволяющие одновременно или поочередно наблюдать свариваемые волокна в двух взаимно перпендикулярных плоскостях.
Существуют следующие способы юстировки оптических волокон:
1. Более простой по конструкции полуавтомат не производит пространственного выравнивания свариваемых волокон, которые центрируются только за счет укладки в прецизионнуюV-образную канавку (рис. 14). Полуавтоматика аппаратов этой группы осуществляет только линейное сведение волокон. В полуавтоматических сварочных аппаратах российского производства оператор дополнительно имеет возможность ручной визуальной юстировки концов световодов в двух плоскостях с помощью микроподвижек.
|
|
В отличие от полуавтоматов автоматические сварочные аппараты минимизируют потери в точке стыка волокон за счет их дополнительного выравнивания перед сваркой по двум координатам независимыми электромеханическими подвижками с точностью подачи до 0,1 мкм и с последующим сведением после подачи электрической дуги. Обычно одна из подвижек служит для линейных перемещений вдоль оси Z в процессе юстировки и сварки, тогда как вторая выполняет котировочные перемещения по осям X и Y. В аппаратах с выравниванием по оболочке аналогично полуавтоматам контроллер управляет только одной подвижкой, а юстировка производится за счет укладки в V-образную канавку. Дополнительные функции автоматики ограничены подачей волокон в зону сварки с установкой заданной величины зазора, контролем качества скола и расчетом ожидаемой величины потерь [6].
Рис. 14. Юстировка волокон меодом V-образных канавок
2. Непосредственное наблюдение волокон посредством зеркал или двумя взаимно перпендикулярными видеосистемами с фотоприемниками с высокой разрешающей способностью получило название HDCM-метод (High resolution Direct Core Monitoring).
|
|
3. В большинстве аппаратов применяется система выравнивания волокон по изображению в параллельном пучке света PAS-система (Profile Alignment System). При таком методе юстировки волокна освещаются сбоку параллельным пучком света так, что из-за разницы показателей преломления оболочка и сердцевина фокусируют свет, действуя как цилиндрические линзы (рис. 15). При этом формируется изображение, на котором видны границы сердцевины и оболочки волокна, что позволяет определить эксцентриситет в каждом из волокон. Анализ изображения линии, выполняемый с помощью телекамеры и встроенного контроллера сварочного аппарата, позволяет осуществить юстировку световодов. Одновременно контроллер системы управления аппарата оценивает качество скола торцевой поверхности волокон и в случае выявления каких-либо дефектов прекращает процесс сварки. Такая система особенно распространена в аппаратах японских производителей. Она используется и для грубой юстировки, и для тонкой подстройки волокон.
Рис. 15. Юстировка волокон меодом PAS
4. У европейских производителей PAS-система используется для грубой настройки. Тонкая юстировка осуществляется по максимуму мощности излучения, передаваемого через сварное соединение LID-системой (Local Injection and Detection). Этот метод основан на вводе контрольного оптического сигнала в сердцевину первого световода и съеме его из сердцевины второго с максимизацией выходного сигнала за счет перемещения волокон микроподвижками (рис.16).
|
|
Рис. 16. Юстировка волокон меодом LID
Для ввода и вывода сигналов используются изгибные ответвители. Недостаток такого подхода состоит в том, что метод LID допускает работу не со всеми типами одномодовых световодов, не позволяя применять автоматику к волокнам в буферном покрытии 0,9 мм, а использование изгибного ответвителя увеличивает риск возникновения скрытых дефектов в световоде. Однако этот метод позволяет решить проблему, связанную с тем, что силы поверхностного натяжения стремятся совместить оси оболочек, и, следовательно, развести (при наличии в волокнах эксцентриситета) оси сердцевины волокон. Как результат - дополнительные потери на шве. Поэтому при данном методе предусмотрена коррекция эксцентриситета. Оси волокон предварительно разводятся на такое расстояние, на которое согласно компьютерному расчету надо развести оси сердцевины волокон так, чтобы силы поверхностного натяжения совместили их при сварке.
|
|
5. Метод юстировки по тепловизионным изображениям основан на управлении параметрами сварки на основе данных, полученных в результате анализа тепловых фотографий места стыка. В процессе сварки волокна излучают сигнал в ИК-диапазоне. Видеокамера через систему фильтров фиксирует изображения, которые запоминаются программой аппарата. Кроме того, информация обрабатывается численными методами и по команде отображается на дисплее. Таким образом, оператор получает достоверную информацию о состоянии волокон во время сварки, а не до или после нее, как в случае аппаратов с "холодным" изображением. По тепловым фотографиям вычисляются: профиль показателя преломления, градиент деформации сердцевины, диаметр модового пятна. Все значения вычисляются по двум осям. По этим данным можно определить тип волокна, отличить, эрбиевое волокно от волокна со смещенной дисперсией.
6. Кроме того, используется уникальный метод управления в режиме реального времени (RTC), с помощью которого можно получить хорошие результаты независимо от внешних условий и типа используемого волокна. Благодаря RTC удается измерить диаметры модовых пятен свариваемых волокон и изменить режим сварки таким образом, чтобы получить наилучший результат. Метод RTC основан на юстировке волокон способом CDS (Core Detection System) и начинается с короткого импульса, очищающего волокно. Затем следует более мощный импульс, который разогревает волокно до такой степени, что сквозь оболочку волокна становится видна сердцевина. Благодаря этому можно определить смещение сердцевины друг относительно друга. Определив смещение, сварочный аппарат совмещает волокна, учитывая при этом влияние поверхностного натяжения. Затем волокна сращиваются, причем сам процесс сварки отображается на экране дисплея. Если смещение сердцевины лежит в заданных пределах, а диаметры модовых пятен равны, то на этом сварка завершается. В противном случае волокна вновь разогреваются, и вносится очередная поправка. После проведения сварки волокна и оценки в двух плоскостях, можно вывести на экран два сохраненных тепловых изображения. Эти изображения показывают волокна в то время, когда возникает дуговой разряд. Оценки потерь могут отличаться от истинных из-за того, что существует задержка по времени между снимком и малыми перемещениями волокон в процессе сварки. Для оценки потерь и, чтобы учесть все факторы, действующие на волокно в критической зоне сварки (КЗС), необходимо выбрать изображение, на котором наиболее отчетливо видна сердцевина волокна. Метод CDS (Core Detection System) наиболее быстрый. Благодаря этому методу весь процесс сварки, включая юстировку, занимает несколько секунд, при этом получается качественный сросток [5].
Процесс сварки
Целью обеспечения высокого качества сварки предусматривается визуальная, а в ряде случаев и программная проверка устойчивости дуги в процессе разряда. Так, при контроле дуга должна быть прямой и стабильной, в противном случае электроды должны быть очищены или заменены. В связи с этим важным параметром является возможность самодиагностики износа электродов.
Учитывая, что параметры дуги зависят от климатических условий, в ряде сварочных аппаратов предусматривается автоматическая компенсация интенсивности разряда в зависимости от температуры, влажности и давления окружающей среды.
Если же сварочный аппарат не имеет подобной функции, то при изменении его места положения и условий окружающей среды, необходимо сделать калибровку дуги. После чего можно приступать непосредственно к процессу сварки.
Достижение высокого качества сварки невозможно без высокоточного позиционирования, которое осуществляется пьезокерамическими двигателями при юстировке и автоподаче волокон, позволяющими достичь максимального значения люфта системы юстировки, не превышающего 1 мкм. Точность центрирования посредством V-образной канавки достигается использованием стабильных материалов, в частности, керамической основы.
В результате юстировки волокна устанавливаются на расстоянии порядка 9 мкм, после чего разогреваются до температуры размягчения кварцевого стекла (ок. 1000 ºС). Размягченные волокна вдавливаются друг в друга на 5 мкм. Движению волокон при этом противодействует сила внутреннего трения (вязкость) и способствует сила поверхностного натяжения. Вытесненное из волокон при вдавливании расплавленное кварцевое стекло образует на поверхности волокон уплотнение близкое к сферической форме. По завершению сварки в еще нагретом состоянии волокно растягивается для того, чтобы уменьшить уплотнение на сростке.
Применение в сварочных аппаратах видеосистемы позволяет перед началом сварки визуально контролировать результат центрирования, тип сердцевины, качество торцов и микрозагрязнения свариваемых оптических волокон, а по окончании сварки оценить качество свариваемых соединений. Кроме того, ряд сварочных аппаратов представляет в цифровом виде значение угла скола и сдвиге осей оболочек (сердцевины) волокон до и после сварки, а также расчетное значение потерь в месте сварки. Однако такая оценка не учитывает всех возможных факторов, приводящих к возникновению потерь. Так, например, даже при высочайшем качестве сростка возможно возникновение дополнительных потерь, вызванных неравенством диаметров модовых пятен свариваемых волокон.
Результирующее значение потерь определяется либо косвенно по результатам осевых смещений сердечников при внешнем освещении волокна, либо прямым способом, когда центрирование волокон осуществляется по излучению, проходящему через оптические волокна.
Фундаментальными предпосылками обеспечения низкого значения потерь в месте сварки является концентричность сердечника и оболочки, хорошая подготовка торцевых поверхностей волокна.
После завершения сварки полуавтоматический и автоматический аппараты проверяют прочность сростка, растягивая волокна с усилием 200-250 г (стандартный тест) или 450 г(усиленный тест).
После сплавления волокон место стыка необходимо защитить. Наиболее популярной является термоусадка с помощью комплекта деталей защиты сростка (КДЗС) или защитной гильзы (protection sleeve). Этот комплект представляет собой термоусаживающую гильзу длиной 40 или 60 мм, внутри которой расположена трубка из материала с высокой текучестью (сэвилена) и металлический стержень диаметром 1 мм. Обычно внешняя трубка гильзы выполняется бесцветной, возможна поставка на заказ цветных защитных гильз.
Перед сваркой гильзу КДЗС надевают на один из сращиваемых концов волокна. После сваривания ее надвигают на место стыка и нагревают в печке сварочного аппарата до температуры 100...120°С на протяжении 1–1,5 минуты. Для оптимизации процессов разогрева некоторые типы сварочных аппаратов позволяют выбрать одну из нескольких возможных управляющих программ. В процессе нагрева сэвилен расплавляется, заливая место стыка волокон и прочно сцепляясь со стеклом и буферными покрытиями, а термоусаживающая трубка плотно прижимает металлический стержень к сращенным волокнам, надежно защищая за счет этого область сростка от изгибающих воздействий. Необходимость применения металлического стержня, который играет роль упрочняющего элемента, обусловлена тем, что в процессе сварки из-за термического удара прочность волокон снижается примерно на 20–30 %. После выполнения усадки гильзу укладывают в организатор сплайсов настенной муфты или разделочной полки, который, наряду с механической фиксацией, обеспечивает также соблюдение заданного радиуса изгиба волокон. Для восстановления защитных оболочек ленточных кабелей применяются специальные гильзы, рассчитанные на 6 или 12 световодов ленты [7].
Большинство моделей сварочных аппаратов имеет интегрированную в них печку для усадки защитных гильз. В некоторых конструкциях применяется исполнение этого модуля в виде внешнего прибора с отдельным питанием.
Вместо гильз КДЗС в некоторых случаях могут применяться механические элементы защиты стыка (Mechanical Fusion Splice Protection Cover), которые представляют собой полимерный корпус из двух половин, соединенных пружинным шарниром с защелкой. Корпус надевается на место сварки, после чего шарнир закрывается под защелку. Выпускаемый американской фирмой АСА элемент ULTRASleeve этого типа может устанавливаться как на одиночное волокно в буферном покрытии 0,25 и 0,9 мм, так и на ленточные кабели максимум с 4 световодами. Время установки элемента не превышает 30 с.
При производстве волоконно-оптических компонентов, не допускающих использования КДЗС, применяют восстановитель защитного покрытия оптического волокна. Восстановитель покрытия Fujikura FSR-02 обеспечивает восстановление цветного или бесцветного защитного покрытия оптического волокна до исходного диаметра после выполнения сварки. Программируемое усилие при тестировании сварного соединения на прочность от 4 до 20 Н. Для сварного соединения, не прошедшего тест на прочность, фиксируется усилие в момент разрыва бракованных соединений. Время восстановления покрытия составляет 15 с – нанесение, 15 с – полимеризация.
Дата добавления: 2018-11-24; просмотров: 1387; Мы поможем в написании вашей работы! |
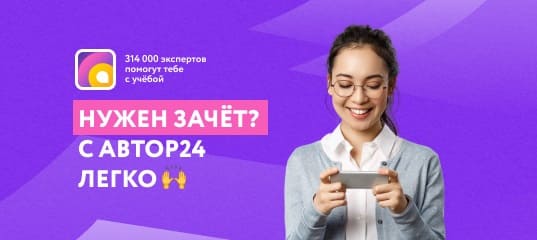
Мы поможем в написании ваших работ!